Analysis on the new development trend of heat treatment technology for automobile fasteners
1. The effect of heat treatment process on improving the fatigue strength of bolts
For a long time, automotive fasteners have been dominated by the basic characteristics of a wide range of varieties, types, and specifications. Its selection and use involve structural analysis, connection design, failure and fatigue analysis, corrosion requirements and assembly methods, and related These factors determine the final quality and reliability of automotive products to a large extent.
The fatigue life of automotive high-strength bolts has always been an important issue. Data shows that most of the failure of bolts is caused by fatigue failure, and there is almost no sign of fatigue failure of the bolt. Therefore, major accidents are likely to occur when fatigue failure occurs. Heat treatment can optimize the properties of fastener materials and increase their fatigue strength. In view of the increasing use requirements of high-strength bolts, it is more important to improve the fatigue strength of bolt materials through heat treatment.
1. The initiation of fatigue cracks in materials
The place where the fatigue crack first starts is called the fatigue source. The fatigue source is very sensitive to the microstructure of the bolt, and can initiate fatigue cracks at a very small scale, generally within 3 to 5 grain sizes. The surface quality of the bolt is the main problem. The source of fatigue, most of the fatigue starts from the bolt surface or subsurface. A large number of dislocations, some alloying elements or impurities in the crystal of bolt material, and the difference in grain boundary strength may all lead to fatigue crack initiation. Studies have shown that fatigue cracks are prone to occur in the following locations: grain boundaries, surface inclusions or second-phase particles, and cavities. These locations are all related to the complex and changeable microstructure of the material. If the microstructure can be improved after heat treatment, the fatigue strength of the bolt material can be improved to a certain extent.
2. The effect of decarburization on fatigue strength
Decarburization of the bolt surface will reduce the surface hardness and wear resistance of the bolt after quenching, and significantly reduce the fatigue strength of the bolt. There is a decarburization test for bolt performance in the GB/T3098.1 standard, and the maximum decarburization depth is specified. When analyzing the reasons for the failure of the 35CrMo hub bolts, it was found that there was a decarburized layer at the junction of the thread and the rod. Fe3C can react with O2, H2O, and H2 at high temperatures to reduce Fe3C in the bolt material, thereby increasing the ferrite phase of the bolt material, reducing the strength of the bolt material, and easily causing micro-cracks. In the heat treatment process, the heating temperature must be controlled well, and at the same time, the controllable atmosphere protection heating must be used to solve this problem.
3. The effect of heat treatment on fatigue strength
The stress concentration on the surface of the bolt will reduce its surface strength. When subjected to alternating dynamic loads, the process of micro-deformation and recovery will continue to occur at the stress concentration part of the notch, and the stress it receives is much greater than the part without stress concentration, so it is easy to Lead to the generation of fatigue cracks.
Fasteners are heat-treated and tempered to improve the microstructure, and have excellent comprehensive mechanical properties, which can improve the fatigue strength of the bolt material, reasonably control the grain size to ensure low-temperature impact energy, and also obtain higher impact toughness. Reasonable heat treatment to refine grains and shorten the distance between grain boundaries can prevent fatigue cracks. If there are a certain amount of whiskers or second particles in the material, these added phases can prevent resident slip to a certain extent. The slip of the belt prevents the initiation and expansion of microcracks.
2. Quenching medium and processing medium for heat treatment
Automotive high-strength fasteners have a series of technical features: high-precision grade; severe service conditions, it will withstand the influence of severe cold and extreme temperature difference all year round along with the host, and withstand the erosion of high and low temperatures; static load, dynamic load, overload, Heavy load and environmental media corrosion, in addition to the effect of the axial pre-tightening tensile load, it will also be subjected to additional tensile alternating loads, transverse shear alternating loads or combined bending loads during work Sometimes it is also subject to impact loads; additional transverse alternating loads can cause bolts to loosen, axial alternating loads can cause fatigue fracture of bolts, and axial tensile loads can cause delayed fracture of bolts, as well as high temperature conditions. Creep of bolts, etc.
