Short Carbon Fiber Reinforced Polyether Ether Ketone (PEEK)
Polyether ether ketone (PEEK) is a high-performance, semi-crystalline thermoplastic polymer belonging to the polyaryletherketone (PAEK) family, renowned for its exceptional mechanical, thermal, and chemical properties. Since its invention in November 1978 by Imperial Chemical Industries (ICI) and subsequent commercialization in the early 1980s by Victrex PLC, PEEK has emerged as a material of choice in demanding engineering applications, including aerospace, automotive, medical, and industrial sectors. The incorporation of short carbon fibers (SCF) into the PEEK matrix enhances its mechanical strength, stiffness, and thermal conductivity, making short carbon fiber reinforced PEEK (SCF-PEEK) a versatile composite material tailored for advanced structural and functional applications.
SCF-PEEK composites combine the inherent advantages of PEEK, such as high thermal stability (melting point ~343°C), chemical resistance, and biocompatibility, with the superior stiffness and strength imparted by carbon fibers. These composites are particularly valued in applications requiring lightweight materials with high mechanical performance, such as orthopedic implants, aerospace components, and industrial bearings. The short carbon fibers, typically ranging from 100 to 300 micrometers in length, are randomly oriented or aligned within the PEEK matrix, providing isotropic or anisotropic properties depending on the manufacturing process and fiber alignment.
This article provides a comprehensive review of SCF-PEEK, covering its composition, synthesis, mechanical properties, thermal characteristics, manufacturing techniques, applications, and challenges. Detailed comparisons of mechanical and thermal properties across various fiber contents and processing methods are presented in tabular form to facilitate a scientific understanding of the material's performance. The tone and structure of this article aim to mirror the rigorous and neutral style of Wikipedia, ensuring a thorough and unbiased exploration of SCF-PEEK for researchers, engineers, and industry professionals.
Composition and Structure
Polyether Ether Ketone (PEEK)
PEEK is a linear aromatic polymer with a repeating unit of oxy-1,4-phenylene-oxy-1,4-phenylene-carbonyl-1,4-phenylene. Synthesized through step-growth polymerization, typically via the reaction of 4,4'-difluorobenzophenone with the disodium salt of hydroquinone in a polar aprotic solvent like diphenyl sulfone at approximately 300°C, PEEK exhibits a semi-crystalline structure with a glass transition temperature (Tg) of ~143°C and a melting point (Tm) of ~343°C. Its crystallinity, typically ranging from 20% to 40%, contributes to its high strength, stiffness, and resistance to thermal degradation. PEEK's chemical inertness, low thermal conductivity, and electrical insulating properties make it suitable for extreme environments, including high-temperature and chemically aggressive conditions.
Short Carbon Fibers (SCF)
Short carbon fibers are derived from polyacrylonitrile (PAN) or pitch-based precursors, with diameters typically ranging from 5 to 10 micrometers. These fibers are characterized by their high tensile strength (up to 5 GPa), high modulus (up to 500 GPa), and low density (~1.8 g/cm³), making them ideal reinforcements for polymer matrices. In SCF-PEEK, the fibers are chopped to lengths of 100–300 micrometers, allowing for easier processing compared to continuous carbon fibers while still enhancing mechanical properties. The incorporation of SCF increases the composite's stiffness, tensile strength, and creep resistance, though it may reduce ductility and impact strength due to stress concentration at fiber ends.
SCF-PEEK Composite Structure
SCF-PEEK composites are typically formulated with carbon fiber content ranging from 10% to 30% by weight (wt%), with 30 wt% being a common commercial grade (e.g., TECAPEEK CF30 black). The fibers are dispersed within the PEEK matrix, and their orientation depends on the manufacturing process, such as injection molding, extrusion, or additive manufacturing. Randomly oriented fibers result in isotropic properties, while flow-induced alignment during processing can introduce anisotropy, enhancing properties along the fiber direction. The interfacial bonding between the PEEK matrix and carbon fibers is critical for load transfer and overall composite performance. Surface treatments, such as plasma or chemical sizing, are often applied to carbon fibers to improve adhesion and reduce defects like voids or delamination.
