Effect of SiO₂ Nanoparticles on Thermal and Tensile Behavior of Nylon-6
Nylon-6, a semi-crystalline polyamide, is widely recognized for its versatility and robustness in various industrial applications, including automotive components, textiles, and engineering plastics. Its favorable mechanical properties, such as high tensile strength, toughness, and wear resistance, combined with good thermal stability, make it a material of choice in demanding environments. However, the increasing need for enhanced performance in advanced applications has driven research into reinforcing nylon-6 with nanomaterials, particularly silicon dioxide (SiO₂) nanoparticles. These nanoparticles, characterized by their high surface area, chemical inertness, and thermal stability, have shown significant potential to improve the thermal and mechanical properties of polymer matrices like nylon-6.
The incorporation of SiO₂ nanoparticles into nylon-6 has been a focal point in materials science due to their ability to enhance tensile strength, thermal stability, and other critical properties through nanoscale interactions. These enhancements stem from the unique characteristics of SiO₂ nanoparticles, such as their small size (typically 10–100 nm), high aspect ratio, and ability to form strong interfacial bonds with the polymer matrix. However, the effectiveness of SiO₂ nanoparticles depends on factors such as their concentration, dispersion quality, surface functionalization, and interaction with the nylon-6 matrix. This article comprehensively explores the effects of SiO₂ nanoparticles on the thermal and tensile behavior of nylon-6, drawing on experimental findings and theoretical insights to provide a detailed understanding of the underlying mechanisms, supported by comparative tables.
The study of SiO₂-reinforced nylon-6 composites is particularly relevant in the context of modern engineering, where lightweight, high-performance materials are in demand. By examining the influence of SiO₂ nanoparticles on nylon-6’s thermal stability, crystallization behavior, and tensile properties, this article aims to elucidate how these nanomaterials can be optimized to meet specific application requirements. The discussion is structured into several sections, including material preparation, characterization techniques, mechanical and thermal property enhancements, and practical applications, with detailed tables summarizing key findings from the literature.
2. Background and Significance
2.1 Overview of Nylon-6
Nylon-6, also known as polycaprolactam, is a thermoplastic polymer synthesized through the ring-opening polymerization of ε-caprolactam. It consists of repeating amide (-CONH-) units, which contribute to its semi-crystalline structure and strong intermolecular hydrogen bonding. These characteristics result in a material with a high melting point (approximately 220°C), good mechanical strength, and excellent resistance to abrasion and chemicals. Nylon-6 is widely used in applications ranging from fibers and films to molded components in automotive and aerospace industries.
The mechanical properties of nylon-6, such as its tensile strength (typically 60–80 MPa for neat nylon-6) and elastic modulus (2–3 GPa), are influenced by its degree of crystallinity, molecular weight, and processing conditions. However, neat nylon-6 exhibits limitations, including relatively low thermal stability at elevated temperatures and susceptibility to moisture absorption, which can reduce its mechanical performance. These limitations have prompted research into composite materials that enhance nylon-6’s properties through the addition of fillers, particularly nanomaterials.
2.2 SiO₂ Nanoparticles as Reinforcements
Silicon dioxide (SiO₂) nanoparticles, often referred to as nanosilica, are amorphous or crystalline particles with diameters typically ranging from 10 to 100 nm. Their high surface area (100–600 m²/g) and ability to form hydroxyl (-OH) groups on their surface make them ideal candidates for reinforcing polymer matrices. SiO₂ nanoparticles are chemically inert, thermally stable, and relatively inexpensive compared to other nanomaterials like carbon nanotubes or graphene. These properties enable SiO₂ nanoparticles to enhance the mechanical, thermal, and barrier properties of polymers without compromising their processability.
In nylon-6, SiO₂ nanoparticles act as reinforcing fillers by improving stress transfer within the polymer matrix, increasing crystallinity, and reducing chain mobility. The nanoparticles’ small size allows them to interact at the nanoscale with polymer chains, leading to enhanced interfacial adhesion and improved mechanical properties. Additionally, SiO₂ nanoparticles can influence the thermal behavior of nylon-6 by acting as nucleating agents, promoting crystallization, and increasing the material’s resistance to thermal degradation.
