CNC Machining Technology for Non-Monotonic Shaft Parts
Computer Numerical Control (CNC) machining represents a cornerstone of modern manufacturing, enabling the production of complex components with high precision and efficiency. Among the diverse array of parts produced using CNC technology, shaft parts hold a critical role in industries such as automotive, aerospace, medical, and robotics. Shafts are mechanical components designed to transmit torque, motion, or bending moments, typically characterized by their rotational geometry and cylindrical or conical surfaces. While many shaft parts feature monotonic profiles—where the diameter consistently increases or decreases along the axis—non-monotonic shaft parts present unique challenges due to their irregular, non-linear profiles. These profiles may include features such as grooves, undercuts, raised notches, or variable diameters that do not follow a unidirectional dimensional trend.
Non-monotonic shaft parts are essential in applications requiring intricate mechanical interactions, such as transmission systems, precision surgical tools, and robotic actuators. The complexity of their geometry necessitates advanced CNC machining strategies to achieve dimensional accuracy, surface quality, and functional performance. This article provides a comprehensive analysis of CNC machining technology tailored to non-monotonic shaft parts, exploring the theoretical foundations, technological approaches, process planning, material considerations, and emerging trends. By examining the interplay of machine tools, programming techniques, and quality control measures, this analysis aims to elucidate the state-of-the-art practices and future directions in this specialized domain of manufacturing.
Definition and Characteristics of Non-Monotonic Shaft Parts
Definition
A shaft is a rotating mechanical element, typically with a length greater than its diameter, used to support transmission components, transfer torque, or bear loads. Shaft parts are broadly categorized based on their structural and geometric characteristics, including smooth shafts, stepped shafts, hollow shafts, and special-shaped shafts (e.g., crankshafts, camshafts). Non-monotonic shaft parts are distinguished by their non-linear dimensional profiles, where the diameter or cross-sectional geometry does not follow a consistent increasing or decreasing trend along the longitudinal axis. This non-monotonicity may manifest as raised features, recessed grooves, undercuts, or complex contours that require multi-axis machining or specialized tooling.
Geometric Features
Non-monotonic shaft parts often include the following geometric features:
-
Raised Notches or Ribs: Protrusions extending axially or circumferentially, used for mechanical interlocking or load distribution.
-
Undercuts: Recessed areas that interrupt the shaft’s outer profile, often for fitting bearings or seals.
-
Grooves and Keyways: Slots for accommodating keys, splines, or seals, critical for torque transmission.
-
Variable Diameters: Sections with alternating large and small diameters, creating a stepped or contoured profile.
-
Threads and Splines: Helical or linear features for fastening or power transmission.
-
Complex Contours: Arcuate or irregular surfaces, such as those found in camshafts or eccentric shafts.
These features complicate the machining process, as they require precise toolpath planning, multiple setups, and advanced CNC capabilities to maintain tolerances and surface finish.
Functional Importance
Non-monotonic shaft parts are integral to systems requiring high precision and reliability. In automotive engines, for example, crankshafts with non-monotonic profiles ensure balanced torque delivery. In aerospace, precision shafts in actuators maintain structural integrity under extreme conditions. In medical devices, non-monotonic shafts in surgical tools enable intricate movements with minimal invasiveness. The functional demands of these applications underscore the need for robust CNC machining strategies tailored to non-monotonic geometries.
Fundamentals of CNC Machining Technology
Overview of CNC Machining
CNC machining is a subtractive manufacturing process that uses computer-controlled machine tools to remove material from a workpiece, shaping it into a desired form. The process relies on pre-programmed instructions, typically in the form of G-code and M-code, to dictate tool movements, speeds, and feeds. CNC machines encompass a range of equipment, including lathes, mills, routers, and multi-axis machining centers, each suited to specific tasks. For shaft parts, CNC lathes and turning centers are primary tools, often supplemented by milling or grinding for complex features.
CNC machining offers several advantages for non-monotonic shaft production:
-
Precision: Tolerances as tight as ±0.001 mm can be achieved, critical for high-performance shafts.
-
Automation: Reduces human error and enables consistent production across large volumes.
-
Flexibility: Allows rapid reprogramming for design changes or custom parts.
-
Versatility: Accommodates various materials, from metals to composites.
However, challenges include high setup costs, complex programming for non-monotonic geometries, and the need for skilled operators to optimize processes.
