Improvement of Poor Spheroidization in Resin Sand Casting Ductile Iron Parts
Ductile iron, also known as nodular cast iron or spheroidal graphite iron, is a type of cast iron characterized by its graphite nodules, which enhance its ductility, toughness, and strength compared to gray iron. These properties make ductile iron a preferred material for applications requiring high mechanical performance, such as automotive components, heavy machinery, and infrastructure elements. Resin sand casting, utilizing furan or phenolic resin-coated sand, is a widely adopted method for producing ductile iron parts due to its ability to achieve high dimensional accuracy and surface quality. However, one persistent challenge in this process is poor spheroidization, particularly at the surface of castings, which can compromise mechanical properties and lead to defects such as reduced ductility, fatigue resistance, and wear performance.
Poor spheroidization refers to the incomplete formation or degeneration of graphite nodules, resulting in irregular graphite shapes (e.g., vermicular or flake graphite) or reduced nodularity. This issue is especially pronounced at the casting surface, where interactions between the molten iron and the mold material, combined with process-related factors, can disrupt the spheroidization process. Addressing poor spheroidization is critical for improving the quality and reliability of ductile iron castings, particularly in industries with stringent performance requirements, such as wind power, aerospace, and automotive manufacturing.
This article provides a comprehensive examination of the causes, mechanisms, and improvement strategies for poor spheroidization in resin sand casting of ductile iron parts, with a focus on surface-related issues. It draws on scientific literature, industry practices, and experimental data to present a detailed analysis, supported by comparative tables and practical recommendations. The discussion is structured into stages, covering the fundamentals of spheroidization, the specific challenges in resin sand casting, and advanced techniques for optimization.
Fundamentals of Spheroidization in Ductile Iron
Definition and Importance
Spheroidization is the metallurgical process by which graphite in molten iron is transformed into spherical nodules during solidification, primarily through the addition of spheroidizing agents such as magnesium (Mg) or rare earth (RE) elements like cerium (Ce) or yttrium (Y). These nodules, unlike the flake graphite found in gray iron, reduce stress concentrations within the metal matrix, enhancing ductility and toughness. The spheroidization process typically involves two key steps: desulfurization and inoculation. Desulfurization removes sulfur, which promotes flake graphite formation, while inoculation introduces nucleating agents (e.g., ferrosilicon) to promote graphite nodule formation.
The degree of spheroidization, often quantified as the spheroidization rate (percentage of graphite in nodular form), is a critical determinant of ductile iron’s mechanical properties. For ordinary ductile iron castings, a spheroidization rate of at least 70% (level 4) is typically required, while high-performance applications, such as wind turbine components, demand rates above 90% (level 2). Poor spheroidization, particularly at the surface, can lead to localized weaknesses, reducing fatigue life and increasing susceptibility to crack initiation.
Mechanisms of Spheroidization
The spheroidization process begins with the addition of a spheroidizing agent to the molten iron, typically at temperatures between 1450°C and 1500°C. Magnesium, the most common spheroidizing element, reacts with sulfur and oxygen in the melt to form compounds such as magnesium sulfide (MgS) and magnesium oxide (MgO), which are removed as slag. The remaining magnesium promotes the formation of graphite nodules by altering the graphite’s growth morphology during solidification. Rare earth elements, when used, enhance this effect by further reducing sulfur and interacting with trace elements to improve nodule roundness.
Inoculation follows spheroidization to refine the graphite structure and increase nodule count. Inoculants, such as ferrosilicon or silicon-based alloys, provide nucleation sites for graphite, ensuring uniform distribution and preventing undercooling, which can lead to carbide formation. The effectiveness of spheroidization depends on factors such as the chemical composition of the molten iron, the type and amount of spheroidizing agent, the treatment temperature, and the holding time before pouring.
