High-Performance Numerical Control for High-Speed Machining by Means of Polynomial Trajectories
High-performance numerical control (NC) systems have become a cornerstone of modern manufacturing, enabling the production of complex parts with high precision and efficiency. The advent of high-speed machining (HSM) has further pushed the boundaries of what NC systems can achieve, particularly in industries such as aerospace, automotive, and biomedical engineering. HSM is characterized by significantly higher spindle speeds, feed rates, and material removal rates compared to conventional machining, requiring advanced control strategies to maintain accuracy and surface quality. Among these strategies, the use of polynomial trajectories, such as Non-Uniform Rational B-Splines (NURBS), Bézier curves, and clothoid splines, has emerged as a transformative approach to optimizing tool paths for HSM. These polynomial-based methods allow for smoother tool motion, reduced feedrate fluctuations, and improved kinematic continuity, addressing the limitations of traditional linear and circular interpolation techniques.
This article explores the principles, methodologies, and advancements in high-performance NC systems for HSM, with a particular focus on polynomial trajectories. It delves into the mathematical foundations of polynomial curves, their implementation in NC systems, and their impact on machining performance. Detailed comparisons of various trajectory formats, control algorithms, and their practical applications are provided, supported by comprehensive tables. The discussion is structured to provide a scientific and rigorous examination of the subject, suitable for researchers, engineers, and practitioners in the field of advanced manufacturing.
Historical Context of Numerical Control and High-Speed Machining
The development of numerical control (NC) began in the 1940s and 1950s, with early systems relying on punched tape to encode tool movements. These systems, pioneered by innovators like John T. Parsons and MIT, marked a significant shift from manual machining to automated processes. The introduction of computer numerical control (CNC) in the 1970s, enabled by minicomputers and later microprocessors, revolutionized manufacturing by allowing more complex and flexible programming. CNC systems use G-code and M-code to define tool paths and machine operations, typically generated through computer-aided design (CAD) and computer-aided manufacturing (CAM) software.
High-speed machining emerged in the late 20th century as a response to the demand for faster production cycles and higher precision in industries producing complex geometries, such as turbine blades and medical implants. HSM typically involves spindle speeds exceeding 10,000 RPM and feed rates that challenge the dynamic capabilities of machine tools. Traditional linear interpolation (G01 commands) and circular interpolation (G02/G03 commands) often result in discontinuities at segment junctions, leading to feedrate reductions, increased machining time, and potential surface defects. Polynomial trajectories were introduced to address these issues, offering smoother transitions and better kinematic performance.
The evolution of NC and HSM has been driven by advancements in computational power, servo control systems, and trajectory planning algorithms. Polynomial trajectories, in particular, have gained prominence due to their ability to represent complex curves with continuous derivatives, ensuring smooth motion and minimizing mechanical stress on machine tools. This section provides a foundation for understanding the role of polynomial trajectories in modern NC systems, setting the stage for a detailed exploration of their mathematical and practical aspects.
Mathematical Foundations of Polynomial Trajectories
Polynomial Curves and Their Properties
Polynomial trajectories in NC systems are mathematical representations of tool paths that use polynomial functions to define the position, velocity, and acceleration of the tool. Unlike linear or circular paths, polynomial curves offer higher-order continuity (C^2 or higher), ensuring smooth transitions in velocity and acceleration. Common polynomial representations include Bézier curves, B-splines, and NURBS, each with distinct mathematical properties suited to HSM.
A polynomial curve in parametric form can be expressed as:
[ \mathbf{P}(u) = \sum_{i=0}^n \mathbf{P}_i B_i(u), \quad u \in [0,1] ]
where (\mathbf{P}_i) are control points, (B_i(u)) are basis functions, and (u) is the parametric variable. The degree of the polynomial determines the smoothness and flexibility of the curve. For instance, a cubic polynomial (degree 3) provides C^2 continuity, meaning the curve has continuous first and second derivatives, which is critical for jerk-limited motion in HSM.
