Process For Repairing Slag Inclusion Defect Of Copper Propeller
Repairing process of slag inclusion defect of copper propeller
The marine propeller is also called the thruster, which is an important casting of the ship's power plant and an important device to ensure the safe navigation of the ship. Propellers operating in seawater are subject to huge alternating loads. They require high mechanical properties, high corrosion fatigue resistance, and excellent cavitation corrosion resistance. Casting defects such as pores and slag inclusions are not allowed. |
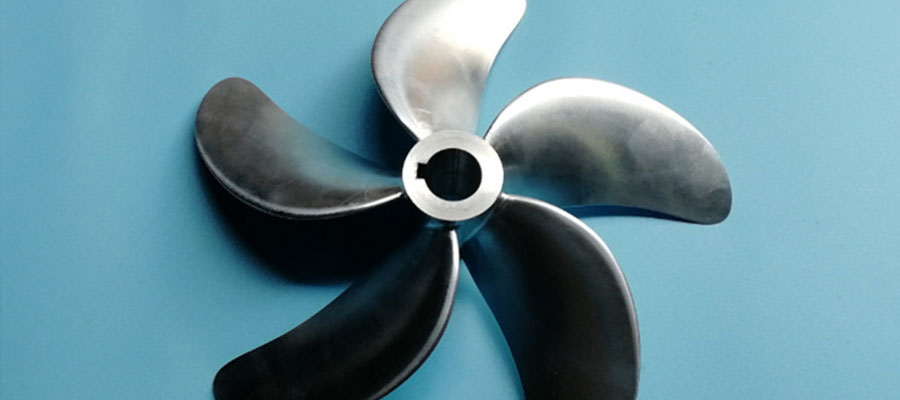
The propeller produced by PTJ Shop uses copper alloy, which is mainly used in the manufacture of machining ship propellers for large and high-speed ships. Its main advantages are light weight and high strength. Fatigue resistance and cavitation erosion resistance are good. Its disadvantages are high casting and processing requirements. If welding is not adopted, corresponding problems such as difficult fusion, porosity, thermal cracks, and low-level welding deformation of joint performance will be returned. . The following describes the use of argon arc welding to repair slag inclusion defects of the propeller.
Defect description
The crystalline range of the copper alloy is relatively narrow, and the volume shrinkage is large, and the alloy also contains active elements Al, Mn, Fe, Ni, etc., which have a strong affinity for oxygen. During the pouring process, high-temperature copper water enters the inadequately dried propeller cement sand casting mold and pouring system, and a large amount of adsorbed water-based crystalline water on the surface of the casting mold is rapidly precipitated to become water vapor. When water vapor interacts with the alloy elements, oxidized inclusions are generated. Slag. More than half of the defects appear in the lower 0.5R-0.8R of the blade surface; there is also an oxide film covering the entire surface of the copper solution during the pouring process, and the copper solution enters the blade. Since then, the surface area has continued to expand. However, when the copper liquid rose to the highest point of the propeller mold, that is, the 0.3R-0.5R guide edge, due to the drastic reduction of the blade's horizontal section and the copper liquid flow direction changed to the upper part of the propeller shell and the riser, it caused secondary A large amount of oxide slag aggregates and the exclusion resistance increases, so that the amount of secondary oxide slag in this area increases sharply.
Selection of welding materials
Welding materials should be selected according to the propeller materials with similar performance.
Preparation before welding
Use a sander to grind the defects and completely remove the defects until a good matrix material appears. Appropriate welding repair grooves should be processed, and the grooves should be smooth and free of burrs. Then use acetone, steel brush, etc. to clean the welding repair site and other magazines within 20mm on both sides of oil, oxides, moisture and so on. Dry the electrode to 200 ℃ and keep it for 1 ~ 2 hours.Due to the high thermal conductivity of copper, heat is easily dissipated during welding, so it must be preheated before welding. On the other hand, preheating can also improve the welding stress distribution and reduce the risk of stress corrosion cracking. The preheating temperature is not lower than 150 ℃. It can be preheated with a flame gun or an electric heating belt. The interlayer temperature should not exceed 300 ℃ and it should be maintained until the end of the welding repair. The preheating range from the welding repair area must not be less than 100mm in all directions.
Post-weld machining
Because copper alloys are very sensitive to stress corrosion, heat treatment must be performed to relieve stress after welding. For small welding repairs, you can use a soft-fire gas distance or electric wire heater to perform local stress relief treatment, and locally heat the welding repair to the annealing temperature. The heat preservation minutes are greater than the millimeters of the section thickness at that place, and then covered with asbestos cloth. cold. After the post-weld heat treatment is completely cooled, perform color inspection until the inspection results do not find defects such as cracks, pores, etc., and the quality meets the requirements. Otherwise, repair welding is required. Finally, static balance test, calibration, pitch measurement, thickness measurement, grinding and polishing.Adopting argon arc welding to repair ship propellers and using reasonable welding process parameters can better repair slag-type defects of the propellers, ensure the mechanical properties of the ship propeller materials, increase the service life of the propellers, and ensure the safe navigation of the ship.
Link to this article: Process For Repairing Slag Inclusion Defect Of Copper Propeller
Reprint Statement: If there are no special instructions, all articles on this site are original. Please indicate the source for reprinting:https://www.cncmachiningptj.com/,thanks!
PTJ® provides a full range of Custom Precision cnc machining china services.ISO 9001:2015 &AS-9100 certified. 3, 4 and 5-axis rapid precision CNC machining services including milling, turning to customer specifications,Capable of metal & plastic machined parts with +/-0.005 mm tolerance.Secondary services include CNC and conventional grinding, drilling,die casting,sheet metal and stamping.Providing prototypes, full production runs, technical support and full inspection.Serves the automotive, aerospace, mold&fixture,led lighting,medical,bicycle, and consumer electronics industries. On-time delivery.Tell us a little about your project’s budget and expected delivery time. We will strategize with you to provide the most cost-effective services to help you reach your target,Welcome to Contact us ( sales@pintejin.com ) directly for your new project.
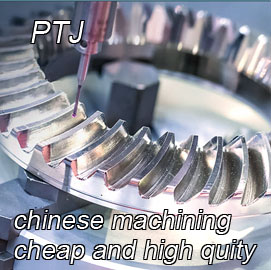
- 5 Axis Machining
- Cnc Milling
- Cnc Turning
- Machining Industries
- Machining Process
- Surface Treatment
- Metal Machining
- Plastic Machining
- Powder Metallurgy Mold
- Die Casting
- Parts Gallery
- Auto Metal Parts
- Machinery Parts
- LED Heatsink
- Building Parts
- Mobile Parts
- Medical Parts
- Electronic Parts
- Tailored Machining
- Bicycle Parts
- Aluminum Machining
- Titanium Machining
- Stainless Steel Machining
- Copper Machining
- Brass Machining
- Super Alloy Machining
- Peek Machining
- UHMW Machining
- Unilate Machining
- PA6 Machining
- PPS Machining
- Teflon Machining
- Inconel Machining
- Tool Steel Machining
- More Material