CNC Machining of Plastic Layered Parts
CNC (Computer Numerical Control) machining of plastic layered parts represents a specialized subset of manufacturing processes that combines the precision of computer-controlled machinery with the unique properties of laminated or layered plastic materials. This technique is widely employed in industries such as aerospace, automotive, electronics, medical device manufacturing, and consumer goods due to the versatility, durability, and cost-effectiveness of plastic laminates. The process involves shaping, cutting, drilling, or milling layered plastic materials to create components with high precision and specific mechanical or aesthetic properties. This article explores the principles, materials, processes, applications, challenges, and advancements in CNC machining of plastic layered parts, providing a comprehensive examination of this critical manufacturing domain.
Introduction to CNC Machining
CNC machining is a subtractive manufacturing process that uses pre-programmed computer software to control tools and machinery. The process is capable of working with a wide range of materials, including metals, plastics, wood, and composites. In the context of plastic layered parts, CNC machining involves the precise removal of material from laminated plastic workpieces to achieve desired geometries, tolerances, and surface finishes. Layered plastics, often referred to as laminates, consist of multiple layers of plastic or composite materials bonded together to enhance strength, flexibility, or other properties. These materials pose unique challenges and opportunities in CNC machining due to their anisotropic nature and varying mechanical properties across layers.
The history of CNC machining dates back to the 1940s, when numerical control (NC) systems were developed to automate machine tools. The integration of computers in the 1970s transformed NC into CNC, enabling greater precision and complexity in manufacturing. Today, CNC machining is a cornerstone of modern manufacturing, with applications in producing intricate plastic layered parts for diverse industries.
Characteristics of Plastic Layered Materials
Plastic layered materials, or laminates, are composite structures composed of multiple layers of plastic or plastic-based materials bonded together through processes such as adhesion, heat, or pressure. These materials are engineered to combine the desirable properties of individual layers, such as strength, flexibility, chemical resistance, or thermal stability. Common types of plastic laminates used in CNC machining include:
-
Thermoset Laminates: These include materials like phenolic, epoxy, and melamine laminates, which are cured through heat and pressure to form rigid, durable structures. Examples include G-10 (epoxy-glass laminate) and FR-4 (flame-retardant epoxy-glass laminate).
-
Thermoplastic Laminates: These are composed of thermoplastics such as polycarbonate, acrylic, or polyethylene, which can be softened and reshaped with heat. They are often used for flexible or semi-rigid parts.
-
Hybrid Laminates: These combine plastic layers with other materials, such as fiberglass, carbon fiber, or metal foils, to enhance specific properties like strength or conductivity.
-
Decorative Laminates: These consist of plastic layers with aesthetic surfaces, often used in consumer goods or architectural applications.
The mechanical properties of plastic laminates vary depending on the composition, orientation, and bonding of the layers. For instance, laminates with glass or carbon fiber reinforcement exhibit high tensile strength, while those with flexible thermoplastic layers offer greater impact resistance. The anisotropic nature of laminates—where properties differ along different axes—requires careful consideration during CNC machining to avoid issues like delamination or uneven wear.
Table 1: Common Plastic Laminates for CNC Machining
Material |
Composition |
Key Properties |
Applications |
Machinability |
---|---|---|---|---|
G-10 |
Epoxy + Glass Fiber |
High strength, electrical insulation |
Aerospace components, circuit boards |
Good, requires sharp tools |
FR-4 |
Flame-Retardant Epoxy + Glass Fiber |
Flame resistance, dimensional stability |
Electronics, insulators |
Good, prone to dust generation |
Polycarbonate Laminate |
Polycarbonate Layers |
Impact resistance, transparency |
Protective covers, medical devices |
Excellent, sensitive to heat |
Phenolic Laminate |
Phenolic Resin + Paper/Cotton |
Wear resistance, low cost |
Gears, bearings |
Moderate, abrasive to tools |
Acrylic Laminate |
Acrylic Layers |
Clarity, UV resistance |
Signage, displays |
Excellent, prone to cracking |
Hybrid (Carbon Fiber + Plastic) |
Thermoplastic + Carbon Fiber |
High strength-to-weight ratio |
Automotive, aerospace |
Challenging, requires diamond tools |
Principles of CNC Machining for Plastic Laminates
CNC machining of plastic layered parts involves several key principles that govern tool selection, machining parameters, and workpiece preparation. The primary goal is to achieve precise material removal while minimizing defects such as delamination, cracking, or thermal degradation. The following subsections outline the core aspects of the process.
