The Role Of Coatings In Lost Foam Casting Production Process
2021-11-20
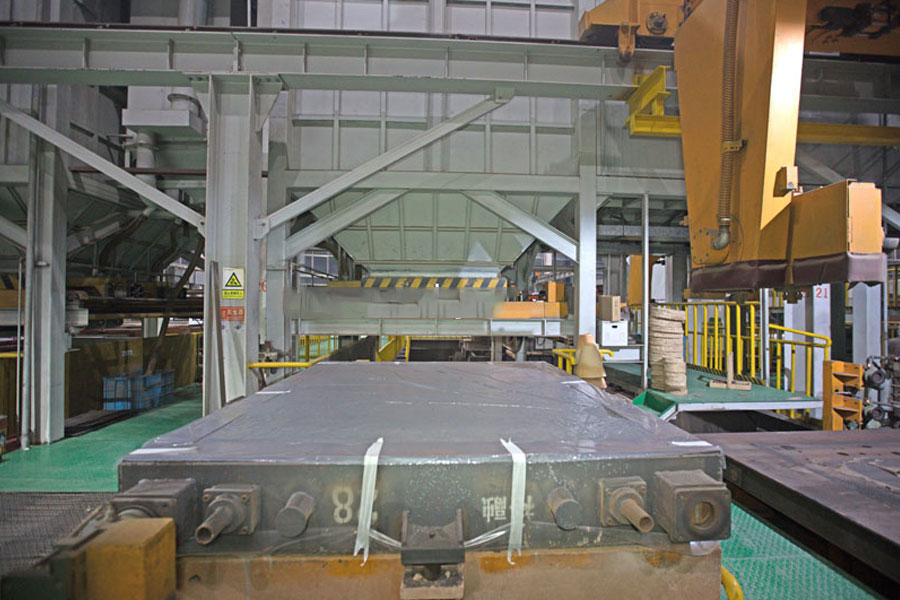
1. The role, basic composition and performance of the lost foam coating
(1) The main function of paint
- 1. The coating layer can improve the strength and rigidity of the foam pattern, and prevent the pattern from being damaged or deformed during handling, coating, sand filling, and vibration.
- 2. When pouring, the coating layer is the isolation medium between liquid metal and dry sand. The coating layer separates the molten metal from the filled sand to prevent the molten metal from penetrating into the sand, thereby ensuring smooth and clean surface castings without sand sticking. At the same time, it prevents dry sand from flowing into the gap between the molten metal and the foam, causing the mold to collapse.
- 3. The coating layer allows foam-type pyrolysis products (a large amount of gas or liquid, etc.) to smoothly escape into the filled sand and be sucked out instantaneously, preventing castings from producing defects such as pores, wrinkles, carbon increase, and residue. (Because the pouring temperature is different when pouring different alloys, the decomposition products of the foam type are very different. When pouring cast iron, cast steel and other ferrous metals, because the temperature is higher than 1350-1600℃, the pyrolysis products are mainly gaseous. The coating is required to have good air permeability. When the aluminum alloy is cast, the pyrolysis products are mainly liquid due to the low temperature of about 760-780°C. The liquid decomposition products are required to be wetted with the coating and smoothly penetrate into the coating. The layer is absorbed by the coating and discharged from the cavity.)
- 4. The coating has thermal insulation properties, which can avoid and reduce the heat loss of molten metal during the filling process, and improve the filling integrity rate of thin-walled parts.
(2) Basic composition of paint
Lost foam coatings are generally composed of refractory materials, binders, carriers (water, ethanol), surfactants, suspending agents, thixotropic agents and other additives. The various ingredients are uniformly mixed together and play a comprehensive role in the coating and pouring process.- 1. Refractory material (aggregate). As the name suggests, it is the backbone material in the coating, which determines the refractoriness, chemical stability, adsorption and thermal insulation properties of the coating. The coarse and fine particle size configuration and particle shape have a greater impact on the air permeability of the coating. The particle size should not be too fine, and the shape is preferably columnar and round, followed by flakes.