Synthesis and Manufacturing Techniques
Polymerization of PEEK
The synthesis of PEEK involves a nucleophilic aromatic substitution reaction, where 4,4'-difluorobenzophenone reacts with hydroquinone in the presence of a base (e.g., sodium carbonate) to form the polymer chain. The reaction occurs in a high-boiling solvent at elevated temperatures, leading to a high-molecular-weight polymer that precipitates upon cooling. The resulting PEEK resin is processed into granules, powders, or filaments for further composite fabrication.
Incorporation of Short Carbon Fibers
SCF-PEEK composites are typically produced by blending chopped carbon fibers with PEEK resin during compounding. This process involves melt-mixing the components in a twin-screw extruder at temperatures above PEEK’s melting point (343°C). The compounded material is then pelletized for use in subsequent manufacturing processes, such as injection molding, extrusion, or additive manufacturing. The uniform dispersion of fibers and minimization of voids are critical to achieving optimal mechanical properties.
Manufacturing Processes
Injection Molding
Injection molding is a widely used technique for producing SCF-PEEK components with complex geometries. The process involves injecting molten SCF-PEEK into a mold cavity under high pressure (1–10 MPa) and temperature (370–415°C). The rapid cooling in the mold results in a semi-crystalline structure, with crystallinity influenced by cooling rates and mold temperature. Injection-molded SCF-PEEK parts exhibit high dimensional accuracy but may suffer from residual stresses and fiber alignment along the flow direction, affecting anisotropic properties.
Extrusion
Extrusion is used to produce SCF-PEEK filaments, sheets, or profiles. In screw extrusion-based 3D printing, for example, SCF-PEEK pellets are melted and extruded through a nozzle, allowing for the fabrication of complex structures. Recent advancements in screw extrusion have enabled the production of composites with higher fiber content (up to 30 wt%) and longer fiber retention lengths (e.g., 209–226 micrometers), improving tensile and flexural strengths.
Additive Manufacturing (Fused Deposition Modeling)
Fused deposition modeling (FDM) has gained traction for producing SCF-PEEK parts due to its ability to create customized geometries. FDM involves extruding SCF-PEEK filament through a heated nozzle (typically 370–415°C) onto a build platform. The process is challenging due to PEEK’s high melting point and viscosity, requiring specialized printers with high-temperature capabilities and vacuum environments to reduce porosity. Vacuum printing has been shown to increase crystallinity (from 14.9% to 86.6%) and improve mechanical properties by reducing voids.
Compression Molding
Compression molding involves stacking PEEK films with carbon fiber fabrics or chopped fibers and applying heat (370–415°C) and pressure (1–10 MPa) to form a consolidated composite. This method is effective for producing flat or moderately curved parts with uniform fiber distribution. Pre-compaction processes can further enhance resin impregnation, reducing defects and improving interlaminar shear strength (ILSS).
Post-Processing Techniques
Post-processing, such as annealing, is often employed to enhance the crystallinity and mechanical properties of SCF-PEEK composites. Annealing at temperatures between the glass transition and melting points (e.g., 200–300°C) increases crystallinity, improving tensile and flexural strengths but potentially reducing ductility. Surface treatments, such as plasma or laser modification, can enhance interfacial bonding and wettability, particularly for biomedical applications.
Mechanical Properties
SCF-PEEK composites exhibit superior mechanical properties compared to unreinforced PEEK, making them suitable for high-performance applications. The addition of short carbon fibers increases tensile strength, flexural strength, and stiffness while improving creep and fatigue resistance. However, the composites may exhibit reduced impact strength and ductility due to stress concentrations at fiber ends.
