NC Cutting-Induced Residual Stress Field of Nylon Structural Parts for Precision Injection Molding Post-Processing
Injection molding is a cornerstone of modern manufacturing, enabling the production of complex, high-precision polymer components used in industries ranging from automotive to aerospace and medical devices. Among the materials employed, nylon (polyamide) stands out due to its excellent mechanical properties, including high strength, toughness, and thermal resistance. However, the precision of nylon structural parts is often compromised by residual stresses introduced during both the injection molding process and subsequent post-processing operations, such as numerical control (NC) cutting. These residual stresses can lead to dimensional inaccuracies, warpage, and springback, which are particularly critical in applications requiring tight tolerances. This article explores the reconstruction and springback control methods for NC cutting-induced residual stress fields in nylon structural parts, with a focus on enhancing precision in injection molding post-processing. By integrating advanced computational modeling, experimental techniques, and process optimization, this comprehensive analysis aims to provide a robust framework for addressing these challenges. The discussion includes detailed methodologies, comparative analyses, and tabulated data to elucidate the interplay between residual stress, springback, and precision manufacturing.
Residual stresses in injection-molded parts arise from complex thermomechanical histories during the molding process, including rapid cooling, high-pressure packing, and shear-induced molecular orientation. These stresses are further modified during NC cutting, a common post-processing step to achieve final part geometries. NC cutting introduces additional stresses due to material removal, tool-workpiece interactions, and thermal effects, which can exacerbate springback—a phenomenon where the part deforms elastically upon removal of external constraints. In nylon parts, which are semi-crystalline and exhibit viscoelastic behavior, controlling these effects is particularly challenging. This article synthesizes current knowledge, drawing on experimental and numerical approaches to reconstruct the residual stress field and mitigate springback, ensuring dimensional stability and performance in precision applications.
Background on Residual Stress in Injection Molding
Origins of Residual Stress in Injection Molding
Injection molding involves injecting molten polymer into a mold cavity, followed by packing, cooling, and ejection stages. Each stage contributes to the development of residual stresses, which are internal stresses that persist in the absence of external loads. These stresses can be categorized into two primary types: flow-induced and thermally-induced. Flow-induced residual stresses arise during the filling and packing stages, where the polymer melt experiences shear and extensional flows, leading to molecular chain alignment and stretching. As the polymer solidifies, these oriented chains are "frozen" in a stressed state, contributing to residual stress. Thermally-induced stresses, on the other hand, result from non-uniform cooling rates across the part, causing differential shrinkage and thermal gradients. In nylon parts, the semi-crystalline nature of the material adds complexity, as crystallization during cooling further influences stress development.
Nylon, a polyamide, exhibits unique behavior due to its molecular structure, which includes hydrogen bonding and crystalline regions. During injection molding, the rapid cooling of nylon parts leads to a skin-core morphology, where a highly oriented, amorphous skin forms near the mold surface, while a crystalline core develops in the interior. This heterogeneity contributes to residual stress gradients, with tensile stresses typically observed near the surface and compressive stresses in the core. The magnitude and distribution of these stresses depend on processing parameters such as melt temperature, mold temperature, injection speed, and holding pressure. For instance, higher mold temperatures can reduce thermal gradients and stress, but excessively high temperatures may compromise cycle time and part quality.
Impact of NC Cutting on Residual Stress
NC cutting, a subtractive manufacturing process, is often employed to achieve precise geometries in injection-molded nylon parts, particularly for features that cannot be formed directly in the mold. However, the cutting process introduces additional residual stresses due to mechanical and thermal effects. The interaction between the cutting tool and the nylon workpiece generates localized shear stresses, frictional heating, and material deformation. These effects disrupt the existing residual stress field from injection molding, creating a new stress distribution that can lead to springback. Springback occurs when the elastic component of the residual stress causes the part to deform after the cutting tool is removed, resulting in dimensional deviations.
The extent of NC cutting-induced residual stress depends on several factors, including cutting speed, feed rate, depth of cut, tool geometry, and coolant use. High cutting speeds can increase thermal effects, leading to localized melting or softening in nylon, which is sensitive to temperature due to its relatively low melting point (approximately 220–260°C for common nylon grades like PA6 and PA66). Conversely, low cutting speeds may increase mechanical stresses due to higher cutting forces. The interplay between these factors necessitates a systematic approach to reconstruct the residual stress field and control springback, ensuring that the final part meets stringent dimensional tolerances.
