Study on CNC Machining Mechanism and Surface Quality Control of Polyimide-Based High-Performance Polymers for Aerospace Thermal Structures
Polyimides (PIs) are a class of high-performance polymers renowned for their exceptional thermal stability, mechanical strength, and chemical resistance, making them indispensable in demanding applications such as aerospace thermal structures. These materials, characterized by imide linkages in their backbone, exhibit remarkable properties, including high glass transition temperatures (Tg > 300°C), low thermal expansion, and resistance to extreme environments, which are critical for aerospace components like engine housings, thermal shielding, and insulation layers. The increasing adoption of polyimides in aerospace is driven by their ability to replace heavier metallic and ceramic materials, offering significant weight savings that reduce launch costs and enhance fuel efficiency. For instance, it is estimated that reducing 1 pound of spacecraft weight can save between $5,000 and $30,000 in launch costs, underscoring the economic and functional advantages of polyimides.
Computer Numerical Control (CNC) machining has emerged as a pivotal manufacturing technique for shaping polyimide-based components with high precision, particularly in aerospace applications where tight tolerances and superior surface quality are paramount. CNC machining, encompassing processes like milling, turning, and ultra-precision fly-cutting, enables the fabrication of complex geometries with submicron accuracy. However, machining polyimides presents unique challenges due to their high hardness, thermal stability, and sensitivity to machining parameters, which can affect surface integrity and performance. Achieving optimal surface quality is critical, as surface roughness and defects like burrs or microcracks can compromise the thermal and mechanical performance of aerospace components.
This article provides a comprehensive exploration of the CNC machining mechanisms for polyimide-based high-performance polymers, focusing on their application in aerospace thermal structures. It examines the material properties of polyimides, the mechanics of CNC machining processes, and strategies for surface quality control. The study integrates recent research findings, experimental data, and theoretical models to offer a detailed understanding of machining polyimides, supported by comparative tables that highlight key parameters and outcomes. The discussion is structured to address the material science, machining techniques, surface quality metrics, and practical applications, providing a holistic perspective for researchers, engineers, and industry professionals.
Polyimide Material Properties and Aerospace Applications
Chemical and Structural Characteristics
Polyimides are high-performance polymers containing imide linkages (-CO-N-CO-) in their backbone, often combined with aromatic or heterocyclic structures, which confer exceptional thermal and mechanical properties. The molecular structure of polyimides, typically synthesized via polycondensation of dianhydrides and diamines, results in strong intermolecular forces and high bond energy, contributing to their resistance to thermal degradation and chemical attack. Common polyimides, such as DuPont’s Vespel SP-1 and NASA’s PMR-15, exhibit glass transition temperatures ranging from 300°C to over 400°C, with decomposition temperatures between 500°C and 600°C. The incorporation of flexible groups (e.g., –O–) or alicyclic structures enhances solubility but may compromise thermal and mechanical properties, necessitating careful molecular design to balance performance attributes.
Polyimides are available in various forms, including films, fibers, foams, and composites, each tailored for specific applications. For aerospace thermal structures, polyimide films and composites are particularly valued for their low density (0.35–1.5 g/cm³), high tensile strength, and low outgassing rates, which prevent contamination in vacuum environments. The addition of nanofillers, such as carbon nanotubes (CNTs) or graphene oxide, further enhances mechanical and thermal properties, enabling the development of multifunctional composites for aerospace applications.
Key Properties for Aerospace
Polyimides possess a unique combination of properties that make them ideal for aerospace thermal structures:
-
Thermal Stability: Polyimides can withstand continuous temperatures above 300°C, with some formulations like DMBZ-15 operating up to 335°C (635°F). This makes them suitable for engine components, thermal shielding, and spacecraft structures exposed to extreme heat during launch and reentry.
-
Mechanical Strength: Polyimides exhibit high tensile strength, modulus, and toughness, enabling them to endure mechanical stresses in load-bearing and non-load-bearing components.
-
Chemical Resistance: Their resistance to acids, bases, and solvents ensures durability in corrosive environments, such as those encountered in aerospace propulsion systems.
-
Low Outgassing: Polyimides have low outgassing rates, critical for preventing contamination of sensitive equipment in space environments.
-
Dielectric Properties: With a dielectric constant of 3.4–3.5, polyimides are excellent electrical insulators, used in flexible circuits and insulation layers.
