Research on Key Technology of CNC Machining Process for Large Complex Structure of Aircraft
CNC Machining Process for Large Complex Structure of Aircraft
In the development of aviation technology, the requirements for large-scale, integrated, thin-walled, and precise aircraft structural parts are very prominent. The size increases but the tolerance is doubled, the wall thickness decreases, but the ribs increase, and the dimensional accuracy increases. At the same time, the weight tolerance index is increased, and the multiple structural features of a single structural component are integrated, which leads to strict shape and position accuracy. The long life and light weight require that the surface roughness of the processing is generally improved by 1-2 levels. Since all aircraft structural components are 100% CNC processed, the processing quality is The contradiction with processing efficiency is prominent. |
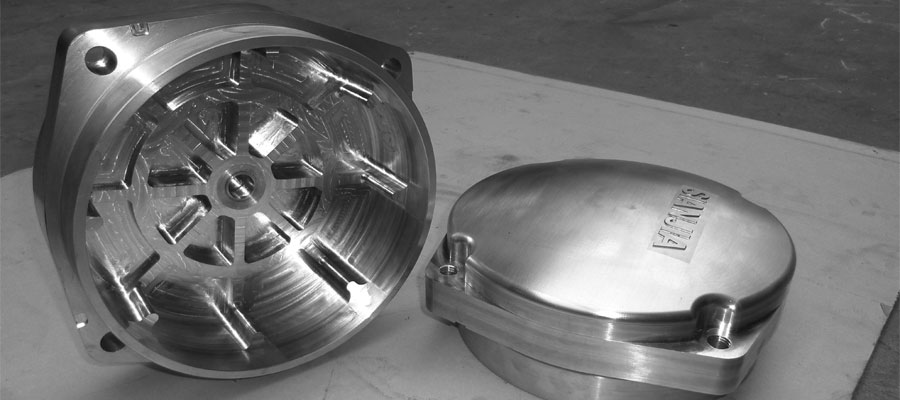
During the development and production of aircraft, NC machining faces three major problems-machining damage, machining instability, and machining deformation. Since 2007, PTJ Shop, with the support of various projects in the aviation industry, has successfully solved the above-mentioned problems.
The essential causes of machining damage, instability and deformation come from the dynamic interaction of the "machine tool-tool-workpiece" process system in the NC machining process. Traditional theories and methods based on experience and single factor do not solve the above problems.
The general idea is to address the problem. Through modeling, analyze the mechanical nature of "overload → damage", "chatter → stability" and "stress → deformation". From the theoretical prediction, "proof" and "equipment equipment" are "dissipated". Start with a combination of anti-cancellation, both hardware and software, and break through the following key technologies:
- 1) Cutting force / thermal load balance pre-adjustment processing technology for processing difficult materials and complex structures;
- 2) Stable and high-speed milling processing technology for large thin-walled structural parts;
- 3) Prediction and control technology of residual stress and deformation during the whole process of large and complex structural parts.
PTJ Shop independently developed: NC milling time-varying cutting force prediction and parameter optimization software and micro-lubrication device, NC cutting dynamics simulation optimization software and passive damping vibration absorption device, machining deformation simulation software and "thermal-vibration" compound stress equalization The device is applied to the numerically-controlled machining process of large and complex structural parts of aircraft, and solves the problems of machining instability, damage and deformation.
Research and application of key technologies:
1. Cutting force / thermal load balance pre-adjustment processing technology for difficult-to-machine materials
The problem of machining damage is that the laser cutting force / thermal load is large and changes sharply during the CNC machining process, which causes mechanical damage and surface burns to the impact of tools and workpieces, especially in the numerical control machining of difficult-to-machine materials.
The traditional way to avoid and reduce machining damage is to greatly reduce the amount of cutting and use a large amount of cutting fluid, which significantly sacrifices cutting efficiency. Faced with new processing requirements, based on dynamic cutting force modeling and considering multiple constraints of the process system, a radial spiral layered localized circular milling method with variable spiral curves was proposed to optimize the tool path and pre-adjust the cutting parameters. Cutting force is balanced to prevent the overload and impact of cutting force.
Time-varying cutting force prediction and parameter optimization software for CNC machining of aircraft parts has been developed, and application specifications have been formed; three types of quasi-dry cutting precision lubrication devices have been developed. The TC4 titanium alloy super large overall frame is processed and tested for complex structures such as ribs, edges, and internal shapes to achieve a stable cutting speed of more than 150m / min, and the surface roughness of the critical parts reaches Ra1.6 ~ Ra0.8.