- 2. Binder. It is an indispensable additive to ensure that the lost foam coating has both higher strength and higher air permeability. There are mainly two kinds of organic and inorganic. Among them, organic binders (syrup, starch, dextrin, carboxymethyl cellulose CMC) can increase the strength of the coating at room temperature, and will be lost during the casting process, effectively improving the air permeability of the coating. Inorganic binders (nanobentonite, water glass, silica sol) can ensure the strength of the coating at room temperature and high temperature. It is usually necessary to use a variety of binders correctly to ensure and improve the performance of the coating.
- 3. Carrier. Water-based and alcohol-based (alcohol).
- 4. Surfactant (wetting agent). Mainly used to improve the coatability of water-based lost foam coatings. Molecules are amphiphilic molecules that can be both hydrophilic and lipophilic. When added to the paint, the hydrophilic end is combined with the water in the water-based paint, and the lipophilic end is attracted by the foam mold, making it oriented and arranged on the surface of the foam mold, like a bridge connecting the plastic mold and the paint.
- 5. Suspending agent. A substance added to prevent the precipitation of solid refractory materials in the coating. At the same time, it plays an important role in adjusting the rheology of the coating and improving the process performance of the coating. The corresponding selection is mainly based on the type of refractory material and the type of carrier. (The commonly used suspending agents for water-based coatings are: bentonite, attapulgite, sodium carboxymethyl cellulose, etc.. The commonly used suspending agents for organic solvent coatings are: organic bentonite, lithium bentonite, attapulgite, polyvinyl butyral PVB, etc.).
- 6. Thixotropic agent. Attapulgite soil. Thixotropy, under the action of a fixed shear rate, the viscosity of the coating gradually decreases with the extension of the shearing time (thinning), and the viscosity gradually recovers (thickening) with the extension of time after the shearing is stopped.
- 7. Other accessories. Defoamer, an additive that can eliminate bubbles in the coating (commonly used defoamers are: n-butanol, n-pentanol, n-octanol), the addition amount is 0.02%. Preservative is an additive to prevent fermentation, corruption and deterioration of water-based coatings (sodium benzoate is a preservative used in the food industry and has good safety). The addition amount is 0.02%-0.04%.
(3) The performance of the coating
Lost foam coatings should have the following properties: strength, air permeability, refractoriness, thermal insulation, rapid cold and heat resistance, moisture absorption, adsorption, easy cleaning, coating, dripping (leveling), suspension Wait. Can be broadly divided into two categories: work performance and process performance.- 1. Work performance. Including: strength, air permeability, refractoriness, thermal insulation, rapid cold and heat resistance, moisture absorption, adsorption, and easy cleaning. Among them, the most important properties are strength, air permeability, and refractoriness.
- 2. Process performance. Including: coating, dripping (leveling), suspension. Among them, the most important performance is coating and dripping (leveling). Because the foam model itself has non-wetting properties, the coatings are required to have good coating properties. Low dripping (leveling) is the main means to ensure uniform thickness of the coating and reduce waste and environmental pollution.The coating should have the process effect of "thick but not sticky" and "slip but not dripping".
- 3. Methods to improve coating performance.
2.The choice of lost foam coatings
(1) Chemical properties (pH)
- 1. Acidic cast iron and cast steel (carbon steel, low-alloy steel) should be selected corresponding acidic and neutral refractory materials such as kyanite, flake graphite, silica sand, etc.
- 2. Neutral High-alloy steel should correspond to weakly acidic and neutral refractory materials such as zirconium kyanite, corundum, zircon sand, and flake graphite.
- 3. Alkaline high manganese steel should be selected corresponding to alkaline refractory materials such as magnesia and forsterite.
