CNC Equipment And Computer Communication
Numerical control equipment has been widely used in our factory for its advantages of high precision, high efficiency, flexible programming, and automatic processing. Our factory now has a certain number of CNC equipment, including Toyota machining center from Japan, honing machine from Germany, CNC machine tool from Italy, etc. The CNC system equipped with SINUMERIK series from Siemens, M32 and M520 series NC from Mitsubishi, etc. . To ensure the normal use of so many CNC equipment and systems, their management and maintenance levels must keep up. After several years of technical preparation, we have developed a personal computer-assisted numerical control equipment and fault diagnosis and maintenance system. The system can be connected online with numerical control equipment, and can input and output machine parameter processing programs and PLC programs, and can also be used for offline editing, modification, storage, backup, etc., and real-time monitoring of machine tools can be used to find faults in time Point for repairs.
1. Computer hardware and software configuration
The hardware configuration of the system:
- 1) 386 or above personal computer (for the convenience of workshop on-site use, we choose notebook 386 AST personal computer)
- 2) 24-pin printer
- 3) Dedicated interface, dedicated cable, etc.
System software configuration:
- 1) MS-DOS 6.22 operating system software
- 2) System data software V24, PCIN, PCIO, etc. that communicate with NC equipment
- 3) Special software for communication with CNC equipment PLC: including data software and system software FAPT LADDER for communication with FANUC PMC; system data software STEP5, GRAPH5 for communication with SINUMERIK S-5 series PLC (S5-100U, 135U, 115U, etc.) Wait.
2. The specific application method of computer in the management and maintenance of numerical control equipment
The computer system can realize effective management and maintenance functions only after it is connected to the NC and PLC of the numerical control equipment.
(1) The communication mode and realized function of computer and numerical control equipment NC
The notebook AST computer we use has a 9-pin RS-232 standard serial interface, while the NC device of the numerical control equipment generally only has a 25-pin RS-232s standard interface. The two must be connected by a special cable to pass the special software. Set up and exchange information with each other.
At present, there are relatively complete system software and data software used in the communication between the computer and the NC of the numerical control equipment in the world. At present, the commonly used ones are: V24, PCIN, PCIO, PCCS and so on. What we often use is the AG communication software PCIO of Siemens AG in Germany. PCIO software has software and rich menu units, simple and fast operation, and complete functions.
NC communication software can mainly realize the following functions:
- 1) Initialize the serial port to set the interface number, baud rate, data bit, stop bit, parity bit and other parameters. These parameters set in the computer communication software must be consistent with the parameters of the internal device of the numerical control equipment NC, so that the NC and the computer can be successfully connected and communicated.
- 2) Transfer the internal data of the numerical control equipment NC to the computer memory.
- 3) Output computer memory data to NC.
- 4) Edit, print, and delete data such as machine parameters and processing procedures.
If the cable signal connection is accurate and the interface communication software can be used correctly, the information between the computer and the NC of the numerical control equipment can be exchanged smoothly, and the machine parameters, machining programs, etc. can be input/output and edited through the PCIO system data software. , Storage, backup and other operations.
(2) Communication mode and realized functions between computer and CNC equipment PLC
There are two types of PLC for CNC equipment: one type is a "BUTLT-IN TYPE" PLC designed and manufactured for the sequential control of CNC machine tools; the other type is a standard "stand-alone type" (STAND-ALONE TYPE) PLC.
At present, our factory has built-in PLC systems such as FANUC 3T, OT and other systems; SINUMERIK810 from SIEMENS; AB-84oo from AB. With independent PLC systems, there are SINUMERIK3, 8 systems, and its PLC is SIMATICS5-100U, 135U, etc. The computer must be connected to the PLC through a dedicated interface and cable, and can exchange and process data with the PLC through the use of dedicated system software and data software. The computer can do "online" or "offline" programming, transmission, debugging, machine tool status monitoring, etc. to the PLC.
The communication between computer and FANUC PMC has special system software and data software FAPT LADDER, and special interface. (The space is limited, so I won’t go into details here.) Communications. We changed the ABC switch converter used on the computer into an interface converter. The A port is connected to the AS511 board. For the SINUMERIK S5 stand-alone PLC series, the AS511 conversion board is required to communicate with the computer.
Port B is connected to the 25-pin standard RS232 serial port of SINUMERIK 810 system. There is software inside the 810NC to set the conversion by itself, and it can be directly connected with the ABC converter. The communication software between Siemens S5 series PLC and computer includes STEP5, GRAPH5 and so on. STEP5 is a full-featured system data software, with abundant software and menu units, easy to operate.
