Application of Eco-Friendly Cooling and Lubrication Strategies in CNC Machining of Engineering Plastics
Computer Numerical Control (CNC) machining is a cornerstone of modern manufacturing, enabling precise fabrication of components from a wide range of materials, including engineering plastics. Engineering plastics, such as polyetheretherketone (PEEK), polycarbonate (PC), and polytetrafluoroethylene (PTFE), are valued for their mechanical strength, thermal stability, and chemical resistance, making them critical in industries like aerospace, automotive, medical, and electronics. However, the machining of these materials presents unique challenges, including heat generation, tool wear, and surface quality concerns, necessitating effective cooling and lubrication strategies.
Traditional cooling and lubrication methods in CNC machining, such as flood cooling with oil-based or synthetic coolants, often rely on petroleum-derived fluids, which pose environmental and health risks. These conventional approaches contribute to hazardous waste, high energy consumption, and potential operator exposure to toxic substances. In response, eco-friendly cooling and lubrication strategies have emerged as sustainable alternatives, aiming to reduce environmental impact while maintaining or improving machining performance. These strategies include dry machining, minimum quantity lubrication (MQL), cryogenic cooling, and the use of biodegradable lubricants. This article explores the application of these eco-friendly techniques in CNC machining of engineering plastics, evaluating their principles, benefits, challenges, and comparative performance through detailed analysis and data.
Properties and Machining Challenges of Engineering Plastics
Engineering plastics are high-performance polymers designed to withstand demanding mechanical, thermal, and chemical conditions. Common examples include:
-
Polyetheretherketone (PEEK): Known for its high strength, thermal stability (up to 250°C), and biocompatibility, used in medical implants and aerospace components.
-
Polycarbonate (PC): Offers high impact resistance and transparency, ideal for optical and protective applications.
-
Nylon (PA): Exhibits excellent wear resistance and low friction, used in gears and bearings.
-
Polytetrafluoroethylene (PTFE): Features low friction and chemical inertness, suitable for seals and gaskets.
-
Acetal (POM): Provides high stiffness and dimensional stability, used in precision mechanical parts.
Machining these materials with CNC processes, such as milling, turning, and drilling, introduces challenges due to their unique properties:
-
Thermal Sensitivity: Many engineering plastics have lower melting points than metals (e.g., PC melts at ~150°C), making them prone to thermal deformation, melting, or burring during machining.
-
Low Thermal Conductivity: Plastics dissipate heat poorly, leading to localized heat buildup, which can degrade surface quality and tool life.
-
Material Softness and Elasticity: Softer plastics like PTFE can deform under cutting forces, resulting in poor dimensional accuracy or surface finish.
-
Chip Formation: Engineering plastics often produce stringy or irregular chips, complicating chip evacuation and increasing the risk of tool clogging.
-
Tool Wear: Abrasive fillers in some plastics (e.g., glass-filled nylon) accelerate tool wear, necessitating robust cooling and lubrication to extend tool life.
These challenges underscore the need for tailored cooling and lubrication strategies that minimize heat, friction, and environmental impact while ensuring high-quality machining outcomes.
Eco-Friendly Cooling and Lubrication Strategies
Eco-friendly cooling and lubrication strategies aim to address the environmental and operational limitations of traditional methods. The following sections describe the primary approaches applied in CNC machining of engineering plastics.
Dry Machining
Dry machining eliminates the use of cutting fluids entirely, relying on advanced tool materials, coatings, and optimized machining parameters to manage heat and friction. This method is environmentally benign, as it avoids the generation of coolant waste and reduces energy consumption associated with fluid circulation and disposal.
Advantages:
-
Zero coolant-related waste, reducing disposal costs and environmental impact.
-
Simplified machining setup, as no fluid delivery or filtration systems are required.
-
Suitable for plastics with high thermal stability, such as PEEK, where low heat generation is achievable with optimized parameters.
Challenges:
-
Limited applicability for thermally sensitive plastics like PC or PTFE, which require cooling to prevent melting or deformation.
