CNC Machining of High-Precision Plastic Fasteners for Space Station Maintenance Systems and Mechanical Behavior Stability
High-precision plastic fasteners are critical components in the maintenance systems of space stations, such as the International Space Station (ISS) and emerging platforms like the Lunar Gateway. These fasteners, often machined using computer numerical control (CNC) techniques, must withstand extreme environmental conditions, including vacuum, thermal cycling, radiation, and microgravity, while maintaining mechanical stability. The study of their mechanical behavior—encompassing strength, creep resistance, fatigue life, and dimensional stability—is essential to ensure reliability in space applications. This article explores the CNC machining processes for producing these fasteners, the selection of engineering plastics, and the scientific investigation of their mechanical behavior under simulated and actual space conditions. It integrates comparative analyses through detailed tables to elucidate material properties, machining parameters, and performance metrics.
Importance of Plastic Fasteners in Space Station Maintenance
Space station maintenance systems rely on fasteners to secure modular components, such as life support systems, scientific experiments, and structural panels, which require frequent assembly and disassembly. Metal fasteners, while robust, pose challenges in space due to their weight, susceptibility to galvanic corrosion, and thermal conductivity, which can exacerbate heat loss or gain. Plastic fasteners, conversely, offer advantages including low weight, corrosion resistance, electrical insulation, and tailored mechanical properties. Materials like polyetheretherketone (PEEK), polytetrafluoroethylene (PTFE), and polyimide (PI) are favored for their high strength-to-weight ratios and stability in harsh environments.
The primary function of these fasteners in maintenance systems is to provide secure, repeatable connections without compromising the integrity of the joined components. For instance, fasteners used in extravehicular activity (EVA) tools must resist outgassing and maintain torque stability under vacuum conditions. The precision required in these applications necessitates advanced manufacturing techniques, with CNC machining being the preferred method due to its ability to achieve tight tolerances and complex geometries.
CNC Machining Processes for Plastic Fasteners
Overview of CNC Machining
CNC machining involves the use of computer-controlled tools to remove material from a workpiece, shaping it into a desired form. For plastic fasteners, CNC milling, turning, and drilling are commonly employed to produce screws, bolts, nuts, and specialized connectors. The process begins with a digital model, typically created using computer-aided design (CAD) software, which is translated into machine instructions via computer-aided manufacturing (CAM) software. Key considerations in CNC machining of plastics include tool selection, cutting parameters, and workpiece fixturing to prevent deformation.
Material Selection for CNC Machining
The choice of plastic material significantly influences machining outcomes and fastener performance. Common materials include:
-
PEEK: Known for its high tensile strength (90–100 MPa), thermal stability (up to 250°C), and resistance to radiation, PEEK is ideal for structural fasteners.
-
PTFE: With low friction and excellent chemical resistance, PTFE is suited for fasteners requiring minimal torque and resistance to aggressive fluids, though its low strength (20–30 MPa) limits load-bearing applications.
-
PI: Offering superior thermal stability (up to 300°C) and creep resistance, PI is used in high-temperature environments but is challenging to machine due to its hardness.
-
Polycarbonate (PC): Valued for transparency and impact resistance, PC is used in non-structural fasteners but is prone to stress cracking under sustained loads.
-
Nylon (PA): With good toughness and wear resistance, nylon is cost-effective but absorbs moisture, affecting dimensional stability in vacuum.
The table below compares key properties of these materials relevant to CNC machining and space applications.
Material |
Tensile Strength (MPa) |
Thermal Stability (°C) |
Radiation Resistance |
Machinability |
Outgassing (TML, %) |
Cost ($/kg) |
---|---|---|---|---|---|---|
PEEK |
90–100 |
250 |
High |
Moderate |
0.1–0.2 |
80–120 |
PTFE |
20–30 |
260 |
Moderate |
High |
0.05–0.1 |
20–40 |
PI |
80–120 |
300 |
Very High |
Low |
0.1–0.3 |
150–200 |
PC |
60–70 |
120 |
Low |
High |
0.3–0.5 |
5–10 |
Nylon (PA66) |
70–85 |
100 |
Moderate |
High |
0.5–1.0 |
3–8 |
Table 1: Comparison of Plastic Materials for CNC-Machined Fasteners in Space Applications. TML = Total Mass Loss per ASTM E595.
Machining Parameters
CNC machining of plastics requires optimized parameters to minimize thermal damage, burr formation, and dimensional inaccuracies. Key parameters include spindle speed, feed rate, depth of cut, and coolant use. Plastics with high thermal conductivity, like PEEK, tolerate higher cutting speeds, while softer materials like PTFE require lower speeds to prevent melting. The table below summarizes typical machining parameters for selected plastics.