-
Radiation Resistance: Polyimides resist degradation from radiation, making them suitable for space applications where exposure to cosmic radiation is a concern.
Aerospace Applications
Polyimides are integral to aerospace thermal structures, including:
-
Engine Components: Polyimide composites, such as PMR-15 and DMBZ-15, are used in engine shrouds, nozzle flaps, and bushings due to their ability to maintain mechanical properties at high temperatures.
-
Thermal Insulation: Polyimide foams and aerogels provide lightweight, flame-resistant insulation for aircraft and spacecraft, with thermal conductivities as low as 0.029 W/mK.
-
Structural Composites: Carbon fiber-reinforced polyimide composites offer high strength-to-weight ratios, used in non-load-bearing components like vent tubes and thermal protection systems.
-
Flexible Electronics: Polyimide films serve as substrates for flexible printed circuits and sensors, leveraging their dielectric properties and thermal stability.
The ability to tailor polyimide properties through molecular design and composite reinforcement has expanded their applications, but their machinability remains a critical factor in achieving the precision required for aerospace components.
CNC Machining of Polyimides
Overview of CNC Machining
CNC machining is a subtractive manufacturing process that uses computer-controlled tools to remove material from a workpiece, achieving precise geometries and surface finishes. For polyimides, CNC machining techniques such as milling, turning, and ultra-precision fly-cutting are employed to fabricate components with tight tolerances and high surface quality. The process involves several stages, including tool selection, parameter optimization, and post-processing, each of which influences the final component’s performance.
Polyimides, despite their excellent properties, pose challenges in CNC machining due to their high hardness, thermal stability, and tendency to generate heat during cutting. These factors can lead to tool wear, surface defects, and thermal damage if not properly managed. Recent studies have focused on optimizing machining parameters and developing advanced techniques like single point diamond turning (SPDT) and ultra-precision fly-cutting (UPFC) to enhance machinability and surface quality.
Machining Mechanisms
The machining mechanism of polyimides involves complex interactions between the cutting tool, workpiece material, and machining environment. Key aspects include:
-
Material Removal: Polyimides are typically machined using shear or ductile cutting mechanisms, where the tool removes material by shearing or plastic deformation. The high hardness and elastic modulus of polyimides (nanoindentation hardness ~0.3–0.5 GPa, elastic modulus ~3–4 GPa) require sharp, durable tools like diamond or carbide to minimize tool wear and achieve clean cuts.
-
Thermal Effects: The low thermal conductivity of polyimides (0.029–0.35 W/mK) causes heat buildup at the tool-workpiece interface, potentially leading to thermal softening or degradation. Cooling strategies, such as dry cutting or minimal lubrication, are critical to managing heat generation.
-
Surface Integrity: The machining process can introduce surface defects like burrs, microcracks, or residual stresses, which affect the performance of aerospace components. The choice of cutting strategy (e.g., climb vs. conventional cutting) and tool path planning significantly influences surface integrity.
CNC Machining Techniques for Polyimides
Several CNC machining techniques are employed for polyimides, each suited to specific applications and geometries:
-
Single Point Diamond Turning (SPDT): SPDT uses a single-crystal diamond tool to achieve nanometer-scale surface roughness (Ra ~1–10 nm) and submicron form accuracy (PV < 1 µm). It is ideal for optical and precision components, such as lenses and mirrors, used in aerospace sensors.
-
Ultra-Precision Fly-Cutting (UPFC): UPFC involves a rotating tool that cuts the workpiece in a single pass, suitable for machining microstructures like grooves or channels on polyimide surfaces. Studies show that horizontal cutting strategies in UPFC reduce burr formation and improve surface roughness compared to vertical cutting.
-
Milling and Turning: These conventional CNC techniques are used for larger components, such as engine parts or thermal shields. Multi-axis (5-axis or 7-axis) machining enhances flexibility, allowing the creation of complex geometries with high precision.
Challenges in Machining Polyimides
Machining polyimides presents several challenges:
-
Tool Wear: The high hardness and abrasiveness of polyimides cause rapid wear of conventional tools, necessitating the use of diamond or coated carbide tools.
-
Surface Defects: Burrs, tears, and microcracks can form due to improper cutting parameters or tool geometry, compromising surface quality.
-
Thermal Management: Heat buildup during machining can lead to material softening or degradation, affecting dimensional accuracy and surface finish.