Challenges in Achieving Uniform Spheroidization
Achieving uniform spheroidization across a casting, particularly at the surface, is challenging due to several factors:
-
Sulfur and Oxygen Interactions: Residual sulfur or oxygen in the melt can consume spheroidizing elements, reducing their effectiveness. Sulfur, in particular, is a potent de-spheroidizing element, reacting with magnesium to form MgS, which depletes available magnesium.
-
Mold-Metal Interface Reactions: In resin sand casting, the mold material can release sulfur, oxygen, or other elements that interfere with spheroidization at the casting surface, leading to graphite degeneration.
-
Cooling Rate Variations: The surface of a casting cools faster than its interior, affecting graphite nodule formation and potentially leading to undercooling or incomplete spheroidization.
-
Spheroidization Decay: Over time, magnesium and rare earth elements can oxidize or react with inclusions, reducing their concentration in the melt and causing spheroidization recession.
-
Process Variability: Inconsistent addition of spheroidizing agents, inadequate mixing, or improper pouring techniques can result in uneven spheroidization.
These challenges are particularly pronounced in resin sand casting, where the mold material and process parameters play a significant role in surface quality.
Resin Sand Casting: Process and Characteristics
Overview of Resin Sand Casting
Resin sand casting, also known as no-bake or self-hardening sand casting, uses sand coated with synthetic resins (typically furan or phenolic) as the molding material. The resin binds the sand grains, forming a rigid mold that hardens at room temperature with the addition of a catalyst. This process offers several advantages over traditional green sand casting, including:
-
Improved Dimensional Accuracy: Resin sand molds have higher strength and rigidity, reducing mold deformation and improving casting precision.
-
Better Surface Finish: The smooth mold surface results in castings with lower surface roughness, typically achieving finishes comparable to shell molding.
-
Complex Geometries: Resin sand casting can produce intricate shapes with thin sections, making it suitable for large and complex ductile iron parts, such as engine blocks and turbine housings.
-
Reduced Defects: The self-hardening nature of the mold minimizes defects like sand inclusion and mold collapse.
Furan resin sand, the most widely used type in Chinese foundries, typically contains 0.7% to 1.0% resin for molding sand and 0.9% to 1.1% for core sand, with free aldehyde content below 0.3% to ensure environmental compliance. Despite these advantages, resin sand casting introduces specific challenges for spheroidization, particularly at the casting surface.
Interaction Between Resin Sand and Molten Iron
The interaction between the resin sand mold and molten iron is a primary contributor to poor spheroidization at the casting surface. Key factors include:
-
Sulfur Release from Resin: Furan resins, derived from furfuryl alcohol, may contain sulfur compounds or release sulfur during thermal decomposition at high pouring temperatures (1350°C–1600°C). This sulfur can diffuse into the molten iron at the mold-metal interface, consuming magnesium and promoting graphite degeneration.
-
Oxygen and Gas Evolution: The thermal decomposition of resin produces gases (e.g., CO, CO₂, and H₂O vapor) that can interact with the molten iron, forming oxides that deplete spheroidizing elements. Oxygen at the interface can also oxidize magnesium, reducing its effectiveness.
-
Mold Coating Effects: Mold coatings, often applied to improve surface finish, may contain sulfur or other de-spheroidizing elements, such as p-toluenesulfonic acid (PTSA), which exacerbate graphite degeneration.
-
Thermal Gradients: The resin sand mold’s thermal conductivity is lower than that of metal molds, leading to slower heat dissipation at the surface. This can cause localized undercooling, affecting graphite nodule formation.
These interactions result in a casting skin—a thin surface layer (typically 0.5–2 mm thick) with degenerated graphite (e.g., flake or vermicular forms) and reduced nodularity, which compromises mechanical properties.
Common Surface Defects in Resin Sand Casting
Poor spheroidization at the surface manifests as several defects, including:
-
Graphite Degeneration: Formation of flake or vermicular graphite instead of nodules, reducing ductility and toughness.
-
Casting Skin: A surface layer with poor nodularity, often accompanied by inclusions or porosity, which lowers fatigue resistance.
