Multi-Scale Simulation of the Influence of Different Crystalline Structures on CNC Processing Performance of Semi-Crystalline Plastics
Semi-crystalline plastics, such as polyethylene (PE), polypropylene (PP), polyamide (PA), and polybutylene terephthalate (PBT), are widely used in engineering applications due to their favorable mechanical properties, chemical resistance, and processability. These materials are characterized by a microstructure that consists of both ordered crystalline regions and disordered amorphous regions, which together govern their macroscopic behavior. The crystalline structures, including lamellae and spherulites, significantly influence the mechanical, thermal, and optical properties of these polymers, making them critical to their performance in manufacturing processes like computer numerical control (CNC) machining. CNC machining, which involves precise material removal through cutting, milling, or drilling, is a key fabrication technique for producing high-precision components from semi-crystalline plastics. However, the interaction between the material’s microstructure and the machining process is complex, necessitating advanced simulation techniques to predict and optimize performance.
Multi-scale simulation has emerged as a powerful tool to bridge the gap between the molecular-level structure of semi-crystalline plastics and their macroscopic processing behavior. By integrating computational methods across different length and time scales—ranging from atomistic to continuum levels—multi-scale simulation provides a comprehensive understanding of how crystalline structures affect CNC processing outcomes, such as surface finish, tool wear, cutting forces, and dimensional accuracy. This article explores the application of multi-scale simulation to study the influence of different crystalline structures on the CNC processing performance of semi-crystalline plastics. It covers the theoretical foundations, computational methodologies, material-specific behaviors, and recent advancements, supplemented by detailed tables comparing simulation results and experimental data.
The article is organized into several sections. First, it provides an overview of semi-crystalline plastics and their crystalline structures, followed by an explanation of CNC machining and its relevance to these materials. Subsequent sections delve into the principles of multi-scale simulation, including atomistic, mesoscale, and macroscale modeling techniques. The influence of crystalline structures on CNC processing is then analyzed, with a focus on mechanical properties, thermal effects, and surface interactions. Case studies on specific semi-crystalline plastics, such as PE, PP, PA, and PBT, are presented to illustrate the practical applications of multi-scale simulation. Finally, the article discusses challenges, future directions, and the integration of machine learning in multi-scale modeling, concluding with a comprehensive summary of key findings.
Semi-Crystalline Plastics: Structure and Properties
Microstructure of Semi-Crystalline Plastics
Semi-crystalline plastics are polymers that exhibit a dual-phase microstructure consisting of crystalline and amorphous regions. The crystalline regions are highly ordered, with polymer chains folded into lamellae—thin, plate-like structures typically 10–20 nm thick. These lamellae aggregate into larger spherulites, which are spherical structures ranging from 1 to 100 micrometers in diameter, depending on processing conditions such as cooling rate and nucleation density. The amorphous regions, conversely, consist of disordered, entangled polymer chains that provide flexibility and toughness to the material. The degree of crystallinity, typically ranging from 10% to 80%, is a critical parameter that influences the material’s mechanical, thermal, and chemical properties.
The crystalline structure is governed by the polymer’s molecular architecture, including chain length, branching, and tacticity. For example, isotactic polypropylene (iPP) forms highly ordered crystalline regions due to its regular stereochemistry, whereas atactic polypropylene (aPP) remains amorphous. The crystallization process occurs during cooling from the melt, mechanical stretching, or solvent evaporation, and is influenced by factors such as temperature, pressure, and additives like nucleating agents. The resulting microstructure, including lamellar thickness, spherulite size, and the rigid amorphous fraction (RAF)—an intermediate phase between crystalline and mobile amorphous regions—plays a significant role in determining the material’s response to mechanical deformation during CNC machining.
Mechanical Properties
The mechanical properties of semi-crystalline plastics, such as stiffness, toughness, and yield strength, are strongly dependent on their crystalline structure. The crystalline regions contribute to the material’s rigidity and strength, as the tightly packed polymer chains resist deformation. The amorphous regions, on the other hand, provide ductility and impact resistance by allowing chain slippage and energy dissipation. The RAF, which consists of stretched chain segments connecting crystalline and amorphous phases, further modulates the mechanical behavior by reducing chain mobility and enhancing stiffness.
