How to expand the profile extrusion capacity in the profile extrusion workshop?
Although many industries have been hit during the coronavirus pandemic, some parts of the construction products industry are booming. Obviously, some consumers who spend a lot of time at home prefer to do DIY and start to do something they want to create a more comfortable and pleasant environment. One of the results is an increase in demand for multiple types of profiles, including wood-plastic composite (WPC) deck and window profiles, to plastic panels, PVC fencing products, wall panels, baffles, and decorative ornaments.
Upstream in the supply chain, plastics and WPC processors welcome the increased demand for these extruded construction products. But for any extrusion processor, the new demand raises questions about how to expand production capacity cost-effectively. Recently, some extrusion processors have solved these problems by "going double profile", that is, converting a single-sided production line to a "double profile" production line to obtain unused extruder capacity, or by installing new, Larger double profile production lines instead of additional single-sided production lines to expand the scale.
Is this method suitable for your operation? Ask yourself these questions first.
1. Should I add a new production line?
If you are already running a productive extrusion line, the easiest way to substantially expand production may be to add the same new production line. Depending on the space availability of your plant, you can simply install more of the same, based on the exact same production model you are currently using. Therefore, the risk of making it work is low - you don't have to push the edge of technology. More importantly, your staff already knows exactly what to do. However, this method is usually more expensive than other alternatives.
2. Can I get more output from the existing products?
May be. If the production capacity of the extruder is not enough to run at full capacity, you can increase the output by speeding up the production line. If the speed of the extruder is increased and the increased output can be managed without affecting the quality of the profile, the output of the production line can be increased by 10% to 20%.
Extracting more output from the existing extrusion line is certainly a cost-effective method, but it requires you to be willing to take a certain risk, redefine the process, redevelop and experiment to obtain the additional output you need. But this is not very certain, because there are many variables: an increase in the speed of the extruder will increase the shear force, which will introduce process instability, profile stress or dimensional problems. Although existing tools may work, you may find that molds and downstream tools need to be lengthened or modified. Moreover, you need to adjust the speed, cooling capacity and other settings of the downstream equipment. Therefore, although there may sometimes be more benefits from the equipment you already own, the potential upside is limited to about 20%.
3. Is it possible to convert single wire to double wire?
Or build a new dual line from scratch? Both are fine. If your single-line extruder has at least 50% unused capacity, it is a wise investment to transform a single-profile production line into a dual-profile production line. If you can sell that much extra output in the foreseeable future, then the ROI numbers for converting to dual-line downstream equipment should be favorable. If you want to make use of excess extruder capacity, but the equipment space is limited, or you have tried to speed up a single extruder production line, but cannot stabilize the output at a higher production speed, then the dual-line transformation will become More favorable option. .
Consider the following example: the processor’s extruder has a rated output of 1500 lb/hr, but the output cannot be stabilized above 1000 lb/hr on a single downstream production line. In many cases, it is possible to successfully use the capacity of the extruder to convert the extrusion line to dual profile production to drive two profiles running at approximately 75% of the original single line speed, thereby increasing the total output by 50%. %. Moreover, since the operating speed of the double extrusion production line is slower than that of the original single extrusion, there will be almost no process stability problems.
The calibration table is equipped with profile-specific tools that can be vacuumed to help maintain and stabilize the shape of the hot profile from the extruder. The vacuum pump is located at the bottom of the table.
Processors that need to increase production should compare the benefits of adding multiple single contour lines with the benefits of using large-capacity double contour lines. For example, with the rapid popularity of maintenance-free WPC flooring, some flooring manufacturers have shifted their main production from a single line at a speed of about 1500 lb/hr (that is, 5/4×6 in. Floor/hr of 700+ ft.) To a larger production line. Two lines run 3000 to 3300 pounds per hour-or close to 1600 feet of pavement per hour.