-
Anisotropy: Polyimide composites, reinforced with fibers or fillers, exhibit anisotropic properties, requiring tailored machining strategies to avoid delamination or fiber pullout.
Surface Quality Control in CNC Machining
Importance of Surface Quality
Surface quality, characterized by surface roughness (Ra), form accuracy (PV), and the absence of defects, is critical for aerospace thermal structures. Poor surface quality can lead to:
-
Reduced Thermal Performance: Surface roughness increases thermal resistance, affecting heat transfer in thermal shields or insulation layers.
-
Mechanical Weakness: Microcracks or residual stresses can initiate fatigue failure, compromising component longevity.
-
Optical Degradation: In optical applications, surface imperfections scatter light, reducing performance in sensors or reflectors.
Achieving high surface quality requires precise control of machining parameters, tool selection, and post-processing techniques.
Surface Roughness and Form Accuracy
Surface roughness (Ra) measures the average deviation of the surface profile from the mean line, typically in the nanometer to micrometer range for polyimides. Form accuracy (PV) quantifies the peak-to-valley height of surface deviations, indicating overall shape fidelity. Studies using SPDT on polyimides (e.g., DuPont Vespel SP-1) have achieved Ra values of 1–10 nm and PV values below 1 µm, demonstrating excellent machinability. UPFC experiments have shown that climb cutting strategies yield lower Ra (e.g., 5–20 nm) compared to conventional cutting due to reduced burr formation.
Factors Affecting Surface Quality
Several factors influence surface quality in CNC machining of polyimides:
-
Cutting Parameters: Spindle speed, feed rate, and depth of cut significantly affect surface roughness and defect formation. Higher spindle speeds and lower feed rates generally improve surface finish but may increase tool wear.
-
Tool Geometry: Sharp tools with high rake angles and low edge radii minimize cutting forces and surface defects. Diamond tools are preferred for their durability and precision.
-
Cutting Strategy: Climb cutting, where the tool moves in the same direction as the workpiece feed, reduces burrs and improves surface smoothness compared to conventional cutting.
-
Material Composition: The presence of fillers (e.g., carbon fibers, SiO2) in polyimide composites can increase surface roughness due to differential machining behavior between the matrix and fillers.
-
Cooling and Lubrication: Dry machining is common for polyimides to avoid chemical interactions, but minimal lubrication can reduce heat buildup and improve surface quality.
Surface Quality Control Strategies
To achieve optimal surface quality, several strategies are employed:
-
Parameter Optimization: Experimental studies use design of experiments (DOE) to optimize parameters like spindle speed, feed rate, and depth of cut. For example, a study on UPFC of polyimides found that a spindle speed of 2000 rpm, feed rate of 0.05 mm/rev, and depth of cut of 0.01 mm minimized Ra to 5 nm.
-
Tool Path Planning: Unidirectional tool paths in UPFC reduce tool engagement/retraction cycles, improving efficiency and surface finish compared to bidirectional paths.
-
Post-Processing: Techniques like polishing or annealing can reduce residual stresses and surface roughness. Annealing at 250°C improves the machinability of polyimides by stabilizing their thermomechanical properties.
-
Advanced Tooling: Diamond-coated or single-crystal diamond tools enhance cutting precision and reduce wear, critical for ultra-precision machining.
-
Machine Learning: Recent studies employ machine learning to predict optimal machining parameters based on material properties and desired outcomes, improving efficiency and surface quality.
Table 1: Comparison of CNC Machining Techniques for Polyimides
Technique |
Surface Roughness (Ra, nm) |
Form Accuracy (PV, µm) |
Applications |
Advantages |
Challenges |
---|---|---|---|---|---|
SPDT |
1–10 |
<1 |
Optical components, sensors |
Nanometer-scale precision, high surface quality |
High tool cost, limited to small components |
UPFC |
5–20 |
0.5–2 |
Microstructures, grooves |
Reduced burr formation, high efficiency |
Complex tool path planning |
Milling (5-axis) |
50–200 |
2–10 |
Engine components, thermal shields |
Versatility for complex geometries |
Higher roughness, tool wear |
Turning |
20–100 |
1–5 |
Cylindrical parts, bushings |
Cost-effective for simple shapes |
Limited to rotational geometries |
Experimental Studies and Findings
Nanoindentation Studies
Nanoindentation is a powerful technique for characterizing the mechanical properties of polyimides, providing insights into their hardness and elastic modulus, which influence machinability. A study on DuPont Vespel SP-1 reported nanoindentation hardness values of 0.3–0.5 GPa and elastic moduli of 3–4 GPa, indicating high resistance to deformation. These properties necessitate robust cutting tools and precise parameter control to avoid excessive tool wear or surface damage.
