Exploring Swiss Type Lathes: Mechanics, Operations, and Applications
2023-10-23
Swiss Type Lathes, also known as Swiss-style lathes or Swiss screw machines, are highly specialized and precision-engineered machining tools that play a pivotal role in various industries, including aerospace, medical, and automotive. In this comprehensive article, we will delve deep into the world of Swiss Type Lathes, unraveling their intricate mechanics and shedding light on how they work. We'll also explore their applications, advantages, and evolving technology.
Section 1: The Genesis of Swiss Type Lathes
1.1. Historical Roots
The history of Swiss Type Lathes can be traced back to the early 19th century when precision machining began to play a crucial role in the Swiss watchmaking industry. Switzerland, renowned for its horological craftsmanship, needed a means to produce intricate watch components with utmost precision. This demand for precision machining tools laid the foundation for what would eventually become Swiss Type Lathes. During the early 19th century, conventional lathes were used in the Swiss watchmaking industry. However, these lathes were not well-suited for the demanding requirements of watchmaking, which necessitated the machining of small, intricate, and highly precise components. Watchmakers were faced with a challenge: they needed a way to turn and mill small parts with exceptional accuracy. The breakthrough moment came with the invention of the lever escapement mechanism by Swiss watchmaker Breguet in 1795. This invention required extremely precise parts, which prompted the need for more advanced machining techniques. As a response, Swiss watchmakers began experimenting with various lathe designs and modifications to achieve the required precision. The concept of a sliding headstock, which allowed for greater control and precision in machining small workpieces, began to emerge. Swiss watchmakers, such as Patek Philippe and Longines, played pivotal roles in refining these early designs. By the mid-19th century, Swiss watchmaking had already gained international recognition for its precision, and these early adaptations of lathes were central to that success.1.2. Evolution of Swiss Lathe Technology
The evolution of Swiss Lathe technology has been marked by a series of significant technological advancements that have continually pushed the boundaries of precision machining. These advancements have not only shaped the development of Swiss Type Lathes but have also influenced the broader field of precision engineering. Here are some key milestones in the evolution of Swiss Lathe technology: 1.2.1. Birth of the Tornos Screw Machine (1880s):- The 1880s saw the development of the Tornos Screw Machine, a significant milestone in the evolution of Swiss Lathe technology.
- This machine featured automatic threading and was capable of producing complex threaded parts with remarkable precision.
- In the early 20th century, the introduction of the guide bushing was a game-changer in Swiss Lathe technology.
- The guide bushing, positioned close to the cutting tools, provided unparalleled support and stability to long, slender workpieces, enabling precise machining.
- The 1970s brought the integration of Computer Numerical Control (CNC) technology into Swiss Type Lathes.
- CNC controls allowed for precise and programmable machining operations, increasing the versatility of these lathes.
- Advances in tooling and toolholder technology have played a vital role in enhancing the performance of Swiss Type Lathes.
- Carbide tooling, quick-change toolholders, and innovative tool geometries have all contributed to improved swiss cnc machining capabilities.
- In recent decades, guide bushingless Swiss Type Lathes have gained popularity.
- These machines, with their reduced material waste and increased versatility, represent a significant leap in Swiss Lathe technology.
- The ability to achieve extremely high spindle speeds has become a hallmark of modern Swiss Type Lathes.
- High-speed machining allows for faster production and superior surface finishes.
Section 2: Mechanics of Swiss Type Lathes
2.1. Structural Components
Swiss Type Lathes are known for their complex yet highly efficient mechanical structures. Let's take an in-depth look at the main structural components and their roles in the machining process: 2.1.1. Headstock:- The headstock is a critical component situated at the front of the Swiss Type Lathe.
- Purpose: It houses the main spindle, which rotates the workpiece. The spindle is powered by the lathe's motor and provides the rotational motion necessary for machining.
- Function: The headstock ensures high spindle accuracy, concentricity, and rigidity, which are crucial for precision machining.
