Precision in CNC Machine Tools: Causes and Strategies
Computer Numerical Control (CNC) machine tools are pivotal in modern manufacturing, enabling the production of complex components with high precision and repeatability. The precision of CNC machines is a critical factor that determines the quality of machined parts, influencing industries such as aerospace, automotive, medical device manufacturing, and electronics. Precision in this context refers to the ability of a CNC machine to produce parts within specified dimensional tolerances and surface finish requirements consistently. Achieving and maintaining this precision involves understanding the multifaceted causes of inaccuracies and implementing strategies to mitigate them. This article explores the causes of precision variations in CNC machine tools, the factors influencing their accuracy, and the comprehensive strategies employed to enhance and sustain precision. It also includes comparative tables to elucidate key concepts and technical specifications.
Fundamentals of CNC Machine Tool Precision
CNC machine tools operate by executing programmed instructions to control the movement of cutting tools and workpieces. Precision in CNC machining is quantified through metrics such as dimensional accuracy, positional accuracy, repeatability, and surface finish quality. Dimensional accuracy refers to how closely the machined part matches the specified dimensions, while positional accuracy indicates the machine's ability to move to a programmed coordinate. Repeatability measures the consistency of achieving the same result across multiple operations, and surface finish pertains to the texture and quality of the machined surface.
The precision of CNC machines is influenced by a combination of mechanical, thermal, environmental, and operational factors. These factors interact in complex ways, making precision management a multidisciplinary challenge. For instance, mechanical inaccuracies may stem from component wear or misalignment, while thermal effects can cause expansion or contraction of machine components. Environmental conditions, such as vibrations or humidity, and operational parameters, like tool wear or programming errors, further complicate the precision landscape.
Key Metrics of Precision
To provide a structured understanding, the following table summarizes the primary metrics of CNC machine precision and their definitions:
Metric |
Definition |
Typical Tolerance Range |
Measurement Method |
---|---|---|---|
Dimensional Accuracy |
Deviation of machined part dimensions from nominal specifications |
±0.001 mm to ±0.1 mm |
Coordinate Measuring Machine (CMM) |
Positional Accuracy |
Error in reaching a programmed coordinate in the machine’s workspace |
±0.002 mm to ±0.05 mm |
Laser Interferometry |
Repeatability |
Variation in achieving the same position or dimension over multiple cycles |
±0.001 mm to ±0.01 mm |
Statistical Analysis of Repeated Trials |
Surface Finish |
Quality of the machined surface, measured as roughness (Ra) |
0.1 µm to 3.2 µm |
Surface Profilometer |
These metrics serve as benchmarks for evaluating CNC machine performance and guide the development of strategies to enhance precision.
Causes of Precision Variations in CNC Machine Tools
Precision variations in CNC machine tools arise from multiple sources, which can be broadly categorized into mechanical, thermal, environmental, and operational factors. Each category encompasses specific issues that contribute to inaccuracies, and understanding these causes is essential for devising effective mitigation strategies.
Mechanical Factors
Mechanical factors are among the primary contributors to precision variations in CNC machines. These factors relate to the physical components of the machine, including its structure, bearings, guideways, and drive systems.
1. Geometric Errors
Geometric errors occur due to imperfections in the machine’s construction, such as non-perpendicularity of axes, misalignment of guideways, or inaccuracies in the spindle. These errors lead to deviations in the tool path, affecting dimensional and positional accuracy. For example, a lack of squareness between the X and Y axes can cause angular errors in machined features.
2. Backlash
Backlash is the play or clearance between mating components, such as gears or ball screws, in the machine’s drive system. When the direction of motion reverses, backlash can cause a delay in tool movement, resulting in positional inaccuracies. High-precision CNC machines often use preloaded ball screws or direct-drive systems to minimize backlash.
3. Component Wear
Over time, mechanical components such as bearings, guideways, and spindles experience wear, leading to increased friction, vibration, and reduced precision. For instance, worn bearings in the spindle can cause runout, where the tool or workpiece wobbles, compromising surface finish and dimensional accuracy.
4. Structural Deformation
The rigidity of the machine’s structure is critical for maintaining precision under cutting forces. Insufficient stiffness can lead to deflection or deformation of the machine bed, columns, or spindle, particularly during heavy-duty machining. This deformation alters the relative position of the tool and workpiece, introducing errors.
