Deep Hole Processing of Aircraft Wing Surfaces
Deep hole processing is a critical manufacturing technique in aerospace engineering, particularly for the production of aircraft wing surfaces. This process involves creating precise, high-aspect-ratio holes in materials such as aluminum alloys, titanium alloys, and carbon fiber-reinforced polymers (CFRPs), which are commonly used in wing structures. These holes serve various purposes, including accommodating fasteners, fuel flow vent holes, and structural reinforcements. The complexity of aircraft wing designs, combined with stringent requirements for precision, structural integrity, and fatigue resistance, makes deep hole processing a challenging yet essential discipline. This article explores the principles, techniques, materials, challenges, and recent advancements in deep hole processing for aircraft wing surfaces, providing a comprehensive overview supported by comparative tables.
Introduction to Deep Hole Processing
Deep hole processing refers to the machining of holes with a depth-to-diameter ratio typically exceeding 10:1. In the context of aircraft wing surfaces, this process is vital for creating holes that ensure structural connectivity, aerodynamic efficiency, and operational safety. Aircraft wings are complex assemblies that integrate structural components, control surfaces, and fuel systems, all of which require precisely machined holes. The primary methods for deep hole processing include drilling, boring, and specialized techniques such as helical milling and abrasive waterjet drilling. Each method has unique advantages and limitations, influenced by material properties, hole specifications, and manufacturing constraints.
The importance of deep hole processing in aerospace cannot be overstated. For instance, a Boeing 747 contains over half a million holes, many of which are located in the wings for rivets, bolts, and other fasteners. These holes must withstand cyclic loading during takeoff, flight, and landing, where micro-cracks can initiate and propagate, leading to fatigue failure if not properly managed. The development of advanced machining techniques and tools has been driven by the need to enhance hole quality, reduce defects such as burrs and surface roughness, and improve the fatigue life of wing components.
Historical Context and Evolution
The history of deep hole processing in aerospace dates back to the early 20th century, when aircraft manufacturing relied on manual drilling techniques using basic twist drills. These methods were labor-intensive and prone to inconsistencies, particularly for deep holes in high-strength materials. The introduction of computer numerical control (CNC) machines in the mid-20th century revolutionized the field, enabling greater precision and repeatability. By the 1990s, advancements in tool materials, such as cemented carbides and coated drills, further improved the efficiency and quality of deep hole processing.
In the late 20th century, the aerospace industry began adopting composite materials like CFRPs for wing surfaces, necessitating new approaches to deep hole processing. Unlike metals, composites are prone to delamination and fiber pull-out during drilling, prompting the development of specialized tools and techniques. The 21st century has seen further innovations, including the integration of automation, robotics, and advanced imaging systems for real-time monitoring of hole quality. These developments have been driven by the increasing complexity of aircraft designs and the demand for lightweight, fuel-efficient wings.
Materials Used in Aircraft Wing Surfaces
Aircraft wing surfaces are constructed from a variety of materials, each presenting unique challenges for deep hole processing. The primary materials include:
-
Aluminum Alloys: Aluminum alloys, such as Al2024-T3, are widely used in aircraft wings due to their high strength-to-weight ratio and resistance to fatigue crack propagation. These alloys are relatively easy to machine but can suffer from burr formation and surface deformation during drilling.
-
Titanium Alloys: Titanium alloys, such as Ti-6Al-4V, are valued for their high strength, corrosion resistance, and ability to withstand extreme temperatures. However, their low thermal conductivity and high hardness make them difficult to machine, leading to tool wear and heat-related defects.
-
Carbon Fiber-Reinforced Polymers (CFRPs): CFRPs are increasingly used in modern aircraft wings, such as those on the Boeing 787 and Airbus A350, due to their exceptional strength and low weight. Drilling CFRPs requires careful control to avoid delamination, fiber pull-out, and matrix cracking.