- The guide bushing is a tube-like component that surrounds the rotating workpiece.
- Purpose: It provides support and stability to the workpiece, reducing vibrations and enabling precise machining.
- Function: The guide bushing holds the workpiece firmly in place while allowing only the required length to extend beyond it, minimizing flex and ensuring accurate machining.
- The main tool holder is positioned close to the guide bushing.
- Purpose: It holds the primary cutting tool used for machining the workpiece.
- Function: The main tool holder provides a stable platform for the cutting tool, ensuring precision in cutting operations.
- Some Swiss Type Lathes are equipped with a sub-spindle located at the back of the machine.
- Purpose: The sub-spindle serves as a secondary spindle that can hold and machine the workpiece from the opposite end.
- Function: It enables the completion of complex parts by allowing machining on both ends of the workpiece in a single setup.
- Swiss Type Lathes may include live tool holders, often located on the machine's gang slide or turret.
- Purpose: Live tool holders allow for secondary machining operations, such as drilling and milling, to be performed on the workpiece without removing it from the machine.
- Function: These tool holders enhance the lathe's versatility and reduce the need for additional machining setups.
- The sliding headstock is a movable assembly that can slide along the lathe's bed.
- Purpose: Its primary function is to enable precise and synchronized machining of long, slender workpieces.
- The sliding headstock ensures exceptional precision by allowing the workpiece to be supported close to the cutting tool.
- Role: This proximity minimizes deflection, vibrations, and errors, resulting in superior part accuracy and surface finish.
- Long and slender workpieces, often challenging to machine on conventional lathes, are efficiently processed using the sliding headstock.
- Function: The sliding headstock facilitates continuous machining without the need for frequent repositioning, reducing cycle times and ensuring part consistency.
- Swiss Type Lathes utilize various types of toolholders, including static and live tool holders.
- Significance: Toolholders secure cutting tools in place and ensure their proper alignment with the workpiece.
- Precision: The rigidity and stability of toolholders are crucial for achieving accurate cuts and maintaining part tolerances.
- Tool geometry, such as rake angles and clearance angles, must be carefully chosen based on the specific machining requirements.
- Importance: Proper tool geometry reduces cutting forces, minimizes tool wear, and enhances surface finish.
- Material Selection: Tool material, such as carbide or high-speed steel, affects tool life and cutting performance, making it a critical consideration.
Section 3: How Swiss Type Lathes Work
3.1. Material Feeding Mechanism
The material feeding mechanism in Swiss Type Lathes is a critical component that allows long, slender workpieces to be efficiently loaded and machined. Here's how it works: Material Loading:- Long, straight bars of raw material, typically made of metals like stainless steel or aluminum, are loaded into the lathe's bar feeder.
- The bar feeder holds and advances the material into the machine.
- As the material enters the machine, it passes through the guide bushing, which is positioned very close to the cutting tools.
- The guide bushing provides essential support and guidance to the material, ensuring that it remains stable and centered during machining.
- The material is advanced through the guide bushing as the machining process progresses, allowing for precise and continuous machining.
- The guide bushing minimizes vibrations and deflection of the material, which is especially critical when machining long and slender workpieces.
- It contributes to the exceptional precision that Swiss Type Lathes are known for.
3.2. Precision Machining
Precision machining on a Swiss Type Lathe involves a series of well-coordinated steps aimed at achieving exceptional accuracy and surface finish: Step 1: Material Preparation- The raw material is loaded into the bar feeder, and its length is adjusted to ensure it extends just beyond the guide bushing.
- The workpiece is rotated by the main spindle while the cutting tools, mounted on toolholders, engage with the material.
- Cutting operations may include turning, threading, grooving, drilling, and milling, depending on the part's design and specifications.
- High spindle speeds are a hallmark of Swiss Type Lathes. They allow for fast material removal rates and superior surface finishes.
- The combination of high spindle speeds and the guide bushing's support minimizes cutting forces and vibrations, enhancing precision.
