What should I do if a weld line appears during injection molding?
Welded wire or braided wire is probably the most common and difficult to eliminate injection defect. They occur when the melt flow front collides in the cavity. Poor braid will not only cause appearance defects, but also greatly weaken the structural integrity of the part. The strength of the braided wire may be only 20% of the nominal strength of the part, or it may be 100% of the nominal strength of the part, depending on many variables.
The origin of the weak welding line is material selection, part design, tooling and processing. For welding wires, certain materials are more or less "forgiving." Part design is very important, because uneven wall thickness will change the shear force and flow rate at the melt front, causing the flow path to split. Processing effects include multiple gates entering the cavity and protrusions (such as bosses and ribs) and holes or depressions in the mold, all of which interrupt the melt flow and divide the melt flow into independent fronts. Temperature changes in one area of the mold surface may also produce uneven flow fronts.
Entangled Chain
Material properties affect the weaving of the melt front. When the polymer chain is only partially entangled on the weld line, weakening can result. Amorphous resins generally have better weld line strength than semi-crystalline resins, and resins with higher flow rates can achieve better stacking, thereby forming a stronger weld line. The addition of glass fiber will also reduce the strength of the weld line.
Sometimes, the volatiles emitted from the resin during processing will reduce the strength of the weld line. Unless vented properly, the gas will separate the front of the gas stream.
Part and tool design
In general, the way the plastic flows when it enters the mold cavity is the most important for the strength of the welding line. Minimizing flow interruptions and placing them carefully so that the flow fronts can meet and flow a distance to merge correctly is the key to optimizing part performance.
The first rule is to place the gate so that the weld is not in the area of the part that will be subjected to high stress during use. Change the gate position to move the weld to a non-stressed area. If the part has multiple gates, try blocking some gates to reduce the number of potential flow fronts (but please get permission first!). Or, try adding an overflow tab to promote air evacuation and molecular chain entanglement.
The welding line is optimized by selecting the gate location, which allows the polymer to continue to flow and fuse after reorganization at the flow front.
Another key rule of part design is a uniform nominal wall to provide a consistent flow front and prevent flow changes during filling. The type of resin and its shrinkage are of great significance here. The maximum wall thickness change for amorphous or low shrinkage resins is 25%, while the maximum nominal wall thickness change for semi-crystalline or high shrinkage resins is limited to 15%.
Optimize the performance of the welding line by selecting the gate location, which will allow the polymer to continue to flow and fuse after recombination at the flow front. It is also important to properly drain the weld and the area around it. It may be worth adding a baffle that can better weave the flow seams and can also be used as a vent for trapped air when the flow fronts merge. The flow tab must be cut off, which requires a second operation. Bosses, ribs, etc. should be in the direction of flow for easy filling and exhaust. Other ways to reduce or exhaust residual air are to use perforated steel inserts or ventilated core pins to improve ventilation. Vacuum exhaust is another method.
If you suspect that there is a hot spot in the mold, let the mold sit until the temperature is uniform. Compare the first shot with subsequent footage shots. If the flow path is different, the cause is temperature and cooling issues related to tool steel. Check the mold for hot spots and try to achieve uniform cooling. Make sure that the two mold halves are at the same temperature.
Handle pointer
Machining affects the strength and appearance of the welding line, but it cannot eliminate the root cause in the design of materials or parts or tools. The low pressure at the flow front does not promote entanglement of molecular chains, resulting in poor impact strength. The parts may not be fully packed, and if the welding line is in the last area to be filled, you may not see too much packing pressure.
The trapped air (or volatile matter) will prevent a good weaving of the confluence front. Core pins, "blind holes" and special mold features can cause air trapping. Jetting may also be the cause of uneven melt flow and weak fusion of the flow front.
It usually helps to increase the injection speed, reduce the filling time and increase the shear rate.