Tool Selection
The choice of cutting tools is critical in CNC machining of plastic laminates due to their diverse mechanical properties. Common tool types include:
-
Carbide Tools: These are widely used for their durability and ability to maintain sharp edges when machining thermoset laminates like G-10 or FR-4.
-
Diamond-Coated Tools: These are preferred for abrasive laminates, such as those reinforced with carbon fiber, as they resist wear and provide clean cuts.
-
High-Speed Steel (HSS) Tools: These are suitable for softer thermoplastic laminates but may wear quickly when machining reinforced materials.
Tool geometry, such as rake angle and clearance angle, also plays a significant role. Positive rake angles reduce cutting forces and heat generation, while polished flutes minimize material adhesion. For layered plastics, tools with low helix angles are often used to reduce the risk of delamination.
Machining Parameters
Machining parameters, including spindle speed, feed rate, and depth of cut, must be optimized to balance productivity and part quality. Key considerations include:
-
Spindle Speed: High spindle speeds (10,000–30,000 RPM) are typically used for plastics to achieve smooth finishes and reduce heat buildup. However, excessive speeds can cause melting in thermoplastics.
-
Feed Rate: Moderate feed rates (100–500 mm/min) are preferred to prevent excessive tool wear or workpiece vibration. Lower feed rates are used for intricate features or thin laminates.
-
Depth of Cut: Shallow depths of cut (0.1–1 mm) are recommended to minimize stress on layered materials and prevent delamination.
Cooling methods, such as air cooling or mist lubrication, are often employed to dissipate heat and remove chips. Liquid coolants are generally avoided for plastic laminates, as they can cause swelling or chemical degradation.
Workpiece Preparation
Proper workpiece preparation is essential to ensure dimensional accuracy and prevent defects. Layered plastics are typically supplied as sheets, panels, or pre-formed blanks, which may require pre-machining steps such as:
-
Surface Cleaning: Removing contaminants like dust or oils to ensure proper tool engagement.
-
Fixturing: Using vacuum tables, clamps, or adhesive fixtures to secure the workpiece without inducing stress.
-
Pre-Drilling: Creating pilot holes for complex features to reduce stress during final machining.
The orientation of the laminate layers relative to the cutting tool must also be considered, as machining parallel to the layers can increase the risk of delamination compared to perpendicular cutting.
CNC Machining Processes for Plastic Layered Parts
Several CNC machining processes are used to fabricate plastic layered parts, each suited to specific geometries and applications. The most common processes include milling, drilling, turning, and routing.
CNC Milling
CNC milling is the most versatile process for machining plastic laminates, allowing the creation of complex 2D and 3D geometries. It involves the use of rotating multi-point cutting tools to remove material from the workpiece. Key milling techniques for plastic laminates include:
-
Face Milling: Used to create flat surfaces or reduce the thickness of laminate sheets.
-
Profile Milling: Employed to cut contours, slots, or pockets along the edges or interior of the workpiece.
-
Engraving: Applied for decorative or functional markings, such as serial numbers or logos.
Milling plastic laminates requires careful control of tool paths to avoid excessive vibration or heat buildup. Climb milling (where the tool rotates in the same direction as the feed) is often preferred to achieve smoother finishes and reduce delamination.
CNC Drilling
Drilling is used to create holes in plastic laminates for fasteners, electrical components, or fluid passages. The process is challenging due to the risk of delamination or cracking, particularly in thin or brittle laminates. Best practices include:
-
Using Peck Drilling: Incremental drilling with periodic tool retraction to clear chips and reduce heat.