- 4. Aluminum alloy should be selected correspondingly and other refractory materials
(2) Physical properties (pouring temperature)
Different requirements are put forward mainly according to factors such as gating system setting, process parameter setting, buried box group type, operating habits and proficiency, and on-site environment.3. Preparation and storage of paint
The equipment for coating preparation mainly includes rubber mill, ball mill, low-speed mixer, high-speed mixer, etc. Among them, the advantage of rubber mill and ball mill is that the components such as aggregate and binder can fully wet each other, and there are few bubbles involved. The disadvantages are inconvenient operation, long coating preparation time and high noise. High-speed mixers have gradually become the mainstream equipment for paint preparation. If you don't have a high-speed mixer, you can use a low-speed mixer to extend the mixing time to obtain the ideal compounding effect.(1) Coating preparation process
- 1. The purpose and function of high-speed mixing. Mix the powder and water thoroughly to make a uniform slurry. Through high-speed stirring, the fibers and powdery substances in the binder are subjected to shearing and discrete processing, which is convenient for full mixing. High speed mixing time is not less than 2 hours
- 2. The purpose and function of low-speed mixing. Remove the gas drawn into the paint due to high-speed stirring. Ensuring the strength of the coating helps to improve the surface quality of the casting. Stir at low speed for 2 hours or continuously.
(2) Quality control of paint
- 1. Density. Reflects the thinness of the coating, and also reflects the thickness of the coating during the coating process. It is an important quality index of coatings, and the density is generally used to control the production site. Measuring tool: hydrometer (Pomemeter)
- 2. PH value (acidity, alkalinity) of the coating. It is necessary to add a variety of organic binders and water to the coating. In order to ensure the stability of these organic substances and water, as well as the adaptability of the chemical properties of the coating to the molten metal, it should be controlled. It can be measured with PH test paper and PH meter.
- 3. Coating weight. The thickness of the coating can be estimated by weighing the weight of the model after two coatings and measuring the weight of the coating.
(3) Storage of paint
The paint is best prepared at any time and used in time. The remaining paint is easy to store in a cool place and should not be stored for a long time. Depending on the weather and the environment of the storage location, the general storage time in summer is 2-5 days, and the storage time in winter: 5-10 days. At the same time, fermentation or freezing should be avoided.4. Coating and precautions
(1) Coating method (brushing, dipping, showering, spraying) and scope of application
Brush: suitable for single-piece small batch production of medium and large shapes. Dipping and drenching: suitable for small shapes with large batches and complex shapes. Spray: Generally suitable for thin-walled or easily deformed and easily damaged shapes.(2) Reasonable choice of coating thickness
The coating thickness should be comprehensively set according to the needs of factors such as the type of molten metal, the structure of the casting, the complexity of the shape, the weight, the wall thickness, and the setting and selection of the gating system. For the mold sample, the thickness of the coating should be reduced as much as possible on the premise of ensuring the strength and erosion resistance of the coating to help improve the air permeability. Can choose between 0.3-3.5mm. For the gating system, the strength of the coating should be increased as much as possible, and the thickness of the coating should be appropriately increased, which can be selected between 3.5-6mm.(3) Matters needing attention
- 1. Make full use of the thixotropy of water-based coatings (the viscosity of the coating decreases during the stirring process, and the viscosity rises after the stirring stops). Under the condition of continuous stirring and temperature control, coating is carried out in order to obtain a uniform coating and reduce the deformation of the model.
- 2. Choose a suitable stirring speed. It can be controlled at 10-20 revolutions/min. If the rotating speed is too low, the paint may precipitate; if the rotating speed is too high, the paint will be engulfed in gas and produce bubbles.
- 3. Attention should be paid to reasonably control the position, angle, direction, speed, strength, etc. of the pattern immersed into the paint to prevent defects and problems such as deformation, damage, and bubbles.
- 4. For coating, ensure that the coating is uniform and completely cover all parts of the pattern.
- 5. Anti-deformation and anti-breakage should run through the whole process of coating and hanging. When placing the coated model, the effect of drying and the prevention of deformation and damage should be fully considered.
