How much do you know about the six skills of the laser cutting machine in the actual cutting process?
During the cutting process of the laser cutting machine, the beam is focused by the lens of the cutting head into a small focal point, so that the focal point can reach a high power density, and the cutting head is fixed on the z axis. At this time, the heat input by the beam far exceeds the part of the heat reflected, conducted or diffused by the material, and the material is quickly heated to the melting and vaporization temperature. At the same time, a high-speed airflow will melt from the coaxial or non-coaxial side. And the vaporized material is blown out to form holes for cutting the material.
In recent years, laser cutting technology is developing at an unprecedented speed, with an annual growth rate of 15% to 20%. Since 1985, China has grown at a rate of nearly 25% per year. Compared with traditional oxyacetylene, plasma and other cutting processes, laser cutting speed is fast, the slit is narrow, the heat-affected zone is small, the edge of the slit is perpendicular, and the cutting edge is smooth. At the same time, there are many types of materials that can be laser cut, including carbon steel. , Stainless steel, alloy steel, wood, plastic, rubber, cloth, quartz, ceramics, glass, composite materials, etc.
During the cutting process, there are six practical functions. With these practical functions, the processing efficiency and cutting performance of the laser cutting machine can be greatly improved.
01 leapfrog
Leapfrogging is the idle way of laser cutting machines. As shown in the figure below, after cutting hole 1, then cutting hole 2. The cutting head must move from point A to point B. Of course, the laser must be turned off during the movement. The movement process from point A to point B, the machine runs "empty", which is called idling.
The idle stroke of the early laser cutting machine is shown in the following figure. The cutting head has to complete three actions: ascending (to a sufficiently safe height), translation (arriving above point B), and descending.
Compressing the idle time can improve the efficiency of the machine. If the next three actions are completed "simultaneously", the idle time can be shortened: when the cutting head starts from point A to point B, it rises at the same time; when it approaches point B, it falls at the same time. As shown below.
The trajectory of the cutting head's idle motion is like an arc drawn by a frog jumping.
In the development process of the laser cutting machine, the leapfrog can be regarded as an outstanding technological advancement. Leapfrogging only takes up the translational time from point A to point B, and saves the time of ascent and descent. The frog jumped and caught the food; the frog jump of the laser cutting machine "caught" high efficiency. If the laser cutting machine does not have the leapfrog function, I am afraid it will not enter the market.
02 Auto focus
When cutting different materials, the focus of the laser beam is required to fall at different positions on the cross-section of the workpiece. Therefore, it is necessary to adjust the position of the focus (focus). Early laser cutting machines generally used manual focusing; now, many manufacturers' machines have achieved automatic focusing.
Some people may say that just changing the height of the cutting head is just fine. When the cutting head is raised, the focal position is higher, and when the cutting head is lowered, the focal position is lower. It's not that simple.
In fact, during the cutting process, the distance between the nozzle and the workpiece (nozzle height) is about 0.5~1.5mm, which may be regarded as a fixed value, that is, the nozzle height does not change, so the focus cannot be adjusted by raising and lowering the cutting head (otherwise Unable to complete the cutting process).
The focal length of the focusing lens is immutable, so you cannot expect to adjust the focus by changing the focal length. If you change the position of the focus lens, you can change the focus position: the focus lens goes down, the focus goes down, and the focus lens goes up, the focus goes up. ——This is indeed a way of focusing. A motor is used to drive the focusing lens to move up and down to achieve automatic focusing.
Another automatic focusing method is: before the beam enters the focusing mirror, a variable curvature mirror (or adjustable mirror) is set, and the divergence angle of the reflected beam is changed by changing the curvature of the mirror, thereby changing the focus position. As shown below.
With the automatic focusing function, the processing efficiency of the laser cutting machine can be significantly improved: the perforation time of thick plates is greatly reduced; when processing workpieces of different materials and different thicknesses, the machine can automatically quickly adjust the focus to the most suitable position.
03 Automatic edge finding
As shown in the figure below, when the sheet is placed on the workbench, if it is skewed, it may cause waste during cutting. If the inclination angle and origin of the sheet can be sensed, the cutting process can be adjusted to suit the angle and position of the sheet to avoid waste. The automatic edge finding function came into being.
After the automatic edge finding function is activated, the cutting head starts from point P and automatically measures 3 points on the two vertical edges of the sheet: P1, P2, P3, and automatically calculates the inclination angle A of the sheet and the origin.
With the help of the automatic edge finding function, it saves the time of adjusting the workpiece earlier-it is not easy to adjust (move) workpieces weighing hundreds of kilograms on the cutting table, which improves the efficiency of the machine.
A high-power laser cutting machine with advanced technology and powerful functions is a complex system integrating light, machine and electricity. The subtlety often hides the mystery. Let us explore the mystery together.
