Adjusting additives in composite materials can improve 3D printed part properties
From Kevlar fiber to artificial wood flooring, there are composite materials everywhere. They are strong, dimensionally stable, wear-resistant and corrosion-resistant.
Although aircraft fuselages are usually made of alternating layers of composite cloth and epoxy, most are made of thermoplastics reinforced with carbon fiber, glass filler, or metal powder. The final structure is very strong and lightweight.
However, manufacturing these structures is challenging. The manual process is time consuming and requires a lot of skills. Therefore, automated methods are more efficient, but require a large investment in complex and difficult-to-scalable machinery.
For smaller parts, 3D printing has proven to be a viable option, but technical barriers have prevented its widespread adoption. One of the problems is that the functional additives (particles and reinforcing fibers) agglomerate and settle during the construction process. In addition, it is almost impossible to achieve fiber alignment on traditional 3D printers.
Stop precipitation
Fortify developed the Flux One 3D printer, which solves the problems associated with printing composite parts. The Boston-based startup calls its process "Digital Composite Manufacturing (DCM)."
Ben Arnold, vice president of business development at Fortify, said that the most important of these technologies is continuous kinetic mixing (CKM). By blending the photosensitive polymer resin of the system with functional additives, continuously circulating and in some cases heating the resulting mixture throughout the printing process, agglomeration and precipitation can be prevented.
These additives include metal flakes, carbon fibers or ceramic fibers, and flame retardants. Each additive has ideal characteristics. Without CKM, these characteristics would be difficult to use. More importantly, these characteristics are consistent throughout the construction process. A property proposed by Fortify CEO and co-founder Josh Martin is missing in many 3D printer designs.
He said: "Using a traditional 3D printer, precipitation may occur within a few minutes, so the physical properties of the bottom will be different compared to the bottom." The solution is usually to use the smallest possible additive particles, but this It often limits the functional characteristics of printed parts. CKM eliminates all of this, opening the door to the use of heavier additives and higher concentrations of additives, while achieving consistent material properties. "
Arnold added that Fortify has also taken steps to promote the adhesion of additives to the base resin. "We do this by chemically treating additives to make them bond well with the resin and make them magnetically responsive under appropriate conditions."
Freeze in time
Magnetic induction is the second part of the DCM problem. Where CKM ensures consistent fiber distribution throughout the build process, Fortify's Fluxprint technology provides selective alignment of these fibers so that they can be interlocked between layers and wound around the load-bearing geometry.
Fluxprint achieves this by introducing a magnetic field throughout the build area, essentially keeping the fibers "in a state of concern" long enough for UV light to "freeze" them and the surrounding resin. This process is repeated in successive layers to finally produce parts with enhanced strength, thermal properties or electrical conductivity in areas where such properties are required.
Martin said: "This selective comparison has some exciting uses." "Consider using 3D printed inserts for plastic injection molds. You can align the fibers to prevent thin parts from breaking, and if you want to print the entire mold, you can Strengthen the part around the runner to improve wear resistance.
Martin said: "On the other hand, you can use Fluxprint to program detachable supports, which are much easier than those built using traditional 3D printing technology."
Move
Since its establishment in 2016, Fortify has deployed multiple test systems. It plans to deploy about a dozen by the end of this year. So far, its applications include plastic injection molds and inserts, electrostatic assembly fixtures, medical equipment components, and proprietary technologies. Due to confidentiality agreements, Martin cannot freely discuss these proprietary technologies.
He said: “Since we have voxel-level control throughout the construction process and have a wide range of materials with enhanced electrical and mechanical properties, we expect our technology to be widely used in many industries.” “For example, If you want a certain area to have higher thermal conductivity, you only need to change the direction of the fiber. We have also seen great interest from companies in the RF (radio frequency) and microwave fields, and these companies expect to use our technology to obtain The required characteristics, rather than the traditional method of assembling parts with many different materials."
However, there is a catch: aligning each voxel is very time-consuming. Having this level of control is a kind of "blessing and curse." "One of the best ways to use it is to use finite element analysis and similar engineering tools to identify the stress locations in the CAD model and reinforce only those areas." Then, the user can fill in the margin of the workpiece with simple cross-hatch lines.
Arnold said that by using this method, CKM "can ensure that the material properties of the entire part are consistent, and Fluxprint provides an optimized microstructure where it is most needed."
Link to this article: Adjusting additives in composite materials can improve 3D printed part properties
Reprint Statement: If there are no special instructions, all articles on this site are original. Please indicate the source for reprinting:https://www.cncmachiningptj.com/,thanks!
Sheet metal, beryllium, carbon steel, magnesium, 3D printing, precision CNC machining services for heavy equipment, construction, agriculture and hydraulic industries. Suitable for plastics and rare alloys machining. It can turn parts up to 15.7 inches in diameter. Processes include swiss machining,broaching, turning, milling, boring and threading. It also provides metal polishing, painting, surface grinding and shaft straightening services. The production range is up to 50,000 pieces. Suitable for screw, coupling, bearing, pump, gearbox housing, drum dryer and rotary feed valve applications.PTJ will strategize with you to provide the most cost-effective services to help you reach your target,Welcome to Contact us ( sales@pintejin.com ) directly for your new project.
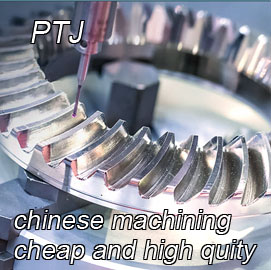
- 5 Axis Machining
- Cnc Milling
- Cnc Turning
- Machining Industries
- Machining Process
- Surface Treatment
- Metal Machining
- Plastic Machining
- Powder Metallurgy Mold
- Die Casting
- Parts Gallery
- Auto Metal Parts
- Machinery Parts
- LED Heatsink
- Building Parts
- Mobile Parts
- Medical Parts
- Electronic Parts
- Tailored Machining
- Bicycle Parts
- Aluminum Machining
- Titanium Machining
- Stainless Steel Machining
- Copper Machining
- Brass Machining
- Super Alloy Machining
- Peek Machining
- UHMW Machining
- Unilate Machining
- PA6 Machining
- PPS Machining
- Teflon Machining
- Inconel Machining
- Tool Steel Machining
- More Material