How To Assemble & Install CNC Machine Tools The Right Way and Good Tips
2023-10-30
Chapter 1: Understanding CNC Machines
In this chapter, we will lay the foundation by exploring what CNC machines are, the various types available, and the key components that make up a CNC machine.a. What is a CNC Machine?
A CNC machine, short for Computer Numerical Control machine, is a sophisticated piece of equipment used in manufacturing and machining processes. Unlike conventional machines operated manually by human operators, CNC machines are automated and controlled by computers, allowing for precise and highly repeatable operations. These machines are capable of executing complex tasks such as cutting, drilling, milling, and shaping materials like metal, plastic, wood, and more. At the core of a CNC machine is its ability to interpret and execute commands from computer-aided design (CAD) or computer-aided manufacturing (CAM) software. This software generates a series of numerical codes, often referred to as G-codes and M-codes, which instruct the CNC machine on how to move its cutting tools and workpiece to achieve the desired outcome. CNC machines have revolutionized manufacturing industries by increasing efficiency, reducing human error, and enabling the production of intricate and customized components.b. Types of CNC Machines
CNC machines come in various types, each designed for specific applications and industries. Here are some common types of CNC machines:- CNC Milling Machines: These machines are used to cut and shape materials by rotating cutting tools. They are widely employed in industries such as aerospace, automotive, and metalworking for tasks like drilling, milling, and engraving.
- CNC Lathes: CNC lathes are designed to rotate the workpiece while a cutting tool is used to remove material from it. They are essential for manufacturing cylindrical components, such as shafts and bushings.
- CNC Routers: These machines are primarily used for cutting and shaping materials like wood, plastic, and composites. CNC routers are common in woodworking and sign-making industries.
- CNC Plasma Cutters: Ideal for cutting metal sheets, CNC plasma cutters use a high-velocity jet of ionized gas to melt and remove material. They are employed in metal fabrication and automotive industries.
- CNC Laser Cutters: Laser cutting machines use a high-powered laser beam to precisely cut or engrave various materials, including metals, plastics, and textiles. They find applications in industries ranging from jewelry making to industrial manufacturing.
- CNC Waterjet Cutters: Waterjet cutters use a high-pressure stream of water mixed with abrasive particles to cut through materials. They are suitable for cutting a wide range of materials, including stone, glass, and metals.
- CNC EDM Machines: Electrical Discharge Machining (EDM) machines use electrical discharges to erode material from the workpiece. They are used for intricate and high-precision tasks, especially in tool and die making.
c. Components of a CNC Machine
Understanding the components of a CNC machine is crucial for effective operation and maintenance. Here are the key components found in most CNC machines:- Machine Frame: The machine frame provides the structural support for the entire CNC machine. It is typically made of heavy-duty materials to ensure stability and rigidity during operation.
- Spindle: The spindle is a motorized component responsible for holding and rotating cutting tools or attachments. It plays a pivotal role in the machining process's precision and speed.
- Axis System: CNC machines operate along multiple axes, usually labeled as X, Y, and Z. These axes define the machine's movement in three-dimensional space. Some machines may have additional rotational axes, such as A, B, and C, for more complex operations.
- Tool Changer: Many CNC machines are equipped with automatic tool changers that allow for the rapid switching of cutting tools during a machining process. This improves efficiency and reduces downtime.
- Control Panel: The control panel contains the interface through which operators or programmers can input commands, load programs, and monitor the machine's status.
- Worktable or Workholding System: The worktable is where the workpiece is securely held in place during machining. Various workholding devices, such as clamps, vises, and fixtures, are used to ensure the workpiece remains stable and properly positioned.
- Drive System: The drive system comprises motors and actuators responsible for moving the machine's components along the specified axes. Precise control of the drive system is essential for accurate machining.
- Coolant System: Cooling is vital during Multi Axis Cnc Machining to prevent overheating of tools and workpieces. CNC machines often have a coolant system in place to maintain the optimal temperature.
- Control Computer: The control computer houses the hardware and software necessary for running the CNC machine. It interprets the G-codes and M-codes generated by CAD/CAM software and converts them into movements and actions.
Chapter 2: Pre-Installation Preparation
Before you embark on the installation of your CNC machine, it's crucial to make thorough preparations. This chapter will guide you through the essential pre-installation considerations, including workspace setup, power and electrical requirements, and safety measures to ensure a smooth and safe installation process.a. Workspace Considerations
- Space Requirements: Begin by assessing the available space in your workshop or facility. Ensure that the area is spacious enough to accommodate your CNC machine, including sufficient room for safe access and maintenance. Consider the machine's dimensions, the space required for material handling, and any additional equipment or workstations.
- Ventilation: Adequate ventilation is crucial to dissipate heat generated during machining and to remove any potentially harmful fumes or dust particles. Install proper ventilation systems or air filtration equipment as needed to maintain a clean and safe working environment.
- Flooring: Ensure that the flooring in the designated area is level, stable, and able to support the weight of the CNC machine. Uneven or weak flooring can lead to machine vibrations and inaccuracies during operation.
- Accessibility: Plan for easy access to the CNC machine for installation, maintenance, and repair. Make sure there are clear pathways and sufficient space for maneuvering heavy machinery and materials.