04 Concentrated piercing
Centralized perforation, also known as pre-perforation, is a processing technology, not a function of the machine itself. When laser cutting thicker plates, each contour cutting process has to go through two stages: 1. perforation and 2. cutting.
Conventional processing technology (point A perforation→cut contour 1→point B perforation→cut contour 2→……), the so-called centralized perforation, is to carry out all the perforation processes on the entire board in advance, and then perform the cutting process again.
Concentrated piercing processing technology (complete perforation of all contours→return to starting point→cutting all contours). Compared with the conventional processing technology, the total length of the machine's running track is increased during concentrated piercing. Then why use concentrated piercing?
Concentrated perforation can avoid over-burning. During the perforation process of the thick plate, heat accumulation is formed around the perforation point. If it is cut immediately, overburning will occur. The centralized perforation process is adopted to complete all perforations and return to the starting point for cutting. Since there is sufficient time to dissipate heat, overburning is avoided.
Centralized perforation can improve processing efficiency. At present, there are still many laser cutting machines that do not have the function of automatic focusing. The process parameters (laser mode, power, nozzle height, auxiliary gas pressure, etc.) are different for processing thick plates, perforating and cutting. The height of the nozzle during the piercing process is higher than that of the cutting process.
If the conventional processing technology is adopted (contour 1 perforation→contour 1 cutting→contour 2 perforation→contour 2 cutting→……), in order to ensure the cutting quality and efficiency, the focus of the laser beam can only be manually adjusted to the best according to the cutting needs Position (Imagine if this is the case: at first, manually set the focus to the position required for the piercing, pierce; then, adjust the focus to the position required for cutting, cut; then adjust to the pierce position, pierce; ...; Until the processing is completed-this is simply a nightmare). Therefore, the focus during perforation must not be at the optimal position, and the perforation time is longer.
However, if the centralized perforation method is adopted, the focus can be adjusted to a position suitable for the perforation first, after the perforation is completed, the machine is paused, and then the focus position is adjusted to the best position required for cutting; in this way, the perforation time can be shortened by more than half , Greatly improve efficiency. Of course, if necessary, other process parameters can be adjusted or changed between concentrated piercing and cutting (for example, air + continuous wave can be used for piercing, and oxygen can be used for cutting, and there is enough time to complete the gas switch). We generally call the automatic zoom of the driving focus lens the F axis; like this, the manual zoom is used to concentrate the piercing and cutting, can it be called the "H" (Hand) axis "zoom"?
Concentrated piercing is also risky. If a collision occurs during the cutting process, which causes the position of the plate to change, the part that has not been cut may be scrapped. The centralized perforation process requires the help of an automatic programming system.
05 Bridge position (micro connection )
During the laser cutting process, the sheet material is supported by the serrated support bar. If the cut part is not small enough, it cannot fall from the gap of the support bar; if it is not big enough, it cannot be supported by the support bar; it may lose its balance and warp. The cutting head moving at high speed may collide with it, and the cutting head may be damaged in the light of the shutdown.
This phenomenon can be avoided by using the bridge position (micro-connection) cutting process. When programming the graphics for laser cutting, the closed contour is intentionally broken in several places, so that after the cutting is completed, the parts adhere to the surrounding materials without falling. These broken places are the bridges. Also known as breakpoint, or micro-connection (this name is derived from the blunt translation of MicroJoint). The distance of the break, about 0.2~1mm, is inversely proportional to the thickness of the sheet. Based on different angles, there are these different names: based on the contour, it is disconnected, so it is called a breakpoint; based on the part, it is adhered to the base material, so it is called a bridge or a micro-connection.
The bridge position connects the parts with the surrounding materials. The mature programming software can automatically add the appropriate number of bridge positions according to the length of the contour. It can also distinguish the inner and outer contours and decide whether to add bridges, so that the inner contours (waste) that do not leave the bridges will fall, and the outer contours (parts) of the bridges will be glued together with the base material and will not fall, thus avoiding Sorting work.
06 Common cutting
If the contours of adjacent parts are straight lines and the angles are the same, they can be combined into a straight line and cut once. This is the common edge cutting. Obviously, coedge cutting reduces the cutting length and can significantly improve processing efficiency.
Co-edge cutting does not require the shape of the part to be rectangular. As shown below.
The sky blue lines are common edges, and the common edges are cut, which not only saves cutting time, but also reduces the number of perforations. Therefore, the benefits are very obvious. If you save 1.5 hours a day due to common edge cutting, about 500 hours are saved every year, and the hourly comprehensive cost is 100 yuan, which is equivalent to creating an additional 50,000 yuan benefit a year. Common edge cutting needs to rely on intelligent automatic programming software.
So, what are the problems that the laser cutting machine often encounters in the actual cutting process?