-
Hybrid Stacks: Many modern wings feature hybrid stacks, where layers of metal and composite materials are bonded together. Processing holes in these stacks is particularly challenging due to the differing mechanical properties of the constituent materials.
Table 1: Properties of Common Aircraft Wing Materials
Material |
Density (g/cm³) |
Tensile Strength (MPa) |
Thermal Conductivity (W/m·K) |
Machinability Challenges |
---|---|---|---|---|
Al2024-T3 |
2.78 |
483 |
121 |
Burr formation, surface deformation |
Ti-6Al-4V |
4.43 |
950 |
6.7 |
Tool wear, heat generation |
CFRP |
1.5–1.8 |
600–2000 |
0.5–5 |
Delamination, fiber pull-out |
Hybrid Stack |
Varies |
Varies |
Varies |
Differential machining, tool wear |
Deep Hole Processing Techniques
Several techniques are employed for deep hole processing in aircraft wing surfaces, each suited to specific materials and applications. The following sections detail the most common methods, their mechanisms, and their suitability for aerospace applications.
Conventional Drilling
Conventional drilling uses twist drills or specialized deep-hole drills to remove material and create holes. This method is widely used for aluminum and titanium alloys due to its simplicity and cost-effectiveness. However, conventional drilling can lead to defects such as burrs, surface roughness, and hole misalignment, particularly in deep holes. The use of coolant is often necessary to manage heat generation and chip evacuation.
In a study on Al2024-T3, conventional drilling with uncoated high-speed steel (HSS) drills resulted in more severe surface deformation compared to carbide drills, highlighting the importance of tool material selection. The application of coolant was found to reduce surface damage and enhance fatigue performance.
Helical Milling
Helical milling, also known as orbital drilling, involves a rotating tool that moves in a helical path to create a hole. This technique is particularly effective for CFRPs and hybrid stacks, as it minimizes axial forces and reduces the risk of delamination. Helical milling produces smoother hole walls and allows for greater control over hole diameter and depth.
A comparative study on Al2024-T3 and Ti-6Al-4V showed that helical milling extended fatigue life compared to conventional drilling, attributed to reduced plastic deformation and surface roughness. However, helical milling is slower and requires more complex CNC programming, which can increase production costs.
Abrasive Waterjet Drilling
Abrasive waterjet drilling uses a high-pressure stream of water mixed with abrasive particles to cut through materials. This non-thermal process is ideal for CFRPs, as it avoids heat-related damage and delamination. However, abrasive waterjet drilling can result in wider kerf widths and less precise hole geometries compared to mechanical drilling.
Recent advancements in abrasive waterjet drilling have focused on optimizing process parameters, such as water pressure and abrasive type, to improve hole quality. A study on SS AISI 316L demonstrated that the Grey Wolf Optimization algorithm could identify optimal parameters for maximizing material removal rate and minimizing roundness deviation.
Deep Hole Boring
Deep hole boring is used to refine the geometry and surface finish of pre-drilled holes. This process employs single-point cutting tools or multi-edge boring heads to achieve tight tolerances and smooth surfaces. Deep hole boring is particularly important for critical applications, such as fuel flow vent holes in aircraft wings, where dimensional accuracy is paramount.
A study on 300M steel landing gear components demonstrated that deep hole boring, combined with optimized NC programming, could achieve surface roughness values as low as 3.2 μm, meeting stringent design requirements.