- Lighting: Adequate lighting is essential for safe and accurate operation. Ensure that the workspace is well-lit to prevent accidents and to provide clear visibility of the machining process.
b. Power and Electrical Requirements
- Electrical Supply: Determine the specific electrical requirements of your CNC machine. Check the machine's technical specifications and consult with the manufacturer or supplier to ensure your facility's electrical supply meets these requirements.
- Voltage and Phase: CNC machines may require different voltage levels (e.g., 110V, 220V, 440V) and phases (single-phase or three-phase). Ensure that the electrical supply matches the machine's specifications.
- Electrical Panel: Install a dedicated electrical panel for the CNC machine to prevent overloading existing circuits. Employ a licensed electrician to handle the wiring and connections professionally.
- Surge Protection: Invest in surge protection devices to safeguard the CNC machine's sensitive electronic components from voltage fluctuations and electrical surges.
- Grounding: Ensure proper grounding of both the CNC machine and the electrical system to mitigate the risk of electrical hazards and equipment damage.
c. Safety Measures
- Safety Equipment: Prioritize safety by providing appropriate personal protective equipment (PPE) for operators and technicians. This may include safety glasses, hearing protection, gloves, and protective clothing.
- Emergency Procedures: Develop and document emergency shutdown procedures that can quickly stop the CNC machine in case of unforeseen events or accidents. Ensure that all personnel are trained in these procedures.
- Fire Safety: Install fire extinguishers and smoke detectors in the vicinity of the CNC machine. Implement fire safety protocols, such as keeping flammable materials away from the machine and maintaining a fire exit plan.
- Lockout/Tagout (LOTO): Implement LOTO procedures to prevent accidental machine startup during maintenance or repair. Use locks and tags to indicate when a machine is undergoing servicing.
- Safety Training: Conduct comprehensive safety training for all personnel who will operate, maintain, or work around the CNC machine. Emphasize safe practices and the importance of following safety protocols.
- First Aid: Keep a well-stocked first aid kit in the vicinity of the CNC machine. Ensure that trained personnel are available to provide immediate first aid in case of injuries.
Chapter 3: Assembling the CNC Machine
Once you have completed the pre-installation preparations, it's time to move on to the assembly phase. In this chapter, we will provide a step-by-step guide on assembling your CNC machine, covering essential tasks from unpacking and inspection to cable management.a. Unpacking and Inspection
- Unboxing: Begin by carefully unpacking all components of your CNC machine. Follow the manufacturer's instructions for unpacking to avoid any damage during the process. Use appropriate tools and lifting equipment if needed.
- Component Inventory: Create an inventory checklist to ensure that you have received all the components listed in the machine's manual or documentation. Verify that nothing is missing or damaged.
- Inspect for Damage: Examine each component thoroughly for any signs of damage, such as dents, scratches, or bent parts. Document any issues and notify the manufacturer or supplier immediately.
b. Organizing Components
- Organize Work Area: Before assembly, ensure that your workspace is clean and well-organized. Clear any clutter and provide ample space to lay out and organize components.
- Group Similar Parts: Group similar parts together to facilitate the assembly process. Components such as fasteners, brackets, and hardware should be organized in separate containers or trays for easy access.
- Refer to Manuals: Review the assembly manuals and documentation provided by the manufacturer. Familiarize yourself with the assembly steps, diagrams, and any specific instructions.
c. Assembling the Machine Frame
- Base Assembly: Begin with the base of the CNC machine. Follow the manufacturer's instructions to assemble the base frame securely. Ensure that it is level and stable.
- Column and Support Structures: Assemble the columns and support structures, aligning them accurately with the base. Tighten all bolts and fasteners to the recommended torque values.
- Guideways and Rails: Install the guideways and rails that will guide the movement of the machine's cutting or tool-holding components. Ensure they are properly aligned and securely attached.
d. Attaching Motors and Drives
- Motor Installation: Mount the motors in their designated positions according to the manufacturer's instructions. Ensure that the motors are securely fastened and aligned with the drive mechanisms.
- Drive System: Connect the motors to the drive mechanisms using appropriate couplings or belts. Ensure proper tension and alignment to prevent backlash and inaccuracies.
e. Installing the Control Panel
- Control Panel Mounting: Install the control panel in a convenient location, usually within easy reach of the operator. Ensure that it is securely mounted and positioned for optimal visibility and accessibility.
- Electrical Connections: Connect the control panel to the machine's electrical system following the wiring diagrams provided in the manufacturer's documentation. Double-check all connections for accuracy.
f. Cable Management
- Cable Routing: Carefully route all cables, wires, and hoses in an organized manner to prevent tangling or interference with moving parts. Use cable trays or clips to secure and protect cables.
- Labeling: Label cables and wires with identifying markers or tags to simplify troubleshooting and maintenance. Clearly mark each cable's purpose and destination.
- Testing: Before closing up any enclosures or panels, conduct a preliminary test to ensure that all electrical connections are functioning correctly. Verify that motors and sensors respond as expected.
