The status quo and development trend of 3D printing technology in metal parts manufacturing
3D printing is also known as "additive manufacturing". The F42 International Committee of the American Society for Testing and Materials (ASTM) clearly defines it as "the technology that uses print heads, nozzles or other printing technologies to deposit materials to make objects."
Therefore, 3D printing is a general term for a type of manufacturing technology, including a wide range of raw material applications and additive process methods from connotation to extension. Since the publication of the patent for 3D terrain model manufacturing based on the principle of laminated manufacturing in 1892, the original innovation activity of 3D printing technology has flourished. In the past 30 years, a large number of scholars at home and abroad have combined additive technology and digital manufacturing technology, and further deepened the foundation. The theoretical system has truly developed 3D printing into a technical category that can be applied industrially.
Metal parts are the product type with the largest proportion and the most widely used in the industrial system. With the acceleration of the "Industry 4.0" process, rapid development, customized manufacturing, and lightweight requirements are facing urgent pressure. And 3D printing technology has the characteristics of high degree of freedom, wide range of materials, excellent part performance and few manufacturing links. It fits well with the future development trend of metal parts and components, and has begun to enter the practical stage.
At this stage, 3D printing technology does not completely serve the field of metal parts manufacturing in the form of a single technology application. It is classified according to its role in the forming process of metal parts. The service methods can be roughly divided into indirect manufacturing, direct manufacturing and combination. Manufacturing method. The multi-mode application method effectively takes into account the manufacturing cost and use value of metal parts products, and expands the application space of 3D printing technology in the industrial field.
1. The status quo and development trend of indirect manufacturing
Casting is an important and extensive technical way to obtain metal parts. In the traditional foundry industry, most of them include the process of mold manufacturing, and mold design, development and modification are a long and expensive process. In 3D printing technology RapidPrototyping technology can effectively solve this problem and obtain a large number of applications. Among them, representative technologies include selective laser sintering (SLS), laser stereo light curing (SLA) and resin droplet jet (3DP) technology. Using selective laser sintering technology can save the mold manufacturing process, directly used to make phenolic resin coated sand molds, investment core shells and other products, used for casting metal parts products; laser stereo light curing technology is through a specific wavelength The laser beam curing photosensitive resin molding method has the characteristics of high molding freedom, low part roughness, and good dimensional accuracy. It is used to make rigid polymer molds with a strength of up to 50MPa. It is suitable for furan resin sand and water glass sand. And the sand mold reversal manufacturing of green sand mold, the mold life and dimensional accuracy level can meet the production of small batch casting products, and the manufacturing time and cost are lower than traditional metal molds; resin droplet injection technology adopts the method of dynamic control of array nozzles to obtain In order to achieve a faster surface scanning speed, it is suitable for the high-efficiency manufacturing of furan resin self-setting sand molds.
The laser sintering mechanism and application technology of coated sand molds have been basically perfected. The earliest institutions in my country to select laser sintering coated sand include Huazhong University of Science and Technology, Xi’an Jiaotong University and other universities. The domestic development and sales of such equipment mainly include Wuhan Bin Lake Mechanical and Electrical Technology Industry Co., Ltd., Beijing Yijia 3D Technology Co., Ltd. and Beijing Longyuan Automatic Forming System Co., Ltd. The equipment of the above three companies has the largest installed capacity in foundry enterprises and scientific research institutes and is also the most widely used.
Laser three-dimensional light curing technology originated in the United States. 3D Systems has always maintained the leading advantage of this technology. my country’s Xi’an Jiaotong University and other universities have conducted more thorough research on photosensitive numerical materials and technical mechanisms. Domestic Suzhou Zhongrui Electromechanical Technology Co., Ltd., Beijing Yijia 3D Technology Co., Ltd. and Shanghai Liantai Technology Co., Ltd. have developed high cost-effective industrial application equipment, which is suitable for industry fields such as model manufacturing.