Of course, packing twice the production capacity into a limited space requires a lot of planning. Upstream, there is a need to increase material handling and preparation capabilities. If you want to extrude WPC, you also need to increase the ability of drying and pelletizing. Due to the high moisture content of wood flour, hot air drying is usually used to dry the composite particles. And, in some applications, a second dehumidification and drying step may be required before extrusion. Then a larger extruder is needed. Downstream, everything needs to be copied-from tooling to cooling, measuring, hauling and cutting/material handling.
The dual model of commitment represents a major commitment to skills and resources. Compared with the single production line you are accustomed to using, to make these larger and larger production lines run stably and smoothly, it really takes more patience and energy, because you will work harder to promote the development of technology. But from a digital point of view, dual-line production may be a very wise investment.
Double effort, do things with your own knowledge
The key to a successful conversion from a single-contour extrusion line to a double-contour extrusion line is to work according to the method you already know. Essentially, the idea is to create the same second contour outside the extruder and replicate as much as possible the tools and process conditions that have proven successful on a single contour.
The first challenge for successful dual-line production is to generate a dual melt flow at the exit of the extruder. This involves the development and installation of "Y blocks", a tool that divides molten material into two equal streams. This output then flows through two identical die heads, providing two parallel profiles for downstream processing.
The second challenge is to steadily increase the output of the extruder. Obviously, if the excess capacity is to be utilized by extruding the second contour, the extruder will run faster than before. And you need to redefine and reprocess your process until the output of the extruder is stabilized and the double contour is successfully produced. Note that line speed, not extruder speed, is the key variable for profile quality. As long as the dual profile output runs at or below 100% of the single line speed, the profile should be able to be processed by basically the same downstream tools and equipment, and its quality is as good as the single line profile product.
Look downstream
Downstream of the extrusion die, the dual profile equipment is basically similar to the single line equipment, but is repeated and arranged in parallel. (For comparison purposes, dual-profile devices usually have the same length as single-line devices and require the same gap as single-line devices, but are about 50% wider.)
Many construction product extrusions, such as WPC flooring, WPC or PVC window profiles, PVC fences, etc., are all taken out of the extruder and "dried" through a series of sizing molds on the calibration table. The molds are equipped with an internal water cooling device, so they can maintain a uniform temperature relative to the hotter profile, and can drip water to gently lubricate the profile as it slides. To help thin or complex profiles maintain their shape, some of these molds may generate a vacuum.
The double-sided paint spray box can provide high-intensity evaporative spray cooling for the extrusion of larger profiles or profiles made of wood-plastic composite materials or other materials with higher cooling requirements.
Then, the profile enters the dual spray cooling box. Compared with immersion cooling, spray cooling is more efficient. The submerged cooling water tank can make the hot water around the high-temperature area form an insulating "layer", while the spray water tank uses more efficient evaporative cooling to dissipate more heat faster. For WPC extrusion (such as paving), spray cooling is necessary because the thermal index of the wood flour component is much higher than that of the typical polymer component in the composite mixture. The storage tank must also provide higher cooling water flow for WPC profiles, up to three times the flow required for ordinary plastic profiles. Spray cooling is also typical for large or complex vinyl extrusions used in window frames and fences.
The overall speed of the process can be fine-tuned using a double-wire double-end puller, which depends on the main extrusion control. Although the two cables share a common equipment housing, the speed of each cable is independently controlled. Therefore, everyone can fine-tune or "trim" the process speed in small increments based on the line speed and continuous feedback from the extrusion process controller. This is important because although the dual extrusion line is designed to have the same performance, small changes in the flow through the y-block and the extruder head are common, so these fine adjustments must be made. (It is necessary to adjust the speed of more than 10% by adjusting the rpm of the extruder.)
Following the puller, the profile then enters the double-wire saw table. Again, the speed of each line and the length of each profile are managed by a dual independent measurement system that drives a dual saw. The profile is cut to the final length and then pushed into the double dumping table, which accumulates and then discharges the cut length into the stack for picking and packaging.