- Swiss Type Lathes often feature quick tool change systems, which allow for rapid tool swaps during machining.
- Quick tool changes reduce downtime and increase productivity, enabling different operations to be performed in a single setup.
- Swiss Type Lathes excel at performing multiple machining operations simultaneously.
- While the main spindle works on one end of the workpiece, live toolholders can perform secondary operations, such as drilling or milling, on the other end.
- Some Swiss Type Lathes have a sub-spindle, allowing for machining on both ends of the workpiece in a single setup.
- This capability is particularly useful for complex parts that require machining on both ends.
3.3. Swiss Lathe Programming
Swiss Lathe programming involves the use of Computer Numerical Control (CNC) systems to control the lathe's movements and operations. Here are the key aspects of Swiss Lathe programming: CNC Controls:- Swiss Type Lathes are equipped with sophisticated CNC controls that allow operators to program and control the machining process.
- CNC controls provide a user-friendly interface for inputting part specifications and toolpaths.
- The programming process typically involves generating G-codes, which are alphanumeric instructions that dictate the tool's movements and cnc machining operations.
- G-codes are generated based on the part's design and the desired machining operations.
- Turning: G00 (rapid positioning), G01 (linear interpolation), G02/G03 (circular interpolation).
- Threading: G76 (threading cycle).
- Drilling: G81 (drilling cycle).
- Milling: G12/G13 (circular pocket milling).
- C-axis positioning: G01 with C-axis motion.
- Before actual machining begins, operators often run simulations to verify the program's correctness and ensure that the toolpaths are free of collisions.
3.4. Cooling and Chip Management
Cooling and chip management are essential aspects of Swiss Type Lathe operation: Coolant Systems:- Swiss Type Lathes are equipped with coolant systems that deliver cutting fluid to the cutting zone.
- Significance: Coolant serves multiple purposes, including dissipating heat, lubricating the tool, and flushing away chips.
- Proper cooling helps maintain tool and workpiece temperatures, preventing overheating and tool wear.
- As the cutting tools remove material, chips are generated and need to be efficiently managed.
- Chip conveyors or chip augers collect and remove the chips from the machining area.
- Effective chip management is crucial for uninterrupted machining and maintaining a clean work environment.
Section 4: Applications and Industries
Swiss Type Lathes have found widespread applications in various industries due to their unmatched precision and efficiency. Let's explore their critical roles in aerospace manufacturing, medical device production, the automotive sector, and electronics and microtechnology.4.1. Aerospace Manufacturing
The aerospace industry demands components with extremely high precision and reliability. Swiss Type Lathes are invaluable for producing critical aerospace components such as turbine blades, fasteners, and more. Turbine Blades:- Swiss Type Lathes are used to machine turbine blades with complex airfoil profiles.
- These blades are critical for aircraft and power generation turbines, where precision is paramount for optimal performance and efficiency.
- Swiss lathes ensure tight tolerances and superior surface finishes, enhancing turbine performance.
- Aerospace fasteners, including bolts and screws, require precision machining to ensure secure and reliable connections.
- Swiss Type Lathes excel at producing these components with consistency and precision.
- The speed and accuracy of these lathes contribute to efficient production in aerospace fastener manufacturing.
4.2. Medical Device Production
Swiss Type Lathes play a crucial role in the medical industry by manufacturing implants, surgical instruments, dental components, and more. Implants:- Orthopedic and dental implants, such as hip prostheses and dental screws, require precision and biocompatibility.
- Swiss Type Lathes are used to machine these components from materials like titanium and stainless steel to exact specifications.
- The precision of these lathes ensures a perfect fit and long-lasting performance in medical implants.
- Surgical instruments, including scalpels and forceps, must be finely crafted for accuracy and ease of use.
- Swiss Type Lathes are employed to produce these instruments with precision and consistency.
- The quality and reliability of surgical instruments made with Swiss lathes are essential in the medical field.
