Why does shape memory alloy have memory?
There is another story about the discovery of the properties of SMA materials. Early research on this material began in the 1930s, when scientists studied some unexpected properties exhibited by different metals. Swedish chemist Arne Ölander discovered a pseudo-elasticity phenomenon while observing gold-cadmium alloys and described it. However, it was not until a laboratory accident about 30 years later that people really started to use the term "shape memory alloy"
The shape memory effect means that a solid material with a certain shape (usually a material with thermoelastic martensitic transformation) undergoes a certain limit of plastic deformation at a certain temperature (in the martensitic state Mf), and is heated to At a certain temperature (usually the material's martensite disappearance temperature Af), the material returns to its original state before deformation.
Shape memory alloy (SMA) is a new type of smart material. Its characteristic is that it can return to its original form at a certain temperature. Generally speaking, the environment where this characteristic occurs is high temperature. Its superelastic effect, High resistance characteristics, variability of elastic modulus at different temperatures and self-recovery function are not realized by general metal materials.
Principle of shape memory effect
The shape memory effect of the alloy is a special thermo-mechanical behavior, which is the result of the reversible transformation of the low temperature phase (martensite) produced by the thermoelastic martensite transformation to the high temperature phase (austenite) during heating.
Most shape memory alloys exhibit a shape memory effect through thermoelastic martensite transformation.
Ordinary martensitic transformation is a quenching strengthening method of steel, that is, heating the steel to a certain critical temperature for a period of time, and then rapidly cooling it, the steel is transformed into a martensitic structure, and the steel is hardened.
With the in-depth research of scholars, they gradually discovered that not only the temperature field and the stress field can induce the shape memory effect, but the magnetic field can also induce the martensitic transformation, which results in the shape memory effect.
It has been found that there are many types of alloys with shape memory effect, which can be divided into three categories: nickel-titanium alloys, copper alloys, and iron alloys. At present, the only practical shape memory alloys are Ni-Ti-based alloys and Cu-based alloys.
So far, people have found more than 50 alloys with shape memory effect, including: Au-Cd, Ag-Cd, Cu-Zn, Cu-Zn-Al, Cu-Zn-Sn, Cu-Zn-Si, Cu- Sn, Cu-Zn-Ga, In-Ti, Au-Cu-Zn, NiAl, Fe-Pt, Ti-Ni, Ti-Ni-Pd, Ti-Nb, U-Nb, Fe-Mn-Si, etc.
Disadvantages and design considerations
When developing a design or component using SMA as a raw material, people need to consider some factors and risks. The main disadvantage of SMA is the risk of fatigue failure. The number of times a certain SMA material can roughly return to its original shape after bending and deformation is limited (too many times, it may break).
From a manufacturing point of view, the production cost of SMA may be high, which limits the use of SMA by manufacturers and consumers. Not only that, because most of these materials rely on temperature to produce deformation, there are certain risks in using SMA in equipment operating under uncontrollable or unstable temperature conditions.
The upstream and downstream industries of shape memory alloys mainly include biomedical, aerospace, mechanical and electronic, bridge construction, automobile manufacturing and other industries. The market demand for products in the shape memory alloy industry is closely related to the demand for products in the downstream industry, and will grow with the development of the downstream industry market. Synchronous development.
At this stage, there are many enterprises and units engaged in the application research or production of shape memory alloys in my country. In the early stage of the industry's development, the research on shape memory alloys by universities and various research institutes has played a huge role in promoting the development of the industry. In recent years, some domestic shape memory alloy manufacturers have risen rapidly and have played an important role in the technological progress of the industry. At this stage, they have become the most important driving force for the development of my country's shape memory alloy industry.
Advanced research results of foreign shape memory alloys
1. Aerospace
Super elastic tire
The NASA Glenn SMA team developed a non-pneumatic tire. This super-elastic tire was originally developed for future missions to the moon and Mars, but it is a viable alternative to pneumatic tires on Earth today. This technology is inspired by the Apollo Lunar Tire, which uses a high-strain shape memory alloy as a load-bearing component instead of a typical elastic material, which results in the tire being able to withstand excessive deformation without permanent damage.