Thermal Factors
Thermal effects are a significant source of precision variations in CNC machines. Temperature changes, whether from internal heat sources (e.g., motors, bearings) or external environmental conditions, cause thermal expansion or contraction of machine components, leading to dimensional inaccuracies.
1. Thermal Expansion
Materials used in CNC machines, such as steel or cast iron, expand or contract with temperature changes. For example, a 1°C increase in temperature can cause a steel component to expand by approximately 12 µm per meter. If the spindle or machine bed expands unevenly, the tool’s position relative to the workpiece shifts, affecting accuracy.
2. Heat Generation
Heat is generated during machining due to friction in bearings, motors, and the cutting process itself. For instance, high-speed spindles can generate significant heat, causing localized expansion of the spindle housing. This alters the tool’s position and affects precision, particularly in long-duration machining operations.
3. Thermal Gradients
Non-uniform temperature distributions, or thermal gradients, across the machine structure exacerbate precision issues. For example, if one side of the machine bed is warmer than the other due to proximity to a heat source, the bed may warp, misaligning the axes and causing geometric errors.
Environmental Factors
The operating environment of CNC machines plays a crucial role in their precision. External conditions, such as temperature, humidity, and vibrations, can introduce errors that are challenging to control.
1. Ambient Temperature Variations
Fluctuations in shop floor temperature affect the machine’s components and the workpiece. For instance, a sudden change in ambient temperature can cause the workpiece to expand or contract during machining, leading to dimensional inaccuracies.
2. Vibrations
Vibrations from nearby machinery, floor traffic, or even the CNC machine itself (e.g., unbalanced spindles) can induce errors. These vibrations cause the tool or workpiece to oscillate, compromising surface finish and dimensional accuracy.
3. Humidity and Dust
High humidity can lead to corrosion of machine components, while dust and debris can accumulate on guideways or sensors, affecting smooth operation and precision. In precision machining, even small contaminants can cause significant errors.
Operational Factors
Operational factors encompass the human, programming, and tool-related aspects of CNC machining that influence precision.
1. Programming Errors
Incorrect or suboptimal CNC programs can lead to precision issues. For example, errors in tool path calculations, incorrect feed rates, or improper compensation for tool wear can result in dimensional inaccuracies. Additionally, inadequate post-processing of CAD/CAM files may introduce errors during program execution.
2. Tool Wear
Cutting tools wear over time due to friction and heat, altering their geometry and cutting performance. Worn tools can produce oversized or undersized features, rough surfaces, and chatter marks, all of which degrade precision. Tool wear is particularly critical in high-precision applications like micromachining.
3. Operator Skill
The skill and experience of the machine operator influence precision. Improper setup, such as incorrect workpiece fixturing or tool calibration, can introduce errors. Additionally, failure to monitor machining conditions or adjust parameters in response to tool wear can compromise accuracy.
4. Cutting Parameters
Inappropriate cutting parameters, such as excessive feed rates, spindle speeds, or depth of cut, can lead to precision issues. For example, high feed rates may cause tool deflection or vibration, while excessive cutting forces can deform the workpiece or machine structure.
Comparative Analysis of Causes
The following table compares the major causes of precision variations, their impact, and typical mitigation approaches:
Cause |
Category |
Impact on Precision |
Typical Mitigation |
---|---|---|---|
Geometric Errors |
Mechanical |
Angular and positional inaccuracies |
Precision alignment, regular calibration |
Backlash |
Mechanical |
Positional errors during direction reversal |
Preloaded ball screws, direct-drive systems |
Component Wear |
Mechanical |
Vibration, runout, reduced accuracy |
Preventive maintenance, wear-resistant materials |
Structural Deformation |
Mechanical |
Deflection under cutting forces |
Enhanced rigidity, finite element analysis (FEA) |
Thermal Expansion |
Thermal |
Dimensional inaccuracies |
Thermal compensation, cooling systems |
Heat Generation |
Thermal |
Localized expansion, tool misalignment |
Active cooling, heat shields |
Thermal Gradients |
Thermal |
Warping, axis misalignment |
Uniform temperature control, insulation |
Ambient Temperature |
Environmental |
Workpiece and machine expansion |
Climate-controlled shops |
Vibrations |
Environmental |
Surface finish degradation, positional errors |
Vibration isolation, balanced components |
Humidity and Dust |
Environmental |
Corrosion, sensor errors |
Cleanroom conditions, regular cleaning |
Programming Errors |
Operational |
Incorrect tool paths, dimensional errors |
CAM software validation, simulation |
Tool Wear |
Operational |
Dimensional inaccuracies, poor surface finish |
Tool condition monitoring, timely replacement |
Operator Skill |
Operational |
Setup errors, improper adjustments |
Training, standardized procedures |
Cutting Parameters |
Operational |
Tool deflection, vibration, deformation |
Optimized parameters, adaptive control |
This table highlights the diversity of precision challenges and the need for targeted strategies to address each cause.