Analysis of solutions to problems frequently encountered by laser cutting machines in the actual cutting process:
1. There is no response after the laser cutting machine is turned on
This kind of problem is generally caused by the output and input of the power supply, which can be solved by checking the power supply; the power failure is generally caused by the burning of the fuse or the problem of the power switch, which requires better and high-quality power fuse and Control switch.
2. The output light of the machine is very weak after running for a period of time
When encountering this situation, first check whether the focal length has changed. If there is no change, check whether the focusing lens on the machine has been contaminated; whether the light path system has accidentally deviated; the most important thing is to check whether the water circulation is flowing, and the water circulation is the most important thing. The smoothness can dissipate the heat of the laser cutting machine as much as possible, improve the energy conversion of the laser equipment, and finally achieve the focus of the light source.
3. Abnormal sparks often appear when cutting thin carbon steel
We know that when laser cutting thin carbon steel, the flames are normally long and flat, with fewer split ends, and abnormal sparks will affect the smoothness and processing quality of the workpiece's cutting surface. At this time, when other parameters are normal, the loss of the laser head nozzle should be considered. If the problem exists, the nozzle should be replaced in time. If there is no replacement of a new nozzle, the cutting working gas pressure should be increased. If the thread at the connection between the nozzle and the laser cutting head is loose, the laser cutting should be suspended immediately, check the connection status of the laser cutting head, and reinstall the thread.
4. The processed round hole or straight line deformation
When this kind of failure occurs, we should first rule out whether the laser cutting control software is moving normally. For example, draw a straight line to observe whether the laser head moves in a straight line during processing. This can basically eliminate the possibility of software problems. At the same time, this step can also find abnormal problems of looseness on the mechanical structure. After excluding software and mechanical possibilities, we should think about whether the laser energy is too high, and the non-processing area is affected by the high energy.
Observe whether the cutting edge of the workpiece is melted, the normal processing edge should be smooth and flat. When this happens, we should appropriately lower the laser power or frequency parameters to solve the problem. There is also a relatively uncommon one. Defects such as the deformation of the focusing lens in the laser head can also cause such problems. It can be judged by observing whether the beam from the laser head is concentric or not.
5. The workpiece often has burrs
The workpiece often has burrs. We must give priority to the factors that cause the burrs during the cutting operation, and cannot blindly increase the cutting speed, because the blindly increase the speed, in the actual cutting process, it is very easy to see the sheet not being cut through. This situation is particularly prominent when processing aluminum-zinc coated sheets. At this time, other factors of the machine tool should be taken into consideration to solve the problem, such as whether the nozzle should be replaced or the guide rail movement is unstable.
6. The laser is not completely cut
The reason for this kind of problem: check whether the selection of laser nozzle matches the thickness of the processed plate, replace the nozzle or process the plate; check whether the laser cutting line speed is too fast, you need to control and reduce the line speed according to the actual plate condition.
Link to this article: How much do you know about the six skills of the laser cutting machine in the actual cutting process?
Reprint Statement: If there are no special instructions, all articles on this site are original. Please indicate the source for reprinting:https://www.cncmachiningptj.com/,thanks!
3, 4 and 5-axis precision CNC machining services for aluminum machining, beryllium, carbon steel, magnesium, titanium machining, Inconel, platinum, superalloy, acetal, polycarbonate, fiberglass, graphite and wood. Capable of machining parts up to 98 in. turning dia. and +/-0.001 in. straightness tolerance. Processes include milling, turning, drilling, boring, threading, tapping, forming, knurling, counterboring, countersinking, reaming and laser cutting. Secondary services such as assembly, centerless grinding, heat treating, plating and welding. Prototype and low to high volume production offered with maximum 50,000 units. Suitable for fluid power, pneumatics, hydraulics and valve applications. Serves the aerospace, aircraft, military, medical and defense industries.PTJ will strategize with you to provide the most cost-effective services to help you reach your target,Welcome to Contact us ( sales@pintejin.com ) directly for your new project.
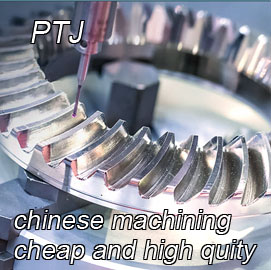
- 5 Axis Machining
- Cnc Milling
- Cnc Turning
- Machining Industries
- Machining Process
- Surface Treatment
- Metal Machining
- Plastic Machining
- Powder Metallurgy Mold
- Die Casting
- Parts Gallery
- Auto Metal Parts
- Machinery Parts
- LED Heatsink
- Building Parts
- Mobile Parts
- Medical Parts
- Electronic Parts
- Tailored Machining
- Bicycle Parts
- Aluminum Machining
- Titanium Machining
- Stainless Steel Machining
- Copper Machining
- Brass Machining
- Super Alloy Machining
- Peek Machining
- UHMW Machining
- Unilate Machining
- PA6 Machining
- PPS Machining
- Teflon Machining
- Inconel Machining
- Tool Steel Machining
- More Material