The Production Process Of Recycled Zinc From Zinc-Containing Waste
China’s zinc mines have identified resource reserves of 91,723,500 tons, and the minerals are widely distributed, but the reserves are relatively concentrated in the six provinces of Yunnan, Inner Mongolia, Gansu, Guangdong, Sichuan, Xinjiang, and Guangxi, accounting for more than 70% of the country’s zinc resource reserves; The metallogenic region and the metallogenic period are relatively concentrated, mainly in the five major mining areas of Lanping in West Yunnan, West Qinling-Qilian Mountains, Langshan-Altai Mountains in Inner Mongolia, Nanling and Sichuan-Yunnan; large and medium-sized deposits have large reserves and complex ore types; deposits The material composition is complex, the co-associated components are many, and the comprehensive utilization value is great; from these factors, there are many lean ores, few rich ores, and complex structure. From these factors, it is shown in a certain sense that zinc resources are not only rich in lean ores, but also difficult to mine in recent years. Recently, due to the closure of several important zinc mines in the world, the market supply of zinc concentrate turned to shortage. China has always been a major producer and consumer of global zinc metal. In 2017, China’s zinc production reached 6.22 million tons, and the proportion of zinc consumption in global zinc consumption increased from 15.18% in 2000 to 48% in 2017 , Nearly half, occupy an important position in global zinc consumption. According to statistics, China's refined zinc consumption in 2017 was about 6.7 million tons.
It is mainly used in five areas, such as galvanizing, die-cast zinc alloy, zinc oxide, brass, and batteries. The zinc plating accounts for 57%. However, there is still a supply gap of 200,000 tons in the refined zinc market. In 2015, there was a zinc shortage of 250,000 tons, and in 2017, there was a zinc shortage of 1.98 million tons. This is not only a serious hidden danger in the development of the zinc industry and the supply of raw materials, but also a positive for the development of the secondary zinc industry.
1. China's secondary zinc smelting process.
The production process of metal zinc smelting mainly includes wet and fire methods. The wet method is electrolytic zinc, and the fire method is blast furnace or vertical tank zinc smelting. Both of these processes have defects such as large investment, high energy consumption, large pollution, and low efficiency. The advantages of recycled zinc are mainly manifested in that per ton of recycled zinc, the energy consumption is only 28% of that of primary zinc, which saves energy by 72%, which not only reduces emissions, but also has obvious environmental protection effects.
However, the domestic secondary zinc smelting is still at a relatively backward stage, and the treatment of zinc-containing solid waste in the industry basically follows the primary zinc smelting process. It is understood that the current wet electrolytic zinc project with an annual output of 10,000 tons of metallic zinc requires an investment of more than 100 million yuan, while the pyrotechnical vertical tank or blast furnace annual output of 10,000 tons of metallic zinc only requires an investment of more than 60 million yuan, and there are high operating costs, Problems such as high energy consumption, poor efficiency, and difficulty in large-scale production.
Therefore, many zinc production companies have joined research institutes, colleges and universities to carry out research and make great efforts to research green and environmentally friendly recycled zinc production processes.
2. China's secondary zinc resources
China's secondary zinc resources include hot-dip galvanizing slag and zinc ash generated during the galvanizing process, zinc waste generated during the production of zinc alloys, and scrap zinc alloys and electric arc furnace dust in the iron and steel industry And gas mud, gas ash, and zinc-containing smoke and dust produced by smelting copper and lead industries. In 2016, the zinc content of the aforementioned resources produced in China was about 2.47 million tons. According to the "China Renewable Resources Recycling Industry Development Report 2017" released by the Ministry of Commerce, the amount of zinc scrap recycled in China in 2016 was approximately 1.5 million tons. The zinc content of cast zinc waste, zinc sheet waste and waste all-zinc chips included in the imported zinc waste and scrap is more than 96%; the zinc content of waste mixed zinc chips is about 55%.
There are also discarded zinc-containing catalysts and discarded alkaline zinc-manganese batteries. These resources have not yet been recycled into secondary zinc resources.
It is understood that most of the raw materials for the production of secondary zinc oxide come from steel mills, galvanizing plants, natural zinc oxide ore and various zinc slag, zinc ash, tailings and other industries. It is mainly composed of two categories. One is the manufacturer of zinc ingots: because the amount of zinc used in galvanizing accounts for 59% of the total zinc consumption, there are more zinc slag and zinc ash during the galvanizing process, and the zinc content is higher. , Easy to recycle; in addition, there are leftovers from copper mills, slag from die-casting zinc alloys, and smoke and dust from the smelting process of lead and copper. The second is all kinds of zinc-containing smoke and dust in steel-making plants, mainly from blast furnace ash, converter ash, electric furnace ash, and zinc alloy scrap, printed zinc plate, offset printed zinc plate, waste rolling Roof panels, auto parts, etc. The zinc grade of the material is about 5%-35%, which has high utilization value.
