Efficient Machining Of Titanium Alloy Aircraft Parts
Efficient Machining Of Titanium Alloy Aircraft Parts
Titanium alloy has the advantages of low density and corrosion resistance, and is widely used in the construction of aircraft bodies, but it is prone to deformation during cnc machining, and the machining accuracy is difficult to guarantee. Therefore, it is necessary to use advanced modern technology and perfect infrastructure to formulate effective machining procedures, and ultimately improve the overall machining efficiency and quality through CNC machining equipment. In-depth analysis combined with titanium alloy machining methods is aimed at improving the machining efficiency of related parts |
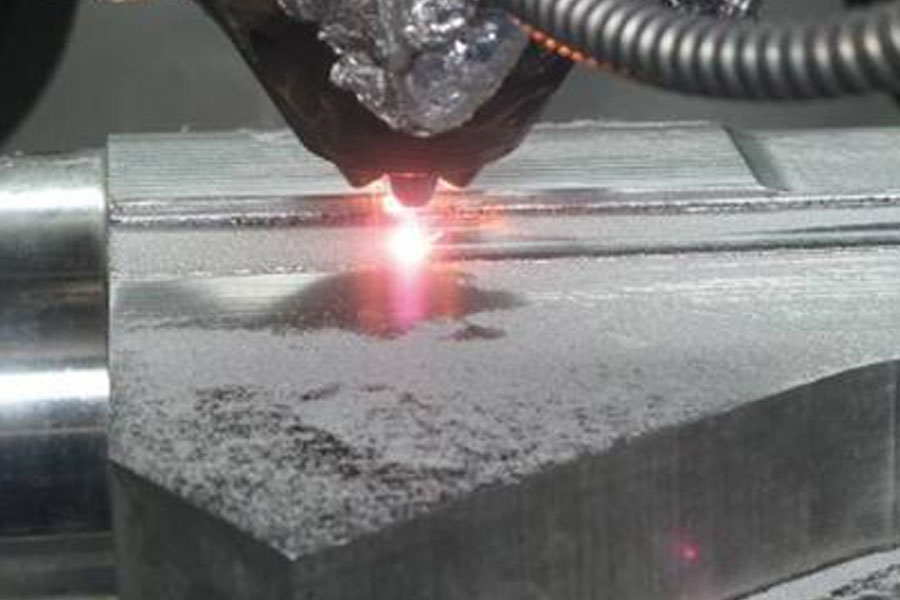
As a kind of high-strength material parts, titanium alloy parts have extremely high application value in the aircraft parts field. Traditional machining methods are no longer suitable for the production requirements of modern aircraft structures. Therefore, the use of titanium alloy parts can meet the requirements of aircraft development to the greatest extent. Titanium alloy parts have been widely used in aircraft construction. For example, screws and nuts can be used to fix larger fuselage frames, and key parts such as engine blades and landing gear can be made of titanium alloy materials.
Application fields and advantages of titanium alloy parts
1.1 Titanium alloy parts application field
Take the B777 passenger aircraft as an example. Titanium alloy castings are used in the manufacture of the aircraft mounting frame. It can be seen that in the manufacture of civil aircraft, the application technology of titanium alloy parts has been relatively mature. In addition, titanium alloy parts are also of great significance to the development of aviation industry. For example, European Doncasters company uses centrifugal casting technology to apply titanium alloy to brake torque.
1.2 application advantages of titanium alloy parts
Titanium alloy parts have the following technical advantages:
- First, there is no need to use molds during the molding process;
- Second, there is no need to invest a lot of energy and funds in the preliminary preparation stage;
- Third, it can effectively improve the efficiency of material usage. Titanium alloy parts not only improve the safety performance of aircraft structural components, but also minimize the number of connected parts, effectively saving manual assembly time, and achieving the effect of two-way development of revenue and quality.
Features of aircraft titanium alloy parts
2.1 not easy to deform
Titanium alloy material has higher strength and thermal strength, and has a lower density. Compared with steel material, it is only 60% of the density of steel. This makes titanium alloy material without deformation problems even at high temperatures of 300°C to 500°C. The titanium alloy structure of a certain type of aircraft engine is processed by TC4 titanium alloy forgings. The mass is 19.987kg, the width is 600mm, and the length is 2800mm, but the wall thickness is only 1.50mm.
2.2 low temperature resistance
Titanium alloy has high low temperature resistance, that is, it can still maintain its own mechanical properties under low or ultra-low temperature conditions. It is a material with strong low temperature resistance. According to related tests, it is known that titanium alloy is at -196°C. Below, the tensile strength σb is 1207Pa.
2.3 strong corrosion resistance
Titanium alloy parts can be widely used in the aircraft field, a very important reason is that it has super corrosion resistance. When the aircraft is flying at high altitude, the substances in the air will have a certain corrosive effect on the surface of the aircraft. Titanium alloy parts can effectively deal with this drawback and ensure the safety of the aircraft.
2.4 With chemical properties
Titanium alloys can react with a variety of metal elements. With the help of chemical reactions, the mechanical properties of titanium alloys can be maximized. For example, in a high temperature environment above 600°C, titanium alloys can react with oxygen to form a corresponding oxide layer.
2.5 low thermal conductivity
The application of titanium alloy parts on airplanes can effectively reduce the probability of failure of airplane parts, and avoid excessive heat conduction of airplane parts that affects the normal application of other parts.
2.6 Small modulus of elasticity
In the process of using titanium alloy parts, do not process them into slender parts. This is because the elastic modulus of titanium alloy is relatively small and it is easy to deform. In addition, in the titanium machining process, due to the large rebound of titanium alloy, it is easy to wear the tool.