A large number of failed bolts indicated that they were broken along the transition between the bolt head and the shaft during service; they were pulled off along the junction of the thread of the bolt shaft and the shaft; and there were sliding buckles along the threaded part. Metallographic analysis: There are more undissolved ferrite on the surface and core of the bolt, and insufficient austenitization during quenching, insufficient matrix strength and stress concentration are one of the important reasons for the failure. For this reason, it is a very important link to ensure the bolt cross-section hardening and the uniformity of the structure.
The function of the quenching oil is to quickly take away the heat of the red-hot metal bolts and reduce them to the martensite transformation temperature to obtain a high-hardness martensite structure and the depth of the hardened layer. At the same time, it must also take into account the reduction of bolt deformation and prevention Cracked. Therefore, the basic characteristic of quenching oil is the "cooling characteristic", which is characterized by a faster cooling rate in the high temperature stage, and a slower cooling rate in the low temperature stage. This characteristic is very suitable for the quenching requirements of alloy structural steel ≥ 10.9 high-strength bolts.
The rapid quenching oil produces thermal decomposition, oxidation and polymerization reactions during use, which leads to changes in cooling characteristics. The trace moisture in the oil will seriously affect the cooling performance of the oil, resulting in a decrease in brightness and uneven hardness of the fasteners after quenching. Produce soft spots or even cracking tendency. Studies have shown that the deformation problems caused by oil quenching are partly caused by water in the oil. In addition, the water content in the oil also accelerates the emulsification and deterioration of the oil and promotes the failure of additives in the oil. When the water content in the oil is greater than or equal to 0.1%, when the oil is heated, the water collected at the bottom of the oil tank may suddenly expand in volume, which may cause the oil to overflow the quenching tank and cause a fire.
For the rapid quenching oil used in the continuous mesh belt furnace, based on the quenching characteristics data accumulated in the 3-month interval test, it is possible to establish the stability and quenching characteristics of the oil, determine the appropriate service life of the quenching oil, and predict the performance of the quenching oil. Change related problems, thereby reducing rework or waste loss caused by changes in quenching oil properties, making it a conventional control method for production. The depth of hardening directly affects the quality of the bolt after heat treatment. When the hardenability of the material is poor, the cooling rate of the cooling medium is slow, and the bolt size is large, the bolt core cannot be all quenched into martensite during quenching. The organization reduces the strength level of the heart area, especially the yield strength. This is obviously very disadvantageous for bolts that bear uniformly distributed tensile stress along the entire cross-section. Insufficient hardenability reduces the strength. Metallographic examination found that there are proeutectoid ferrite and reticulated ferrite structures in the core, indicating that the bolt hardenability needs to be strengthened. As we all know, there are two ways to increase the hardenability to increase the quenching temperature; increase the hardenability of the quenching medium, which can effectively increase the hardening depth of the bolt.
Houghto-Quench has specially developed rapid quenching oil based on the original medium-speed quenching oil, Houghto-Quench G. Houghto-Quench K2000 has further improved its hardening ability, and is especially suitable for use in the quenching and cooling of fasteners. Satisfactory depth of hardening.
The vapor film stage of rapid quenching oil is short, that is, the high temperature stage of the oil cools quickly. This feature is conducive to obtaining a deeper hardened layer for 10B33 and 45 steel ≤ M20 bolts and M42 nuts, while for SWRCH35K and 10B28 steels, it is reduced Only when the thickness is less than or equal to M12 bolts and M30 nuts can the hardness of the core and the surface hardness have a small difference. From the analysis of the cooling rate distribution, in addition to the rapid cooling required in the middle and high temperature stages, the low-temperature cooling rate of the oil has a greater effect on the depth of the hardened layer. The higher the low-temperature cooling rate, the deeper the hardened layer. This is very advantageous for the high-strength fasteners to bear the load uniformly across the entire section, and it is required to obtain about 90% of the martensite structure before tempering in the quenched state. The assessment indicators include nearly 20 indicators such as flash point, viscosity, acid value, oxidation resistance, residual carbon, ash, sludge, quenching cooling rate, and quenching brightness.