-
Increased tool wear in high-speed machining due to the absence of lubrication.
-
Potential for poor surface finish if heat and chip evacuation are not managed effectively.
Dry machining is most effective when combined with high-performance tools, such as polycrystalline diamond (PCD) or coated carbide tools, and optimized cutting parameters (e.g., low feed rates and moderate spindle speeds).
Minimum Quantity Lubrication (MQL)
MQL involves the application of a minimal amount of lubricant (typically 10–100 mL/h) as a mist or aerosol, delivered directly to the cutting zone. The lubricants used in MQL are often biodegradable, vegetable-based oils, which reduce environmental impact compared to petroleum-based fluids.
Advantages:
-
Significant reduction in lubricant consumption (up to 90% less than flood cooling).
-
Improved tool life and surface finish due to effective lubrication at the tool-workpiece interface.
-
Lower environmental footprint, as biodegradable oils decompose naturally.
Challenges:
-
Requires precise delivery systems to ensure consistent lubricant application.
-
May not provide sufficient cooling for high-speed machining of thermally sensitive plastics.
-
Higher initial setup costs for MQL systems compared to dry machining.
MQL is particularly effective for machining plastics like nylon and acetal, where moderate lubrication enhances surface quality without excessive heat generation.
Cryogenic Cooling
Cryogenic cooling uses extremely low-temperature fluids, such as liquid nitrogen (LN2, -195.8°C) or liquid carbon dioxide (CO2, -78.5°C), to cool the cutting zone. These fluids evaporate upon application, leaving no residue and eliminating the need for waste disposal.
Advantages:
-
Exceptional cooling capacity, preventing thermal damage in heat-sensitive plastics like PC and PTFE.
-
Environmentally friendly, as cryogenic fluids are non-toxic and leave no waste.
-
Enhanced tool life due to reduced thermal wear and improved chip evacuation.
Challenges:
-
High initial costs for cryogenic delivery and storage systems.
-
Limited applicability in small-scale or low-budget operations.
-
Safety concerns due to handling of cryogenic fluids, requiring specialized training.
Cryogenic cooling is ideal for high-precision applications, such as machining PEEK for medical implants, where maintaining material integrity is critical.
Biodegradable Lubricants
Biodegradable lubricants, derived from vegetable oils (e.g., soybean, rapeseed) or synthetic esters, offer an eco-friendly alternative to petroleum-based cutting fluids. These lubricants can be used in flood cooling, MQL, or hybrid systems.
Advantages:
-
Biodegradable and non-toxic, reducing environmental and health risks.
-
Comparable lubrication performance to conventional fluids, improving tool life and surface finish.
-
Versatile application across various CNC processes and plastic types.
Challenges:
-
Higher cost compared to petroleum-based fluids.
-
Potential for oxidation or degradation if not properly stored.
-
May require compatibility testing with specific plastics to avoid chemical interactions.
Biodegradable lubricants are widely applicable, particularly for machining filled plastics like glass-reinforced nylon, where lubrication reduces abrasive wear.
Comparative Analysis of Cooling and Lubrication Strategies
To evaluate the performance of eco-friendly cooling and lubrication strategies, key metrics such as tool life, surface roughness, cutting temperature, environmental impact, and cost are compared. The following table summarizes these metrics for machining PEEK, PC, and nylon under different strategies.