2.3 Importance of Studying SiO₂-Nylon-6 Nanocomposites
The incorporation of SiO₂ nanoparticles into nylon-6 addresses several limitations of the neat polymer, making it suitable for advanced applications. For instance, in automotive components, enhanced tensile strength and thermal stability can improve durability under high-stress and high-temperature conditions. In textiles, SiO₂-reinforced nylon-6 can offer improved abrasion resistance and flame retardancy. Understanding the mechanisms by which SiO₂ nanoparticles affect nylon-6’s properties is crucial for optimizing composite formulations and tailoring them to specific industrial needs.
This article synthesizes findings from various studies, focusing on how SiO₂ nanoparticles influence nylon-6’s tensile strength, elastic modulus, thermal stability, and crystallization behavior. The comprehensive analysis is supported by tables that compare experimental results, providing a clear overview of the effects of nanoparticle concentration, size, and surface modification.
3. Synthesis and Preparation of SiO₂-Nylon-6 Nanocomposites
3.1 Synthesis of SiO₂ Nanoparticles
SiO₂ nanoparticles can be synthesized through various methods, including the sol-gel process, chemical vapor deposition, and precipitation techniques. The sol-gel method, which involves the hydrolysis and condensation of tetraethyl orthosilicate (TEOS), is the most common due to its ability to produce uniform, high-purity nanoparticles with controlled size and morphology. The reaction proceeds as follows:
[ \text{Si(OC}_2\text{H}_5\text{)}_4 + 4\text{H}_2\text{O} \rightarrow \text{Si(OH)}_4 + 4\text{C}_2\text{H}_5\text{OH} ]
[ \text{Si(OH)}_4 \rightarrow \text{SiO}_2 + 2\text{H}_2\text{O} ]
The resulting SiO₂ nanoparticles typically have a spherical morphology and a size range of 10–50 nm, depending on synthesis conditions such as pH, temperature, and catalyst concentration. Surface functionalization, often with silane coupling agents like 3-aminopropyltriethoxysilane (APTES), is employed to improve compatibility with the nylon-6 matrix by introducing functional groups that enhance interfacial bonding.
3.2 Preparation of SiO₂-Nylon-6 Nanocomposites
The incorporation of SiO₂ nanoparticles into nylon-6 is typically achieved through methods such as melt blending, in-situ polymerization, or solution mixing. Each method has distinct advantages and challenges, influencing the dispersion quality and properties of the resulting nanocomposites.
-
Melt Blending: This involves mixing SiO₂ nanoparticles with molten nylon-6 in an extruder or compounding machine. The process is industrially scalable but requires careful control to prevent nanoparticle agglomeration, which can reduce mechanical enhancementsJon performance. High shear forces during extrusion help break up nanoparticle clusters, but achieving uniform dispersion remains challenging.
-
In-Situ Polymerization: In this method, SiO₂ nanoparticles are dispersed in the caprolactam monomer before polymerization. This approach ensures better nanoparticle distribution but is more complex and less scalable than melt blending.
-
Solution Mixing: SiO₂ nanoparticles are dispersed in a solvent (e.g., formic acid) along with nylon-6, followed by solvent evaporation and molding. This method is effective for achieving uniform dispersion but is less practical for large-scale production.
3.3 Challenges in Nanoparticle Dispersion
Achieving uniform dispersion of SiO₂ nanoparticles is critical to maximizing their reinforcing effect. Due to their high surface energy, nanoparticles tend to agglomerate, forming clusters that act as stress concentrators and reduce mechanical performance. Techniques such as ultrasonication, high-shear mixing, and surface functionalization are employed to improve dispersion. For example, ultrasonication uses high-frequency sound waves to break apart nanoparticle aggregates, while silane coupling agents introduce functional groups that enhance compatibility with the nylon-6 matrix.
