Nylon Material Properties and Applications in CNC and Other Machining Methods
Nylon, a family of synthetic polyamides, represents one of the most versatile and widely used engineering thermoplastics in modern manufacturing. First developed by Wallace Carothers at DuPont in the 1930s, nylon revolutionized industries with its exceptional mechanical properties, chemical resistance, and adaptability to various processing techniques, including computer numerical control (CNC) machining, injection molding, and additive manufacturing. Its applications span automotive, aerospace, consumer goods, and medical industries, owing to its strength, flexibility, and durability. This article explores the material properties of nylon, its behavior under different machining methods, and its diverse applications, with a focus on CNC machining. Detailed comparisons of nylon types, machining parameters, and performance metrics are provided in tabular form to facilitate a comprehensive understanding.
Historical Context and Development of Nylon
Nylon, introduced as nylon 6,6 in 1935, marked a significant milestone in polymer science. Its discovery emerged from DuPont’s research into synthetic fibers as a substitute for silk, leading to the commercialization of nylon stockings. Subsequent developments introduced variants such as nylon 6, nylon 11, and nylon 12, each tailored for specific properties and applications. The evolution of nylon paralleled advancements in machining technologies, particularly CNC, which enabled precise fabrication of complex nylon components. Today, nylon’s role extends beyond textiles to precision-engineered parts, leveraging its unique combination of toughness, low friction, and thermal stability.
Chemical and Molecular Structure of Nylon
Nylon is a polyamide characterized by repeating amide (–CONH–) linkages in its polymer chain. The nomenclature, such as nylon 6,6 or nylon 6, reflects the number of carbon atoms in the diamine and diacid monomers (for nylon 6,6) or the single monomer (for nylon 6). The molecular structure imparts key properties:
-
Crystallinity: Nylon’s semi-crystalline nature contributes to its strength and rigidity, with crystalline regions providing structural integrity and amorphous regions offering flexibility.
-
Hydrogen Bonding: Strong intermolecular hydrogen bonds between amide groups enhance tensile strength and thermal resistance.
-
Hydrophilicity: Nylon’s ability to absorb moisture affects its dimensional stability and mechanical properties, a critical consideration in machining.
The molecular weight and degree of polymerization influence nylon’s viscosity and processability, impacting its suitability for CNC and other machining methods.
Types of Nylon and Their Properties
Nylon exists in multiple grades, each engineered for specific performance characteristics. The most common types include:
-
Nylon 6,6: Known for high tensile strength, abrasion resistance, and thermal stability, suitable for gears and bearings.
-
Nylon 6: Offers good toughness and flexibility, often used in injection molding and extrusion.
-
Nylon 11 and 12: Exhibit lower moisture absorption and better chemical resistance, ideal for harsh environments.
-
Filled Nylons: Reinforced with glass fibers, carbon fibers, or lubricants like molybdenum disulfide to enhance strength, stiffness, or lubricity.
Table 1: Properties of Common Nylon Types
Nylon Type |
Tensile Strength (MPa) |
Flexural Modulus (GPa) |
Melting Point (°C) |
Moisture Absorption (%) |
Key Applications |
---|---|---|---|---|---|
Nylon 6,6 |
80–100 |
2.8–3.2 |
255–265 |
1.0–2.5 |
Gears, bearings, automotive parts |
Nylon 6 |
60–85 |
2.5–3.0 |
215–225 |
1.3–3.0 |
Consumer goods, molded parts |
Nylon 11 |
50–70 |
1.2–1.8 |
185–195 |
0.3–0.9 |
Flexible tubing, cables |
Nylon 12 |
45–65 |
1.0–1.6 |
175–185 |
0.2–0.7 |
Medical devices, hoses |
Glass-Filled Nylon 6,6 |
120–200 |
5.0–9.0 |
255–265 |
0.8–2.0 |
Structural components |
Mechanical Properties of Nylon
Nylon’s mechanical properties make it a preferred material for machining:
-
Tensile Strength: Ranges from 45 MPa (nylon 12) to over 200 MPa (glass-filled nylon 6,6), suitable for load-bearing applications.
-
Impact Resistance: High toughness, especially in unfilled grades, allows nylon to absorb energy without fracturing.
-
Fatigue Resistance: Excellent resistance to cyclic loading, ideal for dynamic components like gears.
-
Friction and Wear: Low coefficient of friction, especially in lubricated grades, reduces wear in sliding applications.
Moisture absorption, however, can reduce tensile strength and modulus by up to 30%, necessitating controlled machining environments.
Thermal and Chemical Properties
Nylon’s thermal properties vary by type:
-
Melting Point: Ranges from 175°C (nylon 12) to 265°C (nylon 6,6), affecting machining parameters like cutting speed.