Bézier Curves
Bézier curves are defined by a set of control points and Bernstein polynomials. A cubic Bézier curve, commonly used in NC systems, is given by:
[ \mathbf{P}(u) = (1-u)^3 \mathbf{P}_0 + 3u(1-u)^2 \mathbf{P}_1 + 3u^2(1-u) \mathbf{P}_2 + u^3 \mathbf{P}_3 ]
The control points (\mathbf{P}_0, \mathbf{P}_1, \mathbf{P}_2, \mathbf{P}_3) define the shape of the curve, with (\mathbf{P}_0) and (\mathbf{P}_3) being the endpoints and (\mathbf{P}_1) and (\mathbf{P}_2) influencing the curve’s curvature. Bézier curves are computationally efficient and widely used for corner smoothing and path transitions in HSM.
B-Splines and NURBS
B-splines generalize Bézier curves by allowing multiple polynomial segments to be joined with specified continuity. A B-spline curve is defined as:
[ \mathbf{P}(u) = \sum_{i=0}^n \mathbf{P}i N{i,k}(u) ]
where (N_{i,k}(u)) are B-spline basis functions of degree (k), determined by a knot vector. NURBS extend B-splines by incorporating weights, enabling the representation of complex shapes like conic sections:
[ \mathbf{P}(u) = \frac{\sum_{i=0}^n w_i \mathbf{P}i N{i,k}(u)}{\sum_{i=0}^n w_i N_{i,k}(u)} ]
NURBS are particularly valuable in HSM due to their flexibility in modeling freeform surfaces directly from CAD models, reducing the need for segmentation into linear or circular paths.
Clothoid Splines
Clothoid splines, or Euler spirals, have a linearly varying curvature, making them ideal for smooth transitions in high-speed applications. Their curvature (\kappa) is defined as:
[ \kappa(s) = a + bs ]
where (s) is the arc length, and (a) and (b) are constants. Clothoid splines are used in corner smoothing to minimize jerk and ensure kinematic continuity, particularly in 5-axis machining.
Feedrate Scheduling and Jerk Limitation
Polynomial trajectories enable advanced feedrate scheduling to minimize fluctuations and respect machine constraints (velocity, acceleration, and jerk). The feedrate profile is often modeled as a polynomial function to achieve jerk-limited motion, reducing vibrations and improving surface quality. For a cubic feedrate profile, the velocity (v(t)) can be expressed as:
[ v(t) = a_0 + a_1 t + a_2 t^2 + a_3 t^3 ]
where coefficients (a_i) are determined based on kinematic constraints. Jerk, the derivative of acceleration, is limited to prevent mechanical stress:
[ j(t) = \frac{d^3 \mathbf{P}(t)}{dt^3} ]
This mathematical framework underpins the design of polynomial trajectories for HSM, enabling precise control over tool motion.
Implementation of Polynomial Trajectories in NC Systems
Integration with CAD/CAM Systems
Polynomial trajectories are typically generated from CAD models using CAM software, which translates geometric designs into tool paths. The process involves:
-
Surface Modeling: The CAD model defines the workpiece geometry as a set of surfaces (e.g., NURBS surfaces).
-
Tool Path Generation: CAM software computes polynomial trajectories based on the surface geometry, tool geometry, and machining parameters.
-
Post-Processing: The tool paths are converted into G-code or proprietary formats compatible with the CNC controller.
NURBS interpolation, supported by modern CNC systems like Fanuc and Siemens, allows direct processing of polynomial curves, reducing segmentation errors and improving efficiency.
Real-Time Interpolation
Real-time interpolation of polynomial trajectories requires efficient algorithms to compute tool positions at high frequencies (typically 1 kHz or higher). The Taylor series expansion is commonly used to approximate the tool position:
[ u_{t+\Delta t} = u_t + \frac{v(t)}{|\mathbf{P}'(u_t)|} \Delta t + \frac{1}{2} \frac{a(t)}{|\mathbf{P}'(u_t)|} \Delta t^2 + \dots ]
where (v(t)) and (a(t)) are the feedrate and acceleration, and (\mathbf{P}'(u)) is the derivative of the curve. This method ensures accurate tracking of the tool path while respecting kinematic limits.