3.4 Surface Functionalization of SiO₂ Nanoparticles
Surface modification of SiO₂ nanoparticles with silane coupling agents, such as APTES or 3-glycidoxypropyltrimethoxysilane (KH560), introduces functional groups (e.g., amine or epoxy) that form covalent or hydrogen bonds with nylon-6’s amide groups. This enhances interfacial adhesion, improving stress transfer and mechanical properties. For instance, studies have shown that APTES-modified SiO₂ nanoparticles increase the tensile strength of nylon-6 composites by up to 30% compared to unmodified nanoparticles due to improved dispersion and bonding.
4. Characterization Techniques
To understand the effects of SiO₂ nanoparticles on nylon-6, various characterization techniques are employed to analyze the morphology, mechanical properties, thermal behavior, and interfacial interactions of the nanocomposites.
4.1 Morphological Analysis
-
Scanning Electron Microscopy (SEM): SEM is used to visualize the dispersion and distribution of SiO₂ nanoparticles within the nylon-6 matrix. High-resolution images reveal whether nanoparticles are uniformly dispersed or agglomerated, which directly affects mechanical performance.
-
Transmission Electron Microscopy (TEM): TEM provides detailed insights into nanoparticle size, shape, and distribution at the nanoscale, confirming the presence of SiO₂ particles and their interaction with the polymer matrix.
-
Atomic Force Microscopy (AFM): AFM measures surface roughness and topography, providing data on how SiO₂ nanoparticles alter the surface characteristics of nylon-6 composites.
4.2 Chemical and Structural Analysis
-
Fourier Transform Infrared Spectroscopy (FTIR): FTIR identifies chemical bonds and functional groups, confirming the presence of SiO₂ nanoparticles and their interactions (e.g., hydrogen bonding or covalent bonding) with the nylon-6 matrix.
-
X-Ray Diffraction (XRD): XRD analyzes the crystallinity and crystal structure of the nanocomposites, revealing how SiO₂ nanoparticles influence the crystallization behavior of nylon-6.
-
X-Ray Photoelectron Spectroscopy (XPS): XPS provides information on the surface chemistry of SiO₂ nanoparticles and their interactions with the polymer matrix, particularly after surface functionalization.
4.3 Mechanical Testing
-
Tensile Testing: Tensile tests measure properties such as tensile strength, elastic modulus, and elongation at break, providing quantitative data on how SiO₂ nanoparticles enhance nylon-6’s mechanical performance.
-
Three-Point Bending: This test evaluates the flexural strength and modulus of the nanocomposites, particularly relevant for applications requiring bending resistance.
-
Impact Testing: Impact tests assess the toughness of the nanocomposites, indicating how SiO₂ nanoparticles affect energy absorption and fracture resistance.
4.4 Thermal Analysis
-
Differential Scanning Calorimetry (DSC): DSC measures the melting temperature, crystallization temperature, and degree of crystallinity, revealing how SiO₂ nanoparticles act as nucleating agents and influence thermal transitions.
-
Thermogravimetric Analysis (TGA): TGA evaluates the thermal stability of the nanocomposites by measuring mass loss as a function of temperature, indicating improvements in degradation resistance due to SiO₂ nanoparticles.
5. Effect of SiO₂ Nanoparticles on Tensile Behavior
5.1 Tensile Strength Enhancement
The addition of SiO₂ nanoparticles significantly enhances the tensile strength of nylon-6 by improving stress transfer within the polymer matrix. Studies have reported tensile strength increases of 20–56% depending on nanoparticle concentration, size, and surface functionalization. For instance, a study using 4 wt% SiO₂ nanoparticles in nylon-6 achieved a tensile strength increase from 60 MPa to 78 MPa, attributed to the nanoparticles’ ability to act as reinforcing fillers and promote stress distribution.