Chapter 4: Aligning and Leveling
In Chapter 4, we will delve into the critical process of aligning and leveling your CNC machine. Proper alignment and leveling are fundamental to ensuring the accuracy and precision of your machine's operations. This chapter covers the importance of alignment and leveling, the tools and equipment needed, and a step-by-step guide for the alignment and leveling process.a. Importance of Alignment and Leveling
- Accuracy and Precision: Alignment and leveling are essential for achieving the high degree of accuracy and precision required in CNC machining. Misalignment or unevenness can lead to dimensional errors in the finished workpieces.
- Reduced Wear and Tear: Proper alignment reduces unnecessary stress on machine components, such as bearings and guideways. This prolongs the machine's lifespan and reduces maintenance costs.
- Minimized Vibration: A well-aligned and leveled machine generates fewer vibrations, resulting in better surface finishes and reduced tool wear. Vibrations can also affect the longevity of sensitive electronic components.
- Safety: Misaligned or unlevel machines can pose safety hazards. For instance, a machine that is not level may tip or move unexpectedly during operation.
b. Tools and Equipment Needed
To perform alignment and leveling correctly, you will need the following tools and equipment:- Precision Levels: High-quality precision levels are crucial for accurately measuring the machine's alignment and leveling.
- Adjustment Tools: Depending on your machine's design, you may require specific tools such as wrenches, shims, or adjustment screws.
- Dial Indicators: Dial indicators help in measuring the alignment of various machine components, including the tool spindle and worktable.
- Feeler Gauges: Feeler gauges are used to measure gaps and clearances between machine components during alignment.
- Alignment Laser: An alignment laser can be useful for assessing the straightness of guideways and other linear components.
c. Step-by-Step Alignment and Leveling Process
Follow these steps to align and level your CNC machine:Step 1: Prepare the Workspace
Ensure that the workspace is clean, free of debris, and well-lit. Clear any obstacles that may hinder the alignment and leveling process.Step 2: Reference Point Establishment
Select a stable reference point on the machine frame or base, usually provided by the manufacturer. This point will serve as the starting reference for all measurements.Step 3: Level the Machine
- Place precision levels on various surfaces of the machine, such as the base, columns, and worktable.
- Adjust the leveling screws or shims as needed to achieve perfect horizontal alignment. Check the bubble indicators on the levels for precision.
Step 4: Alignment of Guideways and Slides
- Use dial indicators and alignment lasers to check the straightness and parallelism of guideways, slides, and other linear components.
- Adjust the appropriate components to correct any misalignment detected.
Step 5: Spindle Alignment
- Mount a dial indicator on the machine's spindle or tool holder.
- Rotate the spindle to check for runout and concentricity. Adjust the spindle as necessary to minimize runout.
Step 6: Worktable Alignment
- Check the alignment of the worktable or workholding fixture using dial indicators.
- Adjust the worktable's positioning to ensure it is perpendicular to the machine's axes.
- After adjustments, recheck all alignments to ensure they meet the specified tolerances.
- Conduct test runs to verify that the machine operates accurately and produces the desired results.
Step 8: Documentation
Keep detailed records of the alignment and leveling process, including measurements, adjustments made, and any issues encountered. This documentation will be valuable for future reference and maintenance.Step 9: Final Inspection and Certification
Consider having a qualified technician or engineer perform a final inspection and certification to ensure that the CNC machine meets industry standards and safety requirements. Proper alignment and leveling are essential for the reliable and accurate operation of your CNC machine. Take your time during this process, as precision is paramount. By following these steps and using the right tools, you can ensure that your machine is in optimal condition for successful machining operations. In the next chapter, we will explore the electrical wiring requirements for your CNC machine.Chapter 5: Electrical Wiring
In this chapter, we will delve into the electrical wiring aspects of your CNC machine installation. Proper electrical wiring is crucial for the safe and efficient operation of the machine. This chapter covers understanding electrical systems, wiring the CNC machine, and important safety precautions.a. Understanding Electrical Systems
- Power Supply: CNC machines require a stable and appropriate power supply. Understand the voltage, frequency, and phase requirements specified by the machine manufacturer. Ensure that the power supply is reliable and has adequate capacity to handle the machine's electrical load.
- Electrical Panel: Most CNC machines have an electrical panel that houses various components, including circuit breakers, relays, contactors, and terminal blocks. Familiarize yourself with the components in the panel and their functions.
- Wiring Diagrams: Review the wiring diagrams provided by the machine manufacturer. These diagrams illustrate the connections between components and are essential for correct wiring.
- Grounding: Proper grounding is critical for safety. Ensure that the machine and the electrical system are grounded according to local electrical codes and the manufacturer's recommendations.