This innovative tire from the NASA Glenn SMA team uses shape memory alloys (mainly NiTi and its derivatives) as load-bearing components. These shape memory alloys can withstand significant reversible strains (up to 10%), allowing tires to withstand greater deformations than other non-pneumatic tires before undergoing permanent deformation.
Deformed wing
Engineers at NASA's Glenn Research Center use shape memory alloys to make deformed wings. Parts made of shape memory alloys are usually 10% to 20% of the size and weight of traditional parts. Aircraft manufacturers, researchers, and government agencies such as NASA can use these metals to do more work than just reduce fuel. cost.
Boeing engineers invented a system to reduce the noise of turbine engines. It is called the "V" of variable geometry. When heated, the shape memory alloy will bend, and the tips of these V will be immersed in the exhaust gas flow, adding proper turbulence to the hot air to reduce noise. The more the shape memory alloy is heated, the more it bends, so when under different air conditions, more angles can be set in the V.
Foldable wings
Engineers at NASA Glenn Research Center, NASA Armstrong Flight Research Center, and Boeing successfully used shape memory alloy (SMA) to move the full-size wing section of the F/A-18 Hornet.
This successful test is a milestone for the Spanwise adaptive wing project, which is studying the flight bending or forming part of an aircraft wing. The ability to form wings can improve aircraft performance by reducing weight and drag, while improving aircraft control.
NASA will continue to test the SMA actuators on the F/A-18 wings in the future, with the goal of increasing the torque capacity to 2260N and applying them to the leading and trailing edges of the wings. This research is part of NASA's Spanwise Adaptive Wing Project, which is studying how on-board adaptive wings can improve aircraft efficiency and control capabilities.
2. Machinery Industry
No refrigerant refrigeration system
A German research team has developed a prototype of an advanced heating/cooling system that can heat and cool air by compressing and unloading nickel-titanium "muscle lines". The efficiency is twice that of a heat pump or that of an air conditioner. three times. The device does not use refrigerant gas, which means it is a more environmentally friendly way of heating or cooling spaces.
The device is based on the special properties of certain shape memory metal alloys. In some cases, especially nickel-titanium alloys, these metals absorb a lot of heat when they are bent and deformed, and then release heat when they are allowed to return to their normal shape, load line The difference between the release line and the release line can be as high as 20°C.
Micro robot power
Professor Duncan Hand from Heriot-Watt University in the United Kingdom is developing a new type of alloy for use in more complex and controllable micro-robots. In order to produce this advanced material, researchers are developing a new technology called functionally graded laser-induced forward transfer (FG-LIFT).
Flexible robot finger
This technology uses a pulsed laser to deposit metal thin films such as nickel, titanium or copper laminated on a transparent polymer on a substrate. Therefore, this technology can print various metal films layer by layer on the [receiver] substrate like an old typewriter ribbon, so there may be three layers of titanium, four layers of nickel and one layer of copper. In this way, the process can build three-dimensional elements, which the team describes as voxels, composed of different metal layers. The material can then be heat treated to carefully control the diffusion process between the metal layers in each voxel, allowing researchers to precisely control the composition of the material.
Jellyfish robot
Bionic jellyfish robot driven by SMA
A team from the Indian Mechatronics Instrument Laboratory IITIndore has developed a soft robotic jellyfish based on shape memory alloy polymers for noise-free marine biological monitoring using smart and soft materials. Soft robotics technology is an emerging multi-meter power in the field of robotics. SMA can be used as a suitable choice for flexible actuator technology to imitate the posture of living organisms. It is a smart material that can recover from induced deformation and restore its memory shape when heated.