-
Selecting Specialized Drill Bits: Brad-point or step drills are effective for clean entry and exit holes.
-
Backing Materials: Placing a sacrificial backing sheet (e.g., wood or plastic) beneath the workpiece to prevent exit-side delamination.
CNC Turning
Turning is less common for plastic laminates but is used for cylindrical or rotational parts, such as bushings or rollers. The process involves rotating the workpiece while a single-point cutting tool removes material. Turning plastic laminates requires low cutting forces and sharp tools to prevent surface tearing or layer separation.
CNC Routing
Routing is similar to milling but is typically performed on CNC routers designed for softer materials like plastics. It is widely used for cutting large laminate sheets into panels or shapes for applications like signage or furniture. Routers often use high-speed spindles and single-flute tools to achieve clean edges and high throughput.
Table 2: Comparison of CNC Machining Processes for Plastic Laminates
Process |
Suitable Geometries |
Typical Tools |
Advantages |
Challenges |
---|---|---|---|---|
Milling |
Complex 2D/3D shapes |
Carbide/Diamond End Mills |
High precision, versatility |
Heat buildup, delamination risk |
Drilling |
Holes, through-holes |
Brad-Point Drills |
Fast, cost-effective |
Exit-side damage, chip evacuation |
Turning |
Cylindrical parts |
HSS/Carbide Inserts |
Smooth finishes |
Limited to rotational parts |
Routing |
Flat panels, contours |
Single-Flute Routers |
High speed, large-scale |
Limited to 2D shapes |
Applications of CNC-Machined Plastic Layered Parts
CNC-machined plastic layered parts are integral to numerous industries due to their unique combination of properties, such as lightweight construction, corrosion resistance, and design flexibility. The following subsections highlight key applications across various sectors.
Aerospace Industry
In aerospace, plastic laminates like G-10 and carbon fiber-reinforced plastics are machined into components such as structural panels, insulation barriers, and interior fittings. These parts benefit from high strength-to-weight ratios and resistance to environmental factors like moisture and temperature fluctuations. CNC machining ensures tight tolerances for parts that must fit precisely within complex assemblies.
Electronics Industry
The electronics sector relies heavily on laminates like FR-4 for printed circuit boards (PCBs) and insulating components. CNC machining is used to drill precise holes for component mounting, cut board outlines, and create custom enclosures. The process accommodates the fine tolerances and intricate features required for modern electronics.
Automotive Industry
Plastic laminates are used in automotive applications for lightweight interior panels, dashboard components, and under-hood insulators. CNC machining allows manufacturers to produce parts with consistent quality and complex geometries, contributing to vehicle weight reduction and fuel efficiency.
Medical Device Manufacturing
In the medical field, CNC-machined plastic laminates are used for surgical instrument handles, diagnostic equipment housings, and implantable device components. Materials like polycarbonate and PEEK (polyetheretherketone) laminates are chosen for their biocompatibility and sterilizability. Precision machining ensures that parts meet stringent regulatory standards.
Consumer Goods and Architecture
Decorative laminates are machined into components for furniture, signage, and architectural cladding. CNC routing and milling enable the creation of intricate patterns and textures, enhancing the aesthetic appeal of these products. The durability and ease of maintenance of plastic laminates make them ideal for high-traffic environments.
Challenges in CNC Machining of Plastic Layered Parts
Despite its advantages, CNC machining of plastic layered parts presents several challenges that must be addressed to ensure quality and efficiency. These challenges stem from the material properties, process limitations, and environmental considerations.
Delamination
Delamination, or the separation of layers, is a common issue when machining plastic laminates. It occurs due to excessive cutting forces, improper tool geometry, or misalignment of the tool path with the layer orientation. Strategies to mitigate delamination include:
-
Using sharp, low-helix tools to reduce shear forces.
-
Optimizing feed rates and depths of cut to minimize stress.