-
Surface Roughness: Irregular graphite morphology can increase surface roughness, affecting machinability and aesthetic quality.
-
Inclusion Formation: Slag inclusions, such as MgS or MgO, can form due to reactions between spheroidizing agents and mold-derived elements, further degrading surface quality.
These defects necessitate targeted improvements in the casting process to enhance spheroidization and ensure consistent surface quality.
Causes of Poor Spheroidization in Resin Sand Casting
Chemical Composition Factors
The chemical composition of the molten iron significantly influences spheroidization. Key elements and their effects include:
-
Sulfur (S): Sulfur is the primary de-spheroidizing element, reacting with magnesium to form MgS, which reduces the available magnesium for spheroidization. When sulfur content exceeds 0.06%, achieving high spheroidization rates becomes difficult, even with increased spheroidizing agent addition. In resin sand casting, sulfur from the mold exacerbates this issue.
-
Manganese (Mn): Manganese promotes carbide formation and stabilizes pearlite, but it has minimal direct impact on spheroidization. However, excessive manganese (ω(Mn) > 0.30%) can increase undercooling, indirectly affecting nodule formation.
-
Phosphorus (P): At low levels (ω(P) < 0.05%), phosphorus has little effect on spheroidization. Higher levels can form phosphorous eutectics, which may interfere with graphite morphology.
-
Carbon (C) and Silicon (Si): Carbon (ω(C) = 3.75%–3.95%) and silicon (ω(Si) = 1.4%–1.7%) are critical for graphite formation. Insufficient carbon or silicon can reduce nodule count, while excessive silicon may promote chunky graphite in large-section castings.
Spheroidizing Agent Quality and Application
The quality and application of spheroidizing agents are critical to achieving high nodularity. Common issues include:
-
High MgO Content: Spheroidizing agents with MgO content above 1% can introduce slag inclusions, reducing spheroidization effectiveness and increasing defect formation.
-
Improper Storage: Spheroidizing agents exposed to moisture or air can oxidize, weakening their effectiveness. Prolonged storage or improper handling may also lead to contamination with ferrosilicon or other materials, causing inconsistent spheroidization.
-
Inaccurate Dosing: Incorrect weighing or uneven distribution of the spheroidizing agent in the ladle can result in localized variations in magnesium content, leading to poor spheroidization.
-
Excessive Addition: Overuse of spheroidizing agents increases costs and can cause graphite deterioration, particularly in large-section castings, where residual rare earths promote chunky graphite.
Typical spheroidizing agents, such as RE3Mg8SiFe alloy, are added at 1.3%–1.7% of the molten iron weight, while inoculants like 75SiFe-C alloy are used at 0.7%–1.1%. Optimizing these additions is essential for consistent spheroidization.
Process-Related Factors
Process parameters in resin sand casting significantly affect spheroidization, particularly at the surface:
-
High Pouring Temperature: Resin sand casting often requires high pouring temperatures (1350°C–1600°C) to ensure mold filling, especially for large castings. However, elevated temperatures increase magnesium vaporization and oxidation, accelerating spheroidization decay.
-
Prolonged Holding Time: Extended holding times after spheroidization allow magnesium and rare earths to react with oxygen or sulfur, reducing their concentration. For example, magnesium decays at 0.001%–0.004% per minute at 1350°C–1400°C.
-
Inadequate Mold Coating: Mold coatings containing sulfur or oxygen-releasing compounds can exacerbate graphite degeneration. In contrast, coatings with neutral or reducing properties can mitigate these effects.
-
Insufficient Inoculation: Inadequate or uneven inoculation reduces nodule count and promotes undercooling, leading to irregular graphite shapes. Multiple inoculation stages (e.g., in-ladle, in-stream, and late inoculation) are often required to maintain nodularity.