Strategies for Enhancing CNC Machine Tool Precision
Achieving and maintaining high precision in CNC machine tools requires a combination of design improvements, advanced technologies, operational best practices, and environmental controls. The following sections detail the strategies employed to mitigate the causes of precision variations and enhance overall accuracy.
Mechanical Design and Construction
The mechanical design of CNC machines is foundational to their precision. High-precision machines incorporate advanced materials, robust structures, and precision components to minimize errors.
1. High-Rigidity Structures
To reduce structural deformation, CNC machines are designed with high-rigidity materials, such as cast iron or granite, which offer excellent damping and stability. Finite element analysis (FEA) is used during the design phase to optimize the machine’s structure, ensuring minimal deflection under cutting forces. For example, box-type machine beds with reinforced ribs enhance rigidity and reduce vibration.
2. Precision Guideways and Bearings
Linear guideways with low friction and high stiffness are used to ensure smooth and accurate motion. Roller-type or hydrostatic guideways are preferred in high-precision machines due to their superior load capacity and damping properties. Similarly, high-precision angular contact bearings or aerostatic bearings are employed in spindles to minimize runout and vibration.
3. Backlash Elimination
To eliminate backlash, modern CNC machines use preloaded ball screws or linear motors. Linear motors, which provide direct-drive motion without mechanical transmission, offer exceptional accuracy and responsiveness, particularly in high-speed machining applications. For example, linear motor-driven CNC machines can achieve positional accuracies below ±0.001 mm.
4. Error Compensation Mechanisms
Geometric errors are mitigated through hardware and software compensation. Hardware solutions include precision alignment during assembly and the use of laser interferometry for calibration. Software-based error compensation involves mapping the machine’s kinematic errors and adjusting tool paths in real-time to correct for deviations. For instance, volumetric error compensation (VEC) accounts for errors across the entire workspace, improving overall accuracy.
Thermal Management
Thermal management is critical for maintaining precision in CNC machines, particularly in high-speed or long-duration operations. Strategies focus on minimizing heat generation, dissipating heat effectively, and compensating for thermal effects.
1. Active Cooling Systems
Active cooling systems, such as liquid-cooled spindles and machine beds, are used to dissipate heat generated during machining. For example, coolant circulated through the spindle housing maintains a stable temperature, reducing thermal expansion. Similarly, temperature-controlled oil or air systems cool guideways and bearings, ensuring consistent performance.
2. Thermal Compensation Algorithms
Advanced CNC controllers incorporate thermal compensation algorithms that adjust tool positions based on real-time temperature measurements. Sensors embedded in the machine structure monitor temperature changes, and the control system applies corrections to account for thermal expansion. For instance, a 0.01 mm expansion in the spindle can be offset by adjusting the tool’s Z-axis position.
3. Thermal Isolation
To minimize the impact of external heat sources, CNC machines are equipped with thermal shields or insulation. For example, enclosing the machine in a temperature-controlled cabinet isolates it from ambient temperature fluctuations. Additionally, separating heat-generating components, such as motors, from the machine’s precision-critical areas reduces thermal gradients.
4. Warm-Up Cycles
Before machining, CNC machines often undergo warm-up cycles to stabilize their temperature. During this process, the spindle and axes are operated at low speeds to distribute heat evenly, minimizing thermal gradients. Warm-up cycles are particularly important for ultra-precision machining, where even small temperature variations can cause significant errors.