For instance, high-density polyethylene (HDPE) with a high degree of crystallinity (up to 80%) exhibits greater stiffness and tensile strength compared to low-density polyethylene (LDPE), which has a lower crystallinity (around 40%) and is more ductile. Similarly, polyamide 6 (PA6) with well-developed spherulites shows higher yield strength but reduced toughness compared to its amorphous counterparts. These properties directly influence CNC machining performance, as stiffer materials require higher cutting forces, while ductile materials may lead to burr formation or poor surface finish.
Thermal and Chemical Properties
The crystalline structure also affects the thermal and chemical properties of semi-crystalline plastics. Crystalline regions have a distinct melting temperature (Tm), above which the ordered structure breaks down, whereas amorphous regions exhibit a glass transition temperature (Tg), below which chain mobility is restricted. The degree of crystallinity influences the melting point and heat capacity, with higher crystallinity leading to sharper melting transitions and greater thermal stability. For example, PBT with a crystallinity of 30–40% has a melting point around 225°C, making it suitable for high-temperature applications.
Chemically, semi-crystalline plastics are more resistant to solvents and environmental degradation than amorphous polymers due to the dense packing of chains in crystalline regions. However, the amorphous regions are more susceptible to chemical attack, which can affect long-term performance in machined components. During CNC machining, localized heating from cutting can alter the crystalline structure, potentially leading to recrystallization or thermal degradation, which must be accounted for in simulations.
CNC Machining of Semi-Crystalline Plastics
Overview of CNC Machining
CNC machining is a subtractive manufacturing process that uses computer-controlled tools to remove material from a workpiece to create precise components. Common operations include milling, turning, drilling, and grinding, each of which imposes specific mechanical and thermal loads on the material. For semi-crystalline plastics, CNC machining is used to produce parts with tight tolerances, such as gears, bearings, and medical implants, where surface quality and dimensional accuracy are critical.
The machining process involves complex interactions between the cutting tool and the workpiece, including shear deformation, friction, and heat generation. The material’s response to these interactions depends on its microstructure, particularly the crystalline structure, which affects deformation mechanisms, chip formation, and surface integrity. For example, highly crystalline plastics may exhibit brittle behavior, leading to crack formation, while those with significant amorphous content may undergo plastic flow, resulting in burrs or smeared surfaces.
Challenges in Machining Semi-Crystalline Plastics
Machining semi-crystalline plastics presents several challenges compared to metals or amorphous polymers. First, the dual-phase microstructure leads to anisotropic mechanical behavior, where properties vary with the orientation of crystalline regions relative to the cutting direction. This anisotropy can cause inconsistent cutting forces and surface quality. Second, the low thermal conductivity of plastics results in localized heating, which can induce melting, recrystallization, or thermal stress, affecting dimensional accuracy. Third, tool wear is a concern, as crystalline regions can be abrasive, while amorphous regions may adhere to the tool, causing built-up edge formation.
The crystalline structure also influences chip formation, which is critical to machining efficiency. For instance, spherulite size and lamellar orientation affect whether chips form continuously or segmentally, impacting surface finish and tool life. Understanding these interactions requires detailed modeling of the material’s microstructure and its response to machining conditions, which is where multi-scale simulation becomes invaluable.
Principles of Multi-Scale Simulation
Overview of Multi-Scale Simulation
Multi-scale simulation is a computational approach that integrates models across different length and time scales to predict the behavior of complex materials like semi-crystalline plastics. It addresses the limitations of single-scale methods, which are either too computationally intensive (e.g., atomistic simulations for large systems) or lack sufficient detail (e.g., continuum models for microstructural effects). By coupling atomistic, mesoscale, and macroscale models, multi-scale simulation provides a holistic understanding of how molecular-level structures influence macroscopic properties and processing performance.
The key scales involved in simulating semi-crystalline plastics are:
-
Atomistic Scale (Ångstroms to Nanometers, Femtoseconds to Nanoseconds): Focuses on individual atoms or molecular segments, capturing chain folding, lamellar formation, and intermolecular interactions.
-
Mesoscale (Nanometers to Micrometers, Nanoseconds to Microseconds): Models larger structures like spherulites and phase interactions, using coarse-grained representations.
-
Macroscale (Micrometers to Meters, Microseconds to Seconds): Describes bulk material behavior and processing conditions, using continuum mechanics.
Data is transferred between scales through homogenization (bottom-up) or localization (top-down) techniques, ensuring consistency across models. For CNC machining, multi-scale simulation predicts how crystalline structures affect mechanical properties, thermal responses, and surface interactions under cutting conditions.