The American Exone company and the German Voxeljet company are the promoters and leaders of the commercial application of resin droplet jet technology; in China, Guangdong Fenghua Zhuoli Technology Co., Ltd. has launched similar technical equipment and realized the open source use of raw materials. The high cost-effective experience has achieved sales in international and domestic foundry companies; Ningxia Sharing Group has purchased multiple Exone equipment for the construction of intelligent casting production lines, and has carried out the work of localization of raw materials and equipment, which has achieved large-scale The stable operation of the 3D printer with chemical furan resin droplet jetting.
The maturity level of the above rapid prototyping technology has fully met the rapid development needs of molds. The sales of equipment, raw materials and technical services are in the market explosion period, such as CRRC, Guangxi Yuchai Machinery Group Co., Ltd., Jianghuai Automobile and other large-scale equipment Manufacturing companies have established sand mold rapid manufacturing service units based on 3D printing technology, and small companies in the industry for rapid development services for castings are gradually increasing.
It is worth noting that the current rapid prototyping technology speeds up the development of casting products by saving or saving mold development time. It is only suitable for the development of multi-variety, small-batch castings and the rapid shaping of the casting process. It cannot be compared with the traditional casting industry. Compete with mass production models. Judging from the current technology status and application cases, various 3D printing technologies that serve the development of molds have their own advantages and disadvantages. The equipment price of selective laser sintering coated sand technology is relatively reasonable, and the obtained coated sand casting mold has a wide range of applications. It can be widely used in the field of cast steel, cast iron and non-ferrous alloy casting, but the manufacturing efficiency is low; laser stereo light curing The casting mold obtained by the technology cannot compete with traditional metal molds in terms of strength and life, and the poor high-temperature performance limits its application in the thermoforming process of coated sand; although the resin droplet injection technology is relatively efficient , But the core device array nozzle has a short life and high replacement cost, and it is only suitable for furan resin sand as a raw material, which is difficult to meet the production requirements of high-quality castings.
Whether the scope of application of the mold and the efficiency of equipment manufacturing can be effectively balanced is a key factor that affects the application of 3D printing technology in the casting mass production mode. At present, the technology of high-power semiconductor lasers that can be turned off dynamically has achieved a substantial breakthrough. In the future, various research institutions and manufacturing companies will develop array scanning equipment for sintering phenolic coated sand materials, and achieve high-speed wide-width application of sand molds at low maintenance costs. Manufacturing can truly make 3D printing a necessary process for traditional casting.
2. The status quo and development trend of direct manufacturing
For some metal parts products that are difficult to form with traditional processes, high performance requirements, and special operating conditions, they usually have a higher technical cost value. At present, they have begun to use 3D printing to develop and produce directly. Thanks to the coordinated progress of precision CNC machining technology, laser technology and high-speed galvanometer technology, the use of high-energy beams such as laser, electron beam, arc and other high-energy beams to melt metal powders and wires can be directly produced according to the product design three-dimensional drawings. Shape and high-performance metal parts products.
