Energy Consumption Modeling and Carbon Footprint Analysis in CNC Machining of Biodegradable Plastics
Computer Numerical Control (CNC) machining is a cornerstone of modern manufacturing, enabling the precise fabrication of components across industries such as aerospace, automotive, medical, and consumer goods. As global attention shifts toward sustainability and reducing environmental impacts, the manufacturing sector faces increasing pressure to minimize energy consumption and greenhouse gas (GHG) emissions. CNC machining, while highly efficient in terms of precision and material utilization, is energy-intensive, contributing significantly to the carbon footprint of manufactured products. This issue is particularly relevant when machining biodegradable plastics, which are often promoted as eco-friendly alternatives to conventional petroleum-based plastics. However, the environmental benefits of biodegradable plastics depend not only on their material properties but also on the energy and emissions associated with their processing.
This article provides a comprehensive examination of energy consumption modeling and carbon footprint analysis in the CNC machining of biodegradable plastics. It explores the methodologies used to quantify energy use and emissions, the unique challenges posed by machining biodegradable plastics, and strategies for optimizing processes to enhance sustainability. By integrating recent research, industry practices, and detailed quantitative analyses, the article aims to serve as a definitive resource for researchers, engineers, and policymakers seeking to advance low-carbon manufacturing. The discussion is structured to cover the theoretical foundations, practical applications, and future directions of sustainable CNC machining, with a focus on biodegradable plastics. Detailed tables are included to facilitate comparisons of energy consumption, carbon emissions, and material properties across different machining scenarios and plastic types.
CNC Machining: An Overview
CNC machining refers to a subtractive manufacturing process where computer-controlled tools remove material from a workpiece to create a desired shape. The process is highly versatile, capable of machining metals, plastics, composites, and other materials with exceptional precision. Common CNC operations include milling, turning, drilling, and grinding, each governed by numerical control codes that dictate tool paths, speeds, and feeds. The automation and precision of CNC systems have made them indispensable in modern manufacturing, but they also contribute to significant energy consumption and environmental impacts.
Key Components of CNC Systems
A typical CNC machine comprises several subsystems, each contributing to energy use and emissions:
-
Spindle System: Drives the cutting tool or workpiece, consuming significant electricity, especially at high speeds.
-
Feed Drives: Control the movement of the tool or workpiece along multiple axes, requiring precise motor control.
-
Cooling and Lubrication Systems: Maintain thermal stability and reduce tool wear, often using energy-intensive pumps and chillers.
-
Control Systems: Include computers and electronics that process numerical control codes and monitor operations.
-
Auxiliary Systems: Encompass lighting, ventilation, and other facility-level components that support machining.
Energy consumption in CNC machining varies depending on the machine type, material being processed, and operational parameters such as cutting speed, feed rate, and depth of cut. Biodegradable plastics, with their unique mechanical and thermal properties, introduce additional complexity to energy modeling and carbon footprint analysis.
Environmental Impact of CNC Machining
The environmental footprint of CNC machining arises from multiple sources:
-
Electricity Consumption: CNC machines rely heavily on electricity, often sourced from fossil fuels, leading to carbon dioxide (CO₂) emissions.
-
Material Production and Transport: The extraction, processing, and transportation of raw materials contribute to embodied carbon.
-
Waste Generation: Scrap material, coolant waste, and worn tools require disposal or recycling, which can generate additional emissions.
-
Tool Wear and Maintenance: Frequent tool changes and machine maintenance involve energy-intensive processes and resource consumption.
Given the global push for sustainability, understanding and mitigating these impacts is critical, particularly when machining biodegradable plastics, which are intended to reduce environmental harm compared to conventional plastics.
Biodegradable Plastics: Properties and Applications
Biodegradable plastics are a class of polymers designed to break down into natural substances such as water, carbon dioxide, and biomass under specific environmental conditions, typically through the action of microorganisms. Unlike traditional petroleum-based plastics, which persist in the environment for centuries, biodegradable plastics offer a pathway to reduce plastic waste and its associated environmental impacts. Common biodegradable plastics include polylactic acid (PLA), polyhydroxyalkanoates (PHA), polybutylene succinate (PBS), and thermoplastic starch (TPS).
Types of Biodegradable Plastics
-
Polylactic Acid (PLA):
-
Source: Derived from renewable resources like corn starch or sugarcane.