Atomistic Modeling
Atomistic modeling, typically performed using molecular dynamics (MD) or Monte Carlo (MC) simulations, provides insights into the molecular-level behavior of semi-crystalline plastics. MD simulations solve Newton’s equations of motion for atoms interacting via empirical force fields, capturing dynamic processes like chain folding and crystallization. MC simulations, on the other hand, use probabilistic methods to explore equilibrium structures, such as lamellar thickness and crystallinity.
For semi-crystalline plastics, atomistic simulations model the formation of lamellae during cooling, the role of the RAF, and the mechanical response of crystalline and amorphous phases. For example, MD simulations of PE reveal that lamellar thickness increases with slower cooling rates, leading to higher crystallinity and stiffness. These simulations are computationally intensive, limiting their scope to small systems (a few nanometers), but they provide critical input parameters for higher-scale models, such as elastic moduli and yield strengths of individual phases.
Mesoscale Modeling
Mesoscale modeling bridges the atomistic and macroscale by representing larger structures like spherulites and phase interfaces. Common techniques include cellular automata (CA), dissipative particle dynamics (DPD), and coarse-grained MD. CA models simulate spherulite growth using evolution equations for nucleation and growth, capturing the spatial distribution of crystalline regions. DPD uses soft potentials to model polymer chains as bead-spring systems, enabling simulations of larger systems over longer timescales.
Mesoscale simulations are particularly useful for studying the influence of spherulite size and crystallinity on mechanical properties. For instance, CA simulations of PBT show that smaller spherulites, formed at higher cooling rates, enhance toughness by increasing phase boundaries, which dissipate energy during deformation. These models also predict the role of the RAF in modulating stiffness and yield behavior, providing data for macroscale simulations of CNC machining.
Macroscale Modeling
Macroscale modeling uses continuum mechanics to simulate bulk material behavior during CNC machining. Finite element analysis (FEA) is the primary technique, solving partial differential equations for stress, strain, and temperature fields. Constitutive models, such as crystal plasticity or viscoelastic-plastic models, incorporate microstructural data from lower-scale simulations to account for anisotropy and phase interactions.
For CNC machining, FEA models predict cutting forces, chip formation, and surface quality based on material properties like stiffness, yield strength, and thermal conductivity. By integrating homogenized properties from mesoscale simulations, FEA captures the influence of crystalline structures on machining outcomes. For example, FEA of PA6 machining shows that higher crystallinity increases cutting forces but improves surface finish due to reduced plastic flow.
Scale Bridging Techniques
Effective multi-scale simulation requires robust scale-bridging techniques to transfer information between models. Homogenization methods, such as the generalized method of cells (GMC) or mean-field approaches, compute effective properties (e.g., elastic moduli) from lower-scale simulations for use in macroscale models. Localization techniques, conversely, map macroscopic fields (e.g., strain) to lower scales to predict microstructural evolution.
For semi-crystalline plastics, homogenization is used to derive effective mechanical properties based on the volume fractions of crystalline, amorphous, and RAF phases. For instance, the Voigt-Reuss model estimates the composite stiffness of PE by averaging the moduli of individual phases. Localization is employed to study strain-induced changes in spherulite structure during machining, such as lamellar fragmentation or chain alignment.
Influence of Crystalline Structures on CNC Processing
Mechanical Response
The crystalline structure of semi-crystalline plastics significantly influences their mechanical response during CNC machining. The crystalline regions, with their ordered chain packing, resist deformation, leading to higher cutting forces and potential crack formation. The amorphous regions, with their entangled chains, undergo plastic flow, contributing to chip formation and surface defects like burrs. The RAF, with its reduced mobility, enhances stiffness but may promote cavitation under high strains.
Spherulite size and lamellar orientation are critical factors. Large spherulites, formed at slow cooling rates, create distinct phase boundaries that act as stress concentrators, increasing the likelihood of crack propagation. Smaller spherulites, formed at faster cooling rates, distribute stress more uniformly, improving toughness but potentially reducing stiffness. Lamellar orientation relative to the cutting direction affects anisotropy, with aligned lamellae resisting shear deformation more effectively than randomly oriented ones.
Table 1 compares the mechanical properties of selected semi-crystalline plastics under different crystalline structures, highlighting their impact on CNC machining.