For larger size bolts, PAG quenching agent is the main solution, which meets the quenching requirements of most products. PAG quenching agent is in the boiling stage in the martensite transformation zone, and the cooling rate is high and there is a greater risk. It can be adjusted by concentration. The cooling rate at the key index is about 300℃. The lower the cooling rate at this temperature point, the stronger the ability to prevent quenching cracks and the more suitable steel grades. The stability of convection cooling rate during use is the most important factor to ensure the quality of quenching.
In the samples of the early failure bolts, it can be seen that there are crack defects on the threads of the broken bolts near the fracture. The main reason is that the bolts are improperly rolled. Caused by folding; micro-cracks of different depths can also be seen in the bottom of the thread, and the machining built-up tumor forms a stress concentration area. The standard GB/T5770.3-2000 "Special Requirements for Bolts, Screws and Studs with Surface Defects on Fasteners" stipulates that the folds that are not more than a quarter of the thread profile height above the pitch diameter of the bolts under stress are allowed The folding and built-up of the thread bottom are not allowed defects, and folding is one of the main reasons for bolt fracture. The use of Houghton's extreme pressure lubricant for bolt thread processing can effectively prevent built-up edge and reduce stress concentration, thereby helping to improve the fatigue life of the bolt.
3. Surface protection and technology development of automotive fasteners
Fasteners on automobiles, especially fastening bolts, pipe clamps, elastic clamps, etc., are in extremely harsh environments during use, and they are usually corroded seriously, and even difficult to disassemble due to rust. Therefore, fasteners must have good anti-corrosion properties. The most common methods currently used are electro-galvanizing, zinc-nickel alloy, phosphating, blackening and dacromet treatments on the surface. Due to the restriction on the content of hexavalent chromium in the surface coating of automotive fasteners, it does not meet the standards of environmental protection directives, and products containing harmful substances are not allowed to enter the market, which puts an unprecedented high in the innovative ability of automotive fastener surface treatment Standard environmental requirements.
1. Water-based zinc-aluminum coating Geomet
Environmentally-friendly new coating technology-flake zinc-aluminum coating Geomet, Enoufu Group has developed a complete technology based on more than 30 years of DACROMET surface anti-rust technology experience and after years of research and development. The new technology of chromium surface treatment --- GEOMET.
Anti-rust mechanism, the structure of the film treated by Gummet is also the same as the film treated by Dacromet. The metal sheets are overlapped in layers to form a film combined with a silicon-based adhesive to cover the substrate.
Advantages of Geomet: Conductivity, high-strength metal sheet makes Geomet's bolts conductive. Paint adaptability, Geomet can be used as a primer for most paints including electroplating. Environmental protection, water-based solution, does not contain chromium, and no waste water is produced, and no harmful substances are discharged into the air. Excellent corrosion resistance, only 6-8μm film thickness, can reach salt spray test more than 1000h. Heat resistance, inorganic film, and the film does not contain moisture. Hydrogen-free embrittlement process, acid-free and electrolytic coating process, avoid hydrogen embrittlement like ordinary electroplating process.
The stability of the friction coefficient is very important for the assembly of automotive fasteners. The water-based flaky zinc-aluminum coating is a solution to the coefficient of friction. On the basis of the zinc-aluminum coating, a water-based inorganic surface coating with lubricating function ---PLUS is applied.
2. Electrophoretic coating technology
In recent years, some fasteners of some automobile companies have used electrophoretic coating instead of passivation after electroplating. In simple terms, the principle of electrophoretic coating is "opposite sex attracts each other", which is like a magnet. Anode electrophoresis is coated with bolts on the anode and the paint is negatively charged; while cathodic electrophoresis is coated with bolts on the cathode, the paint is positively charged. As we all know, electrophoretic coating is highly mechanized, environmentally friendly, and the paint film has excellent corrosion resistance. Recycle and reuse water resources to reduce emissions; strengthen the recovery of heavy metals to reduce emissions; reduce VOC (volatile organic compounds) emissions; reduce energy consumption (water, electricity, fuel, etc.), and meet environmental protection requirements to reduce costs and improve quality.