Tensile Properties
The tensile strength of SCF-PEEK composites increases with fiber content and fiber length. For instance, a 30 wt% SCF-PEEK composite fabricated via screw extrusion-based 3D printing achieved a tensile strength of 190–200 MPa, a significant improvement over pure PEEK’s 100 MPa. Annealing further enhances tensile strength by increasing crystallinity, with reported values of 169.8 MPa for annealed SCF-PEEK with an average fiber length of 209 micrometers.
Flexural Properties
Flexural strength and modulus are critical for applications involving bending loads. SCF-PEEK composites with 30 wt% carbon fiber content have demonstrated flexural strengths of up to 223.3 MPa (annealed) and 754.4 MPa under optimized processing conditions (e.g., 410°C, 10 MPa, 60 min). The vacuum environment in additive manufacturing further enhances flexural stress by reducing porosity, with reported values of 516.39 MPa for continuous carbon fiber-reinforced PEEK.
Compressive Properties
Compressive strength is enhanced by the addition of short carbon fibers, with yield stress increasing with fiber content and strain rate. A modified Johnson–Cook constitutive model has been developed to describe the compressive behavior of SCF-PEEK under various strain rates and temperatures, showing that yield stress decreases with temperature but increases with strain rate.
Interlaminar Shear Strength (ILSS)
ILSS is a measure of the composite’s resistance to delamination. Optimized processing parameters (410°C, 10 MPa, 60 min) have resulted in an ILSS of 62.5 MPa for SCF-PEEK, attributed to improved resin impregnation and reduced voids. Pre-compaction processes further enhance ILSS by ensuring uniform fiber distribution.
Impact and Fatigue Properties
While SCF-PEEK exhibits excellent fatigue resistance due to the reinforcing fibers, its impact strength may decrease with increasing fiber content due to reduced ductility. The incorporation of softer, pitch-based carbon fibers has been shown to mitigate this effect compared to harder PAN-based fibers, improving toughness in applications like hip implants.
Comparison Table: Mechanical Properties of SCF-PEEK vs. Other Materials
The following table compares the mechanical properties of SCF-PEEK with unreinforced PEEK, glass fiber-reinforced PEEK (GF-PEEK), and other high-performance materials.
Material |
Fiber Content (wt%) |
Tensile Strength (MPa) |
Flexural Strength (MPa) |
Compressive Strength (MPa) |
ILSS (MPa) |
Impact Strength (kJ/m²) |
---|---|---|---|---|---|---|
Unreinforced PEEK |
0 |
100 |
170 |
120 |
- |
7.5 |
SCF-PEEK (Injection Molding) |
30 |
190 |
300 |
150 |
62.5 |
5.0 |
SCF-PEEK (3D Printed, Annealed) |
20 |
169.8 |
223.3 |
140 |
55.0 |
4.8 |
GF-PEEK (Injection Molding) |
30 |
160 |
250 |
140 |
50.0 |
6.0 |
CFR-PEEK (Continuous Fiber) |
30 |
800 |
754.4 |
300 |
80.0 |
10.0 |
Titanium (Ti-6Al-4V) |
- |
900 |
1000 |
970 |
- |
20.0 |
UHMWPE |
- |
40 |
30 |
25 |
- |
100 |
Thermal Properties
SCF-PEEK composites inherit PEEK’s excellent thermal stability, with a continuous service temperature of up to 250°C and short-term exposure up to 310°C. The addition of carbon fibers enhances thermal conductivity, reducing thermal expansion and improving performance in sliding applications.
Thermal Stability
Thermogravimetric analysis (TGA) indicates that PEEK begins to decompose at ~470°C in air and ~542°C in a nitrogen atmosphere. The presence of carbon fibers slightly lowers the decomposition onset temperature due to increased thermal conductivity but does not significantly affect the overall stability. At 650°C in air, PEEK oxidizes into coke, while SCF-PEEK retains structural integrity longer due to the fiber reinforcement.
