Application of Automatic Welding in Mechanical Processing
Automatic welding, a pivotal advancement in manufacturing technology, refers to the use of automated systems to perform welding tasks with minimal human intervention. This technology has revolutionized mechanical processing by enhancing precision, efficiency, and safety in the production of components across industries such as automotive, aerospace, construction, and energy. By integrating robotics, computer numerical control (CNC) systems, and advanced sensors, automatic welding has become a cornerstone of modern industrial processes. This article explores the principles, techniques, applications, advantages, challenges, and future prospects of automatic welding in mechanical processing, providing a comprehensive overview of its transformative impact.
Historical Development of Automatic Welding
The origins of automatic welding trace back to the early 20th century, when industrial demands for faster and more consistent production methods spurred innovations in welding technology. Manual welding, reliant on skilled welders, was labor-intensive and prone to inconsistencies. The introduction of mechanized welding processes, such as submerged arc welding (SAW) in the 1930s, marked the first step toward automation. SAW utilized a continuous wire feed and a granular flux to shield the weld, reducing manual effort and improving weld quality.
World War II accelerated the adoption of automatic welding, as industries required rapid production of ships, tanks, and aircraft. The development of gas metal arc welding (GMAW) in the 1940s further enabled automation by providing a versatile and controllable welding process. By the 1960s, the integration of computers and programmable logic controllers (PLCs) allowed for precise control of welding parameters, paving the way for robotic welding systems.
The 1980s saw a significant leap with the introduction of industrial robots equipped with welding torches. Companies like Fanuc and ABB pioneered robotic welding arms capable of performing complex welds with high repeatability. Today, automatic welding systems incorporate artificial intelligence (AI), machine vision, and real-time monitoring, enabling adaptive and intelligent welding processes that meet the stringent requirements of modern mechanical processing.
Principles of Automatic Welding
Automatic welding operates on the principle of delivering a controlled heat source to join materials, typically metals or thermoplastics, using automated equipment. The process involves several key components:
-
Power Source: Supplies the electrical energy needed to generate the welding arc or heat. Common power sources include direct current (DC) or alternating current (AC) systems, depending on the welding technique.
-
Welding Torch or Gun: Directs the heat source (e.g., arc, laser, or plasma) and filler material (if required) to the workpiece.
-
Wire Feeder: Supplies a continuous feed of consumable electrode or filler wire in processes like GMAW or flux-cored arc welding (FCAW).
-
Motion Control System: Guides the welding torch along the weld path, typically using robotic arms, CNC machines, or gantry systems.
-
Sensors and Controllers: Monitor welding parameters (e.g., voltage, current, speed) and adjust them in real time to ensure consistency.
-
Shielding Mechanism: Protects the weld pool from atmospheric contamination using gases (e.g., argon, helium) or fluxes.
Automatic welding systems are designed to execute predefined weld paths, adjust parameters dynamically, and detect defects, ensuring high-quality welds with minimal human oversight.
Types of Automatic Welding Processes
Automatic welding encompasses a variety of processes, each suited to specific materials, geometries, and applications in mechanical processing. The following sections describe the most prominent techniques.
Gas Metal Arc Welding (GMAW)
GMAW, also known as metal inert gas (MIG) welding, uses a continuous wire electrode fed through a welding gun, with an inert or semi-inert gas shielding the weld pool. Its automation is facilitated by wire feeders and robotic arms, making it ideal for high-volume production of steel and aluminum components. GMAW is widely used in automotive manufacturing for welding chassis and body panels.
Gas Tungsten Arc Welding (GTAW)
GTAW, or tungsten inert gas (TIG) welding, employs a non-consumable tungsten electrode and an inert gas shield. Automated GTAW systems are used for precision welding of thin materials, such as stainless steel and titanium, in aerospace and medical device manufacturing. The process is slower than GMAW but offers superior weld quality.
Submerged Arc Welding (SAW)
SAW involves a continuous wire electrode and a granular flux that submerges the arc, preventing atmospheric contamination. Automated SAW systems are used for thick-section welding in shipbuilding and heavy machinery production, offering high deposition rates and deep penetration.
