Current situation and development trend of mold heat treatment technology
Mold heat treatment is an important process to ensure mold performance, and has a direct impact on mold manufacturing accuracy, mold strength, mold working life, mold manufacturing cost, etc. Since the 1980s, the rapid development of international mold heat treatment technology has been vacuum heat treatment technology, mold surface strengthening technology and mold material pre-hardening technology.
Mold vacuum heat treatment technology
Vacuum heat treatment technology is a new type of heat treatment technology developed in recent years. It has the characteristics that are urgently needed in mold manufacturing, such as preventing heating and oxidation and non-decarburization, vacuum degassing or degassing, and eliminating Hydrogen embrittlement improves the plasticity, toughness and fatigue strength of materials (parts). The slow vacuum heating and the small temperature difference between the inside and outside of the parts determine the small deformation of the parts caused by the vacuum heat treatment process.
The main applications in the vacuum heat treatment of molds are vacuum oil quenching, vacuum quenching and vacuum tempering. In order to maintain the excellent characteristics of the vacuum heating of the workpiece (such as the mold), the selection and formulation of the coolant and the cooling process are very important. The mold quenching process mainly uses oil cooling and air cooling. For mold working surfaces that are no longer machined after heat treatment, vacuum tempering should be used as much as possible after quenching, especially vacuum-quenched workpieces (molds), which can improve the mechanical properties related to surface quality, such as fatigue performance, surface brightness, Corrosion resistance, etc.
The successful development and application of computer simulation technology of the heat treatment process makes the intelligent heat treatment of the mold possible. Due to the small batch (even single piece), multi-variety characteristics of mold production, and the high requirements for heat treatment performance and the characteristics of not allowing waste products, intelligent heat treatment of molds becomes a must. Foreign industrialized countries, such as the United States, Japan, etc., have also developed rapidly in terms of vacuum and high-pressure gas quenching, mainly targeting molds.
Mold surface treatment technology
In addition to the reasonable coordination of the matrix with sufficiently high strength and toughness, the surface properties of the mold are very important to the working performance and service life of the mold. The surface treatment technology of the mold is a systematic engineering of changing the morphology, chemical composition, structure and stress state of the mold surface through surface coating, surface modification or composite treatment technology to obtain the required surface properties. At present, nitriding, carburizing and hardened film deposition are mainly used in mold manufacturing.
Because the nitriding technology can form a surface with excellent performance, and the nitriding process and the quenching process of the die steel have good coordination, at the same time, the nitriding temperature is low, and there is no need for intense cooling after nitriding, and the deformation of the mold is extremely small. Surface strengthening is the earlier nitriding technology, and it is also the most widely used.
Mold carburizing is to improve the overall strength and toughness of the mold, that is, the working surface of the mold has high strength and wear resistance. Hardened film deposition technology is currently more mature CVD, PVD. Molds have been coated with hardened film technology since the 1980s. Under the current technical conditions, the cost of hardened film deposition technology (mainly equipment) is relatively high, and it is still only applied to some precision and long-life molds. If a heat treatment center is established, the cost of coating hardened film will be greatly reduced. , If more molds adopt this technology, the overall level of mold manufacturing in our country can be improved.
Pre-hardening technology of mold materials
Since the 1970s, the idea of pre-hardening has been proposed internationally. However, due to the constraints of the rigidity of the processing machine tool and the cutting tool, the hardness of the pre-hardening cannot reach the hardness of the mold, so the R&D investment in pre-hardening technology is not large. With the improvement of the performance of processing machine tools and cutting tools, the development of pre-hardening technology for mold materials has accelerated. By the 1980s, the proportion of internationally industrialized countries that used pre-hardened modules on plastic mold materials had reached 30% (currently Above 60%).
The pre-hardening technology of mold materials in my country has a late start and small scale, and currently it cannot meet the requirements of domestic mold manufacturing. The use of pre-hardened mold materials can simplify the mold manufacturing process, shorten the mold manufacturing cycle, and improve the manufacturing accuracy of the mold. It is foreseeable that with the advancement of processing technology, pre-hardened mold materials will be used in more mold types.
Link to this article: Current situation and development trend of mold heat treatment technology
Reprint Statement: If there are no special instructions, all articles on this site are original. Please indicate the source for reprinting:https://www.cncmachiningptj.com
PTJ® is a customized manufacturer that provides a full range of copper bars, brass parts and copper parts. Common manufacturing processes include blanking, embossing, coppersmithing, wire edm services, etching, forming and bending, upsetting, hot forging and pressing, perforating and punching, thread rolling and knurling, shearing, multi spindle machining, extrusion and metal forging and stamping. Applications include bus bars, electrical conductors, coaxial cables, waveguides, transistor components, microwave tubes, blank mold tubes, and powder metallurgy extrusion tanks.
Tell us a little about your project’s budget and expected delivery time. We will strategize with you to provide the most cost-effective services to help you reach your target,You are welcome to contact us directly ( sales@pintejin.com ) .
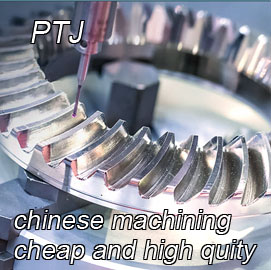
- 5 Axis Machining
- Cnc Milling
- Cnc Turning
- Machining Industries
- Machining Process
- Surface Treatment
- Metal Machining
- Plastic Machining
- Powder Metallurgy Mold
- Die Casting
- Parts Gallery
- Auto Metal Parts
- Machinery Parts
- LED Heatsink
- Building Parts
- Mobile Parts
- Medical Parts
- Electronic Parts
- Tailored Machining
- Bicycle Parts
- Aluminum Machining
- Titanium Machining
- Stainless Steel Machining
- Copper Machining
- Brass Machining
- Super Alloy Machining
- Peek Machining
- UHMW Machining
- Unilate Machining
- PA6 Machining
- PPS Machining
- Teflon Machining
- Inconel Machining
- Tool Steel Machining
- More Material