Material |
Spindle Speed (RPM) |
Feed Rate (mm/min) |
Depth of Cut (mm) |
Coolant |
Tool Material |
---|---|---|---|---|---|
PEEK |
10,000–15,000 |
100–300 |
0.5–2.0 |
Air or Mist |
Carbide |
PTFE |
5,000–8,000 |
50–150 |
0.2–1.0 |
None |
HSS |
PI |
8,000–12,000 |
80–200 |
0.3–1.5 |
Air |
Diamond-Coated |
PC |
12,000–18,000 |
150–400 |
0.5–2.5 |
Air or Water |
Carbide |
Nylon |
10,000–14,000 |
100–250 |
0.5–2.0 |
Air |
HSS |
Table 2: Recommended CNC Machining Parameters for Plastic Fasteners.
Challenges in CNC Machining Plastics
Unlike metals, plastics exhibit viscoelastic behavior, leading to challenges such as:
-
Thermal Deformation: Heat generated during machining can cause melting or warping, particularly in low-melting-point plastics like PTFE.
-
Tool Wear: Hard plastics like PI accelerate tool wear, necessitating diamond-coated or carbide tools.
-
Burr Formation: Soft plastics are prone to burrs, requiring post-machining deburring processes.
-
Dimensional Stability: Moisture-absorbing plastics like nylon may deform in vacuum, affecting tolerances.
Advanced techniques, such as cryogenic cooling and ultrasonic-assisted machining, are being explored to mitigate these issues, though their adoption in space-grade fastener production remains limited.
Mechanical Behavior of Plastic Fasteners in Space Environments
Overview of Mechanical Behavior
The mechanical behavior of plastic fasteners in space is governed by their response to tensile, compressive, shear, and fatigue loads under extreme conditions. Key properties include:
-
Strength: Ability to resist failure under static loads.
-
Creep: Time-dependent deformation under constant stress, critical in long-duration missions.
-
Fatigue Life: Resistance to cyclic loading, relevant for fasteners in vibrating systems.
-
Fracture Toughness: Ability to resist crack propagation, important in impact-prone environments.
These properties are tested under simulated space conditions, including vacuum, thermal cycling (−150°C to +150°C), and radiation exposure (up to 10^6 Gy).
Environmental Factors Affecting Mechanical Stability
Vacuum and Outgassing
In the vacuum of space (10^-6 Pa), plastic fasteners may outgas, releasing volatile compounds that can contaminate nearby optics or electronics. Materials are tested per ASTM E595, with acceptable total mass loss (TML) below 1% and collected volatile condensable material (CVCM) below 0.1%. PEEK and PTFE exhibit low outgassing, making them suitable for sensitive applications.
Thermal Cycling
Space stations experience thermal cycling due to orbital day-night transitions. Fasteners must maintain dimensional stability and mechanical integrity across wide temperature ranges. PI and PEEK outperform PC and nylon, which soften or become brittle at extreme temperatures.
Radiation Exposure
Cosmic and solar radiation degrade polymer chains, reducing strength and toughness. PI and PEEK resist radiation-induced embrittlement better than PC, which yellows and cracks after prolonged exposure.
Microgravity
While microgravity has minimal direct impact on fastener mechanics, it influences machining processes on Earth by affecting chip evacuation and coolant flow. CNC machines for space-grade fasteners are designed to simulate microgravity effects during testing.
Experimental Studies on Mechanical Behavior
Studies conducted by NASA, ESA, and academic institutions have characterized the mechanical behavior of plastic fasteners. For example:
-
Tensile Testing: PEEK fasteners exhibited a yield strength of 95 MPa at 23°C, dropping to 80 MPa at 200°C, per ASTM D638.
-
Creep Testing: PI fasteners showed a creep strain of 0.5% after 1,000 hours at 150°C under 50 MPa, compared to 2% for nylon.
-
Fatigue Testing: PEEK fasteners withstood 10^6 cycles at 50% of ultimate tensile strength, outperforming PC (10^5 cycles).
The table below summarizes mechanical test results for selected fasteners.
Material |
Yield Strength (MPa, 23°C) |
Creep Strain (%, 150°C, 1,000 hr) |
Fatigue Life (Cycles, 50% UTS) |
Fracture Toughness (MPa·m^0.5) |
---|---|---|---|---|
PEEK |
95 |
0.8 |
10^6 |
4.5 |
PTFE |
25 |
3.0 |
10^4 |
1.5 |
PI |
110 |
0.5 |
10^6 |
5.0 |
PC |
65 |
2.5 |
10^5 |
2.0 |
Nylon |
80 |
2.0 |
10^5 |
3.0 |
Table 3: Mechanical Properties of Plastic Fasteners Under Space-Relevant Conditions. UTS = Ultimate Tensile Strength.
Modeling and Simulation
Finite element analysis (FEA) and molecular dynamics (MD) simulations predict fastener behavior under complex loading. FEA models incorporate viscoelastic constitutive equations to simulate creep and stress relaxation, while MD simulations reveal radiation-induced chain scission at the molecular level. These tools guide material selection and fastener design, reducing reliance on costly physical testing.