Table 2: Comparison of Deep Hole Processing Techniques
Technique |
Materials Suited |
Advantages |
Limitations |
Typical Applications |
---|---|---|---|---|
Conventional Drilling |
Aluminum, Titanium |
Cost-effective, widely available |
Burrs, surface roughness, misalignment |
Fastener holes, rivet holes |
Helical Milling |
CFRP, Hybrid Stacks |
Reduced delamination, smooth surfaces |
Slower, complex programming |
Composite wing panels |
Abrasive Waterjet Drilling |
CFRP |
Non-thermal, no heat damage |
Less precise, wider kerf |
Composite structures |
Deep Hole Boring |
All materials |
High precision, smooth surfaces |
Time-consuming, requires pre-drilling |
Fuel flow vent holes, critical fasteners |
Challenges in Deep Hole Processing
Deep hole processing for aircraft wing surfaces presents several challenges, driven by material properties, geometric constraints, and operational requirements. These challenges include:
Tool Wear and Heat Generation
Titanium alloys and hybrid stacks are particularly prone to causing tool wear due to their high hardness and abrasive nature. The low thermal conductivity of titanium leads to heat accumulation at the tool-workpiece interface, accelerating wear and potentially causing thermal damage. Advanced tool coatings, such as diamond-like carbon (DLC) and titanium nitride (TiN), have been developed to mitigate these issues.
Delamination and Fiber Damage in CFRPs
Drilling CFRPs can result in delamination, where layers of the composite separate, and fiber pull-out, where individual fibers are torn from the matrix. These defects compromise structural integrity and fatigue performance. Techniques such as helical milling and the use of specialized drill geometries have been shown to reduce delamination.
Burr Formation and Surface Roughness
Burr formation is a common issue in drilling aluminum and titanium alloys, requiring additional post-processing steps such as deburring. Surface roughness also affects fatigue life, as rough surfaces can act as stress concentrators. The use of coolant and optimized cutting parameters can minimize these defects.
Hole Misalignment and Geometric Tolerances
Deep holes are susceptible to misalignment due to tool deflection and vibration, particularly in high-aspect-ratio applications. Maintaining tight geometric tolerances is critical for ensuring proper fitment of fasteners and structural components. Advanced CNC machines and real-time monitoring systems have improved alignment accuracy.
Chip Evacuation
Effective chip evacuation is essential in deep hole processing to prevent tool jamming and surface damage. This is particularly challenging in titanium alloys, which produce long, stringy chips. High-pressure coolant systems and peck drilling strategies are commonly used to address this issue.
Advanced Technologies and Innovations
Recent advancements in deep hole processing have focused on improving precision, efficiency, and sustainability. Key innovations include:
Automation and Robotics
The integration of robotic systems in deep hole processing has enhanced productivity and consistency. Robotic arms equipped with drilling units can perform complex operations on large wing surfaces, reducing human error and labor costs. For example, the use of robotic assembly systems in CFRP wing manufacturing has improved hole positioning accuracy.
Visual Measurement and Quality Control
Visual measurement techniques, such as those using high-resolution cameras and neural networks, have been developed to assess hole quality in real time. A study on CFRP components demonstrated that a visual measurement system using a Basler acA2440-20gm camera could detect hole inlet edges with high accuracy, enabling rapid quality control.
Advanced Tool Materials and Coatings
The development of new tool materials, such as polycrystalline diamond (PCD) and cubic boron nitride (CBN), has improved performance in machining titanium and CFRP. Coatings like TiN and DLC reduce friction and wear, extending tool life and improving hole quality.
Sustainable Machining Practices
Dry drilling and minimum quantity lubrication (MQL) have gained attention as environmentally friendly alternatives to traditional coolant-based machining. These methods reduce the environmental impact of coolant disposal while maintaining acceptable hole quality. A study on Al2024-T3 showed that dry drilling with carbide drills could achieve comparable fatigue performance to wet drilling under optimized conditions.