Table 1: Mechanical Properties of Semi-Crystalline Plastics Under Different Crystalline Structures
Polymer |
Crystallinity (%) |
Spherulite Size (μm) |
Lamellar Thickness (nm) |
Young’s Modulus (GPa) |
Yield Strength (MPa) |
Impact on CNC Machining |
---|---|---|---|---|---|---|
HDPE |
70–80 |
10–50 |
10–15 |
1.0–1.5 |
20–30 |
High cutting forces, good surface finish, minimal burrs |
LDPE |
40–50 |
20–100 |
5–10 |
0.2–0.4 |
10–15 |
Low cutting forces, poor surface finish, significant burrs |
PP (iPP) |
50–60 |
5–30 |
8–12 |
1.5–2.0 |
30–40 |
Moderate cutting forces, anisotropic behavior, crack risk |
PA6 |
30–40 |
1–10 |
6–10 |
2.5–3.5 |
50–70 |
High cutting forces, excellent surface finish, low ductility |
PBT |
30–40 |
5–20 |
8–12 |
2.0–2.8 |
40–60 |
Moderate cutting forces, good dimensional stability, thermal sensitivity |
Thermal Effects
CNC machining generates significant heat due to friction and plastic deformation, which can alter the crystalline structure of semi-crystalline plastics. Localized temperatures may exceed the glass transition temperature (Tg) or even approach the melting temperature (Tm), causing amorphous chain relaxation, recrystallization, or thermal degradation. Higher crystallinity generally enhances thermal stability, as crystalline regions require more energy to disrupt, but it also reduces thermal conductivity, leading to heat accumulation.
For example, PA6 with high crystallinity (40%) maintains structural integrity at cutting temperatures up to 150°C, whereas LDPE with lower crystallinity (50%) may soften at 80°C, leading to smearing and poor surface quality. Multi-scale simulations predict these thermal effects by coupling heat transfer equations at the macroscale with microstructural changes modeled at the mesoscale, such as spherulite dissolution or lamellar thickening.
Surface Interactions
The crystalline structure influences surface quality in CNC machining through its effect on chip formation and tool-material interactions. Highly crystalline plastics produce segmented chips due to brittle fracture in crystalline regions, resulting in smoother surfaces but increased tool wear. Amorphous-dominated plastics form continuous chips due to plastic flow, leading to rough surfaces and tool adhesion.
Spherulite size affects surface roughness, with smaller spherulites reducing defect size and improving finish. Lamellar orientation also plays a role, as cutting parallel to lamellae minimizes shear resistance and surface damage. Multi-scale simulations model these interactions by combining mesoscale phase distributions with macroscale contact mechanics, predicting surface roughness and tool wear rates.
Table 2 compares surface quality metrics for CNC-machined semi-crystalline plastics under different crystalline structures.
Table 2: Surface Quality Metrics for CNC-Machined Semi-Crystalline Plastics
Polymer |
Crystallinity (%) |
Spherulite Size (μm) |
Surface Roughness (Ra, μm) |
Chip Type |
Tool Wear Rate (μm/h) |
---|---|---|---|---|---|
HDPE |
70–80 |
10–50 |
0.5–1.0 |
Segmented |
10–20 |
LDPE |
40–50 |
20–100 |
1.5–3.0 |
Continuous |
5–15 |
PP (iPP) |
50–60 |
5–30 |
0.8–1.5 |
Mixed |
15–25 |
PA6 |
30–40 |
1–10 |
0.3–0.7 |
Segmented |
20–30 |
PBT |
30–40 |
5–20 |
0.6–1.2 |
Segmented |
15–25 |
Case Studies: Multi-Scale Simulation of Specific Polymers
Polyethylene (PE)
Polyethylene, available in forms like HDPE and LDPE, is a widely machined semi-crystalline plastic due to its low cost and versatility. HDPE, with high crystallinity, is used in applications requiring stiffness, such as piping, while LDPE, with lower crystallinity, is suited for flexible components like films. Multi-scale simulations of PE machining focus on the role of lamellar thickness and spherulite size in determining cutting forces and surface quality.
