Metal manufacturers must make these preparations to reduce the risk factor of sheet metal edges
To determine the sharpness of sheet metal edges, metal manufacturers must be prepared in the design stage. Whether in sharp products or non-sharp products, there are very few modern standards to define clarity. Manufacturers usually use several standards or proprietary standards, but it is difficult to find a balanced, cost-effective way to deal with clarity.
If you do not want clarity for safety reasons, you should follow the safety product rating system defined in ISO 12100.2010:
1. Design hazards.
2. If this is not possible, please prevent them.
3. If it is not possible, please warn them.
Usually, the manufacturer will easily abandon the first two and issue a warning. These can be placed in the manual or on the product label, and can transfer the risk to the consumer. If you get hurt, as a manufacturer, you may blame consumers for not paying attention to warnings and misusing the product. Although this may be correct, if a subsequent product liability lawsuit occurs, it needs to be able to prove to the jury.
If your design process mainly follows ISO 12100.2010, and you try to follow a hierarchy, but can't find a reasonable way to implement the first two methods, you can best prove this. Ensure that reasonable, objective and recordable safety reviews are included as part of the design documentation.
Metal manufacturers need to learn how to remove burrs to ensure the safety of sheet metal edges
If you can rely on consumers to read product manuals and safety warnings, this should be the last defense. Usually, depending on the product, consumers begin to expect ordinary products to have inherent safety.
Standards and test methods
There are few publication standards that define clarity. Some of them are intended to be used in products that should be sharp, and some are written to prevent products from becoming sharp.
In the latter case, UL Standard 1439 attempts to address the sharp edges on the product. It was released in the early 1970s. Since then, other organizations have issued other similar standards.
UL 1439 aims to provide a standardized method for testing clarity, and adds: "The edges of the housing opening, frame, guards, knobs, handles, etc. should be smooth and rounded to avoid cuts during cutting. In normal Contact us during use or user maintenance.” It requires pressing and sliding the product edge on a special layer of tape under a controlled contact force of 1.5 pounds. If the layers can be cut by the edges, they are considered sharp. The Sharp Edge Tester device was developed to fix the tape and control the contact force, and its version is still being sold today.
Manufacturers of knives and razors test clarity through other tests, many of which are subjective. The frequently cited standard is BS EN ISO 8442.5:2005, which is similar to the NIJ Standard-0115.00 of the National Academy of Justice. These standards can be used to test the sharpness of objects that should be sharp. The available test equipment uses silicone rubber and cards as the test medium, and measures the contact force and penetration standards at the same time.
Some razor blade manufacturers use optical equipment (such as laser interferometers) to measure the sharpness of their blade edges. In addition to these controlled methods, other low-tech methods are often used, including cutting into man-made materials and looking for reflected light on the cutting edge. Of course, these have dubious uses in identifying harm to consumers.
Another related standard of the National Academy of Justice is NIJ Standard-0101.05, which is used to test the effectiveness of body armor on the penetration of sharp objects. The standard only covers the effects of stab wounds and mentions the need for "simulated pulp" materials (such as clay), but the standard does not specify how to determine or specify the required material properties.
Since the cutting process involves bringing the material to its failure stress level, you must consider how to control the stress in the material before using the test blade. Compared to materials without a razor, a material that is taut before applying the razor to its surface will be more prone to failure. On looser materials, the blade must generate all stresses, so it must be applied with a greater contact force.
Even under the same force, a sharp edge used on a smaller contact area will produce higher stress than a larger contact area.
Certain tests are performed just to determine relative clarity, such as testing two edges to see which edge is clearer. For this type of test, low-cost materials such as polymers, rubber sheets, clay, foam, suede cloth and felt can be used.
Stress and cutting process
When materials (including skin) are in contact with objects that exceed a certain stress, they will fail.
Stress is a measure of when force is applied to an area. Stress is the key to clarity, because if the force is spread over a large enough area, even a large force will produce a small stress, and vice versa. Depending on the contact area, you can withstand the same force but different stresses.