CNC Machine Types for Shaft Machining
Several CNC machine types are employed for non-monotonic shaft parts, each offering distinct capabilities:
Machine Type |
Description |
Applications for Non-Monotonic Shafts |
---|---|---|
CNC Lathe |
Rotates the workpiece against a stationary cutting tool for cylindrical parts. |
Turning outer and inner surfaces, threads, and grooves. |
CNC Turning Center |
Advanced lathe with live tooling for milling, drilling, and multi-axis work. |
Complex contours, keyways, and non-cylindrical features. |
CNC Milling Machine |
Uses rotating tools to remove material from a stationary workpiece. |
Slots, undercuts, and raised features requiring multi-axis machining. |
Multi-Axis CNC |
Combines linear and rotational axes (e.g., 5-axis) for complex geometries. |
Intricate profiles and simultaneous machining of multiple features. |
CNC Grinding Machine |
Employs abrasive wheels for high-precision finishing. |
Achieving tight tolerances and superior surface finish on shafts. |
Key CNC Processes
The machining of non-monotonic shaft parts involves multiple processes, each addressing specific geometric or functional requirements:
-
Turning: Shapes the outer and inner cylindrical surfaces, often the primary process for shafts.
-
Milling: Creates slots, keyways, and non-cylindrical features using rotating cutters.
-
Drilling: Forms holes for mounting or fluid passages.
-
Grinding: Refines surfaces to achieve high dimensional accuracy and smoothness.
-
Threading: Cuts helical threads for fastening or transmission.
-
Knurling: Produces textured surfaces for grip or aesthetic purposes.
For non-monotonic shafts, these processes are often combined in a single setup using multi-axis machines or sequential operations across multiple machines.
Challenges in Machining Non-Monotonic Shaft Parts
Geometric Complexity
The non-monotonic nature of these shafts introduces several machining challenges:
-
Toolpath Complexity: Non-linear profiles require intricate toolpaths, increasing programming time and computational demands.
-
Tool Access: Undercuts and recessed features may be difficult to reach with standard tools, necessitating specialized tooling or multi-axis machines.
-
Collision Risks: Complex geometries increase the likelihood of tool or machine collisions, requiring careful simulation and verification.
-
Multiple Setups: Features on different planes or axes may require repositioning the workpiece, reducing efficiency and introducing alignment errors.
Tolerances and Surface Quality
Non-monotonic shafts often serve in high-precision applications, demanding tight tolerances (e.g., ±0.01 mm) and superior surface finishes (e.g., Ra 0.8 µm or better). Achieving these specifications is challenging due to:
-
Vibration and Deflection: Slender or flexible shafts may vibrate during machining, affecting accuracy.
-
Tool Wear: Hard materials or interrupted cuts accelerate tool wear, compromising surface quality.
-
Thermal Effects: Cutting heat can cause workpiece expansion, leading to dimensional inaccuracies.
-
Residual Stresses: Machining-induced stresses may distort the shaft, particularly in thin-walled or hollow designs.
Material Considerations
Non-monotonic shafts are fabricated from a range of materials, each presenting unique machining challenges:
Material |
Properties |
Machining Challenges |
---|---|---|
Carbon Steel |
High strength, moderate machinability. |
Tool wear, heat generation, achieving fine surface finish. |
Stainless Steel |
Corrosion-resistant, tough. |
High cutting forces, work hardening, poor thermal conductivity. |
Aluminum Alloys |
Lightweight, highly machinable. |
Chip control, burr formation, soft material deformation. |
Titanium Alloys |
High strength-to-weight, heat-resistant. |
Low thermal conductivity, high tool wear, chemical reactivity. |
Exotic Alloys |
Extreme strength, corrosion resistance. |
Very high tool wear, specialized tooling, low machinability. |
Material selection impacts tool choice, cutting parameters, and process planning, requiring careful optimization for non-monotonic geometries.
CNC Machining Strategies for Non-Monotonic Shaft Parts
Process Planning
Effective process planning is critical for machining non-monotonic shaft parts. The process typically follows a structured sequence:
-
Part Analysis: Review drawings to identify geometric features, tolerances, and material properties.
-
Blank Selection: Choose an appropriate blank (e.g., bar stock, forging) based on size and material.
-
Datum Establishment: Define reference surfaces or center holes for positioning.
-
Operation Sequencing: Arrange machining steps (e.g., rough turning, semi-finishing, finishing) to minimize setups and ensure accuracy.