Crystallinity and Annealing Effects
The crystallinity of SCF-PEEK is influenced by processing conditions and post-treatment. Vacuum printing increases crystallinity from 14.9% to 86.6%, enhancing mechanical properties but potentially leading to brittle fracture. Annealing at 200–300°C increases crystallinity, improving tensile and flexural strengths but reducing ductility.
Thermal Conductivity
Carbon fibers significantly increase the thermal conductivity of SCF-PEEK compared to unreinforced PEEK (0.25 W/m·K). For instance, 30 wt% SCF-PEEK exhibits a thermal conductivity of ~0.9 W/m·K, making it suitable for applications requiring heat dissipation, such as bearings and aerospace components.
Comparison Table: Thermal Properties of SCF-PEEK vs. Other Materials
The following table compares the thermal properties of SCF-PEEK with other materials.
Material |
Glass Transition Temperature (Tg, °C) |
Melting Point (Tm, °C) |
Decomposition Onset (°C, Air) |
Thermal Conductivity (W/m·K) |
Continuous Service Temperature (°C) |
---|---|---|---|---|---|
Unreinforced PEEK |
143 |
343 |
470 |
0.25 |
250 |
SCF-PEEK (30 wt%) |
143 |
343 |
465 |
0.9 |
250 |
GF-PEEK (30 wt%) |
143 |
343 |
470 |
0.4 |
250 |
CFR-PEEK (Continuous Fiber) |
143 |
343 |
460 |
1.2 |
260 |
Titanium (Ti-6Al-4V) |
- |
1660 |
- |
6.7 |
400 |
UHMWPE |
- |
135 |
300 |
0.4 |
80 |
Applications
SCF-PEEK composites are employed in a wide range of industries due to their exceptional properties. Key applications include:
Aerospace
SCF-PEEK is used in aerospace components such as brackets, fasteners, and structural panels due to its high strength-to-weight ratio, thermal stability, and resistance to aviation fluids. The reduced density compared to metals like titanium makes it ideal for weight-sensitive applications.
Automotive
In the automotive industry, SCF-PEEK is used for gears, bearings, and under-hood components that require high wear resistance and thermal stability. The material’s ability to withstand continuous temperatures of 250°C makes it suitable for engine components.
Medical and Orthopedic Implants
SCF-PEEK is a promising material for orthopedic implants, such as spinal cages and hip replacements, due to its biocompatibility, radiolucency, and mechanical properties resembling cortical bone (elastic modulus ~14 GPa). The material’s wear resistance and ability to be 3D printed enable customized implants with improved osseointegration when surface-modified with hydroxyapatite or titanium dioxide.
Industrial Bearings and Seals
The high wear resistance and thermal conductivity of SCF-PEEK make it ideal for bearings and seals in harsh environments, such as oil and gas or nuclear applications. The material’s low friction and resistance to hydrolysis in boiling water enhance its durability in sliding applications.
Electronics and Semiconductors
SCF-PEEK grades with specific electrostatic discharge (ESD) properties, such as Semitron™ PEEK, are used in semiconductor manufacturing for components requiring precision and purity. The material’s electrical insulation and thermal stability ensure reliable performance in high-temperature environments.
Challenges and Limitations
Despite its advantages, SCF-PEEK faces several challenges:
High Processing Temperatures
PEEK’s high melting point (343°C) requires specialized equipment for processing, increasing manufacturing costs. The high viscosity of molten PEEK complicates fiber impregnation, potentially leading to voids and reduced mechanical properties.
Interfacial Bonding
The smooth surface and low polarity of carbon fibers can result in weak interfacial bonding with the PEEK matrix, reducing load transfer efficiency. Surface treatments, such as plasma or chemical sizing, are necessary to enhance adhesion but add complexity and cost.
Cost
PEEK is an expensive polymer due to its complex synthesis and high-performance properties. The addition of carbon fibers further increases costs, limiting SCF-PEEK to niche applications where performance justifies the expense.