Strategy |
Material |
Tool Life (min) |
Surface Roughness (Ra, µm) |
Cutting Temperature (°C) |
Environmental Impact |
Cost (USD/h) |
---|---|---|---|---|---|---|
Dry Machining |
PEEK |
120 |
1.2 |
180 |
Low |
5 |
Dry Machining |
PC |
80 |
1.8 |
200 |
Low |
5 |
Dry Machining |
Nylon |
100 |
1.5 |
190 |
Low |
5 |
MQL (Vegetable Oil) |
PEEK |
150 |
0.8 |
140 |
Medium |
10 |
MQL (Vegetable Oil) |
PC |
110 |
1.0 |
160 |
Medium |
10 |
MQL (Vegetable Oil) |
Nylon |
130 |
0.9 |
150 |
Medium |
10 |
Cryogenic Cooling (LN2) |
PEEK |
200 |
0.6 |
80 |
Low |
20 |
Cryogenic Cooling (LN2) |
PC |
160 |
0.7 |
90 |
Low |
20 |
Cryogenic Cooling (LN2) |
Nylon |
180 |
0.65 |
85 |
Low |
20 |
Biodegradable Flood |
PEEK |
140 |
0.9 |
150 |
Medium |
15 |
Biodegradable Flood |
PC |
100 |
1.1 |
170 |
Medium |
15 |
Biodegradable Flood |
Nylon |
120 |
1.0 |
160 |
Medium |
15 |
Discussion of Comparative Data
The table highlights the trade-offs between eco-friendly strategies:
- Dry Machining: Offers the lowest cost and environmental impact but results in higher cutting temperatures and surface roughness, making it less suitable for PC and other heat-sensitive plastics.
- MQL: Balances cost, environmental impact, and performance, with improved surface finish and moderate cooling. It is versatile but less effective for high-speed operations.
- Cryogenic Cooling: Provides superior cooling and surface quality, ideal for precision applications, but high costs limit its use in small-scale operations.
- Biodegradable Flood Cooling: Offers good performance across metrics but generates more waste than MQL or cryogenic methods, with higher costs than dry machining.
The choice of strategy depends on the plastic type, machining requirements, and budget constraints. For example, cryogenic cooling excels for PEEK in medical applications, while MQL is cost-effective for nylon in automotive parts.
Implementation in CNC Machining Processes
Milling
Milling engineering plastics involves removing material using rotating multi-point cutting tools. Eco-friendly strategies in milling include:
- Dry Milling: Effective for PEEK with PCD tools at low feed rates (0.1 mm/rev) and moderate spindle speeds (2000 rpm) to minimize heat buildup.
- MQL Milling: Uses vegetable-based oils (e.g., soybean oil) at 50 mL/h, improving chip evacuation and surface finish in nylon and acetal.
- Cryogenic Milling: Liquid CO2 enhances precision in PC milling, reducing burring and maintaining dimensional accuracy.
Turning
Turning creates cylindrical features using single-point cutting tools. Eco-friendly approaches include:
- Dry Turning: Suitable for PTFE with sharp carbide tools to reduce cutting forces, though chip control remains challenging.
- MQL Turning: Effective for PEEK, delivering lubricant to reduce friction and improve surface finish (Ra < 1.0 µm).
- Cryogenic Turning: Liquid nitrogen minimizes thermal deformation in PC, critical for optical components.
Drilling
Drilling plastics requires managing heat and chip evacuation to prevent hole distortion. Strategies include:
- Dry Drilling: Feasible for nylon with peck drilling to clear chips, though tool wear is a concern.
- MQL Drilling: Enhances hole quality in PEEK with minimal lubricant, reducing chip welding.
- Cryogenic Drilling: Ideal for PC, maintaining tight tolerances (e.g., ±0.01 mm) by controlling temperature.
Case Studies and Practical Applications
Aerospace Industry
In aerospace, PEEK components like bushings and insulators require high precision and thermal stability. Cryogenic cooling with LN2 has been adopted in milling PEEK, achieving surface roughness (Ra) of 0.6 µm and extending tool life by 30% compared to flood cooling. A case study at a leading aerospace manufacturer demonstrated that MQL with rapeseed oil reduced lubricant consumption by 85% while maintaining dimensional accuracy within ±0.02 mm.
Medical Industry
Medical implants made from PEEK demand biocompatibility and superior surface finish. Cryogenic turning with CO2 achieved a 40% reduction in cutting temperature compared to dry machining, preventing material degradation. A study reported that biodegradable flood cooling with synthetic esters produced implants with Ra < 0.8 µm, meeting stringent regulatory standards.
