How to choose a suitable cooling stack for plates?
Through water, air and cooling rollers, the extruded plastic can be cooled in many ways. Quench roll cooling is the easiest cooling calculation to define, but I still see a lot of ambiguity when choosing the roll stack for the sheet.
For sheet extrusion, there are usually some geometric changes in the vertical stacking of three rolls, and there may be some extra rolls for ultra-high-speed production lines with short contact times. In the sheet, since the polymer has a small contact area, the top roller only has a small cooling effect.
J-Stack designs like this are commonly used for PET, PETG, PS and PP.
When choosing the right paper stack for your application, there are four main aspects to consider: the overall cooling capacity, the product to be processed, the mechanical properties and the internal design of the roll. Consider only the cooling capacity, where the top roll sets the sheet thickness and its uniformity. Generally, less than 10% of the coil is in contact with the plastic, thereby minimizing the heat transfer area. The middle roll performs most of the cooling because about half of the middle circumference is covered by the polymer, where the plastic is the hottest, thereby transferring the heat to the cooled roll to the greatest extent. The third roller also has 50% or more of the circumference in contact with the plastic, but since a large amount of heat in the plastic enters the middle roller, the heat transfer rate of the third roller is generally much lower. However, since the third roller cools the side of the paper opposite to the middle roller, it is more effective for thicker paper. It takes time for heat to move on the paper, and the thicker the paper, the lower the percentage extracted on a particular paper roll.
According to different polymer properties, there are quite a few considerations for suitable roll sizing. In other words, there is no universal roller set. The cooling effect of the roll varies with polymer type, roll design and coolant. I will stick to the differences in polymers in this article because they have a significant effect on cooling. Heat transfer rate, specific heat and melt temperature are the main factors that determine the cooling rate.
Let's consider the comparison between the assembly line processing HIPS and the assembly line processing HDPE. The melt temperature of both is 375 degrees Fahrenheit, and the outlet temperature is both 120 degrees Fahrenheit. So in both cases, 375-120 = 255 degrees Fahrenheit, but if you multiply it by the specific heat of the polymer, the result is completely different.
HIPS: 255 F × 0.32 BTU/lb-°F = 81.6 BTU/lb
HDPE 255 F × 0.55 BTU/lb-°F = 140.3 BTU/lb
At the same output rate (lb/hr), HDPE has 72% more heat. However, the heat transfer rate of HDPE is more than twice that of HIPS. Therefore, even if more heat is transferred with HDPE, it passes through the sheet from the polymer to the surface of the roll at more than twice the speed. Although this means that the two polymers can be cooled at a similar rate, HDPE requires more coolant to achieve this goal.
Now let's compare HDPE and PP:
PP: 255 F × 0.52 BTU/lb-°F = 132.6 BTU/lb
HDPE: 255 F × 0.55 BTU/lb-°F = 140.3 BTU/lb
Their heat content is very close (0.55 vs. 0.52 BTU/lb-°F), but the heat transfer rate of PP is 60% of HDPE (0.15 vs. 0.09 BTU/Ft-Hr-°F). This means that under the same output, roll temperature and melt temperature, it will take 60% more time for the roll to obtain the same outlet temperature as HDPE.
In addition to these characteristics, melt density also plays a role when comparing on a pound/hour basis. In the case of HIPS and HDPE, the density of HIPS melt is 33% higher than that of HDPE, so the heat has a shorter propagation distance, eliminating the half advantage of HDPE in terms of heat transfer rate. In the comparison of PP/HDPE, the melt density of PP is slightly lower than that of HDPE, which makes the propagation distance of heat slightly larger and worsens the comparison.
Heat transfer rate, specific heat and melt temperature are the main factors that determine the cooling rate.
Due to the different thermal properties of polymers, there is no "universal" roll cooling equipment. Even the melt density of the polymer will affect the cooling effect of the roll due to the difference in the heat transfer rate. When the thermal properties of the polymer are combined with mechanical requirements, roll design/dimensions, and roll cooling systems, the choice of roll stack becomes a rather complicated issue.
This may be especially important for foreign-made or second-hand equipment, where experienced OEM expertise may not be available. When buying new or used equipment, make sure someone can evaluate the roll cooling effect based on your exact application.
Link to this article: How to choose a suitable cooling stack for plates?
Reprint Statement: If there are no special instructions, all articles on this site are original. Please indicate the source for reprinting:https://www.cncmachiningptj.com/,thanks!
PTJ® provides a full range of Custom Precision cnc machining china services.ISO 9001:2015 &AS-9100 certified. 3, 4 and 5-axis rapid precision CNC machining services including milling, sheet metal to customer specifications,Capable of metal & plastic machined parts with +/-0.005 mm tolerance.Secondary services include CNC and conventional grinding, laser cutting,drilling,die casting,sheet metal and stamping.Providing prototypes, full production runs, technical support and full inspection.Serves the automotive, aerospace, mold&fixture,led lighting,medical,bicycle, and consumer electronics industries. On-time delivery.Tell us a little about your project’s budget and expected delivery time. We will strategize with you to provide the most cost-effective services to help you reach your target,Welcome to Contact us ( sales@pintejin.com ) directly for your new project.
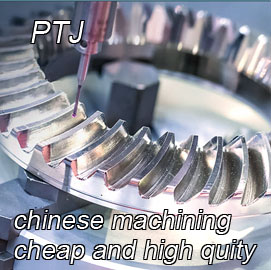
- 5 Axis Machining
- Cnc Milling
- Cnc Turning
- Machining Industries
- Machining Process
- Surface Treatment
- Metal Machining
- Plastic Machining
- Powder Metallurgy Mold
- Die Casting
- Parts Gallery
- Auto Metal Parts
- Machinery Parts
- LED Heatsink
- Building Parts
- Mobile Parts
- Medical Parts
- Electronic Parts
- Tailored Machining
- Bicycle Parts
- Aluminum Machining
- Titanium Machining
- Stainless Steel Machining
- Copper Machining
- Brass Machining
- Super Alloy Machining
- Peek Machining
- UHMW Machining
- Unilate Machining
- PA6 Machining
- PPS Machining
- Teflon Machining
- Inconel Machining
- Tool Steel Machining
- More Material