Environmental Controls
Controlling the operating environment is essential for maintaining CNC machine precision, particularly in high-precision industries like aerospace and medical device manufacturing.
1. Climate-Controlled Facilities
Precision CNC machines are often housed in climate-controlled shops where temperature and humidity are tightly regulated. For example, a temperature variation of ±1°C and humidity of 40–60% are typical requirements for high-precision machining. Air-conditioned cleanrooms with HEPA filtration further reduce dust and contaminants.
2. Vibration Isolation
To mitigate vibrations, CNC machines are mounted on vibration-damping foundations or active isolation systems. These systems use pneumatic or piezoelectric actuators to counteract external vibrations in real-time. Additionally, balancing spindles and tools minimizes internal vibrations, improving surface finish and accuracy.
3. Cleanroom Conditions
In industries requiring ultra-precision, such as semiconductor manufacturing, CNC machines operate in cleanrooms with stringent dust and particle control. Regular cleaning of guideways, sensors, and workpieces prevents contaminants from affecting precision. For example, a single dust particle on a guideway can cause a positional error of several micrometers.
Operational Best Practices
Operational strategies focus on optimizing programming, tool management, operator training, and cutting parameters to enhance precision.
1. Advanced CAM Software
Computer-Aided Manufacturing (CAM) software plays a crucial role in generating accurate tool paths. Modern CAM systems simulate machining processes to identify potential errors, such as collisions or tool deflection, before execution. Additionally, adaptive tool path strategies, such as trochoidal milling, reduce cutting forces and improve precision in complex geometries.
2. Tool Condition Monitoring
Real-time tool condition monitoring (TCM) systems use sensors to detect tool wear, breakage, or deflection during machining. For example, acoustic emission sensors can identify changes in cutting sound, indicating tool wear. TCM systems enable timely tool replacement or parameter adjustment, ensuring consistent precision.
3. Operator Training
Comprehensive operator training programs emphasize proper machine setup, tool calibration, and process monitoring. Operators are trained to recognize signs of precision issues, such as chatter marks or dimensional deviations, and take corrective actions. Standardized operating procedures (SOPs) further ensure consistency across shifts.
4. Optimized Cutting Parameters
Selecting optimal cutting parameters, such as feed rate, spindle speed, and depth of cut, is critical for precision. For example, lower feed rates and shallower cuts reduce tool deflection and vibration, improving surface finish. Adaptive control systems automatically adjust parameters based on real-time feedback, such as cutting force or tool temperature.
Advanced Technologies for Precision Enhancement
Emerging technologies are revolutionizing CNC machine precision, enabling unprecedented levels of accuracy and repeatability.
1. Ultra-Precision Machine Tools
Ultra-precision CNC machines, designed for applications like optics and semiconductor manufacturing, achieve accuracies below ±0.0001 mm. These machines use diamond-turning tools, aerostatic spindles, and granite beds to minimize errors. For example, a diamond-turning lathe can produce mirror-like surfaces with roughness (Ra) below 0.01 µm.
2. In-Process Metrology
In-process metrology integrates measurement systems, such as laser scanners or touch probes, into the CNC machine. These systems measure the workpiece during machining, allowing real-time adjustments to maintain precision. For instance, a laser scanner can detect a 0.001 mm deviation in a machined feature and correct the tool path accordingly.
3. Artificial Intelligence and Machine Learning
Artificial intelligence (AI) and machine learning (ML) are increasingly used to optimize CNC machining. AI algorithms predict tool wear, thermal expansion, or vibration based on historical data and sensor inputs, enabling proactive corrections. For example, an ML model can adjust cutting parameters to minimize surface roughness in real-time.
4. Hybrid Manufacturing
Hybrid manufacturing combines additive and subtractive processes in a single CNC machine, offering unique precision advantages. For instance, a hybrid machine can 3D-print a near-net-shape part and then machine it to tight tolerances, reducing material waste and improving accuracy in complex geometries.