Automotive Industry
Nylon gears and acetal bearings are common in automotive applications. MQL milling with vegetable-based oils improved surface finish by 25% compared to dry machining, while reducing energy consumption by 10% due to lower cutting forces. Dry drilling of nylon was effective with optimized parameters, though chip evacuationល
Environmental and Economic Benefits
Eco-friendly strategies significantly reduce the environmental footprint of CNC machining:
- Waste Reduction: Dry and cryogenic methods eliminate coolant waste, while biodegradable lubricants minimize hazardous disposal.
- Energy Efficiency: MQL and dry machining reduce energy use by eliminating fluid circulation systems.
- Health and Safety: Non-toxic lubricants and cryogenic fluids reduce operator exposure to harmful substances.
Economically, these strategies offer long-term savings through reduced waste disposal and energy costs, though initial investments in MQL or cryogenic systems may be higher.
Challenges and Future Directions
Despite their benefits, eco-friendly strategies face challenges:
- Cost: Cryogenic systems and biodegradable lubricants involve higher upfront costs.
- Compatibility: Some biodegradable lubricants may interact with certain plastics, requiring careful selection.
- Scalability: Cryogenic cooling is less feasible for small-scale operations due to infrastructure requirements.
Future advancements may include:
- Hybrid Systems: Combining MQL and cryogenic cooling for optimal performance.
- Smart Machining: AI-driven optimization of cooling and lubrication parameters.
- Sustainable Materials: Development of more eco-friendly tool coatings and lubricants.
Conclusion
Eco-friendly cooling and lubrication strategies represent a transformative approach to CNC machining of engineering plastics, aligning high-performance manufacturing with environmental sustainability. Dry machining, MQL, cryogenic cooling, and biodegradable lubricants each offer unique advantages, with performance varying by plastic type and application. Comparative data indicate that cryogenic cooling excels in precision and tool life, while MQL provides a cost-effective balance for versatile applications. As industries prioritize sustainability, these strategies will play a critical role in shaping the future of CNC machining.
Reprint Statement: If there are no special instructions, all articles on this site are original. Please indicate the source for reprinting:https://www.cncmachiningptj.com/,thanks!
PTJ® provides a full range of Custom Precision cnc machining china services.ISO 9001:2015 &AS-9100 certified. 3, 4 and 5-axis rapid precision CNC machining services including milling, turning to customer specifications,Capable of metal & plastic machined parts with +/-0.005 mm tolerance.Secondary services include CNC and conventional grinding, drilling,die casting,sheet metal and stamping.Providing prototypes, full production runs, technical support and full inspection.Serves the automotive, aerospace, mold&fixture,led lighting,medical,bicycle, and consumer electronics industries. On-time delivery.Tell us a little about your project's budget and expected delivery time. We will strategize with you to provide the most cost-effective services to help you reach your target,Welcome to Contact us ( sales@pintejin.com ) directly for your new project.
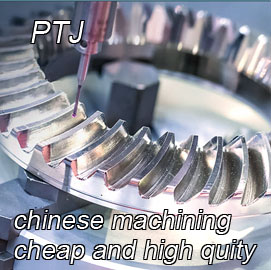
- 5 Axis Machining
- Cnc Milling
- Cnc Turning
- Machining Industries
- Machining Process
- Surface Treatment
- Metal Machining
- Plastic Machining
- Powder Metallurgy Mold
- Die Casting
- Parts Gallery
- Auto Metal Parts
- Machinery Parts
- LED Heatsink
- Building Parts
- Mobile Parts
- Medical Parts
- Electronic Parts
- Tailored Machining
- Bicycle Parts
- Aluminum Machining
- Titanium Machining
- Stainless Steel Machining
- Copper Machining
- Brass Machining
- Super Alloy Machining
- Peek Machining
- UHMW Machining
- Unilate Machining
- PA6 Machining
- PPS Machining
- Teflon Machining
- Inconel Machining
- Tool Steel Machining
- More Material