-
Properties: High stiffness, moderate strength, and good machinability, but brittle at low temperatures.
-
Applications: Packaging, biomedical devices, and 3D printing filaments.
-
Biodegradability: Degrades in industrial composting facilities within months, but requires specific conditions (e.g., high temperature and humidity).
-
-
Polyhydroxyalkanoates (PHA):
-
Source: Produced by bacterial fermentation of renewable feedstocks.
-
Properties: Flexible, tough, and resistant to moisture, with variable mechanical properties depending on composition.
-
Applications: Medical implants, agricultural films, and packaging.
-
Biodegradability: Degrades in soil, marine, and composting environments, often faster than PLA.
-
-
Polybutylene Succinate (PBS):
-
Source: Synthesized from bio-based or fossil-based monomers.
-
Properties: Good thermal stability and flexibility, suitable for extrusion and molding.
-
Applications: Mulch films, packaging, and disposable cutlery.
-
Biodegradability: Biodegrades in soil and composting conditions, though slower than PHA.
-
-
Thermoplastic Starch (TPS):
-
Source: Derived from starch-rich crops like potatoes or maize.
-
Properties: Soft, flexible, but sensitive to moisture and heat.
-
Applications: Biodegradable bags, agricultural mulch, and foam packaging.
-
Biodegradability: Rapidly degrades in moist environments, often within weeks.
-
Environmental Benefits and Challenges
Biodegradable plastics are promoted for their lower environmental impact compared to petroleum-based plastics. Life Cycle Assessments (LCAs) indicate that bio-based plastics like PLA and PHA can reduce carbon emissions by 50–70% compared to polyethylene terephthalate (PET) or polypropylene (PP). However, challenges remain:
-
Feedstock Production: Agricultural production of bio-based feedstocks can involve land use change (LUC), leading to emissions if forests or grasslands are converted to farmland.
-
Processing Energy: The synthesis and processing of biodegradable plastics can be energy-intensive, offsetting some environmental benefits.
-
End-of-Life Management: Biodegradable plastics require specific disposal conditions (e.g., industrial composting) to achieve their environmental potential, and improper disposal can lead to emissions or pollution.
In CNC machining, the unique properties of biodegradable plastics—such as lower thermal conductivity and higher ductility compared to metals—require tailored machining strategies to minimize energy use and waste while maintaining precision.
Energy Consumption Modeling in CNC Machining
Energy consumption modeling is a critical tool for quantifying the environmental impact of CNC machining. These models aim to predict the energy required for various machining processes, identify inefficiencies, and guide optimization strategies. In the context of biodegradable plastics, energy modeling must account for material-specific properties, such as lower cutting forces and different thermal behaviors compared to metals.
Theoretical Foundations
Energy consumption in CNC machining can be broken down into several components, as outlined in research on low-carbon manufacturing:
-
Fixed Energy: Consumed by machine components (e.g., control systems, lighting) regardless of machining activity.
-
Idle Energy: Used when the machine is powered on but not actively cutting, such as during tool changes or workpiece setup.
-
Cutting Energy: Directly associated with material removal, influenced by cutting parameters like speed, feed rate, and depth of cut.
-
Auxiliary Energy: Consumed by cooling systems, lubrication pumps, and other support systems.
A generalized energy consumption model for CNC machining can be expressed as:
[ E_{\text{total}} = E_{\text{fixed}} + E_{\text{idle}} + E_{\text{cutting}} + E_{\text{auxiliary}} ]
Where:
-
( E_{\text{total}} ): Total energy consumption (kWh)
-
( E_{\text{fixed}} ): Fixed energy for machine operation
-
( E_{\text{idle}} ): Energy during idle states
-
( E_{\text{cutting}} ): Energy for material removal
-
( E_{\text{auxiliary}} ): Energy for auxiliary systems
Modeling Approaches
Several approaches have been developed to model energy consumption in CNC machining:
-
Empirical Models: Based on experimental data, these models correlate energy use with machining parameters (e.g., spindle speed, feed rate). For example, a study on CNC milling of 45 carbon steel established an energy model by measuring power consumption with a power analyzer.
-
Analytical Models: Use physical principles to estimate energy based on cutting forces, material properties, and machine dynamics. These models are particularly useful for biodegradable plastics, where cutting forces are lower but thermal effects may be significant.