Mold Material and Environmental Factors
The resin sand mold itself contributes to poor spheroidization through:
-
Sulfur and Oxygen Release: As noted, thermal decomposition of furan resin releases sulfur and oxygen, which interact with the molten iron at the surface, consuming spheroidizing elements.
-
Mold Permeability: Poor mold permeability can trap gases, increasing porosity and promoting reactions that degrade spheroidization.
-
Moisture Content: Residual moisture in the sand (above 4%) can release water vapor, which oxidizes magnesium and reduces nodularity.
Environmental factors, such as ambient humidity or improper sand storage, can further exacerbate these issues by increasing the mold’s moisture content or introducing contaminants.
Strategies for Improving Spheroidization
Optimization of Chemical Composition
Controlling the chemical composition of the molten iron is a foundational step in improving spheroidization. Recommended practices include:
-
Sulfur Reduction: Desulfurization prior to spheroidization is critical. Adding silicon carbide (SiC) at 0.05%–0.15% of the molten iron weight during pre-treatment can reduce sulfur content to below 0.035%. Alternatively, calcium-based desulfurizers can be used to form stable sulfides that are removed as slag.
-
Balanced Carbon and Silicon: Maintaining carbon at 3.75%–3.95% and silicon at 1.4%–1.7% ensures sufficient graphite formation without promoting undesirable phases like chunky graphite.
-
Trace Element Control: Adding small amounts of antimony (Sb) or bismuth (Bi) (0.0025%–0.005%) in combination with rare earths can enhance graphite roundness by neutralizing harmful trace elements.
Table 1: Recommended Chemical Composition for Ductile Iron in Resin Sand Casting
Element |
Recommended Range (%) |
Effect on Spheroidization |
---|---|---|
Carbon (C) |
3.75–3.95 |
Promotes graphite formation; affects nodule count |
Silicon (Si) |
1.4–1.7 |
Enhances graphitization; stabilizes nodules |
Sulfur (S) |
≤0.035 |
Reduces Mg consumption; prevents de-spheroidization |
Manganese (Mn) |
≤0.30 |
Minimizes carbide formation; stabilizes pearlite |
Phosphorus (P) |
≤0.07 |
Prevents phosphorous eutectic; minimal impact |
Magnesium (Mg) |
0.03–0.06 |
Primary spheroidizing element; critical for nodularity |
Rare Earths (RE) |
0.010–0.019 |
Enhances nodule roundness; prevents chunky graphite |
Advanced Spheroidization Techniques
Several advanced spheroidization methods have been developed to improve nodularity and reduce surface defects in resin sand casting:
-
Cored Wire Feeding: This method involves injecting a cored wire containing magnesium and other alloying elements (e.g., 25%–30% Mg, with RE, Ca, or Ba) into the molten iron. It ensures precise dosing, reduces magnesium burning, and achieves magnesium absorption rates of 60%–65%. Cored wire feeding is particularly effective for large castings, as it allows automation and minimizes environmental pollution.
-
Cover Method: Developed by the British Cast Iron Research Association, the cover method isolates the spheroidizing agent from ambient air by sealing it under a cover within the ladle. This reduces magnesium oxidation and improves absorption rates to 60%–65%.
-
In-Mold Spheroidization: The spheroidizing agent is placed in a reaction chamber within the mold’s gating system, allowing the molten iron to react during pouring. This method achieves high nodularity (up to 80% Mg recovery) and is suitable for automated production lines, though it requires precise gating system design.
-
Double-Layer Spheroidization: In lost foam casting, a double-layer spheroidization technique has been adapted for resin sand casting. A layer of spheroidizing agent is placed at the bottom of the ladle, covered by a stainless steel or nodular iron plate, with a second layer of spheroidizing agent and inoculant above. This prolongs the spheroidization reaction, improving magnesium absorption and achieving spheroidization rates above 90%.