Corner Smoothing and Path Optimization
Corner smoothing is critical in HSM to eliminate discontinuities at linear segment junctions. Polynomial curves like Bézier or clothoid splines are inserted at corners to ensure C^2 continuity. The dual-Bézier transition algorithm, for example, smooths both translational and rotational axes in 5-axis machining, reducing feedrate fluctuations and improving surface quality. The optimization process involves:
-
Geometric Constraints: Ensuring the smoothed path stays within tolerance.
-
Kinematic Constraints: Limiting velocity, acceleration, and jerk.
-
Computational Efficiency: Using analytical solutions to avoid iterative computations.
Intelligent Agents and Machine Learning
Recent advancements incorporate intelligent agents and machine learning for trajectory optimization. Deep learning models, such as the MCRL model with linear attention mechanisms, analyze G-code to identify and smooth defective paths. Optimization algorithms like the novel adaptive coati optimization algorithm (NACOA) enhance path smoothness, as demonstrated in machining gear models and complex surfaces.
Advantages of Polynomial Trajectories in HSM
Smoothness and Surface Quality
Polynomial trajectories provide higher-order continuity, reducing vibrations and improving surface finish. Linear interpolation often results in tangential discontinuities, causing feedrate drops and surface marks. Polynomial curves ensure smooth transitions, minimizing these issues.
Reduced Machining Time
By maintaining higher feedrates through smooth paths, polynomial trajectories reduce machining time. For example, NURBS-based tool paths can decrease cycle times by up to 30% compared to linear interpolation for complex geometries.
Flexibility and Compatibility
Polynomial formats are compatible with CAD/CAM systems and modern CNC controllers, enabling seamless integration into existing workflows. NURBS, in particular, are widely supported, making them a standard for HSM applications.
Kinematic Performance
Jerk-limited polynomial trajectories reduce mechanical stress on machine tools, extending tool life and improving reliability. This is particularly important in HSM, where high accelerations can lead to wear and tear.
Challenges and Limitations
Computational Complexity
Generating and interpolating polynomial trajectories requires significant computational resources, especially for 5-axis machining. Real-time interpolation must balance accuracy and speed to avoid delays in the control loop.
Parameterization Issues
Proper parameterization of polynomial curves is critical to avoid feedrate fluctuations. Poor parameterization can lead to uneven tool motion, negating the benefits of polynomial trajectories.
Machine Constraints
The benefits of polynomial trajectories are limited by the machine’s dynamic capabilities. Older CNC systems may not support NURBS interpolation, requiring upgrades or alternative approaches.
Error Sensitivity
Polynomial trajectories are sensitive to numerical errors in CAD/CAM systems or CNC controllers, which can affect accuracy. Robust algorithms, such as feed correction polynomials, are needed to mitigate these issues.
Comparative Analysis of Trajectory Formats
The following tables compare polynomial trajectories with traditional linear and circular interpolation methods, focusing on key performance metrics.
Table 1: Comparison of Trajectory Formats
Trajectory Type |
Continuity |
Feedrate Stability |
Surface Quality |
Computational Complexity |
Compatibility with CNC |
---|---|---|---|---|---|
Linear (G01) |
C^0 |
Low (discontinuities) |
Poor (surface marks) |
Low |
High |
Circular (G02/G03) |
C^1 |
Moderate |
Moderate |
Moderate |
High |
Bézier Curves |
C^2 or higher |
High |
High |
Moderate |
Moderate |
NURBS |
C^2 or higher |
High |
High |
High |
High (modern systems) |
Clothoid Splines |
C^2 |
Very High |
High |
Moderate |
Moderate |
Table 2: Performance Metrics for HSM Applications
Metric |
Linear Interpolation |
Circular Interpolation |
NURBS |
Clothoid Splines |
---|---|---|---|---|
Cycle Time Reduction (%) |
Baseline |
10-15% |
20-30% |
15-25% |
Surface Roughness (Ra, µm) |
1.5-2.0 |
1.0-1.5 |
0.5-1.0 |
0.7-1.2 |
Jerk (m/s³) |
Uncontrolled |
50-100 |
20-50 |
10-30 |
Tool Life Extension (%) |
Baseline |
5-10% |
15-20% |
10-15% |
Table 3: Application Suitability
Application |
Linear |
Circular |
NURBS |
Clothoid |
---|---|---|---|---|
2D Contouring |
High |
High |
Moderate |
Moderate |
3D Freeform Surfaces |
Low |
Moderate |
High |
Moderate |
5-Axis Machining |
Low |
Low |
High |
High |
High-Speed Drilling |
High |
Moderate |
Low |
Low |
Case Studies and Practical Applications
Aerospace Industry
In aerospace, polynomial trajectories are used to machine complex components like turbine blades and fuselage panels. NURBS-based tool paths enable precise contouring of freeform surfaces, reducing machining time by 25% and improving surface finish (Ra < 1.0 µm).