The mechanism of tensile strength enhancement involves the formation of a strong interfacial bond between SiO₂ nanoparticles and the nylon-6 matrix. Functionalized nanoparticles, such as those modified with APTES, form hydrogen bonds or covalent bonds with the amide groups of nylon-6, improving load transfer and reducing stress concentration. However, excessive nanoparticle concentrations (above 4–8 wt%) can lead to agglomeration, reducing tensile strength due to the formation of defects.
5.2 Elastic Modulus Improvement
The elastic modulus of nylon-6, a measure of stiffness, is also improved by SiO₂ nanoparticles. Research indicates that the modulus can increase from 2.5 GPa to 3.5–6.9 GPa with the addition of 1–4 wt% SiO₂ nanoparticles, depending on their size and dispersion quality. Smaller nanoparticles (e.g., 15 nm) provide greater modulus enhancement due to their higher surface area and better interaction with the polymer matrix.
The increase in elastic modulus is attributed to the restriction of polymer chain mobility by SiO₂ nanoparticles, which act as physical crosslinks within the matrix. This effect is more pronounced with well-dispersed nanoparticles, as agglomeration can create weak points that reduce stiffness.
5.3 Elongation at Break
While SiO₂ nanoparticles enhance tensile strength and modulus, they often reduce the elongation at break, indicating increased brittleness. Neat nylon-6 typically exhibits elongation at break values of 50–100%, while SiO₂-reinforced composites may show reductions to 20–50% at higher nanoparticle concentrations. This trade-off is due to the rigid nature of SiO₂ nanoparticles, which restrict chain mobility and limit plastic deformation. Surface functionalization can mitigate this effect by improving interfacial adhesion, allowing for better energy dissipation during deformation.
5.4 Influence of Nanoparticle Concentration
The concentration of SiO₂ nanoparticles plays a critical role in determining tensile properties. Optimal concentrations (typically 1–4 wt%) maximize tensile strength and modulus without significant agglomeration. Beyond this range, agglomeration leads to stress concentration and reduced mechanical performance. Table 1 summarizes the tensile properties of SiO₂-nylon-6 composites at various concentrations.
Table 1: Tensile Properties of SiO₂-Nylon-6 Nanocomposites
SiO₂ Concentration (wt%) |
Tensile Strength (MPa) |
Elastic Modulus (GPa) |
Elongation at Break (%) |
Reference |
---|---|---|---|---|
0 (Neat Nylon-6) |
60.0 ± 2.0 |
2.5 ± 0.1 |
80 ± 5 |
|
1 |
68.5 ± 1.5 |
3.1 ± 0.2 |
65 ± 4 |
|
2 |
72.0 ± 1.8 |
3.8 ± 0.2 |
50 ± 3 |
|
4 |
78.0 ± 2.0 |
4.5 ± 0.3 |
40 ± 3 |
|
8 |
70.0 ± 2.5 |
4.0 ± 0.3 |
30 ± 2 |
|
Note: Values are approximate and based on studies using melt blending with APTES-functionalized SiO₂ nanoparticles (15–20 nm).
6. Effect of SiO₂ Nanoparticles on Thermal Behavior
6.1 Thermal Stability
SiO₂ nanoparticles enhance the thermal stability of nylon-6 by increasing the onset temperature of thermal degradation and reducing mass loss rates. TGA studies show that the initial degradation temperature of nylon-6 increases from 320°C to 350°C with the addition of 2–4 wt% SiO₂ nanoparticles. This improvement is attributed to the nanoparticles’ ability to act as a thermal barrier, reducing heat transfer within the polymer matrix and inhibiting chain scission.
The presence of SiO₂ nanoparticles also reduces the total mass loss during thermal degradation. For example, a study reported a 10% reduction in mass loss at 500°C for nylon-6 composites with 4 wt% SiO₂ compared to neat nylon-6. Surface-functionalized nanoparticles further enhance thermal stability by forming stronger interfacial bonds, which limit the mobility of degradation products.