At present, the 3D printing technologies for direct manufacturing of metal parts that have been practically applied include laser three-dimensional forming technology (LDM), selective laser melting technology (SLM), selective electron beam melting technology (SEBM), etc. The product material range covers titanium alloys, Series of high-temperature alloys, non-ferrous alloys, high-strength steels, etc. Among them, the laser three-dimensional forming technology uses the beam synchronous powder feeding method to quickly melt and accumulate metal powders point by point, which can produce large-scale metal parts products. The research and application of this technology in China are equivalent to, or even partly beyond, the level of foreign technology. . The team of Professor Huang Weidong of Northwestern Polytechnical University has developed a titanium alloy central flange part based on the technology and equipment with independent intellectual property rights. The maximum size is 3.07m and the maximum deformation is less than 0.8mm. It has been successfully applied to the test stage of the C919 passenger aircraft prototype, comprehensive evaluation Meet the requirements of mechanical properties, fatigue strength and fracture toughness of forgings, and the consistency level of mechanical properties is much higher than the American Boeing company manufacturing and construction standards; AirBus company and Northwestern Polytechnical University signed a cooperation agreement with the expectation of developing laser three-dimensional forming technology manufacturing System demonstration of large-scale titanium alloy components; currently, GE is relying on Northwestern Polytechnical University to optimize and verify the process plan of laser three-dimensional forming of composite material wide-chord fan blades titanium alloy and high-temperature alloy inlet. The team of Academician Wang Huaming of Beijing University of Aeronautics and Astronautics focused on the laser three-dimensional forming technology of aircraft large titanium alloy structural parts. The titanium alloy main bearing reinforced frame exhibited in 2013 has increased the utilization rate of materials by 5 times compared with forging and shortened the manufacturing cycle by 2/ 3. The manufacturing cost is reduced by 1/2, and a variety of models have been applied in a number of domestic military models.
Selective laser melting and selective electron beam melting are technologies that use energy beams to melt the layered area of the powder bed to realize the layer-by-layer melting-solidification of metal powder, which is suitable for the direct manufacturing of small and complex metal parts. In the selection of laser melting technology, EOS, ConceptLaser, and SLMSolution of Germany are the world leaders in technology application and equipment development; in China, the Zeng Xiaoyan team of Huazhong University of Science and Technology pioneered aerospace metal parts through self-developed technology and equipment Using the precedent of laser melting technology in selected areas, Northwestern Polytechnical University has successively carried out the development of laser sintering equipment and core technology in selected areas, and established Xi’an Bright Additive Technology Co., Ltd., which has developed into the largest metal additive manufacturing in China. As a comprehensive service company, the comprehensive performance indicators of various types of equipment are close to the level of German EOS equipment, and it has achieved multiple sets of sales to European aviation manufacturing companies. The scope of product services covers aviation, aerospace, education, medical and other fields. In the area of electron beam melting, Sweden's Arcam company is a leader in technology and equipment. The Northwest Non-Ferrous Metal Research Institute in China has purchased its equipment and carried out related forming technology research work.
The 3D printing technology for the direct manufacturing of metal parts makes full use of the grain refinement and the small tendency of solute segregation in the solidification process of the metal melt away from the equilibrium state. It can obtain a fine and uniform matrix structure and make the metal parts appear Good mechanical properties; in addition, the lattice structure and topology optimization technology in the modern structural design concept can be fully utilized through the free forming ability of 3D printing, which greatly improves the lightweight level of metal parts. The synergy of these advantages has laid the foundation for the application of 3D printing. It has been widely used in the extremely lightweight and high-reliability parts of high-end equipment such as aviation and aerospace. In addition, with the continuous expansion of metal powder grades and specifications, The price of equipment core devices continues to drop, and the application cost of 3D printing technology for direct manufacturing of metal parts is approaching a reasonable range. Civilian high-end equipment products such as rail transit and ships have similar batch characteristics to aviation and aerospace products, and contain their own unique structural features and requirements for lightweight and safety indicators. They will provide selective laser melting technology and laser three-dimensional forming technology. New application space.