-
Tool Selection: Select tools based on feature geometry, material, and cutting conditions.
-
Parameter Optimization: Set cutting speeds, feeds, and depths to balance efficiency and quality.
-
Simulation and Verification: Use CAM software to simulate toolpaths and detect potential issues.
For non-monotonic shafts, process planning must account for the need to machine features in multiple orientations, often requiring multi-axis machines or indexed setups.
Toolpath Generation
Toolpath generation for non-monotonic shafts leverages Computer-Aided Manufacturing (CAM) software to translate CAD models into G-code. Key considerations include:
-
Profile Following: Toolpaths must accurately follow non-linear contours, often using spline or arc interpolation.
-
Multi-Axis Coordination: Simultaneous control of multiple axes ensures access to complex features.
-
Collision Avoidance: Algorithms detect and prevent tool or workpiece collisions.
-
Optimization: Toolpaths are optimized to minimize machining time, tool changes, and air cutting.
For raised notches or undercuts, specialized toolpaths such as trochoidal milling or contour-parallel paths may be employed to maintain tool life and surface quality.
Multi-Axis Machining
Multi-axis CNC machines (e.g., 4-axis or 5-axis) are particularly suited for non-monotonic shafts, as they allow simultaneous machining of features on different planes. Benefits include:
-
Reduced Setups: Features can be machined in a single setup, improving accuracy and efficiency.
-
Complex Geometries: Enables machining of undercuts, angled slots, and contoured surfaces.
-
Improved Surface Finish: Continuous tool engagement reduces scallops and improves smoothness.
However, multi-axis machining requires advanced programming skills, robust machine rigidity, and precise calibration to avoid errors.
Tooling Solutions
Specialized tooling is often required for non-monotonic shaft features:
Tool Type |
Purpose |
Applications |
---|---|---|
Carbide Inserts |
General turning and milling. |
Roughing and finishing cylindrical surfaces. |
Ball Nose End Mills |
Machining curved or contoured surfaces. |
Arcuate features, complex contours. |
Grooving Tools |
Cutting slots and undercuts. |
Keyways, grooves, and recessed features. |
Thread Mills |
Forming internal and external threads. |
Precision threading with high repeatability. |
Custom Form Tools |
Machining unique profiles. |
Raised notches, specialized contours. |
Tool materials (e.g., carbide, ceramic, CBN) and coatings (e.g., TiN, AlTiN) are selected to enhance durability and performance in challenging materials.
Case Study: Machining a Non-Monotonic Crankshaft
Component Description
A crankshaft, a common non-monotonic shaft part, is used in internal combustion engines to convert linear piston motion into rotational motion. Its geometry includes:
-
Main Journals: Cylindrical surfaces that rotate within bearings.
-
Crank Pins: Offset cylindrical surfaces connected to connecting rods.
-
Counterweights: Raised features to balance rotational forces.
-
Fillets: Radiused transitions to reduce stress concentrations.
-
Oil Passages: Drilled holes for lubrication.
The non-monotonic profile, with varying diameters and offset features, poses significant machining challenges.
Machining Process
The production of a crankshaft typically involves the following steps:
-
Blank Preparation: Forged steel blank is normalized to relieve stresses.
-
Rough Turning: Main journals and crank pins are turned to approximate dimensions.
-
Milling: Counterweights and fillets are machined using multi-axis milling.
-
Drilling: Oil passages are drilled at precise angles.
-
Grinding: Journals are ground to achieve tight tolerances and smooth finishes.
-
Balancing: Dynamic balancing ensures rotational stability.
-
Finishing: Polishing or superfinishing enhances surface quality.
CNC Technology Employed
A 5-axis CNC turning center with live tooling is ideal for crankshaft machining, enabling simultaneous turning and milling. CAM software generates toolpaths to navigate the complex geometry, while in-process metrology ensures dimensional accuracy.
Challenges and Solutions
-
Challenge: Maintaining concentricity between main journals and crank pins.
-
Solution: Use precision center holes as datums and employ in-situ probing.
-
-
Challenge: Machining offset crank pins without vibration.
-
Solution: Utilize steady rests and optimized cutting parameters.
-
-
Challenge: Achieving smooth fillet radii.
-
Solution: Employ ball nose end mills with high-precision toolpaths.
-
Outcome
The crankshaft is produced with tolerances of ±0.005 mm on journal diameters and a surface finish of Ra 0.4 µm, meeting automotive industry standards. The use of multi-axis CNC technology reduces production time by 30% compared to traditional methods.