b. Wiring the CNC Machine
Follow these steps to wire your CNC machine:Step 1: Power Off
Ensure that the machine and the power source are turned off before you begin any wiring work. Disconnect the machine from the power source.Step 2: Wiring Plan
Create a wiring plan based on the manufacturer's wiring diagrams. Identify the components, such as motors, sensors, switches, and the control panel, and determine their interconnections.Step 3: Cable Selection
Use appropriate cables and wires that meet the machine's voltage and current requirements. Ensure that the cables are of the correct gauge and insulation type.Step 4: Cable Routing
Carefully route the cables and wires along the machine's cable trays or conduits. Keep them organized and separate from moving components to prevent damage.Step 5: Terminal Connections
Connect the wires to the appropriate terminals on components like motors, sensors, and switches. Ensure secure connections by crimping or soldering as required. Use wire labels for easy identification.Step 6: Control Panel Wiring
Inside the control panel, connect the wires to the respective terminal blocks, circuit breakers, contactors, and relays as specified in the wiring diagrams. Be meticulous in your work to avoid cross-connections or loose wires.Step 7: Power Supply Connection
Connect the machine to the power supply following the manufacturer's guidelines. Double-check the voltage, phase, and frequency settings to ensure they match the machine's requirements.Step 8: Safety Measures
Implement safety features such as emergency stop switches and safety interlocks as necessary. Ensure that these safety devices are wired correctly and tested for functionality.Step 9: Testing
Before closing the control panel and powering up the machine, perform a continuity test to check for any wiring faults or short circuits. Ensure that all connections are secure and free from loose strands.c. Safety Precautions
- Lockout/Tagout (LOTO): Implement LOTO procedures to prevent accidental machine startup during wiring or maintenance activities. Lockout devices should be used to isolate power sources.
- Qualified Electrician: Electrical work should be performed by a qualified electrician or technician who is knowledgeable about the machine's electrical requirements and local electrical codes.
- Overload Protection: Install appropriate overload protection devices, such as circuit breakers or fuses, to prevent damage in case of electrical faults.
- Grounding: Ensure that the machine and all electrical components are properly grounded to prevent electrical hazards.
- Labeling: Clearly label all wires, cables, and components to facilitate troubleshooting and future maintenance.
- Regular Inspections: Periodically inspect the electrical system for signs of wear, damage, or loose connections. Address any issues promptly.
- Emergency Procedures: Establish and communicate emergency procedures for electrical issues, including electrical fires or electrical shock incidents.
Chapter 6: Installing the Control Software
In this chapter, we will explore the installation process of the control software for your CNC machine. The control software is the brain of your CNC system, responsible for interpreting and executing the machining instructions. This chapter covers an overview of CNC machine control software, a step-by-step guide for software installation, and the calibration and testing procedures.a. CNC Machine Control Software Overview
- Role of Control Software: CNC machine control software is responsible for translating the design and toolpath data from CAD/CAM software into specific machine movements. It generates the G-codes and M-codes that command the machine's motors and actuators.
- Types of Control Software: There are various types of CNC control software, ranging from proprietary software provided by machine manufacturers to open-source and third-party solutions. Choose software that suits your machine's requirements and your familiarity with its interface.
- Features: Control software can vary in terms of features and capabilities. Look for software that offers the necessary functionalities for your specific machining needs, such as toolpath generation, tool changes, and spindle speed control.
b. Step-by-Step Software Installation
Follow these steps to install the control software for your CNC machine:Step 1: System Requirements
Check the system requirements specified by the control software manufacturer. Ensure that your computer meets these requirements in terms of hardware, operating system, and available memory.Step 2: Software Download or Installation Media
Obtain the control software either by downloading it from the manufacturer's website or using installation media provided by the manufacturer.Step 3: Installation
- Double-click on the software installation file to initiate the installation process.
- Follow the on-screen instructions provided by the installer. This may include selecting installation directories, accepting license agreements, and configuring software settings.
- Ensure that the installation is successful, and no errors are encountered.
Step 4: Licensing and Activation
If the control software requires licensing or activation, follow the manufacturer's guidelines to complete this process. Ensure that you have the necessary license keys or activation codes.Step 5: Machine Configuration
Configure the control software to match the specifications of your CNC machine. This may involve setting parameters for the machine's axes, motor types, and other hardware components.Step 6: Tool and Material Database
Create or import a tool and material database into the control software. This information is crucial for toolpath generation and selecting appropriate machining parameters.c. Calibration and Testing
After the control software is installed, follow these steps for calibration and testing:Step 1: Homing and Reference Point Setup
- Home the machine by moving all axes to their reference or home positions. This establishes a known starting point for the machine's movements.
- Verify that the machine returns to the reference position accurately.
Step 2: Tool Calibration
- Calibrate the tool length and tool diameter. This ensures that the machine knows the exact dimensions of the tools it will use.
- Perform test cuts or tool touch-off routines to validate tool calibration.
Step 3: Workpiece Setup
- Secure a test workpiece or material on the machine's worktable or workholding system.
- Ensure that the workpiece is properly aligned and secured.
Step 4: Test Runs
- Load a simple test program into the control software.
- Run the test program to observe the machine's movements and machining results.
- Check for any issues such as unexpected movements, tool collisions, or inaccuracies.
