Why has silicone become the No. 1 3D printing material?
The materials currently available for 3D printing include resins, alloys (such as nickel-based chromium, cobalt, aluminum, titanium, etc.), polymers, ceramics, and plastics. With ACEO® Imagine Series 100, WACKER became the first company to industrially produce elastomers through 3D printing. Before WACKER first introduced this revolutionary technology, 3D printing was not possible for silicones. Today, 100% silicone has been used for modeling or small batch production, which has benefited many industries. So, what is so special about "100% silicone" or "true elastomer" for the 3D printing industry?
In this regard, we specially invited Dr. Bernd Pachaly from the German WACKER ACEO® expert team. The following will share with you some of his insights on the application of silicone materials to 3D printing technology in the form of an interview. The mystery of silicone 3D printing.
Guests interviewed in this issue:
Dr. Bernd Pachaly
Ph.D. in Chemistry from the Technical University of Berlin, post-doctoral research at the University of Wisconsin in 1984. He has many years of research and work experience in the field of silicones. In 1985, he joined the Wacker Chemie Group. He successively served as the head of the core R&D department, the R&D manager of the silicone business, and the business team leader of the silicone engineering department. In 2013, he took over the silicone innovation business and has been responsible for the silicone 3D printing project since 2017.
Q1. Dr. Pachaly, what exactly is silicone?
A: The scientific name of organosilicon is polysiloxane, which is a general name for a kind of polymer whose main chain is alternated with silicon and oxygen atoms. Among these materials, silicone rubber is an important member, which is made from liquid silicone rubber or solid silicone rubber through a variety of cross-linking reactions.
Q2. What type of silicone does ACEO® use?
A: ACEO® uses liquid silicone rubber, which is already well-known because it is widely used in injection molding by WACKER. As one of WACKER’s brands, ACEO® has benefited from WACKER’s 70 years of expertise in silicones and has continued to develop such silicones to meet specific application requirements.
The main components of silicone rubber are silicone polymer, cross-linking agent, reinforcing filler and catalyst. These materials form rubber after cross-linking reaction with high-viscosity mixture. No organics or copolymers are used, and the finished product is real rubber (100% silicone), not a "rubber-like" material. In addition, this cross-linking reaction is a platinum-catalyzed hydrosilylation reaction with no by-products or residues.
Q3. Compared with other types of rubber, what is special about 100% silicone?
A: What makes synthetic rubber unattainable is that silicone has unique chemical and mechanical properties, such as flexibility and elasticity/weather resistance/wide application temperature range/radiation resistance/biological inertness.
Under normal circumstances, silicone rubber is biocompatible and meets the requirements of food applications. Because of its own stability, no additives and stabilizers are needed.
Q4. Compared with silicone injection molding, what are the advantages of silicone 3D printing?
A: Silicone 3D printing can directly convert digital models into real objects without using any tools or molds, thereby reducing production costs, especially when used for modeling or small batch production.
Another advantage of silicone 3D printing is to save production time: the process cycle can be greatly shortened; at the same time, the product can be quickly improved during product development.
Each 3D printed part can be personalized to meet the needs of industries such as oral or dental care, and facilitate the production of anatomical models that simulate human tissues.
Q5. What applications and industries can benefit from 3D printed 100% silicone?
A: In industrial fields such as transportation or mechanical equipment, rapid modeling, small batch production of products, and on-demand production of spare parts are all very important.
In the medical field, with silicone 3D printing, personalized customized applications such as dental clips or anatomical models can be produced, and ACEO® products can also help customize the treatment according to the different conditions of specific patients, thereby further promoting medical education and surgery. Formulation of the previous plan.
WACKER has more than 70 years of silicone expertise and technology, so every process meets the highest industry standards.
Link to this article: Why has silicone become the No. 1 3D printing material?
Reprint Statement: If there are no special instructions, all articles on this site are original. Please indicate the source for reprinting:https://www.cncmachiningptj.com
PTJ® provides a full range of Custom manufacturer of precision fabricated parts made from aluminum parts, brass parts, bronze, copper parts, high yield alloy, low carbon steel investment casting, high carbon steel and stainless steel alloy. Capable of handling parts up to +/-0.0002 in. tolerance. Processes include cnc turning, cnc milling, laser cutting,.ISO 9001:2015 &AS-9100 certified.
Tell us a little about your project’s budget and expected delivery time. We will strategize with you to provide the most cost-effective services to help you reach your target,You are welcome to contact us directly ( sales@pintejin.com ) .
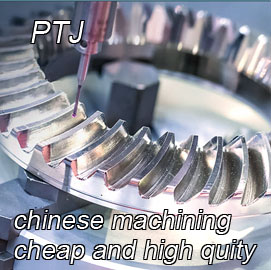
- 5 Axis Machining
- Cnc Milling
- Cnc Turning
- Machining Industries
- Machining Process
- Surface Treatment
- Metal Machining
- Plastic Machining
- Powder Metallurgy Mold
- Die Casting
- Parts Gallery
- Auto Metal Parts
- Machinery Parts
- LED Heatsink
- Building Parts
- Mobile Parts
- Medical Parts
- Electronic Parts
- Tailored Machining
- Bicycle Parts
- Aluminum Machining
- Titanium Machining
- Stainless Steel Machining
- Copper Machining
- Brass Machining
- Super Alloy Machining
- Peek Machining
- UHMW Machining
- Unilate Machining
- PA6 Machining
- PPS Machining
- Teflon Machining
- Inconel Machining
- Tool Steel Machining
- More Material