It has been applied to auto parts and fasteners for several years. The electrophoretic coating process is relatively mature. It is a product that replaces electroplating. PPGElect ropolyseal fastener special electrophoretic coating material, EPll/SST 120~200h anode electrophoresis, EPlll/SST 200~300h cathodic electrophoresis, EPlV/SST 500~1000h cathodic electrophoresis, EP V/SST 1000~1500h cathodic electrophoresis; and ZiNC Rich coating zinc-rich organic coating (conductive).
With the development of technology, in addition to cathodic electrophoretic coating with excellent corrosion resistance, anodic electrophoretic coating with certain weather resistance and cathodic electrophoretic coating with edge corrosion resistance have also been practically applied on the production line. At present, PPG's electrophoretic coating series have been approved by many automobile manufacturing companies, and a series of specifications have been changed to a unified standard, S424 is changed to S451, such as Ford WSS-M21P41-A2, S451; General Motors GM6047 code G; Chrysler PS-7902 Mcthod C.
The advantages of electrophoretic coating are conducive to environmental protection. Electrophoretic coating adopts water-based paint, and passivation adopts trivalent chromium; improve the corrosion resistance of the product, excellent adhesion; no plug hole, no screw thread, uniform film thickness, consistent torque value; traditional electroplating + passivation Process, the salt spray test reaches about 144h. After adopting zinc phosphating + zinc-rich primer + cathodic electrophoretic coating process, the salt spray test can reach more than 1000h, if electroplating + cathodic electrophoretic coating process is adopted, the salt spray test can reach more than 500h
4, the conclusion
In the future, the development of automotive fasteners will be more personalized, heat treatment processes will be more prominent in service characteristics, and intelligent, green, and lightweight technologies will all play an important role. The development of technology and equipment is the foundation for the development of advanced manufacturing, and there is still a lot of room for development. To narrow the gap with the advanced level of foreign countries, the task is still very arduous, and the task is heavy and long.
Link to this article: Analysis on the new development trend of heat treatment technology for automobile fasteners
Reprint Statement: If there are no special instructions, all articles on this site are original. Please indicate the source for reprinting:https://www.cncmachiningptj.com
PTJ® is a customized manufacturer that provides a full range of copper bars, brass parts and copper parts. Common manufacturing processes include blanking, embossing, coppersmithing, wire edm services, etching, forming and bending, upsetting, hot forging and pressing, perforating and punching, thread rolling and knurling, shearing, multi spindle machining, extrusion and metal forging and stamping. Applications include bus bars, electrical conductors, coaxial cables, waveguides, transistor components, microwave tubes, blank mold tubes, and powder metallurgy extrusion tanks.
Tell us a little about your project’s budget and expected delivery time. We will strategize with you to provide the most cost-effective services to help you reach your target,You are welcome to contact us directly ( sales@pintejin.com ) .
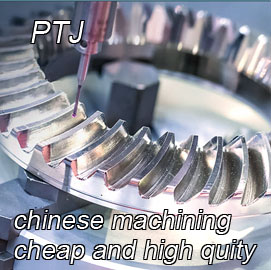
- 5 Axis Machining
- Cnc Milling
- Cnc Turning
- Machining Industries
- Machining Process
- Surface Treatment
- Metal Machining
- Plastic Machining
- Powder Metallurgy Mold
- Die Casting
- Parts Gallery
- Auto Metal Parts
- Machinery Parts
- LED Heatsink
- Building Parts
- Mobile Parts
- Medical Parts
- Electronic Parts
- Tailored Machining
- Bicycle Parts
- Aluminum Machining
- Titanium Machining
- Stainless Steel Machining
- Copper Machining
- Brass Machining
- Super Alloy Machining
- Peek Machining
- UHMW Machining
- Unilate Machining
- PA6 Machining
- PPS Machining
- Teflon Machining
- Inconel Machining
- Tool Steel Machining
- More Material