Design Considerations for Space-Grade Plastic Fasteners
Geometric Design
Fastener geometry, including thread profile, head shape, and shank diameter, is optimized for specific applications. Common designs include:
-
Threaded Fasteners: Metric or unified threads (e.g., M3, 1/4-20) with coarse pitches to reduce stress concentration.
-
Captive Fasteners: Integrated retaining features to prevent loss in microgravity.
-
Custom Connectors: Non-standard shapes for proprietary maintenance tools.
Tolerances are typically ±0.01 mm to ensure fit and function in EVA gloves or robotic manipulators.
Surface Treatments
Surface treatments enhance fastener performance:
-
Plasma Etching: Improves adhesion for coatings and reduces outgassing.
-
Lubricious Coatings: PTFE or molybdenum disulfide coatings reduce friction in threaded fasteners.
-
UV-Resistant Layers: Protect PC fasteners from solar degradation.
Quality Control
Non-destructive testing (NDT) methods, such as X-ray computed tomography and ultrasonic inspection, verify internal integrity. Dimensional metrology using coordinate measuring machines (CMMs) ensures compliance with specifications.
Applications in Space Station Maintenance Systems
Plastic fasteners are integral to:
-
Life Support Systems: Securing oxygen generators and water recyclers, where corrosion resistance is critical.
-
Scientific Payloads: Mounting experiments with minimal electromagnetic interference.
-
Structural Repairs: Temporary fixes during EVAs, leveraging lightweight and easy-to-install designs.
-
Robotic Systems: Fasteners in robotic arms, requiring high fatigue life.
Case studies, such as the ISS’s Alpha Magnetic Spectrometer (AMS-02) repair in 2019, highlight the reliability of PEEK fasteners in high-stakes missions.
Future Trends and Research Directions
Advanced Materials
Emerging polymers, such as liquid crystal polymers (LCPs) and carbon-fiber-reinforced PEEK, promise enhanced strength and stiffness. Nanocomposites with graphene or carbon nanotubes may improve radiation resistance.
Additive Manufacturing Integration
Hybrid manufacturing, combining CNC machining with 3D printing, enables rapid prototyping of complex fasteners. Selective laser sintering (SLS) of PEEK is being explored for on-orbit production.
In-Situ Testing
Deploying testbeds on the Lunar Gateway will allow real-time evaluation of fastener performance, reducing reliance on Earth-based simulations.
Sustainability
Recyclable plastics and closed-loop manufacturing processes are being developed to minimize waste in space missions.
Conclusion
CNC machining of high-precision plastic fasteners is a cornerstone of space station maintenance systems, enabling reliable, lightweight, and corrosion-resistant connections. Materials like PEEK, PTFE, and PI, machined with optimized parameters, meet the stringent demands of space environments. Mechanical behavior studies, supported by experimental testing and simulations, ensure stability under vacuum, thermal cycling, and radiation. As space exploration advances, innovations in materials, manufacturing, and testing will further enhance the role of plastic fasteners in sustaining human presence beyond Earth.
Reprint Statement: If there are no special instructions, all articles on this site are original. Please indicate the source for reprinting:https://www.cncmachiningptj.com/,thanks!
PTJ® provides a full range of Custom Precision cnc machining china services.ISO 9001:2015 &AS-9100 certified. 3, 4 and 5-axis rapid precision CNC machining services including milling, turning to customer specifications,Capable of metal & plastic machined parts with +/-0.005 mm tolerance.Secondary services include CNC and conventional grinding, drilling,die casting,sheet metal and stamping.Providing prototypes, full production runs, technical support and full inspection.Serves the automotive, aerospace, mold&fixture,led lighting,medical,bicycle, and consumer electronics industries. On-time delivery.Tell us a little about your project's budget and expected delivery time. We will strategize with you to provide the most cost-effective services to help you reach your target,Welcome to Contact us ( sales@pintejin.com ) directly for your new project.
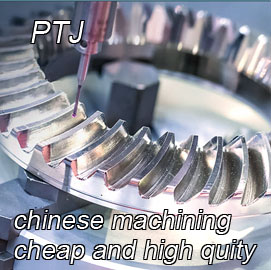
- 5 Axis Machining
- Cnc Milling
- Cnc Turning
- Machining Industries
- Machining Process
- Surface Treatment
- Metal Machining
- Plastic Machining
- Powder Metallurgy Mold
- Die Casting
- Parts Gallery
- Auto Metal Parts
- Machinery Parts
- LED Heatsink
- Building Parts
- Mobile Parts
- Medical Parts
- Electronic Parts
- Tailored Machining
- Bicycle Parts
- Aluminum Machining
- Titanium Machining
- Stainless Steel Machining
- Copper Machining
- Brass Machining
- Super Alloy Machining
- Peek Machining
- UHMW Machining
- Unilate Machining
- PA6 Machining
- PPS Machining
- Teflon Machining
- Inconel Machining
- Tool Steel Machining
- More Material