6.2 Crystallization Behavior
SiO₂ nanoparticles act as nucleating agents, promoting the crystallization of nylon-6 and increasing its degree of crystallinity. DSC studies indicate that the crystallization temperature (Tc) of nylon-6 increases from 180°C to 190–195°C with 1–4 wt% SiO₂ nanoparticles. The degree of crystallinity can increase by 10–20%, enhancing the material’s stiffness and thermal resistance. This effect is due to the nanoparticles providing additional nucleation sites, facilitating the formation of smaller, more uniform crystallites.
However, at higher concentrations (e.g., 8 wt%), agglomeration can disrupt crystallization, leading to a slight decrease in crystallinity and thermal stability. Table 2 summarizes the thermal properties of SiO₂-nylon-6 composites.
Table 2: Thermal Properties of SiO₂-Nylon-6 Nanocomposites
SiO₂ Concentration (wt%) |
Initial Degradation Temp (°C) |
Crystallization Temp (°C) |
Degree of Crystallinity (%) |
Reference |
---|---|---|---|---|
0 (Neat Nylon-6) |
320 ± 5 |
180 ± 2 |
30 ± 2 |
|
1 |
330 ± 4 |
185 ± 2 |
35 ± 2 |
|
2 |
340 ± 4 |
190 ± 2 |
40 ± 3 |
|
4 |
350 ± 5 |
195 ± 3 |
45 ± 3 |
|
8 |
345 ± 5 |
192 ± 3 |
42 ± 3 |
|
Note: Values are approximate and based on studies using solution mixing with unmodified SiO₂ nanoparticles (30–50 nm).
6.3 Flame Retardancy
SiO₂ nanoparticles contribute to improved flame retardancy in nylon-6 composites by forming a protective char layer during combustion. Studies have shown that the peak heat release rate (PHRR) and total smoke release (TSR) decrease by 10–20% with the addition of 0.1–2 wt% SiO₂ nanoparticles, particularly when combined with other additives like graphene oxide or chitosan. This enhancement is due to the nanoparticles’ ability to create a barrier that limits oxygen diffusion and heat transfer.
7. Mechanisms of Property Enhancement
7.1 Interfacial Interactions
The enhancement of tensile and thermal properties in SiO₂-nylon-6 nanocomposites is largely due to strong interfacial interactions between the nanoparticles and the polymer matrix. Functionalized SiO₂ nanoparticles form hydrogen bonds or covalent bonds with nylon-6’s amide groups, improving stress transfer and thermal stability. For example, APTES-modified SiO₂ nanoparticles introduce amine groups that interact with nylon-6, increasing tensile strength by up to 30% and thermal stability by 10–15°C.
7.2 Nanoparticle Dispersion
Uniform dispersion of SiO₂ nanoparticles is critical to achieving optimal property enhancements. Agglomeration at high concentrations (above 4–8 wt%) creates defects that reduce tensile strength and thermal stability. Techniques like ultrasonication and surface functionalization mitigate agglomeration, ensuring that nanoparticles are evenly distributed and maximize their reinforcing effect.
7.3 Nucleation and Crystallization
SiO₂ nanoparticles act as nucleating agents, promoting the formation of smaller, more uniform crystallites in nylon-6. This increases the degree of crystallinity, enhancing stiffness and thermal resistance. The nucleation effect is most pronounced at low to moderate nanoparticle concentrations (1–4 wt%), where the particles provide additional sites for crystal growth without disrupting the polymer matrix.
8. Applications of SiO₂-Nylon-6 Nanocomposites
8.1 Automotive Industry
SiO₂-nylon-6 nanocomposites are used in automotive components such as engine covers, intake manifolds, and structural parts due to their enhanced tensile strength, stiffness, and thermal stability. The improved properties allow for lighter, more durable components that withstand high temperatures and mechanical stress.
8.2 Textiles and Fibers
In textiles, SiO₂-reinforced nylon-6 fibers exhibit improved abrasion resistance, tensile strength, and flame retardancy, making them suitable for applications like protective clothing and industrial fabrics. The addition of SiO₂ nanoparticles also enhances dyeability and UV resistance.