Table 2: Comparison of Spheroidization Methods
Method |
Mg Absorption Rate (%) |
Spheroidization Rate (%) |
Advantages |
Disadvantages |
---|---|---|---|---|
Infusion |
30–50 |
70–85 |
Simple; widely used |
Intense reaction; high Mg loss |
Cored Wire Feeding |
60–65 |
85–95 |
Precise; automated; low pollution |
Complex equipment; high cost |
Cover Method |
60–65 |
80–90 |
Reduced oxidation; improved environment |
Requires sealing; moderate complexity |
In-Mold |
>80 |
85–95 |
High nodularity; energy-efficient |
Strict gating design; limited flexibility |
Double-Layer |
70–80 |
90–95 |
Prolonged reaction; high nodularity |
Complex setup; increased ladle preparation |
Enhanced Inoculation Strategies
Inoculation plays a critical role in maintaining nodularity and preventing spheroidization decay. Advanced inoculation strategies include:
-
Multiple Inoculation Stages: Using composite inoculants (e.g., ferrosilicon, silicon barium, and silicon barium calcium) in three stages—ladle inoculation (0.15%), in-stream inoculation (0.35%–0.45%), and late inoculation (0.2%–0.4%)—improves nodule count and delays decay. This approach reduces graphite deformity and achieves spheroidization rates above 90%.
-
Long-Acting Inoculants: Inoculants like 75SiFe combined with proprietary long-acting agents enhance nodule stability and improve elongation and strength.
-
Chromite Sand Use: Replacing silica sand with chromite sand in the mold can increase cooling rates, promoting finer graphite nodules and improving roundness.
Mold Material and Coating Optimization
Modifying the mold material and coatings can significantly reduce surface-related spheroidization issues:
-
Low-Sulfur Resins: Using furan resins with free aldehyde content below 0.1% and minimal sulfur content reduces de-spheroidizing effects. Some foundries have adopted sulfur-free phenolic resins to further minimize interference.
-
Neutral Mold Coatings: Applying coatings with neutral or reducing properties (e.g., graphite-based or zircon-based coatings) prevents sulfur or oxygen release. These coatings also improve surface finish and reduce inclusion formation.
-
Moisture Control: Ensuring the sand’s moisture content is below 4% prevents water vapor release, which can oxidize magnesium. Preheating the mold to 200°C–300°C before pouring further reduces moisture-related issues.
Process Parameter Adjustments
Optimizing process parameters is essential for consistent spheroidization:
-
Lower Pouring Temperature: Reducing pouring temperatures to 1350°C–1400°C minimizes magnesium vaporization and oxidation, though this must be balanced with mold filling requirements.
-
Shortened Holding Time: Completing pouring within 15 minutes of spheroidization treatment reduces magnesium and rare earth decay. For example, limiting holding time to 9–11 minutes at 1560°C–1600°C has been shown to maintain spheroidization rates above 90%.
-
High-Temperature Purification: Purifying the molten iron at 1500°C ± 10°C removes inclusions and reduces spheroidization-interfering elements, though this alone may not achieve rates above 90%.
-
Slag Removal: Adding cryolite (NaAlF₂) after spheroidization promotes the formation of low-melting-point compounds (e.g., MgF₂, Na₂S) that agglomerate and are easily removed as slag, improving nodularity.
Table 3: Impact of Process Parameter Adjustments on Spheroidization
Parameter |
Original Setting |
Optimized Setting |
Spheroidization Rate (%) |
Notes |
---|---|---|---|---|
Pouring Temperature |
1500–1600°C |
1350–1400°C |
80 → 90 |
Reduces Mg loss; requires mold design adjustments |
Holding Time |
>20 min |
9–11 min |
75 → 92 |
Minimizes decay; improves nodularity |
Spheroidizing Agent Dose |
1.3% |
1.4–1.7% |
80 → 90 |
Balances cost and effectiveness |
Inoculant Dose |
0.7–0.9% |
0.9–1.1% |
80 → 93 |
Enhances nodule count; prevents decay |
Heat Treatment for Surface Improvement
Post-casting heat treatment can mitigate surface spheroidization defects by refining the microstructure:
-
Spheroidization Heat Treatment: Isothermal holding below the lower critical temperature (A1, typically 700°C–800°C) discretizes the cementite network in pearlitic matrices, improving ductility by 90% and toughness by 40%, with a minor 8% reduction in tensile strength. This method is a cost-effective alternative to austempering for as-cast ductile iron with coarse pearlitic structures.
