The CNC Machine Requirements For Position Detection Devices
Direct measurement and indirect measurement
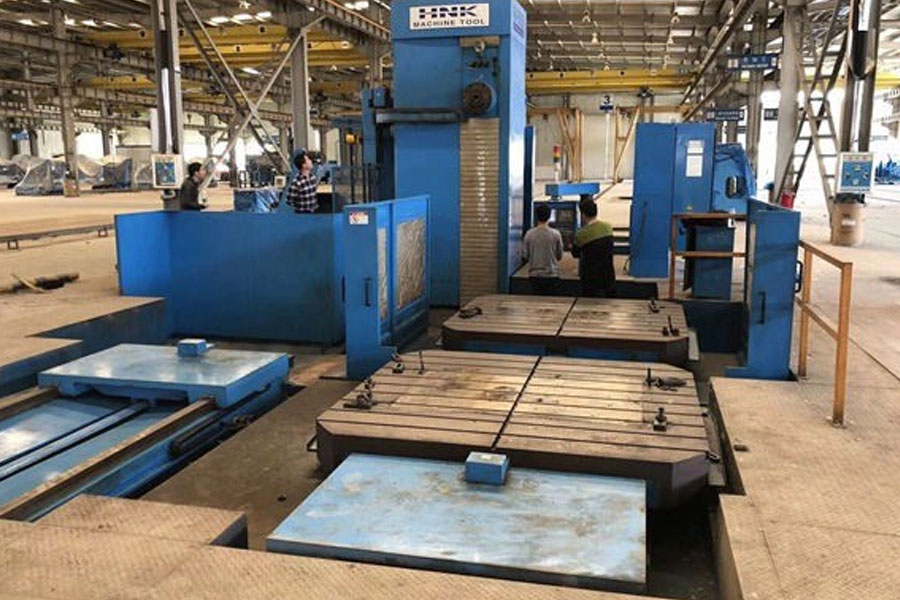
1. Direct measurement
Direct measurement is to install the detection device directly on the execution part, such as grating, inductosyn, etc. to directly measure the linear displacement of the workbench, and the position detection device is installed on the execution part (that is, the end piece) to directly measure the end piece of the execution part Linear displacement or angular displacement can form a closed-loop feed servo system. Measurement methods include linear grating, linear induction synchronizer, magnetic grating, laser interferometer, etc. to measure the linear displacement of the executive components. Because this detection method uses a linear detection device to measure the linear displacement of the machine tool, its advantage is that it directly reflects the linear displacement of the worktable; the disadvantage is that the detection device and the stroke length are required to be the same for large-scale CNC machine tools. , This is a big limitation.
2. Indirect measurement
Indirect measuring device is to install the detection device on the ball screw or drive motor shaft, and indirectly measure the linear displacement of the actuator by detecting the angular displacement of the rotating part.
The position detection device is installed on the transmission element or the drive motor shaft in front of the actuator to measure its angular displacement. After the transmission ratio is changed, the linear displacement of the actuator can be obtained. This can form a closed-loop servo feed system, such as a pulse encoder. On the motor shaft.
Indirect measurement is reliable and convenient to use, and has no length limitation; its disadvantage is that the transmission chain error that converts a straight line into a rotary motion is added to the detection signal, which affects the measurement accuracy. Generally, it is necessary to compensate the transmission error of the CNC machine tool in order to improve the positioning accuracy.
In addition to the above position detection devices, servo systems often include speed detection components to detect and adjust the engine speed. A commonly used component is a tachogenerator.
Position detection device is an important part of CNC machining tool servo system. Its function is to detect displacement and speed, send feedback signals, and form closed-loop or semi-closed-loop control. The machining accuracy of CNC machine tools is mainly determined by the accuracy of the detection system. Different types of CNC machine tools have different requirements for position detection components, accuracy requirements of the detection system, and higher moving speeds of the tested parts. The current level of the detection element and the system is: when the moving speed of the measured part is as high as 240m/min, the detection displacement resolution (the smallest amount of displacement that can be detected) can reach 1μm, such as 0.1μm at 24m/min.
CNC machine tools have the following requirements for position detection devices
- (1) It is less affected by temperature and humidity, works reliably, can maintain accuracy for a long time, and has strong anti-interference ability.
- (2) The accuracy and speed requirements can be met within the moving range of the machine tool's execution parts.
- (3) Easy to use and maintain, adapt to the working environment of the machine tool.
- (4) Low cost.
Link to this article: The CNC Machine Requirements For Position Detection Devices
Reprint Statement: If there are no special instructions, all articles on this site are original. Please indicate the source for reprinting:https://www.cncmachiningptj.com/,thanks!
3, 4 and 5-axis precision CNC machining services for aluminum machining, beryllium, carbon steel, magnesium, titanium machining, Inconel, platinum, superalloy, acetal, polycarbonate, fiberglass, graphite and wood. Capable of machining parts up to 98 in. turning dia. and +/-0.001 in. straightness tolerance. Processes include milling, turning, drilling, boring, threading, tapping, forming, knurling, counterboring, countersinking, reaming and laser cutting. Secondary services such as assembly, centerless grinding, heat treating, plating and welding. Prototype and low to high volume production offered with maximum 50,000 units. Suitable for fluid power, pneumatics, hydraulics and valve applications. Serves the aerospace, aircraft, military, medical and defense industries.PTJ will strategize with you to provide the most cost-effective services to help you reach your target,Welcome to Contact us ( sales@pintejin.com ) directly for your new project.
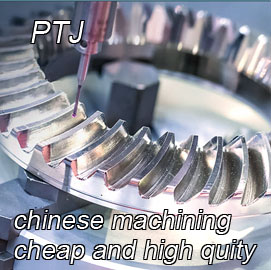
- 5 Axis Machining
- Cnc Milling
- Cnc Turning
- Machining Industries
- Machining Process
- Surface Treatment
- Metal Machining
- Plastic Machining
- Powder Metallurgy Mold
- Die Casting
- Parts Gallery
- Auto Metal Parts
- Machinery Parts
- LED Heatsink
- Building Parts
- Mobile Parts
- Medical Parts
- Electronic Parts
- Tailored Machining
- Bicycle Parts
- Aluminum Machining
- Titanium Machining
- Stainless Steel Machining
- Copper Machining
- Brass Machining
- Super Alloy Machining
- Peek Machining
- UHMW Machining
- Unilate Machining
- PA6 Machining
- PPS Machining
- Teflon Machining
- Inconel Machining
- Tool Steel Machining
- More Material