The communication between the computer and the PLC of the CNC system can mainly realize the following functions:
- 1) Use the keyboard or floppy disk to input the PLC program into the computer. The computer can store all PLC programs in the floppy disk software or print them into a program list or ladder diagram.
- 2) The PLC sequence program can be displayed on the LCD. It can be edited by keyboard or light pen, etc., and diagnose program errors in editing, and display the diagnosis result.
- 3) After the computing system is connected to the PLC, the program in the computer can be sent to the PMC-RAM board of the CNC device. The PLC program on the RAM board in the machine tool can also be sent to the computer.
- 4) It can monitor the running status of the PLC, analyze the PLC program according to the computer display, analyze the various statuses of the machine tool, such as whether the temperature is too high, whether the solenoid valve is operating, etc., find the fault point in time, and repair it as soon as possible.
3.Application examples
Using a computer, we back up the machine parameters and processing programs of all CNC equipment, establish files for special management; also file some PLC programs on the computer, which brings a lot of convenience to the maintenance and management of CNC equipment.
The machine tool once lost all the machine parameters and machining programs stored in the RAM board due to a battery failure. This machine tool undertakes the urgent task, and the parameters and programs are large. It takes a few days to input the manual panel as before, which seriously affects the production process. However, we used this computer system to input, and it only took more than ten minutes to re-input the machine data and machining programs that had been backed up to the NC of the machine tool. This greatly reduces the downtime and improves the efficiency of the equipment.
A CNC grinder fails: the machine cannot be started, and the program is locked and cannot run. After inspection, the peripheral circuits are all intact, so it is judged that the fault is from inside the NC. Since the machine tool could not be started, we used the computer to analyze the PLC program of the machine tool, and compared it with the original backup PLC program. We found that the PLC program of the machine tool was wrong, and we modified it one by one. After re-input, we finally used The machine tool resumes movement. In this way, with the help of the computer system, all the machine tools can be restored to normal.
Practice has proved that the use of computer to assist in the management and maintenance of CNC equipment is simple and efficient in diagnosis and maintenance, which raises the level of management and maintenance of CNC equipment to a higher level. At the same time, it can also solve some equipment failure problems that cannot be handled by conventional methods. , Reduce maintenance costs and downtime, and improve the efficiency of equipment use.
Link to this article: CNC Equipment And Computer Communication
Reprint Statement: If there are no special instructions, all articles on this site are original. Please indicate the source for reprinting:https://www.cncmachiningptj.com/,thanks!
3, 4 and 5-axis precision CNC machining services for aluminum machining, beryllium, carbon steel, magnesium, titanium machining, Inconel, platinum, superalloy, acetal, polycarbonate, fiberglass, graphite and wood. Capable of machining parts up to 98 in. turning dia. and +/-0.001 in. straightness tolerance. Processes include milling, turning, drilling, boring, threading, tapping, forming, knurling, counterboring, countersinking, reaming and laser cutting. Secondary services such as assembly, centerless grinding, heat treating, plating and welding. Prototype and low to high volume production offered with maximum 50,000 units. Suitable for fluid power, pneumatics, hydraulics and valve applications. Serves the aerospace, aircraft, military, medical and defense industries.PTJ will strategize with you to provide the most cost-effective services to help you reach your target,Welcome to Contact us ( sales@pintejin.com ) directly for your new project.
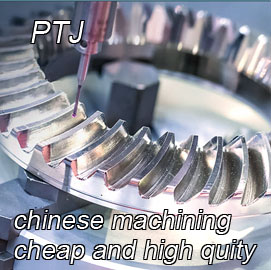
- 5 Axis Machining
- Cnc Milling
- Cnc Turning
- Machining Industries
- Machining Process
- Surface Treatment
- Metal Machining
- Plastic Machining
- Powder Metallurgy Mold
- Die Casting
- Parts Gallery
- Auto Metal Parts
- Machinery Parts
- LED Heatsink
- Building Parts
- Mobile Parts
- Medical Parts
- Electronic Parts
- Tailored Machining
- Bicycle Parts
- Aluminum Machining
- Titanium Machining
- Stainless Steel Machining
- Copper Machining
- Brass Machining
- Super Alloy Machining
- Peek Machining
- UHMW Machining
- Unilate Machining
- PA6 Machining
- PPS Machining
- Teflon Machining
- Inconel Machining
- Tool Steel Machining
- More Material