-
Thermal Conductivity: Low, typically 0.25–0.35 W/m·K, requiring careful heat management during machining.
-
Chemical Resistance: Resists oils, greases, and most solvents but is susceptible to strong acids and bases.
These properties dictate tool selection and coolant use in CNC machining to prevent thermal degradation or chemical interactions.
CNC Machining of Nylon
CNC machining, encompassing milling, turning, and drilling, is widely used to fabricate nylon components with high precision. Nylon’s machinability stems from its toughness and low thermal conductivity, but challenges include:
-
Heat Generation: Excessive heat can cause melting or deformation, requiring low cutting speeds and effective cooling.
-
Tool Wear: Abrasive fillers like glass fibers increase tool wear, necessitating carbide or diamond-coated tools.
-
Dimensional Stability: Moisture absorption can lead to warping, requiring dry storage and machining conditions.
CNC Milling
Milling involves rotating tools to remove material, creating complex shapes like slots and pockets. For nylon:
-
Cutting Speeds: Typically 100–300 m/min, adjusted for filled grades to minimize heat buildup.
-
Feed Rates: 0.1–0.3 mm/rev for smooth finishes, higher for roughing cuts.
-
Tool Geometry: Sharp, high-rake-angle tools reduce cutting forces and heat.
CNC Turning
Turning produces cylindrical parts like bushings and rollers. Key considerations:
-
Spindle Speeds: 500–1500 RPM, lower for filled nylons to avoid tool wear.
-
Coolants: Minimal or dry machining preferred to prevent moisture absorption.
-
Clamping: Soft jaws prevent deformation of flexible nylon parts.
CNC Drilling
Drilling creates holes for fasteners or fittings. Challenges include:
-
Chip Evacuation: Nylon’s stringy chips require peck drilling to clear debris.
-
Drill Bit Selection: High-speed steel (HSS) or carbide bits with polished flutes reduce friction.
-
Hole Quality: Low feed rates ensure smooth, accurate holes without burrs.
Table 2: CNC Machining Parameters for Nylon
Process |
Cutting Speed (m/min) |
Feed Rate (mm/rev) |
Tool Material |
Coolant |
Notes |
---|---|---|---|---|---|
Milling |
100–300 |
0.1–0.3 |
Carbide, Diamond |
Dry or Air |
Use sharp tools to minimize heat |
Turning |
150–400 |
0.05–0.25 |
Carbide, HSS |
Dry |
Soft jaws for clamping |
Drilling |
50–200 |
0.02–0.1 |
HSS, Carbide |
Dry or Mist |
Peck drilling for chip removal |
Other Machining Methods for Nylon
Beyond CNC, nylon is processed using various methods:
-
Injection Molding: Produces high-volume, complex parts with tight tolerances. Nylon’s low viscosity aids mold filling, but shrinkage (1–2%) requires precise mold design.
-
Extrusion: Used for rods, tubes, and profiles. Nylon 6 and 12 are common due to their melt flow properties.
-
Additive Manufacturing: Fused deposition modeling (FDM) and selective laser sintering (SLS) use nylon powders or filaments for prototyping and small-batch production.
-
Laser Cutting: Suitable for thin nylon sheets, though thermal sensitivity limits its use.
-
Waterjet Cutting: Effective for thick nylon parts, offering cold cutting to avoid thermal distortion.
Each method leverages nylon’s properties differently, with CNC offering superior precision for custom parts and injection molding excelling in mass production.
Applications of Nylon in CNC Machining
Nylon’s versatility enables its use in diverse CNC-machined components:
-
Automotive: Gears, bushings, and fuel system components benefit from nylon’s strength and chemical resistance.
-
Aerospace: Lightweight, durable parts like insulators and fittings, often using glass-filled nylon for added stiffness.
-
Medical: Biocompatible grades (e.g., nylon 12) are used for surgical guides and tubing.
-
Consumer Goods: Handles, connectors, and sporting equipment leverage nylon’s toughness and aesthetics.
-
Industrial: Rollers, pulleys, and wear pads utilize nylon’s low friction and durability.
Table 3: Nylon Applications by Industry
Industry |
Component |
Nylon Type |
Key Properties |
Machining Method |
---|---|---|---|---|
Automotive |
Gears |
Nylon 6,6, Glass-Filled |
High strength, wear resistance |
CNC Milling, Turning |
Aerospace |
Insulators |
Nylon 11 |
Low moisture absorption |
CNC Milling |
Medical |
Tubing |
Nylon 12 |
Biocompatibility, flexibility |
Extrusion, CNC Drilling |
Consumer Goods |
Handles |
Nylon 6 |
Toughness, aesthetics |
Injection Molding, CNC |
Industrial |
Wear Pads |
Lubricated Nylon |
Low friction, durability |
CNC Milling |
Challenges and Limitations in Machining Nylon
Machining nylon presents several challenges:
-
Moisture Sensitivity: Absorbed water (up to 8% by weight in nylon 6) causes swelling and reduced strength, requiring controlled environments.