-
Employing fixturing techniques that distribute clamping forces evenly.
Thermal Degradation
Plastic laminates, particularly thermoplastics, are susceptible to thermal degradation caused by excessive heat during machining. Melting, warping, or discoloration can occur if spindle speeds or feed rates are not properly controlled. Air cooling and low-friction tool coatings can help dissipate heat and maintain part integrity.
Tool Wear
Reinforced laminates, such as those with glass or carbon fiber, are highly abrasive and cause rapid tool wear. This increases production costs and requires frequent tool changes. Diamond-coated or polycrystalline diamond (PCD) tools are often used to extend tool life, but their high cost necessitates careful process optimization.
Dust and Chip Management
Machining plastic laminates generates fine dust and chips that can pose health risks and contaminate the workspace. Effective dust extraction systems and personal protective equipment (PPE) are essential to maintain a safe working environment. Additionally, chip evacuation must be managed to prevent tool clogging or surface damage.
Environmental Considerations
The production and machining of plastic laminates raise environmental concerns due to the use of non-renewable materials and the generation of waste. Sustainable practices, such as recycling laminate scraps or using bio-based plastics, are increasingly being adopted to address these issues.
Advancements in CNC Machining of Plastic Laminates
Recent advancements in CNC machining technology have improved the efficiency, precision, and sustainability of machining plastic layered parts. These developments span machine design, tooling, software, and process innovation.
High-Speed Machining
Modern CNC machines with high-speed spindles (up to 60,000 RPM) and advanced motion control systems enable faster material removal rates and finer surface finishes. These machines are particularly effective for machining thin or intricate laminate parts without compromising quality.
Multi-Axis Machining
Five-axis and six-axis CNC machines allow for complex geometries and reduced setup times by machining multiple surfaces in a single operation. This is particularly beneficial for aerospace and automotive components with curved or angled features.
Advanced Tooling
Innovations in tool materials, such as nano-composite coatings and hybrid carbide-diamond tools, have extended tool life and improved cutting performance. Additionally, adaptive tool paths that adjust cutting parameters in real-time help optimize machining for specific laminate properties.
CAM Software Integration
Computer-Aided Manufacturing (CAM) software has become more sophisticated, offering features like simulation, toolpath optimization, and material-specific machining strategies. These tools enable manufacturers to predict and mitigate issues like delamination or thermal stress before machining begins.
Automation and Robotics
The integration of robotics and automation in CNC machining has streamlined production processes, particularly for high-volume applications. Automated tool changers, workpiece handling systems, and in-process inspection technologies reduce labor costs and improve consistency.
Sustainable Machining Practices
Advancements in sustainable machining include the development of biodegradable laminates and the use of dry machining techniques to eliminate coolant waste. Additionally, closed-loop recycling systems for laminate scraps are being implemented to reduce material waste.
Table 3: Advancements in CNC Machining Technology for Plastic Laminates
Advancement |
Description |
Benefits |
Applications |
---|---|---|---|
High-Speed Machining |
Spindles up to 60,000 RPM |
Faster production, better finishes |
Thin laminates, electronics |
Multi-Axis Machining |
5/6-axis CNC systems |
Complex geometries, fewer setups |
Aerospace, automotive |
Advanced Tooling |
Nano-composite, hybrid tools |
Longer tool life, cleaner cuts |
Reinforced laminates |
CAM Software |
Simulation, optimization |
Reduced errors, faster programming |
All industries |
Automation |
Robotics, automated inspection |
Higher throughput, consistency |
High-volume production |
Sustainable Practices |
Biodegradable materials, dry machining |
Lower environmental impact |
Consumer goods, architecture |
Quality Control and Inspection
Ensuring the quality of CNC-machined plastic layered parts requires rigorous inspection and testing to verify dimensional accuracy, surface integrity, and mechanical performance. Common quality control methods include:
-
Dimensional Inspection: Using coordinate measuring machines (CMMs) or laser scanners to verify tolerances and geometries.