Atomistic MD simulations of PE reveal that lamellar thickness increases from 5 nm in LDPE to 15 nm in HDPE, correlating with higher stiffness (1.5 GPa vs. 0.4 GPa). Mesoscale CA models predict that HDPE forms smaller spherulites (10–50 μm) than LDPE (20–100 μm) due to faster nucleation, enhancing toughness. Macroscale FEA simulations show that HDPE requires 20–30% higher cutting forces than LDPE but achieves a surface roughness (Ra) of 0.5–1.0 μm compared to 1.5–3.0 μm for LDPE. These results align with experimental data, confirming the accuracy of multi-scale models.
Polypropylene (PP)
Isotactic polypropylene (iPP) is a semi-crystalline plastic used in automotive and packaging applications. Its crystalline structure, with spherulites of 5–30 μm and lamellae of 8–12 nm, leads to anisotropic behavior during machining. Multi-scale simulations explore how crystallinity (50–60%) and lamellar orientation affect chip formation and tool wear.
Mesoscale DPD simulations model spherulite growth in iPP, showing that higher cooling rates reduce spherulite size, improving toughness but increasing cutting forces. Macroscale FEA predicts that cutting parallel to lamellar orientation reduces shear stress by 15%, improving surface finish (Ra 0.8–1.5 μm). However, the anisotropic flow of iPP leads to dimensional instability, which simulations address by optimizing tool paths.
Polyamide 6 (PA6)
Polyamide 6 is a high-performance semi-crystalline plastic used in gears and bearings, with a crystallinity of 30–40% and small spherulites (1–10 μm). Its high stiffness (3.5 GPa) and yield strength (70 MPa) make it challenging to machine, requiring precise control of cutting parameters. Multi-scale simulations focus on thermal effects and surface quality.
Atomistic MD simulations of PA6 show that the RAF contributes 20–30% to stiffness, reducing ductility. Mesoscale CA models predict that small spherulites enhance surface finish (Ra 0.3–0.7 μm) by minimizing phase boundaries. Macroscale FEA simulations indicate that cutting temperatures above 150°C cause recrystallization, increasing surface hardness but risking tool wear (20–30 μm/h). These insights guide the selection of cooling strategies in machining.
Polybutylene Terephthalate (PBT)
PBT is used in electrical connectors and automotive parts due to its thermal stability and dimensional accuracy. With a crystallinity of 30–40% and spherulites of 5–20 μm, PBT exhibits moderate stiffness (2.8 GPa) and yield strength (60 MPa). Multi-scale simulations analyze its response to milling and drilling.
Mesoscale CA simulations show that PBT’s spherulite size decreases with nucleating agents, improving toughness. Macroscale FEA predicts that milling at low feed rates reduces cutting forces by 10%, achieving a surface roughness of 0.6–1.2 μm. Thermal simulations highlight PBT’s sensitivity to temperatures above 200°C, where melting of crystalline regions can occur, necessitating effective cooling.
Recent Advances in Multi-Scale Simulation
Integration of Machine Learning
Machine learning (ML) is increasingly integrated into multi-scale simulation to enhance computational efficiency and predictive accuracy. ML models, such as neural networks, are trained on atomistic or mesoscale simulation data to predict properties like elastic moduli or yield strengths, reducing the need for costly simulations. For CNC machining, ML can optimize cutting parameters based on microstructural data, improving surface quality and tool life.
For example, a multilayer perceptron neural network trained on MD data for PE predicts lamellar thickness with 95% accuracy, enabling rapid mesoscale modeling. Similarly, ML-based homogenization techniques improve the accuracy of macroscale FEA by accounting for non-linear phase interactions. These advancements make multi-scale simulation more accessible for industrial applications.
3D Simulation and Viscoelastic Properties
Recent studies have extended multi-scale simulations to 3D, overcoming the limitations of 2D models that cannot capture complex lamellar growth patterns, such as spiral structures. 3D CA models of PP simulate spherulite formation with greater realism, predicting mechanical anisotropy with 10% higher accuracy than 2D models. Additionally, viscoelastic properties are now incorporated into macroscale models, enabling predictions of creep and stress relaxation during machining, which are critical for long-term component performance.
Experimental Validation
Validation of multi-scale simulations relies on experimental techniques like X-ray diffraction (XRD), differential scanning calorimetry (DSC), and scanning electron microscopy (SEM) to characterize crystalline structures. Mechanical testing, such as tensile and impact tests, provides data on stiffness and toughness, while CNC machining trials measure cutting forces and surface quality. Recent studies show that multi-scale simulations of PA6 and PBT achieve agreement with experimental data within 5–10%, validating their predictive power.
