Micro-metal 3D printing process for in-situ microstructure control is available
On July 30, the reporter learned that a group of researchers from the Department of Mechanical Engineering at the University of Texas at Dallas invented an electrochemical-based metal 3D printing method named Local Pulse Electrodeposition (L-PED). Using this method, the team obtained in-situ control of the metal microstructure during the printing process. L-PED is not affected by post-processing. By adjusting the process parameters, the mechanical and electrical properties of 3D printing pure crystalline metal are enhanced.
Micro metal 3D printing using L-PED
In L-PED, the electrolyte of the selected metal for electrodeposition is confined to the nozzle tip. When the nozzle approaches the substrate, metal ions are deposited on the meniscus formed between the conductive substrate and the nozzle. A very high current is repeatedly applied between the nozzle and the substrate at millisecond intervals.
Under standard conditions, the team managed to obtain a current efficiency of 90 ± 5%, which means that the presence of impurities or oxygen is minimal. The precise and controlled movement of the relative positions of the nozzle and the substrate enables the structure to be printed in the desired 3D geometry. With this method, different geometric shapes can be printed, such as freestanding lines, micro-pillars (μ-pillars) and layer-by-layer structures.
Increase strength, ductility and conductivity
Using the L-PED process, directly 3D print dozens of copper μ pillars. Dozens of copper μ-pillars are directly 3D printed. The focused ion beam prepares similar μ-pillars with an average current density of 2-35 nm s^-1 from the thin film of the material of interest... For this parameter range, all printed copper μ-pillars contain double boundaries. It is known that there are parallel twin boundary arrays to enhance mechanical and electrical performance.
The key parameter that controls the microstructure of L-PED is the average current density. The average current density is directly proportional to the average deposition rate. As the deposition rate increases, the density of twin boundaries increases. Randomly oriented grains become more cylindrical and smaller in size, and the twin grain boundaries inside the grains become more uniform.
In order to study the relationship between the microstructure and performance of printed copper, the printed copper pillars were tested in an in-situ scanning electron microscope (SEM) micro-compression experiment. The results of the in-situ SEM nanochemistry experiment showed that the average current density increased by about 1.7 times, resulting in an increase of the metal deposition rate by about 1.4 times, which resulted in an increase in the flow stress of the printed metal by about 44%. In particular, by changing the microstructure during printing, the flow stress of 3D printed copper can be adjusted to 3-5 times that of bulk copper.
Three different average current densities and compressed μ-columns were used to perform in-situ SEM micro-compression experiments on the printed μ-columns.
The researchers successfully demonstrated the control of the density and orientation of the twin boundary and grain size by controlling the average current density. The fine copper 3D printing has well-aligned and high-density double borders, showing high strength, ductility and conductivity.
Micro-scale metal additive manufacturing
Although the current focus of micro AM is to create tiny structures with complex geometries, one of the most severe challenges facing the industry is the control of the material properties of the printed metal. Examples of currently available physical and chemical metal μ-AM processes are direct ink printing (DIW) and electrohydrodynamic printing (EHD). DIW and EHD generally require heat treatment to remove the organic matrix from the printed composite. Usually as high as 400-500°C, significant porosity, densification and grain growth of the metallic phase often occur during post-treatment.
To achieve in-situ control of microstructures, L-PED is significantly better than the currently available patterning and 3D printing metal processes. Soheil Daryadel, one of the co-authors of the study, said: "This important advancement eliminates the need for post-processing engineering microstructures, which often adversely affect material properties."
Due to its excellent material properties, L-PED has paved the way for the realization of functional applications of metal μ-AM, such as electronic devices, micro-electromechanical systems (MEMS), optical devices and sensors. But at present, only a limited amount of metals can be deposited, including copper, platinum, and gold, and other metals and alloys will still be printed through L-PED in the future.
Link to this article: Micro-metal 3D printing process for in-situ microstructure control is available
Reprint Statement: If there are no special instructions, all articles on this site are original. Please indicate the source for reprinting:https://www.cncmachiningptj.com
PTJ® provides a full range of Custom Precision cnc machining china services.ISO 9001:2015 &AS-9100 certified.
Machining shop specializing in fabrication services for construction and transportation industries. Capabilities include plasma and oxy-fuel cutting, Tailored machining, MIG and Custom Aluminum Cnc Precision Milling Welding Jig Fixture, roll forming, assembly, Lathe machining stainless steel cnc machine shaft, shearing, and CNC Swiss Machining services. Materials handled include carbon and Passivation Stainless Steel Machining Cover Plate Parts.
Tell us a little about your project’s budget and expected delivery time. We will strategize with you to provide the most cost-effective services to help you reach your target,You are welcome to contact us directly ( sales@pintejin.com ) .
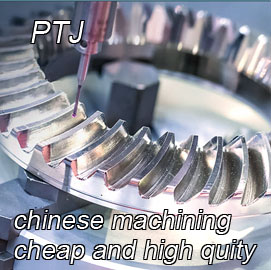
- 5 Axis Machining
- Cnc Milling
- Cnc Turning
- Machining Industries
- Machining Process
- Surface Treatment
- Metal Machining
- Plastic Machining
- Powder Metallurgy Mold
- Die Casting
- Parts Gallery
- Auto Metal Parts
- Machinery Parts
- LED Heatsink
- Building Parts
- Mobile Parts
- Medical Parts
- Electronic Parts
- Tailored Machining
- Bicycle Parts
- Aluminum Machining
- Titanium Machining
- Stainless Steel Machining
- Copper Machining
- Brass Machining
- Super Alloy Machining
- Peek Machining
- UHMW Machining
- Unilate Machining
- PA6 Machining
- PPS Machining
- Teflon Machining
- Inconel Machining
- Tool Steel Machining
- More Material