Step 5: Fine-Tuning
If issues are identified during testing, fine-tune the control software settings, tool offsets, or workpiece setup as necessary. Repeat test runs until the machine performs accurately and reliably.Step 6: Documentation
Document all calibration and testing results, including any adjustments made to the control software. This documentation is valuable for future reference and troubleshooting. The installation of control software is a crucial step in the CNC machine setup process. By following the manufacturer's instructions, calibrating the machine, and conducting thorough testing, you can ensure that your CNC machine is ready for production and capable of producing precise and accurate results. In the next chapter, we will explore the importance of lubrication and maintenance in maintaining the performance and longevity of your CNC machine.Chapter 7: Lubrication and Maintenance
In this chapter, we will focus on the critical aspects of lubrication and maintenance for your CNC machine. Proper lubrication and regular maintenance are essential for ensuring the longevity, accuracy, and reliability of your CNC equipment. We will cover the importance of lubrication, lubrication points, and establishing a maintenance schedule.a. Why Lubrication is Important
Lubrication plays a vital role in the performance and longevity of your CNC machine for several reasons:- Friction Reduction: Lubrication reduces friction between moving parts, such as bearings, guideways, and ball screws. This minimizes wear and tear on components, extending their lifespan.
- Heat Dissipation: Lubricants dissipate heat generated during machining, preventing overheating of critical components. This helps maintain dimensional accuracy and reduces the risk of thermal expansion.
- Smooth Operation: Proper lubrication ensures smoother and more precise movements of the machine's components. This is essential for achieving the high precision required in CNC machining.
- Preventing Corrosion: Lubricants provide a protective barrier against moisture and contaminants, reducing the risk of corrosion on metal surfaces.
- Noise Reduction: Lubrication can reduce the noise generated during machine operation, creating a quieter and more comfortable working environment.
b. Lubrication Points
Different CNC machines have various lubrication points that require attention. Here are some common lubrication points to consider:- Linear Guideways: Apply lubricant to the linear guideways, which facilitate the movement of the machine's axes. These may include ball screws, linear bearings, and slideways.
- Spindle Bearings: Lubricate the spindle bearings to ensure smooth rotation and reduce friction during cutting or machining operations.
- Tool Changer Mechanism: If your machine has an automatic tool changer, ensure that the mechanism's moving parts are adequately lubricated to prevent jams or malfunctions.
- Gearboxes: Gearboxes, if present in your machine, may require lubrication at specified intervals to maintain efficiency and reduce wear.
- Ball Screws: Ball screws are crucial components in CNC machines. Proper lubrication of ball screws and their associated components is essential for accurate positioning and movement.
- Coolant Pump: If your machine uses a coolant system, ensure that the pump is properly lubricated and that the coolant is clean and free from contaminants.
- Axis Motors: Depending on the type of motors used for axis movement (e.g., stepper or servo), follow manufacturer recommendations for lubrication or maintenance.
- Seals and Gaskets: Inspect and replace worn or damaged seals and gaskets as needed to prevent lubricant leakage and contamination.
c. Maintenance Schedule
Establishing a regular maintenance schedule is essential to keep your CNC machine in optimal condition. Here are steps to create a maintenance schedule:Step 1: Manufacturer Guidelines
Consult the manufacturer's documentation and recommendations for maintenance intervals, lubrication types, and specific procedures.Step 2: Daily Maintenance
Implement daily maintenance routines that include tasks like clearing debris, checking for loose fasteners, and inspecting coolant levels. These tasks help prevent minor issues from escalating.Step 3: Weekly or Monthly Maintenance
Schedule more in-depth maintenance tasks on a weekly or monthly basis, depending on your machine's usage. This may involve thorough cleaning, lubrication, and inspections of critical components.Step 4: Quarterly or Semi-Annual Maintenance
Perform more extensive maintenance tasks, such as checking and adjusting alignment, inspecting electrical connections, and replacing worn or damaged parts.Step 5: Annual Maintenance
Annually, consider a comprehensive inspection by a qualified technician or engineer. This should include a full lubrication cycle, calibration checks, and any necessary repairs or replacements.Step 6: Documentation
Maintain detailed records of all maintenance activities, including dates, tasks performed, and any issues identified. This documentation is invaluable for tracking the machine's history and planning future maintenance.Step 7: Training
Ensure that personnel responsible for maintenance are adequately trained and have access to the necessary tools and resources. Regular lubrication and maintenance are essential for maximizing the lifespan and performance of your CNC machine. By following a well-established maintenance schedule and addressing lubrication points, you can prevent premature wear and ensure that your machine continues to produce accurate and high-quality workpieces. In the next chapter, we will discuss safety procedures and guidelines for operating your CNC machine.Chapter 8: Safety Procedures for CNC Machines
Safety is of paramount importance when working with CNC machines. In this chapter, we will explore key safety procedures and guidelines for operating CNC machines, including CNC machine safety, emergency shutdown procedures, and the use of personal protective equipment (PPE).a. CNC Machine Safety
- Training: Ensure that all personnel operating or working around CNC machines have received comprehensive safety training. This should include machine-specific training, safe operating procedures, and hazard recognition.
- Machine Guards: Keep all machine guards and safety interlocks in place and functioning correctly. These safety features are designed to protect operators from moving parts and potential hazards.
- Safety Labels: Ensure that safety labels and warning signs are prominently displayed on the machine. These labels provide essential information about potential hazards and safety precautions.
- Emergency Stop: Familiarize operators with the location and use of the emergency stop button. Make sure it is easily accessible in case of an emergency.
- Clear Workspace: Maintain a clutter-free workspace around the CNC machine. Remove any unnecessary tools, materials, or debris that could pose a tripping hazard or interfere with machine operation.