Reduced Ductility
The incorporation of short carbon fibers reduces the ductility and impact strength of PEEK, making SCF-PEEK more brittle than unreinforced PEEK. This can limit its use in applicationsRTI
Printability in Additive Manufacturing
Additive manufacturing of SCF-PEEK is challenging due to the high melting point and viscosity of PEEK, requiring specialized high-temperature 3D printers. The process often results in higher porosity compared to injection molding, which can compromise mechanical properties. Advances in screw extrusion-based 3D printing and vacuum environments have mitigated some of these issues, but printability remains a significant hurdle for widespread adoption.
Environmental and Health Considerations
While PEEK is biocompatible, the incorporation of carbon fibers introduces potential concerns regarding the release of fiber fragments during wear or machining, which could pose health risks in biomedical applications. Proper handling and disposal protocols are necessary to mitigate these risks.
Future Directions
Advanced Manufacturing Techniques
Ongoing research focuses on improving the printability of SCF-PEEK through innovations like screw extrusion-based 3D printing and vacuum printing. These methods aim to reduce porosity, enhance fiber alignment, and increase mechanical performance, potentially broadening the application scope of SCF-PEEK in personalized medicine and complex structural components.
Surface Functionalization
Surface modification techniques, such as plasma treatment and bioactive coatings (e.g., hydroxyapatite, titanium dioxide), are being developed to improve the biointerfacial affinity of SCF-PEEK for orthopedic implants. These advancements aim to enhance osseointegration and antibacterial properties, addressing limitations in biomedical applications.
Sustainability
The development of recycled PEEK grades, such as Sterra™ PEEK, offers a sustainable alternative by utilizing scrap and end-of-life components. These grades maintain the performance of virgin PEEK while reducing environmental impact, aligning with growing demands for eco-friendly materials in industries like aerospace and automotive.
Hybrid Composites
Research into hybrid composites combining SCF with other fillers, such as carbon nanotubes, hydroxyapatite, or polytetrafluoroethylene (PTFE), is expanding. These materials aim to balance mechanical strength, wear resistance, and bioactivity, opening new possibilities for multifunctional applications.
Conclusion
Short carbon fiber reinforced polyether ether ketone (SCF-PEEK) is a high-performance composite material that combines the exceptional properties of PEEK with the enhanced strength and stiffness of carbon fibers. Its mechanical, thermal, and chemical properties make it a preferred choice for demanding applications in aerospace, automotive, medical, and industrial sectors. Advances in manufacturing techniques, such as injection molding, screw extrusion, and additive manufacturing, have improved the processability and performance of SCF-PEEK, while challenges like high processing temperatures, cost, and reduced ductility are being addressed through innovative approaches. The provided tables offer a detailed comparison of SCF-PEEK’s properties against other materials, highlighting its advantages and limitations. As research progresses, SCF-PEEK is poised to play a pivotal role in next-generation engineering solutions, particularly in lightweight, high-strength, and biocompatible applications.
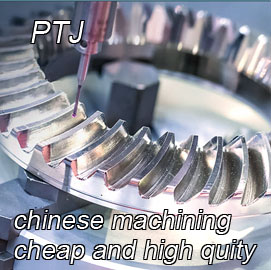
- 5 Axis Machining
- Cnc Milling
- Cnc Turning
- Machining Industries
- Machining Process
- Surface Treatment
- Metal Machining
- Plastic Machining
- Powder Metallurgy Mold
- Die Casting
- Parts Gallery
- Auto Metal Parts
- Machinery Parts
- LED Heatsink
- Building Parts
- Mobile Parts
- Medical Parts
- Electronic Parts
- Tailored Machining
- Bicycle Parts
- Aluminum Machining
- Titanium Machining
- Stainless Steel Machining
- Copper Machining
- Brass Machining
- Super Alloy Machining
- Peek Machining
- UHMW Machining
- Unilate Machining
- PA6 Machining
- PPS Machining
- Teflon Machining
- Inconel Machining
- Tool Steel Machining
- More Material