4.3. Automotive Sector
The automotive industry relies on Swiss Type Lathes for the production of critical components, including fuel injectors, shafts, and connectors. Fuel Injectors:- Fuel injectors are essential automotive components that require high precision for efficient fuel delivery.
- Swiss Type Lathes are used to machine injector parts, ensuring tight tolerances for optimal engine performance and emissions control.
- Precision shafts are used in various automotive systems, including transmissions and drivetrains.
- Swiss Type Lathes are employed to produce these shafts with the accuracy and surface finish necessary for smooth operation.
- Automotive connectors, such as those used in electrical systems, require precise machining for reliable connectivity.
- Swiss Type Lathes are used to manufacture connectors with intricate designs and tight tolerances.
- The automotive industry is undergoing significant changes, including the shift toward electric and autonomous vehicles.
- Swiss Type Lathes are adapting to meet the evolving requirements, such as the machining of components for electric powertrains and advanced sensor systems.
4.4. Electronics and Microtechnology
The electronics and microtechnology sectors benefit from Swiss Type Lathes, especially in the production of intricate electronic connectors and microcomponents. Electronic Connectors:- Swiss Type Lathes excel at machining miniature connectors used in electronics and telecommunications.
- These connectors require precise pin and socket components, which are efficiently produced using Swiss lathes.
- Swiss Type Lathes are indispensable for crafting microcomponents like gears, nozzles, and tiny screws used in various microtechnology applications.
- As the trend toward miniaturization continues, Swiss lathes play a vital role in meeting the demands of smaller, more precise components.
- The demand for smaller and more compact electronic devices continues to grow.
- Swiss Type Lathes are well-suited to produce the tiny, high-precision components required for smartphones, wearables, and other miniaturized technologies.
Section 5: Advantages and Limitations
Swiss Type Lathes offer a range of advantages that make them indispensable in many industries. However, they also come with certain limitations and challenges that need to be considered. Let's explore both aspects in detail:5.1. Advantages of Swiss Type Lathes
5.1.1. High Precision:
Swiss Type Lathes are renowned for their exceptional precision and accuracy. Advantages: Tight tolerances can be consistently achieved, making them ideal for industries like aerospace and medical device manufacturing. Parts produced with Swiss lathes require minimal post-machining or additional finishing operations.5.1.2. Reduced Cycle Times:
These lathes are designed for high-speed machining, resulting in shorter cycle times. Advantages: Increased productivity and faster turnaround times in industries where efficiency is critical, such as automotive and electronics.5.1.3. Exceptional Surface Finishes:
Swiss Type Lathes produce parts with superior surface finishes due to their high spindle speeds and precision. Advantages: Components with excellent surface finishes are crucial in applications like medical devices and electronics, where aesthetics and performance are vital.5.1.4. Simultaneous Operations:
Swiss lathes can perform multiple machining operations simultaneously, reducing setup times. Advantages: Enhanced efficiency and cost-effectiveness, particularly in industries like aerospace and automotive, where complex parts require various operations.5.1.5. Long and Slender Workpieces:
These lathes are uniquely suited for machining long and slender workpieces. Advantages: Ideal for industries like aerospace, where components like turbine blades demand precision and stability during machining.5.1.6. Versatility:
Swiss Type Lathes can handle a wide range of materials, from metals to plastics. Advantages: Versatility in material selection is vital in industries like medical device manufacturing and electronics, which often require specialized materials.5.1.7. Efficient Chip Management:
Swiss lathes are equipped with effective chip management systems. Advantages: Uninterrupted machining and reduced downtime due to efficient chip removal. Impact on Various Industries:- Aerospace: Swiss lathes ensure precise machining of critical components, enhancing safety and performance.
- Medical Devices: High precision and biocompatible materials make Swiss lathes invaluable for manufacturing medical implants and instruments.
- Automotive: Shorter cycle times and precise machining contribute to improved vehicle performance and reduced costs.