Comparative Analysis of Precision Strategies
The following table compares key strategies for enhancing CNC machine precision, their benefits, and implementation challenges:
Strategy |
Category |
Benefits |
Challenges |
---|---|---|---|
High-Rigidity Structures |
Mechanical |
Reduced deformation, improved stability |
Higher cost, increased machine weight |
Precision Guideways/Bearings |
Mechanical |
Smoother motion, higher accuracy |
Expensive components, maintenance complexity |
Backlash Elimination |
Mechanical |
Eliminated positional errors |
Cost of linear motors, retrofit difficulties |
Error Compensation |
Mechanical |
Corrected geometric errors |
Requires calibration, software complexity |
Active Cooling Systems |
Thermal |
Stable temperatures, reduced expansion |
Energy consumption, maintenance of cooling systems |
Thermal Compensation |
Thermal |
Real-time correction of thermal errors |
Sensor accuracy, computational overhead |
Thermal Isolation |
Thermal |
Minimized external heat effects |
Cost of enclosures, space requirements |
Warm-Up Cycles |
Thermal |
Uniform temperature distribution |
Increased setup time |
Climate-Controlled Facilities |
Environmental |
Stable operating conditions |
High operational costs, infrastructure needs |
Vibration Isolation |
Environmental |
Reduced vibration-induced errors |
Cost of isolation systems, space constraints |
Cleanroom Conditions |
Environmental |
Contaminant-free operation |
Expensive setup, ongoing maintenance |
Advanced CAM Software |
Operational |
Accurate tool paths, error detection |
Software cost, learning curve |
Tool Condition Monitoring |
Operational |
Timely tool replacement, consistent precision |
Sensor integration, data processing |
Operator Training |
Operational |
Reduced human errors, consistent setup |
Time and cost of training programs |
Optimized Cutting Parameters |
Operational |
Minimized deflection, improved finish |
Requires expertise, process optimization |
Ultra-Precision Machine Tools |
Advanced Technology |
Sub-micron accuracy, superior surface finish |
Extremely high cost, limited applications |
In-Process Metrology |
Advanced Technology |
Real-time error correction |
Integration complexity, measurement accuracy |
AI and Machine Learning |
Advanced Technology |
Predictive maintenance, optimized parameters |
Data requirements, algorithm development |
Hybrid Manufacturing |
Advanced Technology |
Complex geometries, reduced waste |
Machine complexity, process integration |
This table underscores the trade-offs between precision benefits and implementation challenges, guiding manufacturers in selecting appropriate strategies.
Case Studies in CNC Machine Precision
To illustrate the practical application of precision strategies, the following case studies highlight real-world examples across industries.
Aerospace: Turbine Blade Machining
In aerospace, turbine blades require dimensional tolerances of ±0.005 mm and surface finishes below 0.4 µm Ra. A leading manufacturer implemented a 5-axis CNC machining center with linear motors, active cooling, and in-process metrology. The machine used thermal compensation algorithms to correct for spindle expansion and vibration isolation to minimize shop floor disturbances. As a result, the manufacturer achieved a 30% reduction in scrap rates and improved blade performance due to tighter tolerances.
Medical Devices: Orthopedic Implants
Orthopedic implants, such as hip joints, demand biocompatible materials and surface finishes below 0.1 µm Ra. A medical device company employed an ultra-precision CNC machine with diamond tools and a cleanroom environment. Tool condition monitoring ensured consistent cutting performance, while AI-based parameter optimization reduced surface roughness by 15%. The resulting implants met stringent regulatory requirements and improved patient outcomes.
Semiconductor: Wafer Fabrication
In semiconductor manufacturing, CNC machines produce wafer chucks with flatness tolerances below ±0.0005 mm. A semiconductor equipment supplier used a diamond-turning lathe with aerostatic spindles and a climate-controlled cleanroom. In-process metrology and volumetric error compensation ensured sub-micron accuracy, enabling the production of defect-free wafers for advanced microchips.
Future Trends in CNC Machine Precision
The pursuit of precision in CNC machine tools is an evolving field, driven by advancements in materials, sensors, and digital technologies. Several trends are shaping the future of CNC precision:
1. Smart Manufacturing
The integration of Industry 4.0 technologies, such as the Internet of Things (IoT) and big data analytics, is transforming CNC machining. Smart CNC machines equipped with IoT sensors collect real-time data on temperature, vibration, and tool wear, enabling predictive maintenance and adaptive control. For example, a smart CNC machine can automatically adjust feed rates to compensate for detected vibrations, improving precision.