-
Surface Analysis: Employing profilometers or optical microscopes to assess surface roughness and detect defects like scratches or delamination.
-
Mechanical Testing: Conducting tensile, compressive, or shear tests to confirm the strength and integrity of machined parts.
-
Non-Destructive Testing (NDT): Techniques like ultrasonic testing or X-ray imaging are used to detect internal defects without damaging the part.
In-process monitoring systems, such as tool wear sensors or vibration analyzers, are increasingly used to detect issues during machining and prevent defective parts.
Future Trends in CNC Machining of Plastic Laminates
The future of CNC machining for plastic layered parts is shaped by emerging technologies, market demands, and environmental pressures. Key trends include:
-
Additive-Subtractive Hybrid Manufacturing: Combining 3D printing with CNC machining to create complex laminate structures with minimal material waste.
-
Smart Manufacturing: The adoption of Industry 4.0 technologies, such as IoT-enabled machines and AI-driven process optimization, to enhance productivity and quality.
-
Bio-Based Laminates: Increased use of sustainable, bio-derived plastics to meet environmental regulations and consumer preferences.
-
Micro-Machining: Advances in precision machining for micro-scale laminate parts, driven by demand in electronics and medical devices.
-
Customization and On-Demand Production: Growing use of CNC machining for low-volume, customized laminate parts enabled by flexible manufacturing systems.
Conclusion
CNC machining of plastic layered parts is a dynamic and evolving field that plays a critical role in modern manufacturing. By leveraging the precision of CNC technology and the unique properties of plastic laminates, manufacturers can produce high-quality components for a wide range of applications. Despite challenges like delamination and tool wear, advancements in tooling, machine design, and process optimization continue to enhance the efficiency and sustainability of the process. As industries demand lighter, stronger, and more environmentally friendly materials, the importance of CNC machining for plastic layered parts will only grow, supported by ongoing innovations and a commitment to quality.
Reprint Statement: If there are no special instructions, all articles on this site are original. Please indicate the source for reprinting:https://www.cncmachiningptj.com/,thanks!
3, 4 and 5-axis precision CNC machining services for aluminum machining, beryllium, carbon steel, magnesium, titanium machining, Inconel, platinum, superalloy, acetal, polycarbonate, fiberglass, graphite and wood. Capable of machining parts up to 98 in. turning dia. and +/-0.001 in. straightness tolerance. Processes include milling, turning, drilling, boring, threading, tapping, forming, knurling, counterboring, countersinking, reaming and laser cutting. Secondary services such as assembly, centerless grinding, heat treating, plating and welding. Prototype and low to high volume production offered with maximum 50,000 units. Suitable for fluid power, pneumatics, hydraulics and valve applications. Serves the aerospace, aircraft, military, medical and defense industries.PTJ will strategize with you to provide the most cost-effective services to help you reach your target,Welcome to Contact us ( sales@pintejin.com ) directly for your new project.
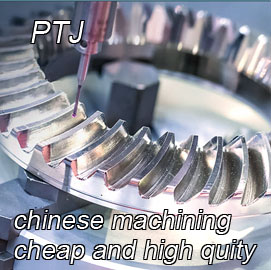
- 5 Axis Machining
- Cnc Milling
- Cnc Turning
- Machining Industries
- Machining Process
- Surface Treatment
- Metal Machining
- Plastic Machining
- Powder Metallurgy Mold
- Die Casting
- Parts Gallery
- Auto Metal Parts
- Machinery Parts
- LED Heatsink
- Building Parts
- Mobile Parts
- Medical Parts
- Electronic Parts
- Tailored Machining
- Bicycle Parts
- Aluminum Machining
- Titanium Machining
- Stainless Steel Machining
- Copper Machining
- Brass Machining
- Super Alloy Machining
- Peek Machining
- UHMW Machining
- Unilate Machining
- PA6 Machining
- PPS Machining
- Teflon Machining
- Inconel Machining
- Tool Steel Machining
- More Material