We know that many steel plants have galvanizing production lines. If a zinc-containing fume collection device is built in the plant, the zinc ingot can be used again for the galvanizing production line; the zinc slag and zinc ash from the galvanizing production line can be returned to the zinc smelting device Heavy production of zinc ingots. At the same time, the high-speed iron slag from zinc smelting will be returned to the iron smelting system to continue iron smelting, realizing recycling.
The iron and steel industry is a major producer of secondary zinc resources, including zinc-containing fumes from electric furnace smelting scrap and gas mud and gas ash from blast furnace ironmaking. Solid waste includes blast furnace gas mud, electric arc furnace dust, etc. Blast furnace gas mud and gas ash, also known as soot or flue ash, are the raw material dust carried by the blast furnace gas during the blast furnace smelting process and the particles produced by the intense reaction in the high temperature zone. The products obtained by wet or dry dust removal have similar chemical properties. The main components are iron oxide and carbon, and also contain a small amount of valuable non-ferrous metals such as zinc, lead, copper and bismuth.
At present, according to the investigation of leading domestic steel smelting enterprises, these bulk ash and other wastes used to be bundled together with other wastes for bidding and takeaway. Now, due to the reform of the bidding system, steelmaking bulk materials are in an embarrassing situation where no one wants them, and bulk materials cannot be handled. They can only be piled up on site or discarded at will, causing environmental pollution. At the same time, on the one hand, workers often get burned on their skin during the process of collecting and transporting lime. On the other hand, workers clean the ash once a month and stop production for 4 hours, and the working conditions for ash removal are very bad.
Blast furnace gas mud and gas ash are by-products of the iron and steel industry. Every 1 ton of steel produced produces 20 kilograms of gas mud and gas ash containing 10%-20% zinc. According to reports, China's steel output in 2016 was 800 million tons, ranking first in the world for 16 consecutive years. Based on this calculation, the annual output of gas mud and gas ash in China is estimated to be 1.6 million tons, which is equivalent to 1.6 million to 3.2 million tons of zinc metal, which is equivalent to 25.88 million to 51.76 million tons of zinc ore mining. . If a 30 million tons steel company will produce 600,000 tons of gas ash, the zinc content is roughly 10.61%. Calculated on the basis of 600,000 tons of gas ash processing capacity, the annual gas ash produced will contain 60,000 tons of zinc. According to the 80% direct production rate, 48,000 tons of No. 5 zinc ingots can be obtained. The output value will be more than 1 billion yuan, and the profit and tax will be at least Above 150 million yuan. However, if these solid wastes cannot be properly treated and used rationally, they will not only cause serious pollution to the environment, but also cause huge resource losses.
3. R&D Ideas and Industrial Test Results
The original Huludao Zinc Smelting Plant was established in 1994. It is one of the important zinc smelting manufacturers in Liaoning Province and a large-scale private zinc smelting enterprise with high technical level in Liaoning Province. The products have a good reputation in domestic and foreign markets. In 2010, in accordance with national requirements, the plant completely eliminated the vertical tank zinc smelting process. In view of the abundant domestic reclaimed zinc resources and the support of national policies, coupled with the backward status of the original reclaimed zinc process, the plant organized relevant experts Established a research and development team with scientific researchers to break through the original recycled zinc production process to carry out research and development on the recycling of zinc-containing smoke and dust in steel plants. After more than 20 tests in 6 years, through multi-party research and research and development, it cost more than 60 million yuan, and finally successfully developed abroad. The technology and equipment for the production of regenerated zinc by electric heating or gas rotary kilns pioneered inside and outside, and respectively obtained national invention patents and utility model patents.
The trial production results show that the use of electric cargo gas rotary kiln to produce recycled zinc technology, the exhaust gas emissions in the production process meet the standard, the waste residue can be mixed to continue ironmaking, the waste water is recycled, the energy consumption is reduced by one-third compared with the primary zinc production process, and the metal recovery rate And product quality is in the leading position of domestic and foreign recycled zinc technology, and has the conditions for industrialized production and popularization and application.
Due to the characteristics of the process using electric energy to convert heat energy, it can realize automatic control throughout the whole process, which not only saves manpower, but also plays a vital role in the internal cost control of the enterprise. The specific conditions of each manufacturer choose the number of equipment, which is flexible and convenient; based on the successful technology research and development and the successful production of 10,000 tons, it is planned to build a zinc smelting plant with an annual output of 20,000 tons and use the solids produced by domestic steel enterprises. Waste materials have realized the use of gas or electric rotary kiln to produce recycled zinc technology to replace the existing zinc smelting technology with high energy consumption and high emissions.