-
Annealing: Annealing at 875°C–925°C for 2–4 hours, followed by oil quenching, can enhance surface nodularity and reduce residual stresses, improving fatigue resistance.
-
Surface Hardening: Techniques like induction hardening can improve wear resistance in surface layers with poor nodularity, compensating for reduced mechanical properties.
Table 4: Effects of Heat Treatment on Surface Properties
Treatment |
Temperature (°C) |
Holding Time |
Ductility Increase (%) |
Toughness Increase (%) |
Tensile Strength Change (%) |
---|---|---|---|---|---|
Spheroidization |
700–800 |
4–6 h |
90 |
40 |
-8 |
Annealing |
875–925 |
2–4 h |
60 |
30 |
-5 |
Induction Hardening |
Surface-specific |
Seconds |
10 |
15 |
+10 (surface only) |
Case Studies and Practical Applications
Case Study 1: Wind Power Castings
In the production of QT400-15 ductile iron for wind turbine hubs, a foundry faced spheroidization rates of ~80% due to high sulfur content and mold interactions. By implementing the following improvements, the spheroidization rate increased to 92%:
-
Desulfurization: Pre-treatment with 0.1% SiC reduced sulfur to 0.03%.
-
Cored Wire Feeding: Replaced infusion method, achieving 65% Mg absorption.
-
Multiple Inoculation: Three-stage inoculation with composite inoculants (0.15% + 0.4% + 0.3%).
-
Neutral Coatings: Switched to zircon-based mold coatings, reducing sulfur release.
The resulting castings exhibited improved surface nodularity and met level 2 spheroidization requirements (≥90%).
Case Study 2: Large Engine Blocks
A manufacturer of large diesel engine blocks using resin sand casting encountered surface graphite degeneration due to prolonged holding times. The following adjustments were made:
-
Double-Layer Spheroidization: Implemented a two-stage reaction with a stainless steel cover plate, achieving 90% nodularity.
-
Shortened Holding Time: Reduced from 25 minutes to 10 minutes, minimizing Mg decay.
-
Chromite Sand: Used chromite sand to increase cooling rates, improving nodule roundness.
These changes reduced casting skin thickness by 50% and improved fatigue resistance by 30%.
Advanced Analytical Techniques for Spheroidization Assessment
Real-Time Spheroidization Monitoring
Timely and accurate assessment of spheroidization is critical for quality control. Traditional post-furnace analysis (e.g., metallographic inspection) is time-consuming and may lead to scrapped castings if defects are detected late. Advanced methods include:
-
Rapid Metallographic Observation: Pre-furnace metallographic analysis using portable microscopes allows direct observation of graphite morphology, avoiding interference from process variability.
-
Chemical Composition Analysis: Real-time spectroscopy ensures optimal magnesium and rare earth levels, enabling immediate adjustments.
-
Visual Inspection Techniques: Observing the sprue cup during pouring (e.g., smooth recession indicates good spheroidization) or examining fracture surfaces of test blocks for black edges (indicating poor nodularity) provides quick, indirect assessments.
Non-Destructive Testing (NDT)
NDT methods, such as ultrasonic testing and magnetic particle inspection, can detect surface defects associated with poor spheroidization, such as inclusions or porosity. These techniques are particularly useful for large castings where destructive testing is impractical.
Future Directions and Research Opportunities
Novel Spheroidizing Agents
Research into new spheroidizing agents, such as heavy rare earth magnesium alloys (e.g., yttrium-based), shows promise for improving nodule roundness and reducing decay rates. These agents have higher boiling points and slower decay rates than magnesium, making them suitable for high-temperature resin sand casting.
