Selection requirements of cutting fluid in CNC machine tool processing
With the development of industrialization, the metal processing industry is also developing rapidly, and various new materials and new process innovations are constantly emerging. However, the processing quality and processing efficiency of the products are guaranteed and improved. When choosing the right metal cutting fluid, Land reduction of environmental pollution has become an important link. However, the choice of metal cutting fluids for different machining tools is also a difficult problem to choose.
1. Common cutting fluid types for CNC machine tools
In order to adapt to different processing occasions and process requirements, the types of metal cutting fluids are also diverse, which are mainly divided into two categories according to chemical composition and state, namely water-based cutting fluid and oil-based cutting fluid.
1. Water-based cutting fluid refers to the cutting fluid that needs to be diluted with water in advance. Anti-rust emulsions, anti-rust lubricant emulsions, extreme pressure emulsions and microemulsions all belong to this category. The role of water-based cutting fluid is usually mainly cooling and cleaning, and the effect of lubrication is not obvious.
2. Oil-based cutting fluid refers to a cutting fluid that does not need to be diluted with water when used. Pure mineral oil, fatty oil, oily additives, mineral oil, inactive extreme pressure cutting oil and active extreme pressure cutting oil all belong to this type. Contrary to water-based cutting fluids, oil-based cutting fluids have obvious lubrication effects, but have poor cooling and cleaning capabilities.
2, the choice of cutting fluid for different machining tools
Different processing tools, due to their different tool performance, the material characteristics suitable for processing are also different, so it is suitable to use different types of cutting fluids
1. For tools made of high-speed steel materials, during medium and low-speed cutting, the heat is not large, so it is suitable to use oil-based cutting fluid or emulsion. In high-speed cutting, the use of water-based cutting fluid can achieve a good cooling effect due to the large heat generation. At this time, if an oil-based cutting fluid is used, a large amount of oil mist will be generated, which will pollute the environment and easily cause burns to the workpiece, which will affect the processing quality and the service life of the tool. In addition, it is best to use extreme pressure aqueous solutions or extreme pressure emulsions during rough machining, and extreme pressure emulsions or extreme pressure cutting oils are more suitable for finishing.
High-speed steel uses medium-speed cutting operations, and its speed is about 70m/m. High-speed steel is an iron alloy containing elements such as tungsten and chromium to increase its hardness and wear resistance; even so, their hardness and wear resistance quality are reduced to an unacceptable level due to temperatures above 600°C. However, water-soluble cutting oil can be used to keep its operating temperature below 600°C.
2. For cemented carbide tools, since they are more sensitive to sudden heat, the tools should be heated and cooled evenly as much as possible, otherwise it is easy to cause chipping. Therefore, oil-based cutting fluids with relatively mild thermal conductivity are usually used, and an appropriate amount of anti-wear additives are added. When cutting at high speed, spray the tool with a large flow of cutting fluid to avoid uneven heating. And this method can effectively reduce the temperature and reduce the appearance of oil mist.
3. Cast alloys (chromium cobalt tungsten) These alloys are non-ferrous elements based on cobalt. When its temperature is higher than 600℃, it is harder and has better wear resistance than high-speed steel. This can be used for high-speed cutting, and can also be used for difficult-to-cut alloys and cutting operations that generate high temperatures. Cast alloys are very sensitive to large temperature changes, such as sudden interruptions in cutting operations. They are more suitable for continuous cutting operations and can use water-soluble cutting oil.
4. Since ceramic tools and diamond tools have more outstanding high temperature wear resistance than cemented carbide, they often use dry cutting processing techniques. Sometimes, in order to avoid excessively high temperature, water-based cutting fluid with higher thermal conductivity is also used to continuously and fully pour the cutting area.
5. Carbides are widely used in the metal processing industry. They are usually called cemented carbides or super-hard alloys. They are made by adding carbide powder of tungsten, titanium, niobium, and tantalum to a cobalt mold and sintering at high temperature. Changing the ratio and type of metal carbides can produce different types of cemented carbides. Cemented carbide is used because it still retains hardness and wear resistance at a high temperature of 1000°C. They are usually used as inserts or replaceable cutting heads. Each head has a different shape and angle. It can be reinstalled and stored according to different needs. Another simple manufacturing method is to cover a layer of carbide on the cutting tool head. Its manufacturing method is to cover the traditional carbide tool by evaporation of titanium carbide. The cutter head made by this method has high abrasion resistance, and the cutter itself is not easy to break. Carbide tools are often used together with water-soluble cutting oil, but they must be selected carefully. Certain additives will corrode the metal covering the cobalt.
6. The main component of ceramic/diamond ceramic cutting tools is alumina, which can maintain their hardness and wear resistance at high temperatures. However, as mentioned above, the harder the material, the more fragile it is, which makes ceramic tools unsuitable for discontinuous cutting or shock loads and temperature changes. When machining, you can use non-water-soluble cutting oil (oil-based cutting oil) or not use cutting oil at all, avoid using water-soluble cutting oil.
7. The hardest cutting tool is diamond, but it is also fragile. Diamonds can be used in high-content aluminum processing operations, this alloy contains hard silicon particles, will quickly wear carbide tools. It is also suitable for the grinding and processing of non-ferrous materials, such as stone and cement. Diamond can be oxidized at high temperature, so it is not suitable for alloys that are difficult to process. Because it is extremely hard, it is often used for grinding. Oil-based cutting oil or water-soluble cutting oil or synthetic cutting fluid can be used.
Link to this article: Selection requirements of cutting fluid in CNC machine tool processing
Reprint Statement: If there are no special instructions, all articles on this site are original. Please indicate the source for reprinting:https://www.cncmachiningptj.com
PTJ® is a customized manufacturer that provides a full range of copper bars, brass parts and copper parts. Common manufacturing processes include blanking, embossing, coppersmithing, wire edm services, etching, forming and bending, upsetting, hot forging and pressing, perforating and punching, thread rolling and knurling, shearing, multi spindle machining, extrusion and metal forging and stamping. Applications include bus bars, electrical conductors, coaxial cables, waveguides, transistor components, microwave tubes, blank mold tubes, and powder metallurgy extrusion tanks.
Tell us a little about your project’s budget and expected delivery time. We will strategize with you to provide the most cost-effective services to help you reach your target,You are welcome to contact us directly ( sales@pintejin.com ) .
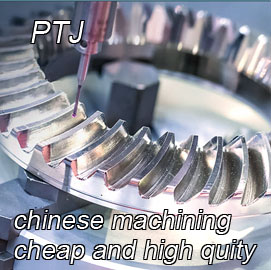
- 5 Axis Machining
- Cnc Milling
- Cnc Turning
- Machining Industries
- Machining Process
- Surface Treatment
- Metal Machining
- Plastic Machining
- Powder Metallurgy Mold
- Die Casting
- Parts Gallery
- Auto Metal Parts
- Machinery Parts
- LED Heatsink
- Building Parts
- Mobile Parts
- Medical Parts
- Electronic Parts
- Tailored Machining
- Bicycle Parts
- Aluminum Machining
- Titanium Machining
- Stainless Steel Machining
- Copper Machining
- Brass Machining
- Super Alloy Machining
- Peek Machining
- UHMW Machining
- Unilate Machining
- PA6 Machining
- PPS Machining
- Teflon Machining
- Inconel Machining
- Tool Steel Machining
- More Material