- Machine Lockout/Tagout (LOTO): Implement lockout/tagout procedures to de-energize and secure the machine before performing maintenance or repairs. Lockout devices prevent accidental machine startup.
- Spindle and Tool Safety: Handle cutting tools and tool changes with care. Ensure that tools are properly secured in toolholders and that tool changes are performed following safe procedures.
- Material Handling: Use appropriate lifting equipment and techniques when handling heavy materials or workpieces. Avoid overloading the machine's weight capacity.
- Fire Safety: Keep fire extinguishers and smoke detectors nearby. Develop and communicate fire safety protocols, including the location of fire exits and evacuation procedures.
b. Emergency Shutdown Procedures
- Emergency Stop Button: In the event of an emergency or when immediate shutdown is required, press the emergency stop button. This button is typically large, red, and easily accessible.
- Stop All Motion: The emergency stop button should halt all machine movements and shut down power to the machine. Ensure that the machine comes to a complete stop.
- Lockout/Tagout: After using the emergency stop button, follow lockout/tagout procedures to secure the machine and prevent accidental restarts.
- Notify Authorities: If an accident or hazardous situation occurs, contact the appropriate authorities, such as maintenance personnel or supervisors, to address the issue and ensure that the machine is safe to operate again.
c. Personal Protective Equipment (PPE)
- Safety Glasses: Operators and personnel in the vicinity of the CNC machine should wear safety glasses with appropriate impact resistance to protect their eyes from flying debris.
- Hearing Protection: In noisy machine shops, hearing protection, such as earplugs or earmuffs, should be worn to prevent hearing damage.
- Gloves: When handling materials or performing maintenance tasks, wear gloves appropriate for the job. Ensure that gloves do not pose a risk near moving machine parts.
- Respiratory Protection: If machining materials generate dust or fumes, use respiratory protection equipment, such as dust masks or respirators, to safeguard against inhalation hazards.
- Safety Shoes: Wear sturdy safety shoes or boots with slip-resistant soles to protect against foot injuries and ensure good traction in the workspace.
- Protective Clothing: Depending on the machining process and materials used, wear appropriate protective clothing, such as aprons or full-body coveralls.
- Safety Helmets: In environments where falling objects are a risk, wear safety helmets or hard hats for head protection.
- Face Shields: For tasks that involve potential face hazards, such as splashing coolant or chips, use face shields in addition to safety glasses.
Chapter 9: Troubleshooting Common Installation Issues
In this chapter, we will explore common problems that may arise during the installation of CNC machines and provide solutions to address these issues. Additionally, we will discuss troubleshooting techniques that can help you identify and resolve problems effectively.a. Common Problems and Solutions
-
Electrical Issues:
- Problem: The CNC machine won't power on.
- Solution: Check the power source, electrical connections, and fuses. Ensure the emergency stop button is released.
-
Mechanical Misalignment:
- Problem: The machine produces inaccurate cuts or workpiece dimensions.
- Solution: Realign and level the machine. Check for loose components or worn guideways and replace as needed.
-
Tool Chatter or Vibration:
- Problem: The machine produces vibrations or tool chatter, affecting surface finish.
- Solution: Check toolholder and spindle collet for proper seating. Adjust cutting parameters and toolpath settings.
-
Communication Errors:
- Problem: The CNC controller cannot communicate with the computer or CAD/CAM software.
- Solution: Verify cable connections, baud rates, and settings on both the machine and computer. Ensure proper software and driver installations.
-
Tool Breakage:
- Problem: Tools frequently break during machining.
- Solution: Check tool alignment, toolholder condition, and spindle runout. Adjust feeds and speeds based on tool material and workpiece.
-
Coolant or Lubrication Problems:
- Problem: Insufficient or uneven coolant/lubrication flow.
- Solution: Check coolant and lubrication system components, such as pumps, hoses, and nozzles. Clean or replace filters and ensure proper fluid levels.
-
Software Errors:
- Problem: The control software displays error messages or unexpected behavior.
- Solution: Review error messages and consult software documentation. Check for compatibility issues and update software or firmware as needed.
b. Troubleshooting Techniques
- Systematic Approach: When troubleshooting issues, adopt a systematic approach by identifying and isolating the problem's source. Begin with the most straightforward checks and progressively investigate more complex causes.
- Documentation: Refer to machine manuals, documentation, and manufacturer-provided resources for troubleshooting guidance and error code interpretations.
- Measurement and Testing: Use measuring instruments like dial indicators, calipers, and micrometers to assess alignment, dimensions, and tool runout. Conduct test cuts to verify machining accuracy.
- Visual Inspection: Conduct a thorough visual inspection of the machine, checking for loose fasteners, damaged components, or visible signs of wear.
- Logs and Records: Review maintenance logs, error logs, and records of past issues to identify recurring problems or patterns.
- Consult Experts: If you encounter complex or persistent issues, consult with experts, such as manufacturer technical support, qualified technicians, or experienced machinists who may have encountered similar problems.
- Safe Troubleshooting: Always ensure safety during troubleshooting. Follow lockout/tagout procedures, power off the machine, and use appropriate personal protective equipment (PPE).