SPDT Experiments
Single point diamond turning experiments on polyimides have demonstrated their potential for ultra-precision machining. A study by Ji et al. achieved Ra values of 1–10 nm and PV values below 1 µm using a diamond tool with a 0.1 µm edge radius and a spindle speed of 1500 rpm. The results highlight the importance of low feed rates (e.g., 0.02 mm/rev) and shallow depths of cut (e.g., 0.005 mm) to minimize surface defects.
UPFC Experiments
Ultra-precision fly-cutting experiments have focused on machining microstructures on polyimide surfaces, such as rectangular grooves for aerospace sensors. A 2025 study by the Harbin Institute of Technology compared horizontal and vertical cutting strategies, finding that horizontal cutting reduced burr formation by 50% and achieved Ra values of 5–20 nm. The study also developed theoretical models for tool motion and chip thickness, validated by experimental results, which showed consistent chip thickness predictions within 5% of measured values.
Table 2: Experimental Results for Polyimide Machining
Study |
Technique |
Material |
Ra (nm) |
PV (µm) |
Parameters |
Key Findings |
---|---|---|---|---|---|---|
Ji et al. (2018) |
SPDT |
Vespel SP-1 |
1–10 |
<1 |
1500 rpm, 0.02 mm/rev, 0.005 mm depth |
Nanometer-scale roughness, high form accuracy |
Harbin Inst. (2025) |
UPFC |
PI (unspecified) |
5–20 |
0.5–2 |
2000 rpm, 0.05 mm/rev, 0.01 mm depth |
Horizontal cutting reduces burrs by 50%, lower Ra than vertical cutting |
Lukubira et al. (2019) |
Milling |
PI/Carbon fiber |
50–150 |
2–8 |
3000 rpm, 0.1 mm/rev, 0.02 mm depth |
Fiber reinforcement increases roughness, requires higher cutting forces |
Theoretical Models and Machine Learning
Tool Motion and Chip Thickness Models
Theoretical models for CNC machining of polyimides focus on predicting tool motion and chip thickness to optimize surface quality. In UPFC, the chip thickness (h_max) is modeled as:
[ h_{max} = f \cdot \sin(\theta) \cdot \left( \frac{R}{R - d} \right) ]
where ( f ) is the feed rate, ( \theta ) is the tool angle, ( R ) is the tool radius, and ( d ) is the depth of cut. This model, validated in a 2025 study, accurately predicts chip thickness within 5% of experimental values, aiding in parameter optimization.
Machine Learning for Parameter Optimization
Machine learning (ML) has emerged as a powerful tool for optimizing CNC machining parameters. A 2025 study developed six ML models to predict the mechanical properties of polyimides and their composites, identifying optimal machining conditions for tensile strength, modulus, and surface quality. The models used a dataset of 8 million hypothetical polyimides, achieving prediction accuracies above 90% for properties like Young’s modulus and surface roughness. ML-assisted approaches enable rapid identification of machining parameters, reducing trial-and-error in experimental setups.
Practical Applications in Aerospace Thermal Structures
Engine Components
Polyimide composites, such as PMR-15 and DMBZ-15, are used in engine components like bypass ducts and nozzle flaps, where they withstand temperatures up to 335°C and provide weight savings of 20–30% compared to metallic alternatives. CNC machining ensures precise fabrication of these components, with surface roughness (Ra < 50 nm) critical for aerodynamic performance.
Thermal Insulation
Polyimide foams and aerogels, machined into complex shapes using UPFC, serve as thermal insulation in spacecraft, offering low thermal conductivity (0.029 W/mK) and flame resistance up to 1200°C. Surface quality control ensures minimal defects, enhancing insulation efficiency.
Structural Composites
Carbon fiber-reinforced polyimide composites are machined into lightweight structural components, such as vent tubes and thermal protection systems. 5-axis CNC machining enables the creation of complex geometries with PV values below 5 µm, meeting stringent aerospace tolerances.
