Spacecraft parts are expected to be "self-sufficient"
In the process of human exploration of space, the "supply line problem" of equipment and materials has been preventing people from flying further into space. With the rapid development of 3D printing technology, it is becoming possible to achieve "self-sufficiency" of spacecraft components. From receiving the design drawings to pressing the "print" button, a wrench was quickly manufactured-can you imagine this is an operation performed by an astronaut in a zero-gravity environment? In fact, this is the first appearance of a 3D printer in space.
It is reported that NASA and the US Space Manufacturing Company have signed a contract to jointly develop a space 3D printing system. At the Second World Intelligence Conference in Tianjin, which ended not long ago, some researchers said that the application potential of space 3D printing technology in the field of aerospace intelligent manufacturing is huge in the future.
The booming "space manufacturing plant"
Beginning in 2010, NASA and the U.S. Space Manufacturing Corporation have conducted hundreds of experiments in microgravity environments. In order to support the development of 3D printing technology, the United States also established the "National Additive Manufacturing Innovation Alliance" in August 2012. In 2014, the world's first space 3D printer arrived at the International Space Station on board the "Dragon" spacecraft, and successively printed a series of space-specific parts and components, unveiling the prelude to mankind's "manufacturing in space".
In fact, opening a "space manufacturing plant" is not complicated. The concept is consistent with traditional printing. 3D printing is a rapid prototyping technology that builds objects based on model files and uses bondable materials such as powdered metals and plastics through layer-by-layer printing. Traditional 3D printing technology includes process flows such as layered processing, overlay molding, and layer-by-layer heating.
However, 3D printing in space is not simply "building blocks." Every 3D printer launched into the sky has a smart "core". The astronauts receive the digital three-dimensional model of the parts uploaded on the ground through the space-to-earth communication, and after the post-software processing of the 3D printer, can they automatically generate specific control data and print operation codes. Therefore, as long as there is a constant "net" between the sky and the earth, theoretically any tool can be designed on the ground, and then handed over to a 3D printer to complete the "space manufacturing".
In recent years, space 3D printing technology has been highly valued by countries all over the world. In March 2016, NASA shipped an upgraded version of the 3D printer to the International Space Station, achieving larger volume and higher resolution printing in the space environment; the University of Birmingham in the United Kingdom developed a printer that can operate in zero gravity. A metal 3D printer in operation; a German research institution also "printed" metal tools in a zero-gravity environment this year.
The "right assistant" for space travel
At the end of the last century, the Hubble Space Telescope, which gathered human wisdom, was launched into space. Due to the tiny errors in the mirror manufacturing, the Hubble telescope is directly reduced to "myopia". Under the conditions of aerospace technology at that time, people could only carry out another space launch and specially install "myopia glasses" for the Hubble Telescope. The entire repair process requires the completion of operations such as ground manufacturing, air-to-ground transportation, and space assembly. It eventually took 4 years and hundreds of millions of dollars to restore this precision equipment to normal.
Now, with space 3D printing, the "eye diseases" encountered by the Hubble Telescope can be "surgery" on-site in space. Space 3D printing can print parts with different functions directly in outer space. As we all know, the size of spacecraft is mainly limited by the launch vehicle, and space parts manufacturing plants can be built using space 3D printing to realize "space manufacturing".
3D printing technology shows strong application value and development potential in the aerospace field, not only shortening the production cycle of aerospace products, reducing costs, and further improving product performance. As a brand-new production method, products made by space 3D printing can handle tasks that are difficult to complete with traditional manufacturing processes. For example, a part needs to withstand high temperature on one side and high strength on the other side. 3D printing can show its talents.
Nowadays, people pay attention to "travel light", especially in space flight. Carrying a 3D printer into space can save you from the huge hassle of carrying tens of thousands of parts and components, and you only need to carry a few kilograms of 3D printing "cartridges".
In addition, space 3D printing technology can greatly reduce the dependence of space flight on the ground. Compared with the semi-annual space replenishment, 3D printing only takes a few hours to produce the parts that need to be replaced, which will greatly improve the flexibility and maintenance efficiency of the space station, and reduce the space station’s dependence on ground systems.