The project uses self-developed gas or electric rotary kiln patented technology to process zinc-containing solid waste to produce secondary zinc. The characteristic of the process is that the process is short, the exhaust gas is the tail gas after natural gas combustion, and the water to wash the fume is recycled. The sediment is regularly removed and dried and then returned to the system to continue zinc smelting. The waste slag can be returned to the iron-smelting system for batching use, the zinc ingot can be used for the galvanized products of our factory, and the waste slag and waste ash generated during the galvanizing process can be returned to the zinc-smelting system for continued use. The patented technology is to mix various zinc-containing materials with zinc grades greater than 55% and waste coke powder or low-priced anthracite into a closed kiln for preheating, and the reduced zinc vapor is directly condensed into liquid zinc ingots. In addition, the solid waste slag can be returned to the ironmaking system for batching use, and can also be used in construction materials.
The patented technology has a simple process flow and low material requirements. It is also possible to directly put zinc-containing materials such as galvanizing into the kiln to reduce the production of zinc ingots.
4. Technical overview and innovation.
This technology is to add zinc-containing waste into the rotary kiln to start the reaction and produce zinc steam. The zinc vapor is introduced into the condensing system, and the mother zinc is lifted by the splash type graphite rotor, and the zinc liquid is used to absorb the introduced zinc vapor, and then the ingot is condensed. At the same time, the uncondensed zinc vapor and other smoke and dust enter the second condenser. The second condenser is a three-group hydraulic ejector. The smoke and dust washed by water enter the circulating pool for precipitation, and are regularly removed and dried to continue to be used as raw materials. The circulating water is replenished regularly, and there is no discharge. In addition, the purified carbon monoxide is sent to the drying system for supplementary fuel use, and the generated slag is cooled and discharged into the discharge system, and stored in the anti-leakage pool. It can not only be transferred to cement production plants and brick factories for aggregate use, but also Return to the ironmaking system for batching and use, and finally natural gas is sent into the burner through the gas slip ring and burned in the combustion chamber. The combustion exhaust gas is sent to the chimney through the induced draft fan and through the electric dust collector for discharge.
The innovation of this technology shows that: the use of special silicon carbide bricks to build the rotary kiln, separate the raw material feeding channel from the gas combustion channel, and indirectly heat the raw materials in the kiln, which is the core of the technology; the gear shaft hole is used for the material channel , The outer part of the gear is used for the combustion chamber.
Natural gas gas slip ring. The natural gas is sent into the burner through the gas slip ring, the rotary kiln rotates, the slip ring does not move, the natural gas is burned in the combustion chamber, and the combustion exhaust gas is sent to the chimney through the induced draft fan and the electric dust collector for discharge.
Both ends of the kiln are elastically sealed. In the zinc smelting process, the material channel cannot enter oxygen. In addition to rotating, the rotary kiln must move up and down in series. Therefore, the two ends of the feeding and zinc discharge adopt elastic seals.
Easy operation and high production efficiency. The main processes such as preheating, smelting and condensation in production are all completed in the kiln. The airtightness is good, the operation is simplified, and automatic control can be realized. Moreover, there are few operators and high production efficiency. The production efficiency of a single gas rotary kiln is up to daily 30 tons.
reduces the smelting temperature and shortens the smelting time. Compared with other pyrometallurgical smelting, the vertical motionless smelting is changed to horizontal rotation, and the material is changed from a columnar shape to a thin layer rolling motion. The material is heated evenly and quickly, so the smelting temperature can be reduced by 100 ℃-200 ℃, which can be shortened. Smelting time; uniform heating energy increases the metal recovery rate; low smelting temperature can reduce heat loss and reduce the consumption of refractory materials on the kiln wall.
Low energy consumption. Energy-saving measures have been adopted in the process, waste heat utilization, heat preservation, heating materials, heating methods, and raw material smelting pretreatment. The total energy consumption is 1.02 tons of standard coal per ton of zinc, which is not only far lower than the existing fire zinc smelting, but also Lower than hydrometallurgy.
Environmentally friendly. The raw material feeding channel and the gas combustion channel of the gas rotary kiln are separated, which is also the main feature of this patent. Only in this way can the smoke and combustion exhaust gas in the smelting process be better treated.
There are no special requirements for materials. The materials entering the kiln can be in powder, flake, or granular form; there are no strict requirements on the moisture, zinc grade, and lead content in the raw materials; Treatment process.
can recover a variety of valuable metals such as indium, cadmium, and lead. If the raw materials with high lead content are processed, it can also increase the income of lead and greatly improve the efficiency of smelting.
The product quality is good. Due to the low smelting temperature and less entrained impurities, zinc products are of the best quality in existing pyrometallurgical smelting, and each ton of zinc can increase sales income by about 500 yuan.