- Documentation: Maintain detailed records of troubleshooting activities, including the steps taken, observations, and the resolutions applied. These records can be valuable for future reference.
- Continuous Learning: Encourage a culture of continuous learning and knowledge sharing among your team. Experience gained from troubleshooting can lead to improved preventive maintenance practices.
Chapter 10: Final Checks and Testing
In this concluding chapter, we will discuss the essential steps of running test programs, ensuring accuracy, and fine-tuning your CNC machine installation to achieve optimal performance.a. Running Test Programs
- Selection of Test Programs: Prepare test programs that encompass a range of machining operations your CNC machine will perform. These programs should include basic movements, tool changes, and various cutting scenarios.
- Tool and Workpiece Setup: Mount the appropriate tools and secure a test workpiece on the machine's worktable or fixture. Ensure that tool offsets and work offsets are correctly programmed.
- Dry Run: Initially, perform a dry run without any cutting. This allows you to check the machine's movements, tool changes, and overall program flow for any errors or unexpected behavior.
- Material Selection: Choose a test material similar to the one you plan to use for your actual machining projects. This ensures that the test results closely mimic real-world conditions.
- Cutting Tests: Execute the test programs with cutting operations. Monitor the machine's performance, paying close attention to toolpath accuracy, spindle speed, and feed rates.
b. Ensuring Accuracy
- Measurement and Inspection: After running the test programs, measure the dimensions and surface finish of the test workpieces using precision measuring instruments. Compare the results to the intended design specifications.
- Tool Inspection: Inspect the cutting tools for signs of wear, such as chipped edges or excessive tool wear. Replace or re-sharpen tools as needed.
- Workpiece Inspection: Examine the test workpiece for any defects, surface finish issues, or deviations from the desired geometry. Address any issues identified during the inspection.
- Feedback and Analysis: Analyze the test results to identify any discrepancies or deviations from the expected outcomes. Determine whether adjustments are required to improve accuracy.
c. Fine-Tuning
- Toolpath Optimization: If test results reveal inaccuracies or surface finish problems, consider optimizing toolpaths in your CAM software. Adjust toolpath parameters, tool selection, and cutting speeds and feeds as needed.
- Machine Parameter Adjustments: Consult the machine's documentation to fine-tune specific parameters, such as acceleration, deceleration, and backlash compensation. These adjustments can enhance accuracy.
- Tool Offset Calibration: Recalibrate tool offsets if necessary. Ensure that the machine accurately compensates for tool length and diameter, reducing errors in machining.
- Work Offset Correction: Check and correct work offsets to ensure that the machine positions the tool precisely relative to the workpiece. Small errors in work offset can lead to significant inaccuracies.
- Re-Testing: After making adjustments and fine-tuning, re-run the test programs to verify the improvements in accuracy and surface finish.
- Documentation: Document all fine-tuning activities, adjustments, and test results for future reference. This documentation will be valuable for maintaining consistency in your machining operations.
Chapter 11: Training and Skill Development
In this chapter, we will emphasize the significance of training and skill development for both machine operators and maintenance personnel. Proper training and skill enhancement are crucial for ensuring safe and efficient CNC machine operation, as well as for effectively maintaining and troubleshooting the equipment.a. Operator Training
- Basic Machine Operation: Operators should receive comprehensive training on the fundamental aspects of CNC machine operation, including machine startup, shutdown, homing, and jogging.
- Understanding G-codes and M-codes: Operators should be proficient in interpreting and modifying G-codes and M-codes, which control the machine's movements and functions.
- Tool Handling: Proper tool handling techniques, including tool changes, tool offsets, and tool calibration, are essential to prevent accidents and ensure machining accuracy.
- Workpiece Setup: Training should cover workpiece setup, including workholding, material loading, and securing workpieces to the machine's worktable or fixture.
- Safety Procedures: Operators must be well-versed in CNC machine safety procedures, emergency shutdown protocols, and the use of personal protective equipment (PPE).
- Troubleshooting Basics: Basic troubleshooting skills, such as identifying common issues and knowing when to seek assistance, can help operators address minor problems promptly.
- Quality Control: Training in quality control and inspection techniques is vital to ensure that finished workpieces meet specified tolerances and surface finish requirements.
- Simulation and Practice: Operators should have opportunities for hands-on practice and simulation exercises to enhance their skills and build confidence in operating the CNC machine.
b. Maintenance Training
- Preventive Maintenance: Maintenance personnel should receive training on the routine preventive maintenance tasks specific to the CNC machine, including lubrication, cleaning, and inspection routines.
- Machine Components: A deep understanding of the machine's components, including motors, sensors, drives, and electrical systems, is necessary for maintenance personnel to diagnose and resolve issues effectively.
- Troubleshooting Techniques: Advanced troubleshooting skills, such as diagnosing electrical, mechanical, and software-related problems, are essential for minimizing downtime and optimizing machine performance.
- Lubrication and Fluid Management: Proper knowledge of lubrication points, fluid types, and filtration systems is critical for maintaining the machine's mechanical integrity.
- Electrical Systems: Maintenance personnel should be trained in electrical systems, including understanding wiring diagrams, electrical safety protocols, and the replacement of electrical components.