At present, people have begun to design a space manufacturing system, which will directly print antennas, battery panels and other components and necessities for work and life in space. NASA's Jet Propulsion Laboratory is developing a standard space 3D printing process, which aims to use new technologies to be compatible with different metal materials and to produce parts that are more adaptable to the space application environment. In the future, space 3D printers will have the ability to produce various tools, parts and daily necessities on a small scale, and will be standard equipment for manned space flight and space exploration.
"Turn space junk into treasure"
To help astronauts traveling in space drink water normally, people also designed a zero-gravity water cup by using the surface tension of water, which ingeniously solved the problem of water floating everywhere under the condition of weightlessness in space. However, such an ingenious product is manufactured on the ground, and then taken off by "Sky Express" is undoubtedly costly.
The emergence of space 3D printing will play an important role in human space travel.
The National Aeronautics and Space Administration once envisaged to print out the entire satellite directly in space, and put it into orbit after being produced and assembled by the "Space Manufacturing Plant". Space 3D printing technology can also make shelters and tools needed for humans to board other planets. The European Space Agency is exploring the use of 3D printing technology to build a lunar base, and the National Aeronautics and Space Administration has specially launched a 3D printing Mars habitat competition.
Space 3D printing is even more magical, it can "turn decay into magic" like a magician. Once a product made in space is damaged, it can be reused by simply melting it into raw materials. The US Space Manufacturing Company is conducting research on reusable space 3D printing materials. The "Phoenix" research project carried out by the Advanced Research Projects Agency of the US Department of Defense aims to clean up space junk by dismantling old satellites and reassemble them into a brand new space equipment with parts and components of the old satellites. In the future, space 3D printing can also use obsolete satellites in the earth's orbit, or go directly to the planet to obtain materials for "space manufacturing".
Space 3D printing can not only print all kinds of components, but also food. Using space 3D printers can print all kinds of edible raw materials into rich and varied nutrition packages, and astronauts can also experience the feeling of being a "chef" in space.
Of course, for 3D printing to go to space, a series of technical problems must be solved. The biggest obstacle is "weightlessness." In the space environment, materials and glue will "fly", which requires special design on the printer structure. In addition, how to solve problems such as the diffusion of exhaust gas generated by space printing needs to be further studied and perfected.
Link to this article: Spacecraft parts are expected to be "self-sufficient"
Reprint Statement: If there are no special instructions, all articles on this site are original. Please indicate the source for reprinting:https://www.cncmachiningptj.com
PTJ® provides a full range of Custom manufacturer of precision fabricated parts made from aluminum parts, brass parts, bronze, copper parts, high yield alloy, low carbon steel investment casting, high carbon steel and stainless steel alloy. Capable of handling parts up to +/-0.0002 in. tolerance. Processes include cnc turning, cnc milling, laser cutting,.ISO 9001:2015 &AS-9100 certified.
Tell us a little about your project’s budget and expected delivery time. We will strategize with you to provide the most cost-effective services to help you reach your target,You are welcome to contact us directly ( sales@pintejin.com ) .
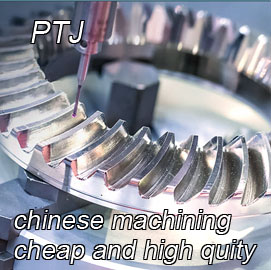
- 5 Axis Machining
- Cnc Milling
- Cnc Turning
- Machining Industries
- Machining Process
- Surface Treatment
- Metal Machining
- Plastic Machining
- Powder Metallurgy Mold
- Die Casting
- Parts Gallery
- Auto Metal Parts
- Machinery Parts
- LED Heatsink
- Building Parts
- Mobile Parts
- Medical Parts
- Electronic Parts
- Tailored Machining
- Bicycle Parts
- Aluminum Machining
- Titanium Machining
- Stainless Steel Machining
- Copper Machining
- Brass Machining
- Super Alloy Machining
- Peek Machining
- UHMW Machining
- Unilate Machining
- PA6 Machining
- PPS Machining
- Teflon Machining
- Inconel Machining
- Tool Steel Machining
- More Material