Plasma Arc Welding (PAW)
PAW uses a constricted arc generated by a tungsten electrode, providing high precision and control. Automated PAW is employed in micro-welding applications, such as electronics and aerospace components, where minimal heat-affected zones (HAZ) are critical.
Laser Beam Welding (LBW)
LBW utilizes a focused laser beam to melt and join materials. Automated LBW systems, integrated with CNC or robotic platforms, are used for high-speed, precise welding of thin materials in industries like automotive and electronics. LBW offers low distortion and high weld strength.
Friction Stir Welding (FSW)
FSW is a solid-state welding process that uses a rotating tool to generate frictional heat, joining materials without melting. Automated FSW systems are used in aerospace and railway industries for welding aluminum alloys, providing strong, defect-free welds.
Comparison of Automatic Welding Processes
The following table compares key automatic welding processes based on their characteristics and applications:
Process |
Heat Source |
Materials |
Automation Level |
Applications |
Advantages |
Limitations |
---|---|---|---|---|---|---|
GMAW |
Electric Arc |
Steel, Aluminum |
High |
Automotive, General Fabrication |
High speed, Versatile |
Limited to thicker materials |
GTAW |
Electric Arc |
Stainless Steel, Titanium |
Moderate |
Aerospace, Medical Devices |
High precision, Clean welds |
Slower process |
SAW |
Electric Arc |
Carbon Steel, Low-Alloy Steel |
High |
Shipbuilding, Heavy Machinery |
High deposition rate, Deep penetration |
Limited to flat positions |
PAW |
Plasma Arc |
Thin Metals, Electronics |
Moderate |
Aerospace, Electronics |
Precise, Low HAZ |
Complex equipment |
LBW |
Laser Beam |
Thin Metals, Plastics |
High |
Automotive, Electronics |
High speed, Low distortion |
High initial cost |
FSW |
Frictional Heat |
Aluminum, Magnesium |
High |
Aerospace, Railways |
Strong welds, No filler needed |
Limited to specific alloys |
Applications in Mechanical Processing
Automatic welding has transformed mechanical processing by enabling the production of complex, high-quality components with unprecedented efficiency. The following sections highlight its applications across key industries.
Automotive Industry
The automotive sector relies heavily on automatic welding for assembling vehicle bodies, chassis, and powertrain components. Robotic GMAW and LBW systems are used to weld steel and aluminum parts, ensuring structural integrity and weight reduction. For example, Tesla’s Gigafactory employs hundreds of welding robots to produce battery packs and vehicle frames, achieving high throughput and consistency.
Automatic welding also supports the production of electric vehicle (EV) components, such as battery enclosures and motor housings, where precision and reliability are paramount. The integration of vision systems allows robots to adapt to variations in part geometry, reducing defects and scrap rates.
Aerospace Industry
In aerospace, automatic welding is critical for manufacturing airframes, engines, and structural components. GTAW and FSW are used to weld lightweight alloys like titanium and aluminum, which require high strength and fatigue resistance. For instance, Boeing uses automated FSW to join aluminum panels for the 787 Dreamliner, achieving seamless welds that enhance fuel efficiency.
Laser welding is employed for micro-welding tasks, such as joining turbine blades and sensor components. The use of adaptive control systems ensures compliance with stringent aerospace standards, such as those set by the Federal Aviation Administration (FAA).
Energy Sector
The energy industry utilizes automatic welding for fabricating pipelines, pressure vessels, and wind turbine towers. SAW is commonly used for longitudinal and circumferential welds in large-diameter pipes, ensuring leak-proof joints. In nuclear power plants, automated GTAW systems weld reactor components, where weld imperfections could have catastrophic consequences.
Renewable energy applications, such as solar panel frames and wind turbine blades, benefit from LBW and FSW, which provide high-strength welds with minimal thermal distortion.
Construction and Heavy Machinery
Automatic welding is integral to the construction of bridges, cranes, and excavators. SAW and GMAW systems are used to weld thick steel plates, ensuring structural stability. For example, the fabrication of offshore oil platforms involves automated SAW to join massive steel sections, with real-time monitoring to detect porosity or cracks.
Electronics and Medical Devices
In electronics, automated LBW and PAW are used to weld micro-components, such as circuit boards and sensors, where precision is critical. Similarly, the medical device industry employs GTAW and LBW to manufacture implants and surgical instruments, ensuring biocompatibility and sterility.