- Advanced Calibration: Training on advanced calibration techniques, such as laser alignment and spindle runout measurement, can improve the accuracy of the CNC machine.
- Software Updates: Familiarity with software updates and firmware upgrades is important to keep the control software and machine firmware up to date.
c. Skill Enhancement
- Continued Learning: Encourage a culture of continuous learning among both operators and maintenance personnel. This may include attending workshops, seminars, and online courses related to CNC technology.
- Skill Evaluation: Periodically evaluate the skills and knowledge of operators and maintenance staff to identify areas for improvement and targeted training.
- Cross-Training: Consider cross-training operators in basic maintenance tasks and vice versa. This can enhance overall understanding and collaboration within the team.
- Mentorship: Implement mentorship programs where experienced employees can provide guidance and share their knowledge with less experienced team members.
- Problem-Solving: Encourage employees to actively engage in problem-solving exercises and root cause analysis, fostering a culture of proactive troubleshooting.
- Feedback Loop: Establish a feedback loop where operators and maintenance personnel can communicate issues, share insights, and suggest improvements for machine operation and maintenance.
Conclusion
In this comprehensive guide, we have explored the intricate process of CNC machine installation, covering a wide range of topics to ensure that your CNC machine is assembled, installed, and operated effectively and safely. Let's summarize the key points, emphasize the importance of proper CNC machine installation, and look ahead to the future of CNC technology.a. Summary of Key Points
Throughout this guide, we've covered the following key points:- Understanding CNC Machines: We started by discussing what CNC machines are, the various types available, and their essential components.
- Pre-Installation Preparation: We emphasized the importance of preparing the workspace, meeting power and electrical requirements, and implementing safety measures before installation.
- Assembling the CNC Machine: Detailed steps were provided for unpacking, organizing components, assembling the machine frame, attaching motors and drives, installing the control panel, and managing cables.
- Aligning and Leveling: We discussed the significance of alignment and leveling, the tools required, and the step-by-step process to achieve precise alignment.
- Electrical Wiring: Understanding electrical systems, wiring the CNC machine, and adhering to safety precautions during electrical work were thoroughly covered.
- Installing the Control Software: The installation of control software, calibration, and testing procedures were discussed to ensure the CNC machine operates correctly.
- Lubrication and Maintenance: The importance of lubrication and maintenance for machine longevity and performance was highlighted, including lubrication points and maintenance schedules.
- Safety Procedures: Safety procedures, emergency shutdown protocols, and personal protective equipment (PPE) use were addressed to create a safe working environment.
- Troubleshooting Common Installation Issues: Common problems and troubleshooting techniques were provided to help identify and resolve issues effectively.
- Final Checks and Testing: Running test programs, ensuring accuracy, and fine-tuning the machine were discussed to achieve optimal performance.
- Training and Skill Development: The significance of operator and maintenance personnel training, as well as ongoing skill enhancement, was emphasized.
b. The Importance of Proper CNC Machine Installation
Proper CNC machine installation is the foundation upon which a successful machining operation is built. It is essential for the following reasons:- Accuracy: A well-installed CNC machine is more likely to produce accurate and precise parts, reducing scrap and rework.
- Safety: Installation that adheres to safety standards and procedures ensures the well-being of machine operators and maintenance personnel.
- Longevity: Correct installation and regular maintenance prolong the life of your CNC machine, protecting your investment.
- Efficiency: A properly installed machine operates efficiently, minimizing downtime and maximizing productivity.
- Quality: The quality of the installation directly affects the quality of the machined parts, leading to satisfied customers and improved reputation.
c. Looking Ahead
As technology continues to advance, CNC machines will become even more capable and versatile. It is essential to stay informed about the latest developments, software updates, and best practices in CNC machining. Additionally, as CNC technology becomes more accessible, more industries and businesses can benefit from its advantages. In conclusion, CNC machine installation is a complex but rewarding process. By following the guidelines and best practices outlined in this guide, you can set the stage for a successful CNC machining operation. Remember that continuous learning, training, and ongoing maintenance are key to maintaining and improving the performance of your CNC machines as you look ahead to a future filled with opportunities in the world of precision manufacturing.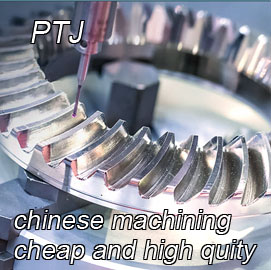
Our Services
- 5 Axis Machining
- Cnc Milling
- Cnc Turning
- Machining Industries
- Machining Process
- Surface Treatment
- Metal Machining
- Plastic Machining
- Powder Metallurgy Mold
- Die Casting
- Parts Gallery
Case Studies
- Auto Metal Parts
- Machinery Parts
- LED Heatsink
- Building Parts
- Mobile Parts
- Medical Parts
- Electronic Parts
- Tailored Machining
- Bicycle Parts
Material List
- Aluminum Machining
- Titanium Machining
- Stainless Steel Machining
- Copper Machining
- Brass Machining
- Super Alloy Machining
- Peek Machining
- UHMW Machining
- Unilate Machining
- PA6 Machining
- PPS Machining
- Teflon Machining
- Inconel Machining
- Tool Steel Machining
- More Material
Parts Gallery