Use memory alloy as a driver to achieve precise positioning of extremely small displacements
Many shape memory alloy (SMA) linear actuator designs have been proposed to use different technologies for precise position control, such as displacement feedback, temperature feedback, force feedback, and resistance feedback. Each technology has its own advantages, as well as limitations and limitations.
The self-sensing SMA drive is considered cost-effective because it does not require the use of external sensors in the system. However, its performance relative to other methods has not been widely discussed.
Research background and experiment
The possibilities of using shape memory alloys as actuators are endless. Application areas include aerospace, robotics, medical, electronics and construction. SMA is considered attractive due to its high strength-to-weight ratio and simplicity, thus making the system more effective and reliable. It can be applied by using passive or active control.
SMA has great potential in applications that require precise position control, such as pistons or valves, manipulators, antenna pointing, and smart aviation structures. In order to adapt to these applications, different techniques have been proposed to produce precise displacements. SMA is also suitable as a driver for reconfigurable parabolic antenna structures because it can generate large deflection. In another study, by measuring the strain on the surface of the structure, and using an improved proportional integral derivative (PID) controller with an anti-compensator to control, force control to produce the crown change. Shape memory alloys are also widely used in robotics research.
A mechanism used in robotics applications uses SMA springs and uses a fuzzy controller to control position and force. In this system, a closed-loop fuzzy logic controller is used to control the force exerted by the actuator and the position of the additional load. Another example is the use of SMA and encoders for highly precise position control of the fingertips of micro-robots, and the use of strain gauges to measure stiffness and force control. SMA is also used in a five-finger prosthetic hand with a tendon-driven drive mechanism to produce the required dexterity while keeping the mechanical and control complexity of the device low. The integrated tactile sensor at the fingertips improves the overall control ability of the hand, and adopts a new type of resistance feedback position control scheme.
In automotive applications, a cost-effective mirror driver was designed and manufactured by combining shape memory alloy wires and control algorithms to provide stable and accurate positioning of the outside rearview mirrors. SMA is also considered in the steering column clamping system, where a shape memory element controls the opening and closing functions of the steering sleeve.
Shape memory alloy wire can generate driving force when temperature changes. This can be achieved by conventional heating and Joule heating. Shape memory alloys also undergo phase transformation under load or temperature changes. The shape memory alloy transforms into a twinned martensite phase when loaded, and transforms into austenite when heated. If the shape memory alloy is cooled, it will return to the twin martensite phase. Many researchers have developed dynamic models of shape memory alloys.
Although it is more effective to directly control the position of the system, in the case of SMA, it is also possible to use its resistivity to control its drive without using an external sensor, thus making the system less complicated.
There are many factors that affect the change of resistivity, but in addition to stress and temperature, real-time control methods are challenging to measure other factors, and it is difficult to apply feedback control technology. In addition, changes in resistivity may be directly or indirectly affected by stress and/or temperature. Due to the possibility and complexity of using resistance feedback in SMA drives, many studies have focused on modeling resistance characteristics to better understand this behavior.
In order to meet the requirements of precise position control within 2mm, a 0.012" type magnetic flux wire with a length of 10 cm was selected. In the experiment, a 70°C bend of 0.012 and a B length of 100 mm ± 1 mm were selected. The 13897 loop end is crimped. The length of this SMA wire will produce about 3% of the stroke, which means a displacement of 2-4 mm. The experimental results related to the precise position control of the SMA have been developed, including the force/position and/or temperature Or internal resistance/position calibration, and a control feedback system for precise position control.
Using a custom test bench developed for this research, the performance of an accurate position feedback system that achieves a 2mm displacement was tested. In order to accurately control the position of the shape memory alloy actuator, a displacement sensor can be used to directly measure the position and use it as an input to the feedback system.
The displacement feedback system has good time response performance and accuracy, and the steady-state error is 1% under all conditions. The accuracy of the self-sensing system is low, and the steady-state error of the step response is 15%. Experiments have found that compared with the self-sensing system, the displacement feedback system has a higher initial power and a longer rise time. The average temperature of the displacement feedback system is lower than the temperature of the self-sensing system, which results in the stroke difference of the SMA system with a lower stroke of the displacement feedback system.