Table 3: Applications of CNC-Machined Polyimides in Aerospace
Application |
Polyimide Type |
Machining Technique |
Surface Requirements |
Performance Benefits |
---|---|---|---|---|
Engine Components |
PMR-15, DMBZ-15 |
Milling, Turning |
Ra < 50 nm, PV < 5 µm |
High thermal stability, weight savings |
Thermal Insulation |
PI Foam, Aerogel |
UPFC |
Ra < 20 nm, PV < 2 µm |
Low thermal conductivity, flame resistance |
Structural Composites |
PI/Carbon Fiber |
5-axis Milling |
Ra < 100 nm, PV < 5 µm |
High strength-to-weight ratio, radiation resistance |
Challenges and Future Directions
Current Challenges
-
Tool Wear and Cost: Diamond tools, while effective, are expensive and require frequent maintenance due to polyimide’s abrasiveness.
-
Thermal Management: Effective cooling strategies are needed to prevent thermal damage without compromising chemical stability.
-
Composite Machining: Anisotropic properties of polyimide composites complicate machining, requiring advanced tool path planning to avoid delamination.
-
Scalability: Scaling up ultra-precision techniques like SPDT and UPFC for large aerospace components remains challenging.
Future Directions
-
Advanced Tool Materials: Developing cost-effective, wear-resistant tool coatings to enhance durability and reduce machining costs.
-
Hybrid Manufacturing: Combining additive manufacturing with CNC machining to create complex polyimide structures with minimal material waste.
-
AI-Driven Optimization: Expanding ML applications to real-time machining control, predicting tool wear, and optimizing surface quality.
-
Sustainable Processing: Exploring eco-friendly machining fluids and recycling strategies for polyimide waste to align with sustainability goals.
Conclusion
Polyimide-based high-performance polymers are critical for aerospace thermal structures, offering unmatched thermal stability, mechanical strength, and weight savings. CNC machining, through techniques like SPDT, UPFC, and multi-axis milling, enables the fabrication of precise, high-quality components essential for aerospace applications. Surface quality control, driven by optimized parameters, advanced tooling, and machine learning, ensures that machined polyimides meet stringent performance requirements. Despite challenges like tool wear and thermal management, ongoing research and technological advancements promise to enhance the machinability and applicability of polyimides. This article provides a comprehensive foundation for understanding the CNC machining mechanisms and surface quality control strategies for polyimides, supported by experimental data and theoretical insights, paving the way for future innovations in aerospace engineering.
Reprint Statement: If there are no special instructions, all articles on this site are original. Please indicate the source for reprinting:https://www.cncmachiningptj.com/,thanks!
PTJ® provides a full range of Custom Precision cnc machining china services.ISO 9001:2015 &AS-9100 certified. 3, 4 and 5-axis rapid precision CNC machining services including milling, turning to customer specifications,Capable of metal & plastic machined parts with +/-0.005 mm tolerance.Secondary services include CNC and conventional grinding, drilling,die casting,sheet metal and stamping.Providing prototypes, full production runs, technical support and full inspection.Serves the automotive, aerospace, mold&fixture,led lighting,medical,bicycle, and consumer electronics industries. On-time delivery.Tell us a little about your project's budget and expected delivery time. We will strategize with you to provide the most cost-effective services to help you reach your target,Welcome to Contact us ( sales@pintejin.com ) directly for your new project.
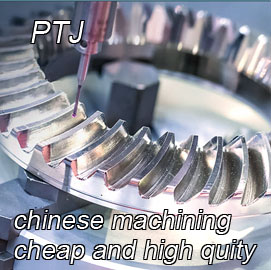
- 5 Axis Machining
- Cnc Milling
- Cnc Turning
- Machining Industries
- Machining Process
- Surface Treatment
- Metal Machining
- Plastic Machining
- Powder Metallurgy Mold
- Die Casting
- Parts Gallery
- Auto Metal Parts
- Machinery Parts
- LED Heatsink
- Building Parts
- Mobile Parts
- Medical Parts
- Electronic Parts
- Tailored Machining
- Bicycle Parts
- Aluminum Machining
- Titanium Machining
- Stainless Steel Machining
- Copper Machining
- Brass Machining
- Super Alloy Machining
- Peek Machining
- UHMW Machining
- Unilate Machining
- PA6 Machining
- PPS Machining
- Teflon Machining
- Inconel Machining
- Tool Steel Machining
- More Material