Research on temperature and molten pool monitoring of laser additive manufacturing monitoring technology
3D printing technology has unique advantages such as short manufacturing cycle, high material utilization, and good process flexibility. It has an important impact on the manufacturing industry and has a wide range of important applications in many fields such as industrial production, aerospace, and medicine. However, many technical challenges hinder the wide application of laser additive manufacturing technology and its great potential.
One of the biggest obstacles is the quality inspection of the final product, especially in areas that have extremely high requirements for product quality, such as aviation. In the aerospace and medical fields, the laser additive manufacturing process needs to be monitored and controlled. By monitoring the manufacturing process to reduce the occurrence of defects, improve the dimensional accuracy and mechanical properties of the product, and ultimately achieve the goal of improving product quality.
At present, many domestic and foreign researchers are studying laser process monitoring in full swing. They have developed a lot of systems that can monitor the laser additive manufacturing process. These systems only need to focus on online detection and correction of the physical parameters of the molten pool. Component defects are detected and feedback control is used to reduce these defects. The laser monitoring process is mainly divided into two parts, one is data acquisition and the other is data processing.
There are two main parts of data collection, the shape of the molten pool and the temperature of the molten pool. The shape of the molten pool is generally obtained by a CCD camera or an infrared camera, and the temperature of the molten pool is generally measured by a photodiode or a pyrometer. Data processing means that the measured data is processed and sent to the controller, and the controller configures and updates the operating parameters of the system, and effectively controls the operating process of the system, thereby improving the quality of the product. It is worth noting that there are many control methods used by the controller, including traditional PID control, fuzzy control, and artificial intelligence control such as neural network control. The most mature currently used is traditional PID control. The current research focus is Various artificial intelligence control methods.
The following describes the working process and results of a specific control system. The experimental process is a laser metal deposition experiment, the purpose of which is to improve the shape accuracy of the product through control. Figure 1 is a process diagram of a laser metal deposition experiment. Through experiments, it can be found that the product's external dimension accuracy has a great relationship with the heat radiation signal during the manufacturing process. When the heat radiation signal remains unchanged, the size of the molten pool is basically unchanged , The stability of the molten pool size will improve the dimensional accuracy of the product shape. Figure 2 is a diagram of the laser metal deposition monitoring process. The process uses an adaptive PID control method. The measured thermal radiation signal is input to the adaptive PID controller, and the controller outputs a control signal. The control signal is applied to the laser transmitter and adjusted The laser power keeps the intensity of the thermal radiation signal basically unchanged.
The overall dimensions and thermal radiation temperature of the molten pool are shown in Figures 3 and 4. Comparing these two figures, it can be seen that the thermal radiation signal of the process using the control system is relatively stable, basically maintaining the set value of 2, and the corresponding melting The size of the pool is also stable, the maximum and minimum difference between the molten pool is 0.1mm; the heat radiation signal of the process without the control system increases, and the corresponding molten pool size increases, and the maximum and minimum difference between the molten pool is 1.27mm.
The macroscopic image of the product is shown in Figure 5 and Figure 6. Comparing these two figures, it can be clearly seen that the surface of the product using the control system is smoother, the height and width are more uniform, and the width change has dropped from 63.6% to 12.5% It can be seen that this adaptive control system has achieved the purpose of improving the accuracy of the product shape.
Of course, this is only one application of the laser monitoring process. For different goals, such as reducing product defects, improving product fatigue strength and various mechanical properties, etc., researchers have proposed various control systems and control methods.
Current research shows that due to the complex integration of control systems and production processes, the limitations of measurement tools and sensors, and the difficulty of real-time control, many systems have not been applied in actual industrial production processes. The research is still in the development stage. It is believed that in the near future, with the continuous deepening of research, laser additive manufacturing monitoring technology will get more mature development and practical applications.
Link to this article:
Reprint Statement: If there are no special instructions, all articles on this site are original. Please indicate the source for reprinting:https://www.cncmachiningptj.com
PTJ® is a customized manufacturer that provides a full range of copper bars, brass parts and copper parts. Common manufacturing processes include blanking, embossing, coppersmithing, wire edm services, etching, forming and bending, upsetting, hot forging and pressing, perforating and punching, thread rolling and knurling, shearing, multi spindle machining, extrusion and metal forging and stamping. Applications include bus bars, electrical conductors, coaxial cables, waveguides, transistor components, microwave tubes, blank mold tubes, and powder metallurgy extrusion tanks.
Tell us a little about your project’s budget and expected delivery time. We will strategize with you to provide the most cost-effective services to help you reach your target,You are welcome to contact us directly ( sales@pintejin.com ) .
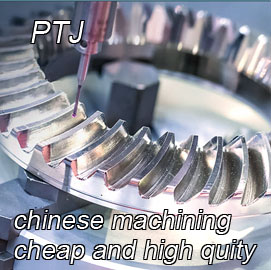
- 5 Axis Machining
- Cnc Milling
- Cnc Turning
- Machining Industries
- Machining Process
- Surface Treatment
- Metal Machining
- Plastic Machining
- Powder Metallurgy Mold
- Die Casting
- Parts Gallery
- Auto Metal Parts
- Machinery Parts
- LED Heatsink
- Building Parts
- Mobile Parts
- Medical Parts
- Electronic Parts
- Tailored Machining
- Bicycle Parts
- Aluminum Machining
- Titanium Machining
- Stainless Steel Machining
- Copper Machining
- Brass Machining
- Super Alloy Machining
- Peek Machining
- UHMW Machining
- Unilate Machining
- PA6 Machining
- PPS Machining
- Teflon Machining
- Inconel Machining
- Tool Steel Machining
- More Material