3. The status quo and development trend of combined manufacturing
Combining the traditional forming method of metal parts with the direct manufacturing method of 3D printing extends the combined manufacturing method. The methods that have been reported so far are mainly: the combination of casting and laser three-dimensional forming technology, and the combination of forging and laser three-dimensional forming technology Combination and combination of laser three-dimensional forming technology and cutting processing. Domestically, Northwestern Polytechnical University adopted the combination technology of casting + laser three-dimensional forming in the manufacturing of the rear casing of my country’s first aero-engine with thrust-to-weight ratio of 10 in 2005. The regular shape area of the lower part of the product is formed by In961 alloy casting and the upper part of the complex structure area is formed. The laser three-dimensional forming of GH4169 nickel-based superalloy was completed and passed the installation assessment; in 2009, Optomec Design of the United States used laser three-dimensional forming technology to repair the military aircraft T700 forged blisk, and passed the military's vibration fatigue verification test; In the late 1990s, a joint research project between Japanese universities and industry combined laser three-dimensional forming with CNC machine tools, and launched the earliest commercial equipment, namely Matsuura's LUMEX Avance-25. Nowadays, Mazak, DMG, Trumpf and other world-leading precision machine tool manufacturers have judged the huge demand in the future market, respectively launched their own laser three-dimensional forming + CNC cutting commercial equipment and began to sell them. The combined manufacturing method reduces the cost range of 3D printing to directly manufacture metal parts to a certain extent, overcomes the traditional manufacturing limitations of difficult-to-form materials, and opens up a new way for the additive manufacturing of metal parts, which is expected to be in the civilian field. Get a wide range of applications.
4, the conclusion
Compared with traditional metal parts forming technologies such as casting, forging, welding and mechanical cutting, 3D printing technology has been applied in the industrial field for a short time, and the earliest research and application activities carried out around the demand are mostly concentrated in high-value aviation, aerospace, etc. In the product field, the high manufacturing cost prohibits the ordinary civilian field, but its free forming, near-net forming and high-performance parts are unmatched by the traditional forming process. This is also in the adjustment of economic structure and upgrading of industrial structure. Under the historical development trend of the world, the fundamental reason why 3D printing technology is being developed by the world's industrial powers is the competition. 3D printing technology itself is also a broad technology category. Relatively mature sub-technologies are being integrated into the existing industrial system through modification and transformation. Various new cost-effective and high-efficiency 3D printing technology models are also under continuous development. In the future, through the in-depth collaboration of scholars in the field of science and technology and practitioners in the field of engineering applications, 3D printing technology will surely form a multi-level and multi-dimensional application pattern under the new industrial system.
Link to this article: The status quo and development trend of 3D printing technology in metal parts manufacturing
Reprint Statement: If there are no special instructions, all articles on this site are original. Please indicate the source for reprinting:https://www.cncmachiningptj.com
PTJ® provides a full range of Custom Precision cnc machining china services.ISO 9001:2015 &AS-9100 certified.
Machining shop specializing in fabrication services for construction and transportation industries. Capabilities include plasma and oxy-fuel cutting, Tailored machining, MIG and Custom Aluminum Cnc Precision Milling Welding Jig Fixture, roll forming, assembly, Lathe machining stainless steel cnc machine shaft, shearing, and CNC Swiss Machining services. Materials handled include carbon and Passivation Stainless Steel Machining Cover Plate Parts.
Tell us a little about your project’s budget and expected delivery time. We will strategize with you to provide the most cost-effective services to help you reach your target,You are welcome to contact us directly ( sales@pintejin.com ) .
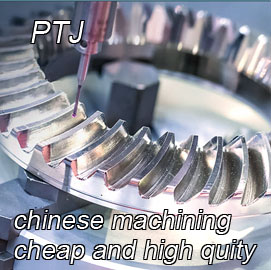
- 5 Axis Machining
- Cnc Milling
- Cnc Turning
- Machining Industries
- Machining Process
- Surface Treatment
- Metal Machining
- Plastic Machining
- Powder Metallurgy Mold
- Die Casting
- Parts Gallery
- Auto Metal Parts
- Machinery Parts
- LED Heatsink
- Building Parts
- Mobile Parts
- Medical Parts
- Electronic Parts
- Tailored Machining
- Bicycle Parts
- Aluminum Machining
- Titanium Machining
- Stainless Steel Machining
- Copper Machining
- Brass Machining
- Super Alloy Machining
- Peek Machining
- UHMW Machining
- Unilate Machining
- PA6 Machining
- PPS Machining
- Teflon Machining
- Inconel Machining
- Tool Steel Machining
- More Material