2.Stable high-speed milling processing technology for large thin-walled components
The problem of machining instability is that the thin-walled and high-reinforced structures cause the dynamic characteristics of the process system to deteriorate, and cutting flutter occurs. Faced with new processing requirements, based on the analysis of process system interactions, a “machine tool-tool-workpiece” dynamic model was established. Through testing and identification, the flutter stability domain curve was calculated by simulation. Under the multiple constraints of the process system, Optimized cutting parameters are provided to achieve high-speed and high-efficiency cutting without chattering, and to "prevent" machining instability.
Based on the flutter model, a variety of damping and vibration damping devices have been developed and installed on the corresponding parts of the machined structure or machine tool to suppress or attenuate the vibrations that occur, and achieve the "elimination" of machining vibrations.
Independently developed the identification test hardware, X-Cut / e-Cutting software, and damping device, and established a process database based on a large number of tests. Example tests of fuselage frames in aircraft aluminum alloys show that:
Realize chatter-free stable processing of weak rigid edges;
Material removal rate increased by more than double;
The surface roughness of the critical parts reaches Ra0.8 μm.
3. Prediction and control technology of residual stress and deformation during the whole process
The deformation of large and complex components mainly comes from:
- 1) the deformation caused by the residual stress in the blank continuously released and redistributed during the cutting process;
- 2) the deformation between the tool and the workpiece (including clamping) under the action of cutting force Relative deformation.
Therefore, the formation of residual stress in aircraft structural parts and the evolution of elastic deformation of the blade are the core of predicting and controlling machining deformation. For large and complex aircraft components, carry out simulation analysis of the residual stress from the blank to the finished product of the structural part, predict the residual stress distribution state and processing deformation law, and optimize the process and parameters to control the residual stress state of the blank to realize the prediction of subsequent CNC machining deformation. "Protection"; developed a "thermal-vibration" composite residual stress equalization device, which applies "point-cavity" type thermal and vibration compound effects to the workpiece to perform residual stress equalization to "eliminate" the workpiece deformation.
The overall technology of this project achievement has reached the international advanced level, and it has reached the international advanced level in the cutting force / thermal load balance pre-adjustment processing technology.
Link to this article: Research on Key Technology of CNC Machining Process for Large Complex Structure of Aircraft
Reprint Statement: If there are no special instructions, all articles on this site are original. Please indicate the source for reprinting:https://www.cncmachiningptj.com/,thanks!
PTJ® provides a full range of Custom Precision cnc machining china services.ISO 9001:2015 &AS-9100 certified. 3, 4 and 5-axis rapid precision CNC machining services including milling, turning to customer specifications,Capable of metal & plastic machined parts with +/-0.005 mm tolerance.Secondary services include CNC and conventional grinding, drilling,die casting,sheet metal and stamping.Providing prototypes, full production runs, technical support and full inspection.Serves the automotive, aerospace, mold&fixture,led lighting,medical,bicycle, and consumer electronics industries. On-time delivery.Tell us a little about your project’s budget and expected delivery time. We will strategize with you to provide the most cost-effective services to help you reach your target,Welcome to Contact us ( sales@pintejin.com ) directly for your new project.
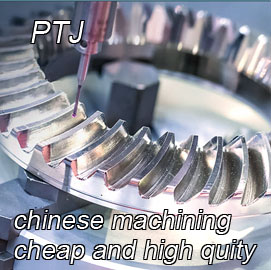
- 5 Axis Machining
- Cnc Milling
- Cnc Turning
- Machining Industries
- Machining Process
- Surface Treatment
- Metal Machining
- Plastic Machining
- Powder Metallurgy Mold
- Die Casting
- Parts Gallery
- Auto Metal Parts
- Machinery Parts
- LED Heatsink
- Building Parts
- Mobile Parts
- Medical Parts
- Electronic Parts
- Tailored Machining
- Bicycle Parts
- Aluminum Machining
- Titanium Machining
- Stainless Steel Machining
- Copper Machining
- Brass Machining
- Super Alloy Machining
- Peek Machining
- UHMW Machining
- Unilate Machining
- PA6 Machining
- PPS Machining
- Teflon Machining
- Inconel Machining
- Tool Steel Machining
- More Material