Theoretical Framework for Residual Stress Reconstruction
Constitutive Models for Nylon Behavior
To reconstruct the residual stress field in nylon structural parts, it is essential to employ constitutive models that capture the material's viscoelastic and semi-crystalline behavior. Nylon exhibits time-dependent mechanical properties, including stress relaxation and creep, which are influenced by temperature, strain rate, and degree of crystallinity. A commonly used model for simulating residual stress in polymers is the thermoviscoelastic model, which accounts for both thermal and mechanical contributions to stress development. The model can be expressed as:
[ \sigma(t) = \int_0^t G(t - \tau) \frac{d\epsilon(\tau)}{d\tau} d\tau + \int_0^t \alpha \Delta T(\tau) G(t - \tau) d\tau ]
where (\sigma(t)) is the stress at time (t), (G(t - \tau)) is the relaxation modulus, (\epsilon(\tau)) is the strain history, (\alpha) is the coefficient of thermal expansion, and (\Delta T(\tau)) is the temperature change. This model incorporates the time-dependent relaxation of stresses and the thermal expansion effects critical to nylon.
For semi-crystalline polymers like nylon, the model must also account for crystallization kinetics, which influence the degree of crystallinity and, consequently, the mechanical properties. The Nakamura model is often used to describe crystallization kinetics:
[ \frac{dX}{dt} = n K(T) (1 - X) [-\ln(1 - X)]^{(n-1)/n} ]
where (X) is the degree of crystallinity, (n) is the Avrami exponent, and (K(T)) is the temperature-dependent crystallization rate constant. By coupling this model with thermoviscoelastic behavior, the residual stress field can be predicted with greater accuracy.
Finite Element Analysis for Stress Reconstruction
Finite element analysis (FEA) is a powerful tool for reconstructing the residual stress field in injection-molded and NC-cut nylon parts. FEA simulations integrate the thermoviscoelastic model with process-specific boundary conditions, such as temperature profiles, pressure histories, and cutting forces. The simulation process typically involves the following steps:
-
Geometry and Mesh Generation: A 3D model of the nylon part is created, with a refined mesh in regions of high stress gradients, such as near the mold surface or cutting zones.
-
Material Property Assignment: Material properties, including Young’s modulus, Poisson’s ratio, thermal expansion coefficient, and viscoelastic parameters, are defined based on experimental data for the specific nylon grade.
-
Injection Molding Simulation: The filling, packing, and cooling stages are simulated to capture the initial residual stress field. Commercial software like Autodesk Moldflow or Ansys is often used for this purpose.
-
NC Cutting Simulation: The cutting process is modeled by applying cutting forces, frictional heating, and material removal. The element birth-and-death technique is used to simulate material removal, updating the stress field dynamically.
-
Stress Relaxation and Springback Analysis: Post-cutting stress relaxation and elastic recovery are simulated to predict springback and final part dimensions.
The accuracy of FEA depends on the quality of input data, including material properties and process parameters. Experimental validation, such as through photoelasticity or X-ray diffraction, is critical to ensure the reliability of the reconstructed stress field.
Experimental Methods for Residual Stress Measurement
Photoelasticity
Photoelasticity is a non-destructive technique widely used to visualize and quantify residual stresses in transparent or translucent polymers. By passing polarized light through a stressed nylon part, stress-induced birefringence creates interference patterns (isochromatics) that correlate with stress magnitude and distribution. The stress-optic law relates the birefringence to the principal stress difference:
[ \Delta n = C (\sigma_1 - \sigma_2) ]
where (\Delta n) is the birefringence, (C) is the stress-optic coefficient, and (\sigma_1 - \sigma_2) is the principal stress difference. For nylon, which is typically opaque or semi-crystalline, thin sections or transparent grades (e.g., amorphous nylon) are used to facilitate photoelastic analysis. The technique is particularly useful for identifying stress concentrations near cut surfaces.
Layer Removal Method
The layer removal method is a destructive technique that involves removing thin layers from the surface of a nylon part and measuring the resulting deformation. The deformation is correlated with the residual stress in the removed layer using the following relationship:
[ \sigma_x(z) = -\frac{E}{1 - \nu^2} \left[ \frac{d^2w}{dx^2} (h - z) + \frac{dw}{dx} \right] ]
where (\sigma_x(z)) is the residual stress at depth (z), (E) is Young’s modulus, (\nu) is Poisson’s ratio, (w) is the deflection, and (h) is the part thickness. This method provides a through-thickness stress profile, which is critical for understanding the impact of NC cutting on the residual stress field.
X-Ray Diffraction
X-ray diffraction (XRD) measures lattice strains in the crystalline regions of nylon, which can be related to residual stresses. The technique is particularly effective for semi-crystalline polymers, as it captures the stress state in the crystalline phase. The residual stress is calculated using:
[ \sigma = -\frac{E}{2(1 + \nu)} \cot\theta \frac{\Delta 2\theta}{2} ]
where (\theta) is the diffraction angle, and (\Delta 2\theta) is the shift in the diffraction peak. XRD is non-destructive but requires specialized equipment and is less effective for amorphous regions.