- Electronics and Microtechnology: Swiss lathes enable the production of intricate components for miniaturized electronic devices, meeting the demands of modern technology.
5.2. Limitations and Challenges
5.2.1. Complexity: Swiss Type Lathes are complex machines that require skilled operators and programmers. Limitations: Initial setup and programming can be time-consuming and require specialized knowledge and training. 5.2.2. Cost: Swiss lathes are a significant investment, and their initial purchase cost can be high. Limitations: Smaller businesses may find the initial cost prohibitive, although the efficiency gains often justify the investment. 5.2.3. Limited Workpiece Size: Swiss lathes are optimized for machining long and slender workpieces. Limitations: They may not be suitable for larger or bulkier components, limiting their application in some industries. 5.2.4. Material Selection: While Swiss lathes can handle various materials, they may not be the best choice for extremely hard or exotic materials. Limitations: Some industries requiring specialized materials may need to explore alternative machining methods. 5.2.5. Setup Time for Small Runs: Swiss lathes excel in high-volume production but may have longer setup times for small production runs. Limitations: For small-batch production, the setup time may offset the advantages of high-speed machining. 5.2.6. Tool Wear: Swiss lathes use high spindle speeds, which can lead to increased tool wear. Limitations:Frequent tool changes and maintenance may be necessary, affecting overall efficiency. In conclusion, Swiss Type Lathes offer remarkable advantages, including precision, speed, and versatility, making them invaluable in various industries. However, they are not without their limitations and challenges, such as complexity and cost. It's essential to carefully consider these factors when determining the suitability of Swiss lathes for specific manufacturing needs.Section 6: Emerging Technologies
Swiss Type Lathes are not immune to the technological advancements of Industry 4.0 and materials/tooling innovations. Let's delve into how these lathes are adapting to the evolving landscape:6.1. Industry 4.0 Integration
Swiss Type Lathes are increasingly incorporating Industry 4.0 principles, leveraging automation, data analytics, and connectivity to enhance their capabilities: 6.1.1. Automation:- Integration with robotic systems allows for lights-out machining, where Swiss lathes can operate autonomously 24/7.
- Advantages: Increased production efficiency, reduced labor costs, and enhanced machine utilization.
- Swiss Type Lathes are equipped with sensors and data collection mechanisms.
- Benefits: Real-time monitoring of machine performance and production data, allowing for data-driven decision-making and process optimization.
- Predictive Maintenance: Data analytics enable the prediction of maintenance needs based on machine condition, reducing unplanned downtime.
- Swiss lathes can be connected to Manufacturing Execution Systems (MES) or the Industrial Internet of Things (IIoT).
- Advantages: Seamless communication between machines and systems for production planning, inventory management, and quality control.
- Remote Monitoring: Operators can monitor machine performance and receive alerts remotely, improving responsiveness.
- Digital twin technology creates virtual replicas of Swiss Type Lathes.
- Benefits: Digital twins allow for advanced simulations and optimization, reducing setup times and minimizing errors.
- Modern Swiss lathes feature user-friendly interfaces and touchscreens for intuitive programming and monitoring.
- Advantages: Improved ease of use and reduced training times for operators.
6.2. Materials and Tooling Innovations
Advancements in materials and tooling are expanding the capabilities of Swiss Type Lathes, enabling them to work with a broader range of materials and achieve higher precision: 6.2.1. Advanced Materials:- Swiss Type Lathes are now capable of machining advanced materials like composites, superalloys, and ceramics.
- Benefits: Expanded application areas, particularly in aerospace and high-tech industries where these materials are prevalent.
- Challenges: Machining advanced materials may require specialized tooling and techniques due to their unique properties.
- Tool coatings like diamond-like carbon (DLC) and titanium nitride (TiN) improve tool life and cutting performance.
- Advantages: Reduced tool wear, enhanced surface finish, and longer intervals between tool changes.
- Swiss lathes are equipped with miniaturized tools for machining tiny, intricate components.