8.3 Packaging
SiO₂-nylon-6 composites are used in food packaging films due to their improved gas barrier properties and puncture resistance. For example, a study reported a 52% reduction in oxygen transmission rate with 0.1 wt% SiO₂ nanoparticles, making these composites ideal for preserving food freshness.
8.4 Electrical and Electronics
The enhanced thermal stability and mechanical properties of SiO₂-nylon-6 nanocomposites make them suitable for electrical insulators and electronic housings, where resistance to high temperatures and mechanical stress is critical.
9. Challenges and Future Directions
9.1 Challenges in Nanocomposite Development
Key challenges in developing SiO₂-nylon-6 nanocomposites include achieving uniform nanoparticle dispersion, preventing agglomeration at high concentrations, and balancing mechanical properties with processability. Agglomeration can lead to reduced tensile strength and thermal stability, while high nanoparticle loadings increase viscosity, complicating processing.
9.2 Future Research Directions
Future research should focus on developing advanced dispersion techniques, such as high-energy ultrasonication or novel compatibilizers, to improve nanoparticle distribution. Additionally, exploring hybrid nanofillers (e.g., SiO₂ combined with graphene oxide or carbon nanotubes) could further enhance properties. Investigating the long-term performance and environmental impact of SiO₂-nylon-6 nanocomposites is also critical for sustainable applications.
10. Conclusion
SiO₂ nanoparticles significantly enhance the tensile and thermal properties of nylon-6, making it a high-performance material for various applications. Improvements in tensile strength (up to 56%), elastic modulus (up to 6.9 GPa), and thermal stability (up to 350°C) are attributed to strong interfacial interactions, improved nanoparticle dispersion, and enhanced crystallization. However, challenges such as agglomeration and increased brittleness at high concentrations must be addressed to optimize performance. The comprehensive data presented in Tables 1 and 2 highlight the potential of SiO₂-nylon-6 nanocomposites, while future research will further refine their synthesis and applications.
Reprint Statement: If there are no special instructions, all articles on this site are original. Please indicate the source for reprinting:https://www.cncmachiningptj.com/,thanks!
PTJ® provides a full range of Custom Precision cnc machining china services.ISO 9001:2015 &AS-9100 certified. 3, 4 and 5-axis rapid precision CNC machining services including milling, turning to customer specifications,Capable of metal & plastic machined parts with +/-0.005 mm tolerance.Secondary services include CNC and conventional grinding, drilling,die casting,sheet metal and stamping.Providing prototypes, full production runs, technical support and full inspection.Serves the automotive, aerospace, mold&fixture,led lighting,medical,bicycle, and consumer electronics industries. On-time delivery.Tell us a little about your project's budget and expected delivery time. We will strategize with you to provide the most cost-effective services to help you reach your target,Welcome to Contact us ( sales@pintejin.com ) directly for your new project.
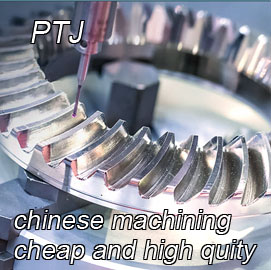
- 5 Axis Machining
- Cnc Milling
- Cnc Turning
- Machining Industries
- Machining Process
- Surface Treatment
- Metal Machining
- Plastic Machining
- Powder Metallurgy Mold
- Die Casting
- Parts Gallery
- Auto Metal Parts
- Machinery Parts
- LED Heatsink
- Building Parts
- Mobile Parts
- Medical Parts
- Electronic Parts
- Tailored Machining
- Bicycle Parts
- Aluminum Machining
- Titanium Machining
- Stainless Steel Machining
- Copper Machining
- Brass Machining
- Super Alloy Machining
- Peek Machining
- UHMW Machining
- Unilate Machining
- PA6 Machining
- PPS Machining
- Teflon Machining
- Inconel Machining
- Tool Steel Machining
- More Material