Advantages of Automatic Welding in Mechanical Processing
Automatic welding offers numerous benefits over manual welding, making it indispensable in mechanical processing:
-
Enhanced Productivity: Automated systems operate continuously, reducing downtime and increasing output. For example, a robotic GMAW cell can weld hundreds of parts per hour, compared to a manual welder’s dozens.
-
Consistency and Quality: Precise control of welding parameters ensures uniform welds, minimizing defects like porosity, cracks, or incomplete fusion.
-
Cost Efficiency: While initial setup costs are high, automation reduces labor costs and material waste, leading to long-term savings.
-
Safety: By removing human operators from hazardous environments, automatic welding reduces the risk of burns, fumes, and radiation exposure.
-
Flexibility: Modern systems can be reprogrammed to handle different parts and materials, supporting diverse production needs.
-
Data Integration: Automated systems generate data on weld quality and process parameters, enabling predictive maintenance and quality assurance.
Challenges and Limitations
Despite its advantages, automatic welding faces several challenges:
-
High Initial Investment: The cost of robotic systems, sensors, and software can be prohibitive for small and medium-sized enterprises (SMEs).
-
Complexity of Setup: Programming and calibrating automated systems require skilled technicians and significant time.
-
Material Limitations: Certain materials, such as high-strength composites, are difficult to weld automatically due to their properties.
-
Maintenance Requirements: Automated systems require regular maintenance to ensure optimal performance, adding to operational costs.
-
Lack of Adaptability: While advanced systems use AI and vision, some applications still require human judgment for complex or irregular welds.
Technological Advancements in Automatic Welding
Recent advancements have further enhanced the capabilities of automatic welding:
Artificial Intelligence and Machine Learning
AI and machine learning enable adaptive welding systems that optimize parameters in real time. For example, AI algorithms analyze sensor data to adjust arc voltage or travel speed, compensating for material variations. Companies like Siemens and General Electric are integrating AI into welding systems to improve defect detection and process efficiency.
Machine Vision and Sensors
Machine vision systems, equipped with cameras and laser scanners, enable robots to detect part misalignments and adjust weld paths dynamically. Sensors monitor weld pool temperature, arc stability, and gas flow, ensuring consistent quality. For instance, Fanuc’s iRVision system allows robots to perform seam tracking with sub-millimeter accuracy.
Collaborative Robots (Cobots)
Cobots, designed to work alongside human operators, are gaining traction in SMEs. These robots are easier to program and more affordable than traditional industrial robots, making automatic welding accessible to smaller manufacturers.
Additive Manufacturing Integration
Automatic welding is increasingly used in additive manufacturing (AM), where wire arc additive manufacturing (WAAM) builds 3D metal structures layer by layer. WAAM combines GMAW or GTAW with robotic motion control, enabling the production of large, complex components with reduced material waste.
Comparison of Traditional vs. Advanced Automatic Welding Systems
Feature |
Traditional Systems |
Advanced Systems |
---|---|---|
Control Method |
Pre-programmed paths |
AI-driven adaptive control |
Defect Detection |
Manual inspection |
Real-time sensor monitoring |
Setup Time |
High (hours to days) |
Reduced (minutes to hours) |
Flexibility |
Limited to specific tasks |
Multi-tasking with reprogrammable software |
Cost |
High initial, moderate maintenance |
Higher initial, lower long-term costs |
Applications |
Mass production |
Mass production, prototyping, AM |
Economic and Environmental Impacts
Automatic welding has significant economic and environmental implications. Economically, it drives competitiveness by reducing production costs and enabling high-volume manufacturing. For example, the automotive industry’s adoption of robotic welding has lowered vehicle prices while improving quality.
Environmentally, automatic welding reduces energy consumption and material waste compared to manual processes. Optimized weld parameters minimize overwelding, and advanced shielding gases reduce emissions. However, the energy-intensive nature of some processes, like LBW, and the disposal of robotic equipment pose environmental challenges.