Extrusion processors considering production expansion should consider multiple options. Although installing a new single production line with the same capacity as an existing production line is usually the simplest task, it is usually the most expensive in terms of capital and facility space costs. Adopting or converting to a dual profile production line requires a lot of preliminary planning and additional startup and process development time, but it can greatly reduce costs in terms of capital and facility space, and at the same time expand the overall production capacity of the enterprise.
Comparison of single wire and double wire
Processors who need additional extrusion capacity are faced with difficult choices on how to best expand. The following is a "rule of thumb" and intuitive comparison of two common expansion schemes.
• Example 1: Install two new single contour lines and a double contour line with the same throughput.
This example assumes that the capacity and throughput of the extruder of the two-line production line is twice that, and the two-line profile runs through two sets of tools, followed by the two-line spray tank, measuring system, drawing/unloading and unloading system. It is assumed that the two-wire device is the same in length and gap as the single-wire device, but the width is larger. For simplicity, each channel is assumed to be 8 feet wide.
• Example 2: Convert a single production line with an unused extruder with a capacity of 50% to dual profile output.
• Example 3: Production space requirements for single-contour and double-contour production
The accompanying illustrations compare the footprint requirements for installing four single co-extrusion lines (top) and two double co-extrusion lines. Lines are typical production lines used to make fences and deck profiles. These production lines are covered with PVC or color-stable WPC materials. Each line includes:
• Co-extruder and die head
• Calibration table with tools
• Cooling water tank
• Drag/pull
• Cutting saw
•Delivery table
Four single lines and overhaul channels require 9252 ft 2 /line, while two dual lines require 5334 ft 2 /line, which is twice the configuration file output.
Link to this article: How to expand the profile extrusion capacity in the profile extrusion workshop
Reprint Statement: If there are no special instructions, all articles on this site are original. Please indicate the source for reprinting:https://www.cncmachiningptj.com/,thanks!
3, 4 and 5-axis precision CNC machining services for aluminum machining, beryllium, carbon steel, magnesium, titanium machining, Inconel, platinum, superalloy, acetal, polycarbonate, fiberglass, graphite and wood. Capable of machining parts up to 98 in. turning dia. and +/-0.001 in. straightness tolerance. Processes include milling, turning, drilling, boring, threading, tapping, forming, knurling, counterboring, countersinking, reaming and laser cutting. Secondary services such as assembly, centerless grinding, heat treating, plating and welding. Prototype and low to high volume production offered with maximum 50,000 units. Suitable for fluid power, pneumatics, hydraulics and valve applications. Serves the aerospace, aircraft, military, medical and defense industries.PTJ will strategize with you to provide the most cost-effective services to help you reach your target,Welcome to Contact us ( sales@pintejin.com ) directly for your new project.
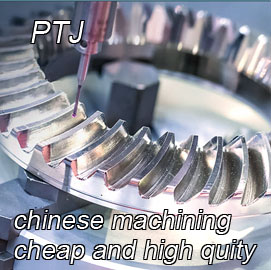
- 5 Axis Machining
- Cnc Milling
- Cnc Turning
- Machining Industries
- Machining Process
- Surface Treatment
- Metal Machining
- Plastic Machining
- Powder Metallurgy Mold
- Die Casting
- Parts Gallery
- Auto Metal Parts
- Machinery Parts
- LED Heatsink
- Building Parts
- Mobile Parts
- Medical Parts
- Electronic Parts
- Tailored Machining
- Bicycle Parts
- Aluminum Machining
- Titanium Machining
- Stainless Steel Machining
- Copper Machining
- Brass Machining
- Super Alloy Machining
- Peek Machining
- UHMW Machining
- Unilate Machining
- PA6 Machining
- PPS Machining
- Teflon Machining
- Inconel Machining
- Tool Steel Machining
- More Material