-
Thermal Management: Low thermal conductivity leads to heat buildup, risking melting or poor surface finish.
-
Filler Abrasiveness: Glass or carbon-filled nylons accelerate tool wear, increasing costs.
-
Chip Control: Stringy chips can clog tools, necessitating optimized feed rates and chip-breaking techniques.
Mitigation strategies include using sharp tools, low cutting speeds, and dry machining to minimize moisture effects.
Advances in Nylon Machining Technologies
Recent innovations enhance nylon’s machinability:
-
Cryogenic Cooling: Liquid nitrogen reduces heat buildup, improving surface finish and tool life.
-
Hybrid Manufacturing: Combining CNC with additive manufacturing allows complex geometries with minimal waste.
-
Tool Coatings: Diamond-like carbon (DLC) coatings reduce friction and wear when machining filled nylons.
-
Automation: CNC machines with real-time monitoring adjust parameters to optimize nylon processing.
These advancements expand nylon’s applications in high-precision industries like aerospace and medical devices.
Environmental and Sustainability Considerations
Nylon production and machining raise environmental concerns:
-
Energy Consumption: High energy requirements for polymerization and machining contribute to carbon footprints.
-
Recyclability: Nylon is recyclable, but filled grades are challenging to reprocess due to fiber degradation.
-
Biodegradable Alternatives: Research into bio-based polyamides aims to reduce reliance on petroleum-based nylon.
Sustainable practices, such as using recycled nylon and optimizing machining to reduce waste, are gaining traction.
Future Trends in Nylon and Machining
Emerging trends include:
-
Nanocomposite Nylons: Incorporating nanoparticles to enhance strength and thermal properties.
-
Smart Machining: AI-driven CNC systems optimize parameters for nylon, reducing waste and improving efficiency.
-
Bio-Based Nylons: Derived from renewable sources, offering eco-friendly alternatives for machining.
-
4D Printing: Nylon’s flexibility enables shape-changing parts in additive manufacturing.
These developments promise to expand nylon’s role in advanced manufacturing.
Conclusion
Nylon’s unique combination of mechanical, thermal, and chemical properties makes it a cornerstone of modern manufacturing, particularly in CNC machining. Its versatility across industries, from automotive to medical, underscores its importance. While challenges like moisture sensitivity and tool wear persist, advancements in machining technologies and material formulations continue to enhance nylon’s utility. The tables provided offer a detailed comparison of nylon types, machining parameters, and applications, serving as a valuable resource for engineers and manufacturers. As sustainable practices and innovative technologies evolve, nylon’s role in precision engineering is poised to grow, solidifying its status as a critical material in the 21st century.
Reprint Statement: If there are no special instructions, all articles on this site are original. Please indicate the source for reprinting:https://www.cncmachiningptj.com/,thanks!
PTJ® provides a full range of Custom Precision cnc machining china services.ISO 9001:2015 &AS-9100 certified. 3, 4 and 5-axis rapid precision CNC machining services including milling, turning to customer specifications,Capable of metal & plastic machined parts with +/-0.005 mm tolerance.Secondary services include CNC and conventional grinding, drilling,die casting,sheet metal and stamping.Providing prototypes, full production runs, technical support and full inspection.Serves the automotive, aerospace, mold&fixture,led lighting,medical,bicycle, and consumer electronics industries. On-time delivery.Tell us a little about your project's budget and expected delivery time. We will strategize with you to provide the most cost-effective services to help you reach your target,Welcome to Contact us ( sales@pintejin.com ) directly for your new project.
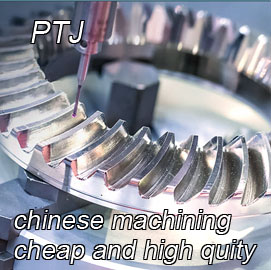
- 5 Axis Machining
- Cnc Milling
- Cnc Turning
- Machining Industries
- Machining Process
- Surface Treatment
- Metal Machining
- Plastic Machining
- Powder Metallurgy Mold
- Die Casting
- Parts Gallery
- Auto Metal Parts
- Machinery Parts
- LED Heatsink
- Building Parts
- Mobile Parts
- Medical Parts
- Electronic Parts
- Tailored Machining
- Bicycle Parts
- Aluminum Machining
- Titanium Machining
- Stainless Steel Machining
- Copper Machining
- Brass Machining
- Super Alloy Machining
- Peek Machining
- UHMW Machining
- Unilate Machining
- PA6 Machining
- PPS Machining
- Teflon Machining
- Inconel Machining
- Tool Steel Machining
- More Material