Analysis conclusion
Using shape memory alloy as a driver, an experimental platform for precise positioning of extremely small displacements in the range of 2 mm has been developed. Various feedback systems can be developed to use shape memory alloy actuators for position control, such as shape memory alloy actuators for displacement, resistance, force or temperature. In the research work of this research, the displacement feedback control system and the self-sensing feedback control system were designed, and their performances were compared. It is expected that the displacement feedback system will produce better accuracy, but self-sensing feedback control may reduce the cost of the system because it does not use sensors.
Therefore, this research aims to study the accuracy of the self-sensing system compared with the displacement feedback system. Use the laser displacement sensor to measure the position and provide input to the displacement feedback system. For self-sensing systems, the voltage drop across the SMA is used as the input measurement of the system. The displacement feedback system has good transient response performance and accuracy, and the steady-state error is 1% under all working conditions. The accuracy of self-sensing feedback is poor, and the response time is slow. However, by preloading the SMA driver, the accuracy of the self-sensing system is improved. When the preload is increased from 500 g to 700 g, the steady-state error is reduced from 15 g to 11%. On the test bench, the performance of the displacement feedback system for the position control of the 2 mm shape memory alloy is better than that of the self-sensing system. However, the feedback system of the self-sensing system can be improved, and the wires that provide tension are proven in experimental studies.
The research results prove the feasibility of replacing the displacement feedback system with a more cost-effective self-sensing actuation system. In the experimental setup of precise position control proposed in this research, the use of laser displacement sensors can be omitted. This technology requires fewer components, thereby reducing the initial cost of the system and the cost of the entire system in the long run. Sensing systems can be considered more cost-effective compared to other drive systems, requiring external position measurement devices, such as linear variable differential transformers (linear), infrared sensors, laser sensors and strain gauges and their related cost procurement and maintenance , Energy consumption and measurement systems for electronic products and software development.
Link to this article: Use memory alloy as a driver to achieve precise positioning of extremely small displacements
Reprint Statement: If there are no special instructions, all articles on this site are original. Please indicate the source for reprinting:https://www.cncmachiningptj.com/,thanks!
PTJ® provides a full range of Custom Precision cnc machining china services.ISO 9001:2015 &AS-9100 certified. Large scale machining Manufacturer of medical bags, providing 3D design, prototype and global delivery services. Also offering hard cases, semi-hard EVA, soft-sewn cases, pouches and more for OEMs. All cases are made custom according to specifications with infinite combinations of materials, molds, pockets, loops, zippers, handles, logos and accessories. Shockproof, water-resistant and eco-friendly options. Medical parts, emergency response, Electronic parts, corporate, education, military, security, sports, outdoors and construction industries. Services include case concept consultation, 3D design, prototyping,rototyping,CNC Drilling Services and manufacturing.Tell us a little about your project’s budget and expected delivery time. We will strategize with you to provide the most cost-effective services to help you reach your target,You are welcome to contact us directly ( sales@pintejin.com ) .
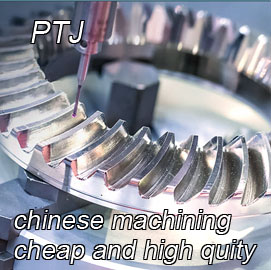
- 5 Axis Machining
- Cnc Milling
- Cnc Turning
- Machining Industries
- Machining Process
- Surface Treatment
- Metal Machining
- Plastic Machining
- Powder Metallurgy Mold
- Die Casting
- Parts Gallery
- Auto Metal Parts
- Machinery Parts
- LED Heatsink
- Building Parts
- Mobile Parts
- Medical Parts
- Electronic Parts
- Tailored Machining
- Bicycle Parts
- Aluminum Machining
- Titanium Machining
- Stainless Steel Machining
- Copper Machining
- Brass Machining
- Super Alloy Machining
- Peek Machining
- UHMW Machining
- Unilate Machining
- PA6 Machining
- PPS Machining
- Teflon Machining
- Inconel Machining
- Tool Steel Machining
- More Material