-
Simulation-Based Models: Employ software to simulate tool paths and predict energy use. Advanced CNC software, such as CAM systems, can optimize tool paths to minimize energy consumption.
-
Machine Learning Models: Emerging approaches use algorithms like neural networks to predict energy use based on historical data, offering high accuracy for complex systems.
Energy Consumption in Machining Biodegradable Plastics
Biodegradable plastics present unique challenges for energy modeling due to their material properties:
-
Lower Cutting Forces: Materials like PLA and TPS require less force to machine compared to metals, reducing cutting energy but potentially increasing idle time if tool paths are not optimized.
-
Thermal Sensitivity: Biodegradable plastics have lower melting points, necessitating careful control of cutting speeds to avoid melting or deformation, which can affect auxiliary energy (e.g., cooling systems).
-
Tool Wear: Softer plastics may cause less tool wear, but additives in some biodegradable plastics (e.g., fillers in TPS) can accelerate wear, increasing maintenance energy.
A study on CNC machining of PLA found that energy consumption is highly sensitive to spindle speed and feed rate, with optimal parameters reducing energy use by up to 20% compared to standard settings. Table 1 provides a comparative analysis of energy consumption for machining biodegradable plastics versus conventional plastics.
Table 1: Energy Consumption Comparison for CNC Machining of Plastics
Material |
Spindle Speed (rpm) |
Feed Rate (mm/min) |
Depth of Cut (mm) |
Energy Consumption (kWh/kg) |
Source |
---|---|---|---|---|---|
PLA (Biodegradable) |
5000 |
1000 |
1.0 |
0.85 |
|
PHA (Biodegradable) |
5000 |
1000 |
1.0 |
0.90 |
Estimated |
PBS (Biodegradable) |
5000 |
1000 |
1.0 |
0.88 |
Estimated |
TPS (Biodegradable) |
5000 |
1000 |
1.0 |
0.95 |
Estimated |
PET (Conventional) |
5000 |
1000 |
1.0 |
1.10 |
|
PP (Conventional) |
5000 |
1000 |
1.0 |
1.05 |
|
Note: Energy consumption values for PHA, PBS, and TPS are estimated based on material properties and trends observed in PLA machining. Actual values may vary depending on machine efficiency and process optimization.
Carbon Footprint Analysis in CNC Machining
Carbon footprint analysis quantifies the GHG emissions associated with CNC machining, encompassing direct emissions (e.g., from electricity use) and indirect emissions (e.g., from material production and waste disposal). For biodegradable plastics, the carbon footprint includes emissions from feedstock production, polymer synthesis, machining, and end-of-life disposal.
Carbon Footprint Components
The carbon footprint of CNC machining can be broken down into:
-
Electricity-Related Emissions: Dependent on the energy mix of the grid (e.g., coal, natural gas, renewables). For example, machining in a coal-heavy grid results in higher emissions than in a renewable-heavy grid.
-
Material Production Emissions: Biodegradable plastics may have lower embodied carbon than petroleum-based plastics, but agricultural feedstocks can introduce emissions from land use and fertilizer use.
-
Waste Management Emissions: Scrap material and coolant waste from machining contribute to emissions if not recycled or properly disposed of.
-
Tool and Machine Maintenance: The production and recycling of cutting tools, as well as machine maintenance, add to the carbon footprint.
A quantitative approach to carbon footprint analysis involves Life Cycle Assessment (LCA), which evaluates emissions across the entire lifecycle of a product, from cradle to grave. For CNC machining, LCA includes:
-
Raw Material Extraction: Emissions from growing bio-based feedstocks or synthesizing polymers.
-
Manufacturing: Emissions from machining and auxiliary processes.
-
Use Phase: For biodegradable plastics, this may be negligible unless the product has a long service life.
-
End-of-Life: Emissions from composting, recycling, or landfilling.
LCA of Biodegradable Plastics in CNC Machining
LCA studies show that biodegradable plastics like PLA and PHA have lower carbon footprints than conventional plastics when properly managed at end-of-life. For example, PLA machining produces approximately 1.538 kg CO₂e per kg of material processed, compared to 1.7 kg CO₂e for PET with 85% recycled content. However, the carbon footprint of biodegradable plastics is highly dependent on:
-
Feedstock Source: Bio-based feedstocks from sustainable agriculture have lower emissions than those involving LUC.