The difference between strength and pressure can be seen in the use of snowshoes. When someone walks on the snow, their weight (strength) presses on the snow, creating pressure. The larger the snow shoes, the lower the pressure, and the less likely it is to snow.
This has the same effect as making a knife sharp. In Figure 1, the force applied to the two objects is distributed over one area, which reduces the contact stress on the surface.
The finished product can have a variety of sharp edges. Small changes in the edges (for example, chamfering into square corners) can reduce the contact area, thereby reducing sharpness.
Mechanical cutting methods (slicing, sawing, shredding, shearing, abrasive cutting) usually use hard and sharp objects to generate some combination of axial stress and shear stress to produce cutting action.
Figure 2 shows several theoretical sharp edges that can be seen on the finished product. In these, small changes in the edges (for example, chamfering square corners) can reduce the contact area, thereby reducing clarity. But there is also a risk of non-intuitive sharpness, such as the edges of cut metal plates. They may pose a greater danger than cutting blades, because this danger is hidden.
The difficulty of determining whether the edges of a product are safe is not an excuse for making unsafe products. Although difficulties should not be underestimated, the consequences of avoiding problems should not be underestimated. When manufacturers underestimate the edge of danger, serious injuries can result.
PPE test
In view of the lack of appropriate standards for testing product clarity under strong conditions, engineers may consider adopting novel methods to test product edge safety. These tests can also be used to determine the effectiveness of personal protective equipment (PPE).
Hand protection is outlined in the U.S. Department of Labor’s OSHA regulations 1910.132 and 1910.138. The latter requires employers to choose and require employees to use "appropriate" hand protection when their hands are harmed to protect them from cuts and cuts, stabs and abrasions. In addition, 1910.132(b) stipulates that even if employees bring their own personal protective equipment, employers are responsible for the suitability, maintenance and hygiene of their equipment.
The most popular standard for testing and evaluating the effectiveness of work gloves in preventing scratches is ANSI / ISEA 105-2016, which is a voluntary standard. It is based on testing a sharp blade across the glove material under a controlled force to create a pass/fail criterion for work gloves. The blade must be changed between each test to ensure consistent clarity and results. If the glove is not cut, it can be rated according to the weight applied.
Suppliers of safety gloves shall test and evaluate products in accordance with their standards. These contents should be checked carefully, because the ASTM test for this standard is for sharp edges, and there is also an ASTM standard for abrasion resistance.
Safe design
Products that appear harmless may cause minor injuries. Usually, these situations can be avoided by a simple deburring operation. Obviously, the manufacturer does not intend to cause these injuries, and of course the manufacturer cannot foresee the extreme abuse of its products.
The solution is part of the design phase and is a comprehensive object safety inspection process. Although you cannot predict all future conditions, you can develop a process to try to do so and minimize the consumer’s responsibility to prevent harm.
In one case, the manufacturer worked hard to ensure product safety, but left a sharp edge exposed during the assembly process. The manufacturer recommends not to use sharp edges, but instead recommends that consumers use safety gloves. The problem is that the product cannot be assembled with safety gloves. This fact has been confirmed by an engineer in the deposition. The manufacturer knows that it is risky not to deburr sharp edges. This caused the assembly technician’s right hand to be cut through the tendons of his palm by the sharp sheet metal edges. The jagged edges shattered the ends of the tendons and prevented them. To reconnect.
The cut sheet metal edges have several properties that make them clear. The edges may look flat, but the cutting die will leave burrs.
Many products use cut sheet metal, but only one standard, UL 1439, directly solves the problem of sheet metal clarity. There are other sharpness standards that define when products that should be sharp are sharp enough, or to rate products designed to protect users from sharp products.
Obviously, it is difficult to design a single standard to protect consumers from a variety of sharp products. But this does not make the manufacturer out of the predicament. In the absence of relevant standards, they must solve product safety issues on a case-by-case basis based on existing and inferred knowledge of products and industries.