Case Studies
Case Study 1: Volkswagen’s Wolfsburg Plant
Volkswagen’s Wolfsburg plant in Germany employs over 1,000 welding robots to produce Golf and Tiguan models. The plant uses a combination of GMAW and LBW, with vision systems ensuring precise welds on complex geometries. The automation has increased production capacity by 30% and reduced defects by 25%, demonstrating the scalability of automatic welding.
Case Study 2: SpaceX’s Starship Program
SpaceX utilizes automated GTAW and FSW to fabricate stainless steel components for its Starship rocket. The use of robotic welding arms has enabled rapid prototyping and production, with welds meeting NASA’s stringent standards. The integration of AI-driven defect detection has reduced rework by 40%.
Case Study 3: Small-Scale Manufacturer
A small U.S.-based manufacturer of agricultural equipment adopted cobots for GMAW, reducing setup costs by 50% compared to traditional robots. The cobots’ ease of programming allowed the company to switch between product lines quickly, improving market responsiveness.
Future Prospects
The future of automatic welding in mechanical processing is promising, driven by ongoing innovations:
-
Industry 4.0 Integration: The integration of automatic welding with the Internet of Things (IoT) and cloud computing will enable real-time data sharing and predictive analytics, optimizing production workflows.
-
Sustainable Welding: Advances in low-energy welding processes and recyclable materials will reduce the environmental footprint of automatic welding.
-
Human-Robot Collaboration: The development of intuitive interfaces and augmented reality (AR) will enhance collaboration between humans and robots, making automation more accessible.
-
Expansion to New Materials: Research into welding ceramics, composites, and dissimilar materials will broaden the scope of automatic welding applications.
-
Global Adoption: As costs decrease and training programs expand, automatic welding will become more prevalent in developing economies, boosting global manufacturing capacity.
Conclusion
Automatic welding has fundamentally reshaped mechanical processing by delivering unparalleled precision, efficiency, and scalability. From automotive assembly lines to aerospace fabrication, its applications span critical industries, driving economic growth and technological innovation. While challenges like high costs and maintenance persist, advancements in AI, machine vision, and collaborative robotics are overcoming these barriers, paving the way for a future where automatic welding is ubiquitous. As industries continue to embrace automation, the role of automatic welding in shaping the next generation of manufacturing cannot be overstated.
Reprint Statement: If there are no special instructions, all articles on this site are original. Please indicate the source for reprinting:https://www.cncmachiningptj.com/,thanks!
3, 4 and 5-axis precision CNC machining services for aluminum machining, beryllium, carbon steel, magnesium, titanium machining, Inconel, platinum, superalloy, acetal, polycarbonate, fiberglass, graphite and wood. Capable of machining parts up to 98 in. turning dia. and +/-0.001 in. straightness tolerance. Processes include milling, turning, drilling, boring, threading, tapping, forming, knurling, counterboring, countersinking, reaming and laser cutting. Secondary services such as assembly, centerless grinding, heat treating, plating and welding. Prototype and low to high volume production offered with maximum 50,000 units. Suitable for fluid power, pneumatics, hydraulics and valve applications. Serves the aerospace, aircraft, military, medical and defense industries.PTJ will strategize with you to provide the most cost-effective services to help you reach your target,Welcome to Contact us ( sales@pintejin.com ) directly for your new project.
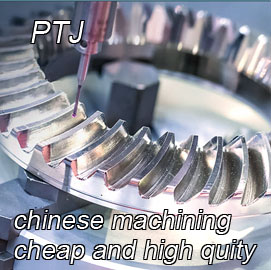
- 5 Axis Machining
- Cnc Milling
- Cnc Turning
- Machining Industries
- Machining Process
- Surface Treatment
- Metal Machining
- Plastic Machining
- Powder Metallurgy Mold
- Die Casting
- Parts Gallery
- Auto Metal Parts
- Machinery Parts
- LED Heatsink
- Building Parts
- Mobile Parts
- Medical Parts
- Electronic Parts
- Tailored Machining
- Bicycle Parts
- Aluminum Machining
- Titanium Machining
- Stainless Steel Machining
- Copper Machining
- Brass Machining
- Super Alloy Machining
- Peek Machining
- UHMW Machining
- Unilate Machining
- PA6 Machining
- PPS Machining
- Teflon Machining
- Inconel Machining
- Tool Steel Machining
- More Material