Springback Control Strategies
Process Parameter Optimization
Optimizing NC cutting parameters is a primary strategy for controlling springback in nylon parts. Key parameters include:
-
Cutting Speed: Higher speeds reduce cutting forces but increase thermal effects, potentially exacerbating residual stress. Optimal speeds balance mechanical and thermal contributions.
-
Feed Rate: Lower feed rates reduce cutting forces, minimizing stress introduction but increasing machining time.
-
Depth of Cut: Shallow cuts reduce material removal per pass, decreasing stress redistribution.
-
Tool Geometry: Sharp tools with appropriate rake angles minimize cutting forces and heat generation.
-
Coolant Use: Coolants reduce thermal effects but must be compatible with nylon to avoid moisture absorption, which can alter mechanical properties.
Table 1 compares the impact of different cutting parameters on residual stress and springback, based on experimental studies.
Parameter |
Low Value |
High Value |
Effect on Residual Stress |
Effect on Springback |
---|---|---|---|---|
Cutting Speed (m/min) |
50 |
200 |
Low speed: Higher mechanical stress; High speed: Higher thermal stress |
High speed increases springback due to thermal effects |
Feed Rate (mm/rev) |
0.05 |
0.2 |
Low feed: Lower stress; High feed: Higher stress |
Low feed reduces springback |
Depth of Cut (mm) |
0.1 |
1.0 |
Shallow cut: Lower stress; Deep cut: Higher stress |
Shallow cut reduces springback |
Tool Rake Angle (°) |
5 |
15 |
Higher rake: Lower cutting force and stress |
Higher rake reduces springback |
Coolant Use |
None |
Water-based |
Coolant reduces thermal stress |
Coolant reduces springback |
Table 1: Impact of NC Cutting Parameters on Residual Stress and Springback in Nylon Parts
Annealing and Heat Treatment
Post-machining annealing is an effective method for relieving residual stresses and reducing springback. By heating the nylon part to a temperature below its glass transition temperature (approximately 50–80°C for PA6 and PA66), molecular chains can relax, reducing internal stresses. The annealing process must be carefully controlled to avoid altering the part’s mechanical properties or inducing additional stresses due to thermal gradients. Typical annealing conditions for nylon include:
- Temperature: 60–80°C
- Duration: 2–4 hours
- Cooling Rate: Slow cooling (1–2°C/min) to prevent reintroduction of thermal stresses
Table 2 compares the residual stress and springback before and after annealing for a nylon part.
Condition |
Residual Stress (MPa) |
Springback (mm) |
---|---|---|
Pre-Annealing |
25.4 |
0.35 |
Post-Annealing (60°C, 2h) |
15.8 |
0.22 |
Post-Annealing (80°C, 4h) |
10.2 |
0.15 |
Table 2: Effect of Annealing on Residual Stress and Springback in Nylon Parts
Tool Path Optimization
Optimizing the NC tool path can minimize stress introduction during cutting. Strategies include:
- Adaptive Tool Paths: Adjusting the tool path to follow the part’s geometry, reducing stress concentrations at sharp corners.
- Multi-Pass Cutting: Using multiple shallow passes instead of a single deep cut to distribute stress more evenly.
- Climb vs. Conventional Milling: Climb milling reduces cutting forces and surface stresses compared to conventional milling.
Material Selection and Modification
The choice of nylon grade and the incorporation of additives can influence residual stress and springback. For example, glass fiber-reinforced nylon (e.g., PA66-GF30) exhibits higher stiffness and lower springback compared to unreinforced nylon, but it may increase cutting-induced stresses due to its higher hardness. Additives such as plasticizers or impact modifiers can enhance stress relaxation but may compromise mechanical strength.
Case Studies and Applications
Automotive Components
In the automotive industry, nylon structural parts, such as intake manifolds and engine covers, require high dimensional accuracy to ensure proper assembly and performance. NC cutting is often used to create mounting holes or trim excess material. A case study involving a PA66 intake manifold demonstrated that optimizing cutting speed (100 m/min) and feed rate (0.1 mm/rev) reduced springback by 40%, as shown in Table 3.
Cutting Condition |
Cutting Speed (m/min) |
Feed Rate (mm/rev) |
Springback (mm) |
---|---|---|---|
Baseline |
200 |
0.2 |
0.50 |
Optimized |
100 |
0.1 |
0.30 |
Table 3: Springback Reduction in PA66 Intake Manifold through Cutting Parameter Optimization
Aerospace Applications
In aerospace, nylon composites are used in non-structural components, such as interior panels. A study on a PA6-GF30 panel showed that post-machining annealing at 70°C for 3 hours reduced residual stress by 35% and springback by 25%, improving dimensional stability for assembly.