Sheet metal manufacturers understand the dangers of trimming and have widely promoted special precautions in the industry. However, many industry preventive measures are anecdotal. For example, the "Sharpness Test" recommended by a manufacturer's organization requires a "toothpick or other object" to be run on the edge without specifying the contact force. This makes this test non-repeatable and subjective.
According to the publication of the British government agency "Health and Safety Executive" (Health and Safety Executive) "Prevent injuries caused by manual handling of sharp edges in the engineering industry" (www.hse.gov.uk/pubns/eis16.pdf), This is the best way to prevent disease and injury caused by sharp edges is to be designed to remove or cover the sharp edges. According to the paper, “wearing gloves should be the last choice.” The metal industry organization’s website also acknowledges the dangers of sheet metal and provides testing recommendations.
As shown in Figure 3, the cut edge of a metal plate has several properties that make it sharp. The edges may look flat, but the cutting die will leave burrs. Although they may not be as sharp, they pose a major threat, especially when the mold is worn or set up incorrectly.
The product in the photo is made of 0.016 inch thick sheared metal sheet and has been released to the public. The manufacturer believes that the edge is not dangerous because it is protected during normal use. However, the edges are not protected during the assembly process (that is, when injury occurs). In this case, consumers permanently lose the ability to use multiple fingers.
In this case, the manufacturer has taken some measures to prevent the metal plate from being injured, but it is not certain whether it needs to be used on a specific edge. Although the sheet metal is so thin that most standard deburring methods are not suitable for use, the manufacturer could have made the product safe in other ways-the method used on other parts of the same product. However, the manufacturer ignores the sharp edge because "it is only exposed during the assembly process."
The product design process should include a safety review covering all possible product usage to identify and quantify risks and design standards. Engineers should drive this process while relying on continuous feedback from sales, customers, and manufacturing. This is the best way to determine what design changes (including product safety) need to be made.
What is the price?
Sometimes, as a manufacturer, you face a trade-off between safety and cost. You need to define the risks and then decide how to address them.
The cost of product safety seems to conflict with profit. However, the cost of part deburring may be less than the cost of resolving injury claims or litigation.
Link to this article: Metal manufacturers must make these preparations to reduce the risk factor of sheet metal edges
Reprint Statement: If there are no special instructions, all articles on this site are original. Please indicate the source for reprinting:https://www.cncmachiningptj.com/,thanks!
Sheet metal, beryllium, carbon steel, magnesium, 3D printing, precision CNC machining services for heavy equipment, construction, agriculture and hydraulic industries. Suitable for plastics and rare alloys machining. It can turn parts up to 15.7 inches in diameter. Processes include swiss machining,broaching, turning, milling, boring and threading. It also provides metal polishing, painting, surface grinding and shaft straightening services. The production range is up to 50,000 pieces. Suitable for screw, coupling, bearing, pump, gearbox housing, drum dryer and rotary feed valve applications.PTJ will strategize with you to provide the most cost-effective services to help you reach your target,Welcome to Contact us ( sales@pintejin.com ) directly for your new project.
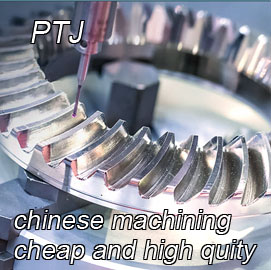
- 5 Axis Machining
- Cnc Milling
- Cnc Turning
- Machining Industries
- Machining Process
- Surface Treatment
- Metal Machining
- Plastic Machining
- Powder Metallurgy Mold
- Die Casting
- Parts Gallery
- Auto Metal Parts
- Machinery Parts
- LED Heatsink
- Building Parts
- Mobile Parts
- Medical Parts
- Electronic Parts
- Tailored Machining
- Bicycle Parts
- Aluminum Machining
- Titanium Machining
- Stainless Steel Machining
- Copper Machining
- Brass Machining
- Super Alloy Machining
- Peek Machining
- UHMW Machining
- Unilate Machining
- PA6 Machining
- PPS Machining
- Teflon Machining
- Inconel Machining
- Tool Steel Machining
- More Material