- Benefits: Enhanced precision for microtechnology and electronics applications.
- Advanced CAM software enables optimal toolpath generation for complex parts.
- Advantages: Reduced cycle times, improved surface finish, and minimized tool wear.
- Adaptive machining uses real-time data to adjust cutting parameters, optimizing the machining process.
- Benefits: Improved efficiency, reduced energy consumption, and prolonged tool life.
Section 7: Conclusion
7.1. Recap of Key Points
In this comprehensive exploration of Swiss Type Lathes, we've covered a wide range of topics, including their historical origins, mechanics, operations, applications, advantages, limitations, and their integration with emerging technologies. Here are the key takeaways:- Historical Roots: Swiss Type Lathes have their origins in the precision demands of the 19th-century Swiss watchmaking industry, evolving to meet the requirements of various high-precision manufacturing sectors.
- Mechanics: These lathes are characterized by structural components like the headstock, guide bushing, and toolholders, with a sliding headstock mechanism for precise and efficient machining.
- Operations: Swiss Type Lathes excel in material feeding, precision machining, programming, cooling, and chip management, making them ideal for industries demanding high precision and efficiency.
- Applications: Swiss Type Lathes play crucial roles in aerospace, medical device manufacturing, the automotive sector, and electronics and microtechnology, producing critical components for these industries.
- Advantages: They offer high precision, reduced cycle times, exceptional surface finishes, simultaneous operations, and efficient chip management, positively impacting various industries.
- Limitations and Challenges: Swiss Type Lathes come with challenges such as complexity, cost, limited workpiece size, and tool wear. Careful consideration is necessary when choosing them for specific applications.
- Emerging Technologies: Swiss Type Lathes are embracing Industry 4.0 integration, incorporating automation, data analytics, and connectivity. Materials and tooling innovations are expanding their capabilities, enabling machining of advanced materials and achieving higher precision.
7.2. Future Outlook
The future of Swiss Type Lathes looks promising, driven by ongoing technological advancements and evolving industry needs:- Industry 4.0: The integration of Industry 4.0 technologies will continue to enhance Swiss Type Lathes' efficiency, productivity, and responsiveness, making them even more vital in modern manufacturing.
- Materials Advancements: As industries demand new materials with unique properties, Swiss lathes will adapt to machine these materials efficiently, expanding their application areas.
- Tooling Innovations: Tooling will continue to evolve with coatings, miniaturization, adaptive machining, and improved toolpath optimization, further enhancing precision and efficiency.
- Miniaturization Trend: As industries push toward miniaturization, Swiss Type Lathes will play a pivotal role in crafting intricate components for electronics, medical devices, and microtechnology.
- Sustainability: The emphasis on sustainability in manufacturing will drive Swiss lathes to adopt eco-friendly practices and reduce energy consumption.
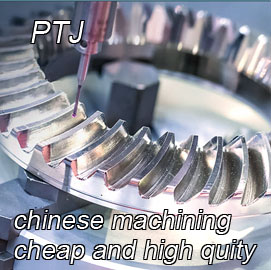
Our Services
- 5 Axis Machining
- Cnc Milling
- Cnc Turning
- Machining Industries
- Machining Process
- Surface Treatment
- Metal Machining
- Plastic Machining
- Powder Metallurgy Mold
- Die Casting
- Parts Gallery
Case Studies
- Auto Metal Parts
- Machinery Parts
- LED Heatsink
- Building Parts
- Mobile Parts
- Medical Parts
- Electronic Parts
- Tailored Machining
- Bicycle Parts
Material List
- Aluminum Machining
- Titanium Machining
- Stainless Steel Machining
- Copper Machining
- Brass Machining
- Super Alloy Machining
- Peek Machining
- UHMW Machining
- Unilate Machining
- PA6 Machining
- PPS Machining
- Teflon Machining
- Inconel Machining
- Tool Steel Machining
- More Material
Parts Gallery