Material Selection and Its Impact
Common Materials
Non-monotonic shaft parts are manufactured from materials chosen for their mechanical properties and application requirements. Common materials include:
-
Carbon and Alloy Steels: Offer high strength and toughness for automotive and industrial shafts.
-
Stainless Steels: Provide corrosion resistance for medical and marine applications.
-
Aluminum Alloys: Lightweight and machinable for aerospace components.
-
Titanium Alloys: High strength-to-weight ratio for aerospace and medical shafts.
-
Nickel-Based Alloys: Extreme heat and corrosion resistance for specialized applications.
Material Properties and Machining
The following table compares material properties and their impact on CNC machining:
Material |
Hardness (HB) |
Tensile Strength (MPa) |
Machinability |
Key Machining Considerations |
---|---|---|---|---|
AISI 1045 Steel |
180-220 |
600-800 |
Good |
Moderate tool wear, requires coolant. |
316 Stainless Steel |
150-200 |
500-700 |
Moderate |
Work hardening, high cutting forces, sticky chips. |
6061 Aluminum |
95-100 |
300-400 |
Excellent |
Soft material, burr formation, chip control. |
Ti-6Al-4V Titanium |
320-380 |
900-1100 |
Poor |
High tool wear, low thermal conductivity. |
Inconel 718 |
350-450 |
1200-1400 |
Very Poor |
Extreme tool wear, high temperatures, slow speeds. |
Material-Specific Strategies
-
Steels: Use carbide tools with TiAlN coatings and moderate cutting speeds to balance tool life and efficiency.
-
Stainless Steels: Employ high-pressure coolant to reduce heat and prevent work hardening.
-
Aluminum: Use high-speed machining with polished tools to minimize burrs and improve surface finish.
-
Titanium: Opt for low cutting speeds, high feed rates, and ceramic or CBN tools to manage heat and wear.
-
Exotic Alloys: Utilize specialized tools (e.g., PCD) and adaptive machining to adjust parameters dynamically.
Quality Control and Metrology
Dimensional Accuracy
Ensuring dimensional accuracy for non-monotonic shafts involves:
-
In-Process Metrology: Probes and laser scanners measure features during machining to detect deviations.
-
Coordinate Measuring Machines (CMM): Post-process inspection verifies tolerances and geometric relationships.
-
Gauging: Go/no-go gauges and micrometers check critical dimensions.
Surface Finish
Surface finish is critical for reducing friction and wear in shaft applications. Techniques include:
-
Grinding and Polishing: Achieve Ra values as low as 0.2 µm.
-
Superfinishing: Uses abrasive films or stones for mirror-like finishes.
-
Surface Profilometry: Measures roughness parameters (Ra, Rz) to ensure compliance.
Non-Destructive Testing (NDT)
NDT methods ensure internal integrity:
-
Ultrasonic Testing: Detects subsurface defects like cracks or voids.
-
Magnetic Particle Inspection: Identifies surface and near-surface flaws in ferromagnetic materials.
-
Dye Penetrant Testing: Reveals surface cracks in non-porous materials.
Quality Standards
Non-monotonic shafts must comply with standards such as:
-
ISO 8015: Geometric product specifications and tolerancing.
-
ASME Y14.5: Dimensioning and tolerancing for engineering drawings.
-
ISO 4287: Surface texture and roughness measurement.
Advanced Technologies and Trends
Hybrid Manufacturing
Hybrid additive-subtractive manufacturing (HASM) combines 3D printing with CNC machining to produce non-monotonic shafts. Benefits include:
-
Near-Net-Shape Blanks: Reduces material waste and roughing time.
-
Complex Features: Additive processes create intricate internal structures, finished by CNC.
-
Material Flexibility: Supports multi-material shafts with tailored properties.
Challenges include integrating additive and subtractive workflows and ensuring material compatibility.
Artificial Intelligence and Machine Learning
AI and ML enhance CNC machining of non-monotonic shafts by:
-
Toolpath Optimization: Algorithms predict optimal paths to minimize machining time and tool wear.
-
Adaptive Machining: Real-time adjustment of parameters based on sensor data (e.g., cutting forces, temperatures).
-
Predictive Maintenance: Machine learning models forecast tool or machine failures, reducing downtime.