Machining and Application Measures of Aircraft Titanium Alloy Parts
China's aviation industry attaches great importance to the application of raw materials, and the R&D focus is on process development and application in order to improve the performance of aircraft.
3.1 Broaden the field of use of titanium alloy castings
Compared with other titanium parts, the investment casting method has its own unique advantages:
- The casting size is accurate, the surface is relatively smooth, and the roughness is low;
- It can cast complex shaped castings;
- While improving the utilization rate of metal raw materials, it can also improve production flexibility and adaptability.
However, in the actual application process, the strength of titanium alloys cannot fully meet the requirements of aircraft construction. Therefore, the emphasis should be placed on the improvement of the tensile strength of titanium alloys during research and development. The development speed of titanium alloy precision casting technology in my country has been continuously increasing in recent years. On this basis, the diagonal overrunning clutch has been widely used in the aviation field. Due to the high requirements of aircraft for titanium alloy parts, the formation rate of my country's aircraft titanium alloy parts is relatively low. Therefore, science and technology must be used to improve the casting level, reduce product production costs and production cycles, and achieve mass production goals. .
3.2 Reduce development cost
On the basis of high-power laser cladding and rapid prototyping, titanium alloy powder laser forming technology has been widely used. This technology uses a high-energy laser beam to melt the titanium alloy powder and solidify it on the substrate in the shape of tiny droplets, and then rely on computer control technology to make the laser head move repeatedly, thereby stacking layer by layer, and finally obtain the required titanium alloy parts model.
At present, the overall performance of the titanium alloy structure has been significantly improved, and the weight of the part itself has been significantly reduced, which has been favored by the aviation field.In combination with the actual situation, the cost of Nb, Mo and V elements in titanium alloys is relatively expensive, leading to higher raw material costs.
Therefore, aviation titanium alloys with relatively low cost investment have attracted great attention. At present, researchers have found that Fe elements can be used to replace the high-cost Nb, Mo and V elements, which can not only ensure the performance of materials, but also effectively reduce The input cost of titanium alloy raw materials.
3.3 Distribution and surface protection method
In the analysis of the surface layer of BT3-1 and OT4-1, it can be concluded that the distribution of hydrogen in the surface layer is relatively complicated, and the hydrogen content will gradually increase, and when it reaches the maximum value, it will decrease accordingly. At present, laser three-dimensional forming technology and titanium alloy parts have been effectively combined, and large-scale titanium alloy main bearing components for aircraft have been developed.
3.4 Improve the metal utilization factor of hot forging dies
The most effective way to increase the metal utilization factor is to use low-oxidation and non-oxidation heating. For titanium alloys, heating the blank with dry air can effectively solve this problem. According to related research, when heating in an electric furnace, the temperature should be controlled at 950℃~980℃. In addition, by conducting tests on BT20 and OT4-1 (TC1), heating all samples and die forging uniformly, it can be found that the low-temperature pre-oxidized wool surface of the blank exhibits a smooth effect, which leads to the conclusion that the oxide layer and the gas saturation state have an important influence on the mechanical properties.
Conclusion
In the context of the continuous development of science and technology, most enterprises have completed their transformation, and my country's aluminum industry has also achieved good results. In the process of rapid economic development, the titanium alloy industry continues to develop in the direction of renewable energy, enabling titanium alloy parts to be effectively used in more fields, laying a solid foundation for the development of energy conservation and emission reduction.
Link to this article: Efficient Machining Of Titanium Alloy Aircraft Parts
Reprint Statement: If there are no special instructions, all articles on this site are original. Please indicate the source for reprinting:https://www.cncmachiningptj.com/,thanks!
PTJ® provides a full range of Custom Precision cnc machining china services.ISO 9001:2015 &AS-9100 certified. 3, 4 and 5-axis rapid precision CNC machining services including milling, turning to customer specifications,Capable of metal & plastic machined parts with +/-0.005 mm tolerance.Secondary services include CNC and conventional grinding, drilling,die casting,sheet metal and stamping.Providing prototypes, full production runs, technical support and full inspection.Serves the automotive, aerospace, mold&fixture,led lighting,medical,bicycle, and consumer electronics industries. On-time delivery.Tell us a little about your project’s budget and expected delivery time. We will strategize with you to provide the most cost-effective services to help you reach your target,Welcome to Contact us ( sales@pintejin.com ) directly for your new project.
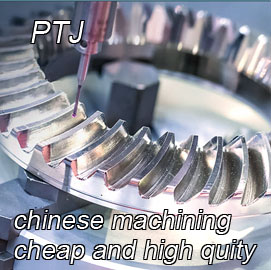
- 5 Axis Machining
- Cnc Milling
- Cnc Turning
- Machining Industries
- Machining Process
- Surface Treatment
- Metal Machining
- Plastic Machining
- Powder Metallurgy Mold
- Die Casting
- Parts Gallery
- Auto Metal Parts
- Machinery Parts
- LED Heatsink
- Building Parts
- Mobile Parts
- Medical Parts
- Electronic Parts
- Tailored Machining
- Bicycle Parts
- Aluminum Machining
- Titanium Machining
- Stainless Steel Machining
- Copper Machining
- Brass Machining
- Super Alloy Machining
- Peek Machining
- UHMW Machining
- Unilate Machining
- PA6 Machining
- PPS Machining
- Teflon Machining
- Inconel Machining
- Tool Steel Machining
- More Material