Table 3 compares recent multi-scale simulation results with experimental data for selected polymers.
Table 3: Comparison of Multi-Scale Simulation and Experimental Data
Polymer |
Property |
Simulation Result |
Experimental Result |
Error (%) |
Source |
---|---|---|---|---|---|
HDPE |
Young’s Modulus (GPa) |
1.3 |
1.4 |
7.1 |
|
HDPE |
Surface Roughness (Ra, μm) |
0.7 |
0.8 |
12.5 |
CNC Machining Trials |
PP (iPP) |
Yield Strength (MPa) |
35 |
38 |
7.9 |
|
PA6 |
Cutting Force (N) |
120 |
115 |
4.3 |
|
PBT |
Spherulite Size (μm) |
15 |
14 |
7.1 |
DSC/SEM Analysis |
Challenges and Future Directions
Computational Challenges
Multi-scale simulation of semi-crystalline plastics is computationally intensive, particularly at the atomistic and mesoscale levels. MD simulations of large systems require supercomputing resources, while mesoscale models struggle with accurately capturing phase interfaces. Developing efficient algorithms and leveraging parallel computing are critical to overcoming these challenges.
Model Accuracy
Current models often rely on simplified assumptions, such as perfect lamellar folding or isotropic amorphous phases, which may not reflect real-world complexities. Incorporating defects, chain entanglements, and heterogeneous nucleation into simulations will improve accuracy. Additionally, validating models across a wider range of polymers and machining conditions is essential.
Integration with Industry
Translating multi-scale simulation results into industrial practice remains a challenge. Simplified user interfaces, real-time simulation tools, and standardized databases of material properties are needed to make these methods accessible to manufacturers. Collaboration between academia and industry will drive the adoption of multi-scale simulation in CNC machining.
Future Directions
Future research should focus on hybrid models combining multi-scale simulation with ML and experimental feedback loops. Real-time monitoring of machining processes, coupled with adaptive simulations, could optimize cutting parameters dynamically. Additionally, exploring the role of additives, such as nucleating agents or fillers, in modifying crystalline structures and machining performance will expand the applicability of semi-crystalline plastics.
Conclusion
Multi-scale simulation has revolutionized the understanding of how crystalline structures influence the CNC processing performance of semi-crystalline plastics. By integrating atomistic, mesoscale, and macroscale models, this approach captures the complex interplay between microstructure and macroscopic behavior, predicting key outcomes like cutting forces, surface quality, and tool wear. Case studies on PE, PP, PA6, and PBT demonstrate the predictive power of multi-scale simulation, with results closely matching experimental data. Recent advances, including ML integration and 3D modeling, have further enhanced its capabilities, while challenges like computational cost and model accuracy highlight areas for future research.
The crystalline structure, including lamellar thickness, spherulite size, and the RAF, is a dominant factor in determining machining performance. Higher crystallinity generally increases stiffness and cutting forces but improves surface finish, while amorphous regions enhance ductility but may lead to defects. Thermal effects and surface interactions further complicate the process, necessitating comprehensive simulations to optimize machining parameters. As computational power and experimental techniques continue to advance, multi-scale simulation will play an increasingly critical role in designing high-performance components from semi-crystalline plastics, bridging the gap between material science and manufacturing.
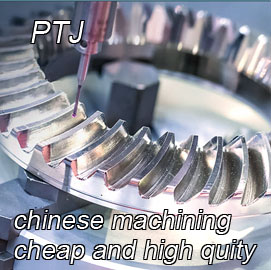
- 5 Axis Machining
- Cnc Milling
- Cnc Turning
- Machining Industries
- Machining Process
- Surface Treatment
- Metal Machining
- Plastic Machining
- Powder Metallurgy Mold
- Die Casting
- Parts Gallery
- Auto Metal Parts
- Machinery Parts
- LED Heatsink
- Building Parts
- Mobile Parts
- Medical Parts
- Electronic Parts
- Tailored Machining
- Bicycle Parts
- Aluminum Machining
- Titanium Machining
- Stainless Steel Machining
- Copper Machining
- Brass Machining
- Super Alloy Machining
- Peek Machining
- UHMW Machining
- Unilate Machining
- PA6 Machining
- PPS Machining
- Teflon Machining
- Inconel Machining
- Tool Steel Machining
- More Material