Automotive Industry
Automotive molds and dies benefit from clothoid splines for corner smoothing, achieving up to 20% faster cycle times and reduced tool wear. The dual-Bézier transition algorithm has been successfully applied to 5-axis machining of engine components.
Biomedical Engineering
The production of custom implants requires high precision and smooth surfaces. NURBS trajectories ensure accurate machining of complex geometries, with cycle time reductions of 15-20% compared to linear interpolation.
Future Trends and Innovations
Digital Twin Technology
Digital twins integrate real-time data from CNC machines to optimize polynomial trajectories dynamically. By simulating tool paths and machine dynamics, digital twins can predict and mitigate errors, enhancing HSM performance.
AI and Machine Learning
AI-driven trajectory optimization, using models like MCRL and NACOA, is poised to revolutionize HSM. These systems can autonomously adjust tool paths based on real-time feedback, improving efficiency and reducing defects.
Hybrid Manufacturing
The integration of additive and subtractive manufacturing (HASM) leverages polynomial trajectories to combine 3D printing and HSM, enabling the production of complex parts with minimal material waste.
Conclusion
High-performance NC systems, enhanced by polynomial trajectories, have transformed high-speed machining by enabling smoother tool paths, reduced cycle times, and improved surface quality. The mathematical elegance of polynomial curves, coupled with advancements in CAD/CAM integration and real-time interpolation, has made them indispensable in modern manufacturing. Despite challenges like computational complexity and machine limitations, ongoing innovations in AI, digital twins, and hybrid manufacturing promise to further enhance their capabilities. The comprehensive comparison tables provided highlight the superiority of polynomial trajectories over traditional methods, making them a critical tool for industries demanding precision and efficiency.
Reprint Statement: If there are no special instructions, all articles on this site are original. Please indicate the source for reprinting:https://www.cncmachiningptj.com/,thanks!
PTJ® provides a full range of Custom Precision cnc machining china services.ISO 9001:2015 &AS-9100 certified. 3, 4 and 5-axis rapid precision CNC machining services including milling, turning to customer specifications,Capable of metal & plastic machined parts with +/-0.005 mm tolerance.Secondary services include CNC and conventional grinding, drilling,die casting,sheet metal and stamping.Providing prototypes, full production runs, technical support and full inspection.Serves the automotive, aerospace, mold&fixture,led lighting,medical,bicycle, and consumer electronics industries. On-time delivery.Tell us a little about your project's budget and expected delivery time. We will strategize with you to provide the most cost-effective services to help you reach your target,Welcome to Contact us ( sales@pintejin.com ) directly for your new project.
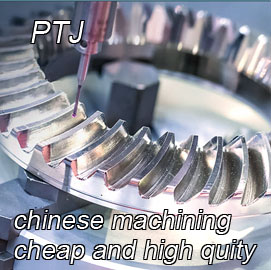
- 5 Axis Machining
- Cnc Milling
- Cnc Turning
- Machining Industries
- Machining Process
- Surface Treatment
- Metal Machining
- Plastic Machining
- Powder Metallurgy Mold
- Die Casting
- Parts Gallery
- Auto Metal Parts
- Machinery Parts
- LED Heatsink
- Building Parts
- Mobile Parts
- Medical Parts
- Electronic Parts
- Tailored Machining
- Bicycle Parts
- Aluminum Machining
- Titanium Machining
- Stainless Steel Machining
- Copper Machining
- Brass Machining
- Super Alloy Machining
- Peek Machining
- UHMW Machining
- Unilate Machining
- PA6 Machining
- PPS Machining
- Teflon Machining
- Inconel Machining
- Tool Steel Machining
- More Material