2. Nanotechnology Integration
Nanotechnology is enabling the development of CNC machines with nanoscale precision. Nano-positioning systems, using piezoelectric actuators, achieve resolutions below 1 nm, opening new possibilities for applications like optical lens manufacturing and quantum device fabrication.
3. Sustainable Precision Machining
Sustainability is becoming a priority in CNC machining, with a focus on energy-efficient designs and eco-friendly coolants. Precision strategies, such as minimum quantity lubrication (MQL), reduce coolant usage while maintaining surface finish quality, aligning with environmental goals.
4. Digital Twins
Digital twins—virtual replicas of CNC machines—enable real-time simulation and optimization of machining processes. By modeling thermal, mechanical, and operational behaviors, digital twins predict precision issues and recommend corrective actions before machining begins, reducing trial-and-error costs.
5. Human-Machine Collaboration
Collaborative robots (cobots) and augmented reality (AR) are enhancing operator efficiency and precision. AR systems provide real-time guidance for machine setup and tool calibration, while cobots assist in workpiece handling, reducing setup errors and improving repeatability.
Conclusion
The precision of CNC machine tools is a cornerstone of modern manufacturing, enabling the production of high-quality components across diverse industries. Precision variations arise from mechanical, thermal, environmental, and operational factors, each requiring targeted strategies to mitigate their impact. Mechanical design improvements, thermal management, environmental controls, operational best practices, and advanced technologies collectively enhance CNC machine precision, achieving tolerances as tight as ±0.0001 mm in ultra-precision applications.
Through case studies in aerospace, medical devices, and semiconductors, we see the practical impact of these strategies, from reduced scrap rates to improved product performance. Emerging trends, such as smart manufacturing, nanotechnology, and digital twins, promise to push the boundaries of CNC precision further, enabling new applications and sustainable practices.
As CNC technology continues to evolve, the interplay of engineering, data science, and human expertise will drive the next generation of precision machining, ensuring that CNC machine tools remain at the forefront of industrial innovation.
Reprint Statement: If there are no special instructions, all articles on this site are original. Please indicate the source for reprinting:https://www.cncmachiningptj.com/,thanks!
3, 4 and 5-axis precision CNC machining services for aluminum machining, beryllium, carbon steel, magnesium, titanium machining, Inconel, platinum, superalloy, acetal, polycarbonate, fiberglass, graphite and wood. Capable of machining parts up to 98 in. turning dia. and +/-0.001 in. straightness tolerance. Processes include milling, turning, drilling, boring, threading, tapping, forming, knurling, counterboring, countersinking, reaming and laser cutting. Secondary services such as assembly, centerless grinding, heat treating, plating and welding. Prototype and low to high volume production offered with maximum 50,000 units. Suitable for fluid power, pneumatics, hydraulics and valve applications. Serves the aerospace, aircraft, military, medical and defense industries.PTJ will strategize with you to provide the most cost-effective services to help you reach your target,Welcome to Contact us ( sales@pintejin.com ) directly for your new project.
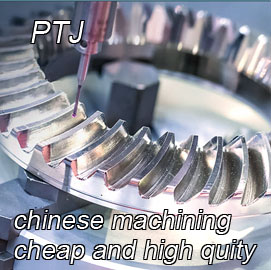
- 5 Axis Machining
- Cnc Milling
- Cnc Turning
- Machining Industries
- Machining Process
- Surface Treatment
- Metal Machining
- Plastic Machining
- Powder Metallurgy Mold
- Die Casting
- Parts Gallery
- Auto Metal Parts
- Machinery Parts
- LED Heatsink
- Building Parts
- Mobile Parts
- Medical Parts
- Electronic Parts
- Tailored Machining
- Bicycle Parts
- Aluminum Machining
- Titanium Machining
- Stainless Steel Machining
- Copper Machining
- Brass Machining
- Super Alloy Machining
- Peek Machining
- UHMW Machining
- Unilate Machining
- PA6 Machining
- PPS Machining
- Teflon Machining
- Inconel Machining
- Tool Steel Machining
- More Material