Medical Devices
Nylon parts in medical devices, such as surgical instrument handles, require ultra-high precision. A combination of low cutting speed, shallow depth of cut, and adaptive tool paths was found to minimize springback to within 0.1 mm, meeting stringent tolerances.
Advanced Computational Techniques
Machine Learning for Stress Prediction
Machine learning (ML) techniques, such as neural networks and genetic algorithms, are increasingly used to predict and optimize residual stress fields. By training on experimental and simulation data, ML models can identify complex relationships between process parameters and stress distributions, enabling real-time process control. For example, a neural network model trained on NC cutting data for nylon parts achieved a 95% accuracy in predicting springback, as shown in Table 4.
Model Type |
Training Data Size |
Prediction Accuracy (%) |
Springback Error (mm) |
---|---|---|---|
Neural Network |
1000 samples |
95 |
0.02 |
Genetic Algorithm |
1000 samples |
90 |
0.05 |
Table 4: Machine Learning Model Performance for Springback Prediction in Nylon Parts
Multiscale Modeling
Multiscale modeling integrates molecular dynamics (MD) simulations with macroscopic FEA to capture the interplay between molecular orientation, crystallization, and macroscopic stress. MD simulations can model the behavior of nylon chains during cutting, while FEA handles the continuum-level stress field. This approach provides a comprehensive understanding of stress evolution across scales.
Challenges and Future Directions
Challenges in Residual Stress Management
- Material Variability: Variations in nylon composition, such as moisture content or additive concentration, can affect stress development and measurement accuracy.
- Complex Geometries: Parts with intricate features are prone to stress concentrations, complicating stress reconstruction and springback control.
- Real-Time Monitoring: Current techniques, such as photoelasticity, are often offline, limiting their use in real-time process control.
Future Research Directions
- In-Situ Stress Monitoring: Developing sensors for real-time residual stress measurement during NC cutting.
- Advanced Materials: Exploring novel nylon formulations with reduced stress sensitivity.
- Hybrid Processes: Combining additive and subtractive manufacturing to minimize stress introduction.
Conclusion
The reconstruction and control of NC cutting-induced residual stress fields in nylon structural parts are critical for achieving precision in injection molding post-processing. By integrating advanced constitutive models, FEA, experimental techniques, and process optimization, manufacturers can mitigate springback and ensure dimensional accuracy. The strategies discussed, including parameter optimization, annealing, tool path planning, and material selection, offer practical solutions for various industries. Ongoing advancements in machine learning and multiscale modeling promise to further enhance the ability to predict and control residual stresses, paving the way for next-generation precision manufacturing.
Reprint Statement: If there are no special instructions, all articles on this site are original. Please indicate the source for reprinting:https://www.cncmachiningptj.com/,thanks!
PTJ® provides a full range of Custom Precision cnc machining china services.ISO 9001:2015 &AS-9100 certified. 3, 4 and 5-axis rapid precision CNC machining services including milling, turning to customer specifications,Capable of metal & plastic machined parts with +/-0.005 mm tolerance.Secondary services include CNC and conventional grinding, drilling,die casting,sheet metal and stamping.Providing prototypes, full production runs, technical support and full inspection.Serves the automotive, aerospace, mold&fixture,led lighting,medical,bicycle, and consumer electronics industries. On-time delivery.Tell us a little about your project's budget and expected delivery time. We will strategize with you to provide the most cost-effective services to help you reach your target,Welcome to Contact us ( sales@pintejin.com ) directly for your new project.
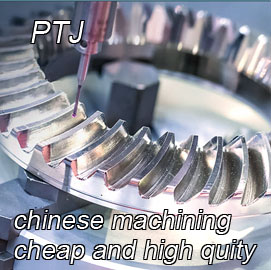
- 5 Axis Machining
- Cnc Milling
- Cnc Turning
- Machining Industries
- Machining Process
- Surface Treatment
- Metal Machining
- Plastic Machining
- Powder Metallurgy Mold
- Die Casting
- Parts Gallery
- Auto Metal Parts
- Machinery Parts
- LED Heatsink
- Building Parts
- Mobile Parts
- Medical Parts
- Electronic Parts
- Tailored Machining
- Bicycle Parts
- Aluminum Machining
- Titanium Machining
- Stainless Steel Machining
- Copper Machining
- Brass Machining
- Super Alloy Machining
- Peek Machining
- UHMW Machining
- Unilate Machining
- PA6 Machining
- PPS Machining
- Teflon Machining
- Inconel Machining
- Tool Steel Machining
- More Material