Industry 4.0 Integration
Industry 4.0 principles, such as IoT and digital twins, are transforming shaft machining:
-
IoT Sensors: Monitor machine performance and workpiece conditions in real time.
-
Digital Twins: Virtual models simulate machining processes to optimize parameters and predict outcomes.
-
Cloud-Based CAM: Enables collaborative design and remote process monitoring.
Sustainable Machining
Sustainability is a growing focus, with strategies including:
-
Minimum Quantity Lubrication (MQL): Reduces coolant use while maintaining tool life.
-
Recycled Materials: Incorporates recycled metals to lower environmental impact.
-
Energy-Efficient Machines: Modern CNC systems reduce power consumption.
Comparative Analysis of Machining Approaches
The following table compares CNC machining approaches for non-monotonic shaft parts:
Approach |
Advantages |
Disadvantages |
Best Suited For |
---|---|---|---|
3-Axis CNC |
Cost-effective, widely available, simple setup. |
Limited to simpler geometries, multiple setups. |
Basic shafts with grooves or steps. |
5-Axis CNC |
Single setup, complex geometries, high precision. |
High cost, complex programming, skilled operators. |
Crankshafts, camshafts, eccentric shafts. |
Hybrid Manufacturing |
Reduced waste, complex internal features. |
High initial investment, process integration. |
Custom shafts with internal structures. |
High-Speed Machining |
Faster material removal, improved finish. |
Increased tool wear, higher machine stress. |
High-volume production with tight tolerances. |
Future Directions
The future of CNC machining for non-monotonic shaft parts lies in:
-
Automation Advancements: Fully autonomous machining cells with robotic loading and inspection.
-
Material Innovations: Development of new alloys and composites optimized for CNC processes.
-
Quantum Computing: Potential to revolutionize toolpath optimization and process simulation.
-
Global Standards: Harmonized standards for non-monotonic shaft design and production.
Conclusion
CNC machining of non-monotonic shaft parts is a complex but critical aspect of modern manufacturing, driven by the need for precision, reliability, and efficiency in demanding applications. By leveraging advanced machine tools, sophisticated programming, and innovative technologies, manufacturers can overcome the challenges posed by non-monotonic geometries. As the industry evolves, the integration of AI, hybrid manufacturing, and sustainable practices will further enhance the capabilities and impact of CNC machining, ensuring its continued relevance in producing high-performance shaft components.
Reprint Statement: If there are no special instructions, all articles on this site are original. Please indicate the source for reprinting:https://www.cncmachiningptj.com/,thanks!
3, 4 and 5-axis precision CNC machining services for aluminum machining, beryllium, carbon steel, magnesium, titanium machining, Inconel, platinum, superalloy, acetal, polycarbonate, fiberglass, graphite and wood. Capable of machining parts up to 98 in. turning dia. and +/-0.001 in. straightness tolerance. Processes include milling, turning, drilling, boring, threading, tapping, forming, knurling, counterboring, countersinking, reaming and laser cutting. Secondary services such as assembly, centerless grinding, heat treating, plating and welding. Prototype and low to high volume production offered with maximum 50,000 units. Suitable for fluid power, pneumatics, hydraulics and valve applications. Serves the aerospace, aircraft, military, medical and defense industries.PTJ will strategize with you to provide the most cost-effective services to help you reach your target,Welcome to Contact us ( sales@pintejin.com ) directly for your new project.
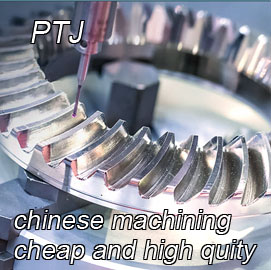
- 5 Axis Machining
- Cnc Milling
- Cnc Turning
- Machining Industries
- Machining Process
- Surface Treatment
- Metal Machining
- Plastic Machining
- Powder Metallurgy Mold
- Die Casting
- Parts Gallery
- Auto Metal Parts
- Machinery Parts
- LED Heatsink
- Building Parts
- Mobile Parts
- Medical Parts
- Electronic Parts
- Tailored Machining
- Bicycle Parts
- Aluminum Machining
- Titanium Machining
- Stainless Steel Machining
- Copper Machining
- Brass Machining
- Super Alloy Machining
- Peek Machining
- UHMW Machining
- Unilate Machining
- PA6 Machining
- PPS Machining
- Teflon Machining
- Inconel Machining
- Tool Steel Machining
- More Material