The cold flow frontier is not generally considered to be the culprit. The temperature of the flow front has little effect on the molecular chains that cross the boundary of the flow front and are entangled with the chains in the converging flow. Although many processors like to increase the melt temperature to improve fluidity and weld line strength, volatiles escaping from the polymer tend to reduce the weld line strength. Adhering to this strategy is a last resort.
On the contrary, it usually helps to increase the injection speed, reduce the filling time and increase the shear rate, which can reduce the viscosity of the polymer during the filling process, thereby achieving better chain entanglement and better packing. Increasing the holding pressure or holding pressure also helps, and the holding and holding time is longer. Increasing the holding pressure or holding pressure helps to eliminate the low pressure of the welding line. Another strategy to promote more chain entanglement at the weld is to increase the mold temperature by 10°C (20°F).
The molder should ensure that the weld line is formed during the first stage of the part filling process. Creating a strong weld line during packing and holding is often problematic because it is difficult to get the flow fronts together in the presence of minimal flow.
The uneven flow front caused by uneven wall thickness can be solved by gating into the thicker area and providing a flow pilot for the thinner area to provide uniform filling. Keep in mind that due to the lower melt pressure required for filling, the thicker parts of the part will be filled first. Plastic flow will accelerate in the thicker part and hesitate in the thinner part. This allows the polymer to "track" and trap air or volatiles around the perimeter or part of the part. The solution may be to increase the injection rate and round the edges or make the joints between areas of different thickness tapered. The best answer is to redesign parts with uniform thickness.
Keep in mind that the soft-hand TPE material is sensitive to shear and can show obvious flow lines even without pre-flow interruption. Although not true weld lines, these flow lines are aesthetic flaws and do indicate weaker areas of the part. These materials will show a streamline wherever the shear rate changes, and this trend tends to occur with the expansion of the stream front.
For multi-gate parts, if possible, try to use valve gates instead of hot nozzles, and sequentially control the actuation of the valve gates in a cascade manner, so that the gates are opened only after the melt flows, thus forming a single The melt front.
Link to this article: What should I do if a weld line appears during injection molding?
Reprint Statement: If there are no special instructions, all articles on this site are original. Please indicate the source for reprinting:https://www.cncmachiningptj.com/,thanks!
3, 4 and 5-axis precision CNC machining services for aluminum machining, beryllium, carbon steel, magnesium, titanium machining, Inconel, platinum, superalloy, acetal, polycarbonate, fiberglass, graphite and wood. Capable of machining parts up to 98 in. turning dia. and +/-0.001 in. straightness tolerance. Processes include milling, turning, drilling, boring, threading, tapping, forming, knurling, counterboring, countersinking, reaming and laser cutting. Secondary services such as assembly, centerless grinding, heat treating, plating and welding. Prototype and low to high volume production offered with maximum 50,000 units. Suitable for fluid power, pneumatics, hydraulics and valve applications. Serves the aerospace, aircraft, military, medical and defense industries.PTJ will strategize with you to provide the most cost-effective services to help you reach your target,Welcome to Contact us ( sales@pintejin.com ) directly for your new project.
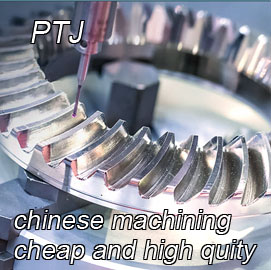
- 5 Axis Machining
- Cnc Milling
- Cnc Turning
- Machining Industries
- Machining Process
- Surface Treatment
- Metal Machining
- Plastic Machining
- Powder Metallurgy Mold
- Die Casting
- Parts Gallery
- Auto Metal Parts
- Machinery Parts
- LED Heatsink
- Building Parts
- Mobile Parts
- Medical Parts
- Electronic Parts
- Tailored Machining
- Bicycle Parts
- Aluminum Machining
- Titanium Machining
- Stainless Steel Machining
- Copper Machining
- Brass Machining
- Super Alloy Machining
- Peek Machining
- UHMW Machining
- Unilate Machining
- PA6 Machining
- PPS Machining
- Teflon Machining
- Inconel Machining
- Tool Steel Machining
- More Material