The process technology has also passed the review of the invention patent of the Huludao Zinc Smelting Plant "a method of electrothermal rotary kiln zinc smelting" and the utility model patent of "gas rotary kiln zinc smelting device" by the China Nonferrous Metals Industry Association.
5. Significant economic and social benefits
Through the construction of a new production system, a new development platform for the non-ferrous metal industry is formed, which is of great significance for strengthening the regional economy, expanding employment space and increasing residents’ income.
The patented technology used in this project has an internationally leading level, not only for pyrometallurgical zinc smelting enterprises, but also for other metal smelting, ferroalloys and other industries. Using rotary kiln smelting technology, the total value of its resource utilization, energy saving, emission reduction, and cost reduction will be more than 200 million yuan, which has a wide range of economic and social benefits.
6. The state's support for the secondary zinc industry is based on the National Hazardous Waste List and the Opinions of the General Office of the State
Council on the Implementation of Third-Party Control of Environmental Pollution, which took effect on August 1, 2016 (Guobanfa [2014] No. 69) Implementation Opinions of the Ministry of Environmental Protection on Promoting the Third-Party Treatment of Environmental Pollution (Huan Gui Cai Han [2017] No. 172), dust collected by dust collection and dust removal devices in the electric furnace steelmaking process, and waste water treatment sludge, in the lead-zinc smelting process The scum produced by cathode zinc melting, the leaching slag produced by the zinc oxide leaching treatment, the blast furnace scum produced by the blast furnace zinc smelting zinc vapor condensation separation system, the zinc slag produced by the zinc rectification furnace, the dust collected by the dust collection and dust removal device, regeneration In the zinc process, the dust collected by the dust removal device and the waste water treatment sludge are all included in the "National Hazardous Waste List", and stricter management will be implemented. With the gradual implementation of the elimination of backward production capacity in China and the gradual increase in environmental protection requirements, more emphasis is placed on circular economy. From the "Twelfth Five-Year Plan" to the "Thirteenth Five-Year Plan", the treatment of industrial solid waste has been included in the strategic emerging industries, and 50 national solid waste treatment industrial parks will be established by 2020. In 2015, the Ministry of Industry and Information Technology stipulated in the "Regulations for Lead and Zinc Industry" (2015 No. 20) that new projects that utilize zinc oxide ore and zinc-bearing secondary resources can reach 15,000 tons per year. From the above-mentioned aspects, it is shown that the state attaches great importance to the treatment of solid waste and advocates and supports the policy on the secondary zinc industry.
Link to this article: The Production Process Of Recycled Zinc From Zinc-Containing Waste
Reprint Statement: If there are no special instructions, all articles on this site are original. Please indicate the source for reprinting:https://www.cncmachiningptj.com/,thanks!
3, 4 and 5-axis precision CNC machining services for aluminum machining, beryllium, carbon steel, magnesium, titanium machining, Inconel, platinum, superalloy, acetal, polycarbonate, fiberglass, graphite and wood. Capable of machining parts up to 98 in. turning dia. and +/-0.001 in. straightness tolerance. Processes include milling, turning, drilling, boring, threading, tapping, forming, knurling, counterboring, countersinking, reaming and laser cutting. Secondary services such as assembly, centerless grinding, heat treating, plating and welding. Prototype and low to high volume production offered with maximum 50,000 units. Suitable for fluid power, pneumatics, hydraulics and valve applications. Serves the aerospace, aircraft, military, medical and defense industries.PTJ will strategize with you to provide the most cost-effective services to help you reach your target,Welcome to Contact us ( sales@pintejin.com ) directly for your new project.
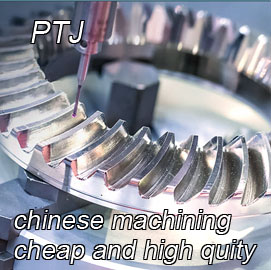
- 5 Axis Machining
- Cnc Milling
- Cnc Turning
- Machining Industries
- Machining Process
- Surface Treatment
- Metal Machining
- Plastic Machining
- Powder Metallurgy Mold
- Die Casting
- Parts Gallery
- Auto Metal Parts
- Machinery Parts
- LED Heatsink
- Building Parts
- Mobile Parts
- Medical Parts
- Electronic Parts
- Tailored Machining
- Bicycle Parts
- Aluminum Machining
- Titanium Machining
- Stainless Steel Machining
- Copper Machining
- Brass Machining
- Super Alloy Machining
- Peek Machining
- UHMW Machining
- Unilate Machining
- PA6 Machining
- PPS Machining
- Teflon Machining
- Inconel Machining
- Tool Steel Machining
- More Material