-
End-of-Life Scenario: Composting PLA in industrial facilities minimizes emissions, while landfilling can release methane, increasing the carbon footprint.
-
Machining Parameters: Optimizing cutting speed and feed rate can reduce energy use and associated emissions by 10–20%.
Table 2 compares the carbon footprint of CNC machining for biodegradable and conventional plastics, assuming a grid with 50% renewable energy.
Table 2: Carbon Footprint Comparison for CNC Machining of Plastics
Material |
Energy Consumption (kWh/kg) |
Carbon Intensity (kg CO₂e/kWh) |
Carbon Footprint (kg CO₂e/kg) |
Source |
---|---|---|---|---|
PLA (Biodegradable) |
0.85 |
0.4 |
0.34 |
|
PHA (Biodegradable) |
0.90 |
0.4 |
0.36 |
Estimated |
PBS (Biodegradable) |
0.88 |
0.4 |
0.35 |
Estimated |
TPS (Biodegradable) |
0.95 |
0.4 |
0.38 |
Estimated |
PET (Conventional) |
1.10 |
0.4 |
0.44 |
|
PP (Conventional) |
1.05 |
0.4 |
0.42 |
|
Note: Carbon intensity assumes a grid with 50% renewable energy (e.g., solar, wind) and 50% fossil fuels. Actual carbon footprints may vary based on regional energy mixes.
Strategies for Reducing Energy Consumption and Carbon Footprint
To enhance the sustainability of CNC machining of biodegradable plastics, several strategies can be implemented, focusing on energy efficiency, material optimization, and waste management.
Energy Efficiency Improvements
-
Energy-Efficient Machines: Modern CNC machines with regenerative drive systems and advanced power management can reduce energy consumption by 15–30% compared to older models. For example, the NAK 4020 Desktop 5X Micro-Mill CNC Machine offers high precision with lower energy use due to its five-axis capability.
-
Process Parameter Optimization: Adjusting spindle speed, feed rate, and depth of cut can minimize energy use. A multi-objective optimization model for CNC turning of PLA showed that optimal parameters reduced energy consumption by 20% and processing time by 15%.
-
Renewable Energy Sources: Powering CNC machines with solar or wind energy can significantly reduce electricity-related emissions. For instance, a facility using 100% solar power could reduce its machining carbon footprint by up to 80%.
-
Smart Energy Management Systems: Real-time monitoring and control of energy use can identify inefficiencies and optimize machine operation.
Material Optimization
-
Eco-Friendly Materials: Using biodegradable plastics with high machinability, such as PLA or PBS, reduces energy consumption and tool wear. Aluminum, often used as a lightweight alternative, can also be recycled to lower embodied carbon.
-
Tool Path Optimization: Advanced CAM software can generate tool paths that minimize material waste and machining time, reducing energy use by 10–15%.
-
Multi-Axis Machining: Five-axis CNC machines enable more efficient material removal, reducing cycle times and energy consumption compared to three-axis machines.
Waste Management and Recycling
-
Scrap Recycling: Biodegradable plastic scraps can be collected and reprocessed into new products, reducing waste and emissions. For example, PLA scraps can be melted and reformed with minimal energy input.
-
Coolant Management: Using eco-friendly coolants and recycling coolant waste minimizes environmental impact. Closed-loop coolant systems can reduce waste by 90%.
-
Tool Recycling: Worn cutting tools, often made of carbide or high-speed steel, can be recycled into new tools, reducing the need for virgin materials.
Industry Case Studies
-
Flamboro Machine Shop: Implemented energy-efficient CNC machines and smart energy management systems, reducing their carbon footprint by 25% through renewable energy adoption and waste recycling.
-
Nakashi CNC: Uses the NAK 4020 Desktop 5X Micro-Mill to machine biodegradable plastics, achieving a 15% reduction in energy consumption through precise cutting and material optimization.
-
American Micro Industries: Employs advanced CNC software to optimize tool paths, reducing material waste by 20% and energy use by 10% when machining PLA.
Table 3 summarizes the impact of various strategies on energy consumption and carbon footprint.