The team has tested the developed robot in a laboratory environment and achieved a movement of 1cm/s. The device uses a mechanism based on SMA springs to simulate the flutter of the rear fin of the fish's tail, thereby generating a propulsive force that pushes the robot fish. The advantage of developing such soft robots is that they allow noise-free drive and simple and flexible design, which consumes less manufacturing time. The continuous heating and cooling of the polymer structure based on the SMA wire is responsible for the expansion and contraction of the antennae of its body, which generates thrust to move the jellyfish robot in the water.
Shape memory alloy bearings
NASA's tribology and rotating machinery expert Christopher DellaCorte is trying to use nickel-titanium alloy to make spherical bearings, because traditional ball bearings are prone to rust and dent in extreme environments, especially during aerospace flights. However, Nitinol is different from traditional bearing steel. Nitinol is a combination of nickel and titanium, usually combined with other metals. The most common alloy is Nitinol 55, a well-known shape memory alloy (SMA). SMA is a highly elastic material that can be twisted and bent, but it can still return to its original shape.
3. Daily life
The main applications of shape memory alloys in daily life are: temperature adjustment devices, overheat protection devices, air-conditioning wind direction adjustment mechanisms, memory glasses frames, shape memory street lights, mobile phone antennas, and fire inspection valves.
As a new type of material that emerged with the continuous development of science and technology, memory alloy has super intelligence and high superiority. It has the excellent advantage of being able to produce various reliable components with superior performance, high automation, and wear resistance and deformability. The continuous rise of the level of science and technology has caused the demand for smart materials in all walks of life to also continue to increase, and shape memory alloys have broad development prospects.
In addition, the shape memory alloy industry is in line with the national strategic emerging industry plan and the central and local supporting support policies to determine the seven emerging industries, which are industries supported and encouraged by the state. In the future, with the development of shape memory alloy technology and the decrease in cost, the promotion of industrial policies and the continuous improvement of consumer acceptance. In the future, with the improvement of people's living standards and consumption power, shape memory alloys will gradually enter the daily commercialization. In addition to products such as automobiles, robots, household appliances, and medical devices, some small items in people's lives will also Popularizing the use of shape memory alloys will also drive the market scale of shape memory alloys to further expand.
Link to this article:Why does shape memory alloy have memory?
Reprint Statement: If there are no special instructions, all articles on this site are original. Please indicate the source for reprinting:https://www.cncmachiningptj.com
PTJ® provides a full range of Custom Precision cnc machining china services.ISO 9001:2015 &AS-9100 certified.
Machining shop specializing in fabrication services for construction and transportation industries. Capabilities include plasma and oxy-fuel cutting, Tailored machining, MIG and Custom Aluminum Cnc Precision Milling Welding Jig Fixture, roll forming, assembly, Lathe machining stainless steel cnc machine shaft, shearing, and CNC Swiss Machining services. Materials handled include carbon and Passivation Stainless Steel Machining Cover Plate Parts.
Tell us a little about your project’s budget and expected delivery time. We will strategize with you to provide the most cost-effective services to help you reach your target,You are welcome to contact us directly ( sales@pintejin.com ) .
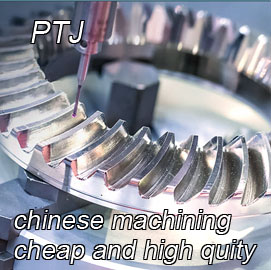
- 5 Axis Machining
- Cnc Milling
- Cnc Turning
- Machining Industries
- Machining Process
- Surface Treatment
- Metal Machining
- Plastic Machining
- Powder Metallurgy Mold
- Die Casting
- Parts Gallery
- Auto Metal Parts
- Machinery Parts
- LED Heatsink
- Building Parts
- Mobile Parts
- Medical Parts
- Electronic Parts
- Tailored Machining
- Bicycle Parts
- Aluminum Machining
- Titanium Machining
- Stainless Steel Machining
- Copper Machining
- Brass Machining
- Super Alloy Machining
- Peek Machining
- UHMW Machining
- Unilate Machining
- PA6 Machining
- PPS Machining
- Teflon Machining
- Inconel Machining
- Tool Steel Machining
- More Material