(4) Typical bad habits in painting operations
- 1. Shake. The coated model should be placed on the static shelf, and the paint will drip naturally in order to obtain a uniform and smooth coating. Although artificial shaking can increase the coating speed, at the same time, it will also destroy the uniformity and leveling of the coating, causing the coating to become thinner or accumulate locally. (Insert video)
- 2. Dew. It is also called "Lu Bai" as the saying goes. Part of the coating or a large area is not covered by paint, and no measures are taken to remedy it, and it is allowed to be transferred to the next process. This will cause the coating to become thinner and reduce the strength and other properties, which will affect the quality of castings. (Insert photo)
5. Drying of paint
(1) Drying method and equipment
Natural environmental protection method: Use open air drying or sun room, greenhouse heating and drying to achieve the effect of dehydration, dehumidification and drying. Heating and dehumidification method: A special drying room is used to increase and maintain the temperature of the drying room by burning coal, gas, electric power, geothermal, steam, etc., and special equipment is used to discharge moisture to achieve the effect of dehydration, dehumidification and drying.(2) Quality control of the drying process
- 1. Drying temperature. 35-50℃. Low-temperature drying can be used on the premise that the dehumidification effect and efficiency are guaranteed. At the same time, the drying temperature should not be set too high. When the temperature exceeds 50°C, the model is prone to problems such as softening and falling off of the colloid.
- 2. Heating rate. The heating speed should not be too fast, and it should be controlled at 5-10℃/hour. If the heating speed is too fast, the coating is prone to cracks, delamination or even peeling.
- 3. Drying time. Depending on the complexity and size of the specific drying equipment, environment and model, in general, the drying time of the first coating should be controlled for 8-12 hours or longer. The drying time of the second coating should be controlled within 16-24 hours or longer, and the drying time of the third coating should be controlled within 20-24 hours or longer. In principle, a weighing check should be carried out between each pass. After confirming that it is completely dry, the paint should be applied for the next time.
- 4. Coating repair and repair.
Link to this article:The Role Of Coatings In Lost Foam Casting Production Process
Reprint Statement: If there are no special instructions, all articles on this site are original. Please indicate the source for reprinting:www.cncmachiningptj.com
PTJ® provides a full range of Custom Precision cnc machining china services.ISO 9001:2015 &AS-9100 certified. 3, 4 and 5-axis rapid precision CNC machining services including milling, turning to customer specifications,Capable of metal & plastic machined parts with +/-0.005 mm tolerance.Secondary services include CNC and conventional grinding, drilling,die casting,sheet metal and stamping.Providing prototypes, full production runs, technical support and full inspection.Serves the automotive, aerospace, mold&fixture,led lighting,medical,bicycle, and consumer electronics industries. On-time delivery.Tell us a little about your project’s budget and expected delivery time. We will strategize with you to provide the most cost-effective services to help you reach your target,Welcome to Contact us ( sales@pintejin.com ) directly for your new project.
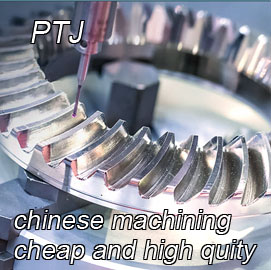
Our Services
- 5 Axis Machining
- Cnc Milling
- Cnc Turning
- Machining Industries
- Machining Process
- Surface Treatment
- Metal Machining
- Plastic Machining
- Powder Metallurgy Mold
- Die Casting
- Parts Gallery
Case Studies
- Auto Metal Parts
- Machinery Parts
- LED Heatsink
- Building Parts
- Mobile Parts
- Medical Parts
- Electronic Parts
- Tailored Machining
- Bicycle Parts
Material List
- Aluminum Machining
- Titanium Machining
- Stainless Steel Machining
- Copper Machining
- Brass Machining
- Super Alloy Machining
- Peek Machining
- UHMW Machining
- Unilate Machining
- PA6 Machining
- PPS Machining
- Teflon Machining
- Inconel Machining
- Tool Steel Machining
- More Material
Parts Gallery