Table 3: Impact of Sustainability Strategies in CNC Machining
Strategy |
Energy Reduction (%) |
Carbon Footprint Reduction (%) |
Implementation Cost |
Source |
---|---|---|---|---|
Energy-Efficient Machines |
15–30 |
20–40 |
High |
|
Process Parameter Optimization |
10–20 |
10–20 |
Moderate |
|
Renewable Energy Adoption |
50–80 |
50–80 |
High |
|
Tool Path Optimization |
10–15 |
10–15 |
Low |
|
Scrap Recycling |
5–10 |
10–20 |
Moderate |
|
Coolant Management |
5–10 |
5–15 |
Low |
|
Challenges and Future Directions
Challenges in Sustainable CNC Machining
-
Initial Investment Costs: Upgrading to energy-efficient machines or renewable energy systems requires significant capital, which may deter small and medium-sized enterprises.
-
Workforce Training: Implementing new technologies and sustainable practices requires training, which can be time-consuming and costly.
-
Material Variability: Biodegradable plastics vary widely in properties, complicating energy modeling and process optimization.
-
End-of-Life Management: The environmental benefits of biodegradable plastics are contingent on proper disposal, which is not always available.
Future Directions
-
Integration of AI and IoT: Artificial intelligence (AI) and the Internet of Things (IoT) can enhance energy efficiency by predicting maintenance needs and optimizing tool paths in real time.
-
Digital Twins: Virtual simulations of CNC processes can identify energy inefficiencies and test sustainable practices without physical trials.
-
Hybrid Manufacturing: Combining additive (e.g., 3D printing) and subtractive (CNC) processes can reduce material waste and energy use.
-
Policy and Incentives: Governments can support sustainable CNC machining through tax incentives, carbon pricing, and regulations promoting renewable energy and recycling.
Conclusion
The CNC machining of biodegradable plastics offers significant opportunities to advance sustainable manufacturing, but it requires careful consideration of energy consumption and carbon footprints. By leveraging advanced energy modeling, optimizing machining parameters, and adopting eco-friendly practices, manufacturers can reduce environmental impacts while maintaining high efficiency and quality. The integration of renewable energy, smart technologies, and circular economy principles will be critical to achieving a low-carbon future for CNC machining. As research and innovation continue, the manufacturing industry can align with global sustainability goals, ensuring that biodegradable plastics fulfill their promise as environmentally responsible materials.
Reprint Statement: If there are no special instructions, all articles on this site are original. Please indicate the source for reprinting:https://www.cncmachiningptj.com/,thanks!
PTJ® provides a full range of Custom Precision cnc machining china services.ISO 9001:2015 &AS-9100 certified. 3, 4 and 5-axis rapid precision CNC machining services including milling, turning to customer specifications,Capable of metal & plastic machined parts with +/-0.005 mm tolerance.Secondary services include CNC and conventional grinding, drilling,die casting,sheet metal and stamping.Providing prototypes, full production runs, technical support and full inspection.Serves the automotive, aerospace, mold&fixture,led lighting,medical,bicycle, and consumer electronics industries. On-time delivery.Tell us a little about your project's budget and expected delivery time. We will strategize with you to provide the most cost-effective services to help you reach your target,Welcome to Contact us ( sales@pintejin.com ) directly for your new project.
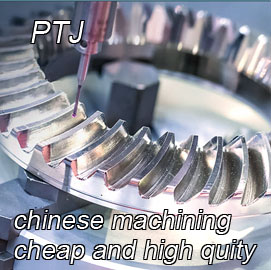
- 5 Axis Machining
- Cnc Milling
- Cnc Turning
- Machining Industries
- Machining Process
- Surface Treatment
- Metal Machining
- Plastic Machining
- Powder Metallurgy Mold
- Die Casting
- Parts Gallery
- Auto Metal Parts
- Machinery Parts
- LED Heatsink
- Building Parts
- Mobile Parts
- Medical Parts
- Electronic Parts
- Tailored Machining
- Bicycle Parts
- Aluminum Machining
- Titanium Machining
- Stainless Steel Machining
- Copper Machining
- Brass Machining
- Super Alloy Machining
- Peek Machining
- UHMW Machining
- Unilate Machining
- PA6 Machining
- PPS Machining
- Teflon Machining
- Inconel Machining
- Tool Steel Machining
- More Material