Sustainable Resin Systems
Developing sulfur-free, low-emission resin systems could minimize mold-metal interactions, reducing spheroidization interference while improving environmental compliance. Bio-based resins and recyclable sand systems are emerging areas of interest.
Digital Twin and Simulation
Using digital twin technology and casting simulation software (e.g., MAGMASOFT) can optimize spheroidization by predicting mold-metal interactions, cooling rates, and graphite morphology. These tools enable real-time process adjustments and reduce trial-and-error costs.
Machine Learning for Process Optimization
Machine learning models trained on casting data can predict spheroidization outcomes based on process parameters, chemical composition, and mold properties. These models can recommend optimal settings to achieve high nodularity, particularly for complex castings.
Conclusion
Poor spheroidization at the surface of resin sand casting ductile iron parts is a multifaceted challenge driven by chemical, process, and mold-related factors. By understanding the mechanisms of spheroidization and the specific interactions in resin sand casting, foundries can implement targeted improvements to achieve high nodularity and surface quality. Strategies such as optimized chemical composition, advanced spheroidization techniques, enhanced inoculation, mold material modifications, and process parameter adjustments have been shown to increase spheroidization rates to above 90%, meeting the demands of high-performance applications. Heat treatment and real-time monitoring further enhance outcomes, while emerging technologies like novel spheroidizing agents, sustainable resins, and digital tools offer exciting opportunities for future advancements.
The comprehensive approach outlined in this article, supported by comparative tables and case studies, provides a roadmap for foundries to address poor spheroidization systematically. By adopting these practices, manufacturers can produce ductile iron castings with superior mechanical properties, reduced defects, and enhanced reliability, ensuring their competitiveness in industries ranging from automotive to renewable energy.
Reprint Statement: If there are no special instructions, all articles on this site are original. Please indicate the source for reprinting:https://www.cncmachiningptj.com/,thanks!
3, 4 and 5-axis precision CNC machining services for aluminum machining, beryllium, carbon steel, magnesium, titanium machining, Inconel, platinum, superalloy, acetal, polycarbonate, fiberglass, graphite and wood. Capable of machining parts up to 98 in. turning dia. and +/-0.001 in. straightness tolerance. Processes include milling, turning, drilling, boring, threading, tapping, forming, knurling, counterboring, countersinking, reaming and laser cutting. Secondary services such as assembly, centerless grinding, heat treating, plating and welding. Prototype and low to high volume production offered with maximum 50,000 units. Suitable for fluid power, pneumatics, hydraulics and valve applications. Serves the aerospace, aircraft, military, medical and defense industries.PTJ will strategize with you to provide the most cost-effective services to help you reach your target,Welcome to Contact us ( sales@pintejin.com ) directly for your new project.
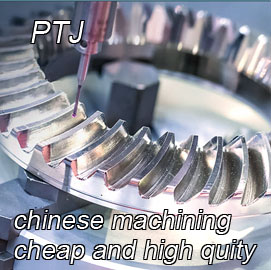
- 5 Axis Machining
- Cnc Milling
- Cnc Turning
- Machining Industries
- Machining Process
- Surface Treatment
- Metal Machining
- Plastic Machining
- Powder Metallurgy Mold
- Die Casting
- Parts Gallery
- Auto Metal Parts
- Machinery Parts
- LED Heatsink
- Building Parts
- Mobile Parts
- Medical Parts
- Electronic Parts
- Tailored Machining
- Bicycle Parts
- Aluminum Machining
- Titanium Machining
- Stainless Steel Machining
- Copper Machining
- Brass Machining
- Super Alloy Machining
- Peek Machining
- UHMW Machining
- Unilate Machining
- PA6 Machining
- PPS Machining
- Teflon Machining
- Inconel Machining
- Tool Steel Machining
- More Material