Table 3: Impact of Tool Materials and Coatings on Deep Hole Processing
Tool Material/Coating |
Material Compatibility |
Benefits |
Limitations |
Tool Life (Holes) |
---|---|---|---|---|
Uncoated HSS |
Aluminum |
Low cost |
High wear, poor for titanium/CFRP |
50–100 |
Carbide |
Aluminum, Titanium |
High hardness, good wear resistance |
Expensive, brittle |
200–500 |
PCD |
CFRP, Hybrid Stacks |
Excellent wear resistance, low friction |
Very expensive, limited availability |
1000–2000 |
TiN Coating |
All materials |
Reduced friction, extended tool life |
Limited thermal stability |
300–700 |
DLC Coating |
Titanium, CFRP |
Low friction, high wear resistance |
High cost, complex application |
500–1000 |
Case Studies and Applications
Fuel Flow Vent Holes in F-111 Aircraft
The F-111 aircraft’s wing pivot fitting includes fuel flow vent holes (FFVHs), which are critical for fuel management and structural integrity. A study on damage tolerance optimization showed that optimizing the shape of FFVHs could improve fatigue life by 70–92%, depending on crack size. The use of spline-based design algorithms ensured smooth, manufacturable hole profiles, reducing stress concentrations.
CFRP Wing Panels in Boeing 787
The Boeing 787’s wings, constructed primarily from CFRP, require thousands of fastener holes. Helical milling has been adopted to minimize delamination and ensure high-quality holes. A visual measurement system was implemented to detect hole inlet edges, achieving a resolution of 2448 × 2048 pixels and improving quality control efficiency.
Titanium Alloy Components in Airbus A350
The Airbus A350 incorporates titanium alloy components in its wing structure, necessitating deep hole drilling for fasteners. A study on Ti-6Al-4V demonstrated that cemented carbide tools with optimized geometries could achieve high efficiency and surface quality, with surface roughness values below 3.2 μm.
Comparative Analysis of Hole Quality
Hole quality is a critical factor in determining the performance and longevity of aircraft wing surfaces. Key metrics include perpendicularity, cylindricity, circularity, surface roughness, and burr formation. The following table compares these metrics across different processing techniques and materials.
Table 4: Comparative Analysis of Hole Quality Metrics
Technique |
Material |
Perpendicularity (μm) |
Cylindricity (μm) |
Circularity (μm) |
Surface Roughness (μm) |
Burr Height (μm) |
---|---|---|---|---|---|---|
Conventional Drilling |
Al2024-T3 |
50–100 |
30–70 |
20–50 |
3.5–6.0 |
50–150 |
Conventional Drilling |
Ti-6Al-4V |
70–120 |
40–80 |
30–60 |
4.0–7.0 |
70–200 |
Helical Milling |
CFRP |
20–50 |
15–40 |
10–30 |
1.5–3.0 |
10–50 |
Helical Milling |
Hybrid Stack |
30–60 |
20–50 |
15–40 |
2.0–4.0 |
20–70 |
Abrasive Waterjet |
CFRP |
100–200 |
50–100 |
40–80 |
5.0–8.0 |
0–20 |
Deep Hole Boring |
300M Steel |
10–30 |
10–25 |
5–20 |
1.0–3.2 |
5–30 |
Fatigue Performance and Structural Integrity
The fatigue performance of aircraft wing surfaces is heavily influenced by the quality of machined holes. Poorly processed holes can act as stress concentrators, initiating cracks that propagate under cyclic loading. Studies have shown that helical milling and deep hole boring produce holes with superior fatigue life compared to conventional drilling, due to reduced surface roughness and plastic deformation.
In Al2024-T3, helical milling resulted in a fatigue life up to 30% longer than conventional drilling, attributed to smoother hole walls and minimal burrs. For CFRPs, the use of PCD tools and helical milling reduced delamination, improving fatigue resistance by up to 40%. In titanium alloys, optimized cutting parameters and coolant use were critical for minimizing heat-related defects and extending fatigue life.
Environmental and Economic Considerations
Deep hole processing in aerospace must balance performance with environmental and economic considerations. Traditional coolant-based machining generates significant waste, prompting the adoption of dry drilling and MQL. These methods reduce environmental impact but require careful optimization to maintain hole quality.
Economically, the high cost of advanced tools (e.g., PCD drills) and processes (e.g., helical milling) must be weighed against their benefits in terms of tool life and component performance. Automation and robotics offer long-term cost savings by reducing labor and improving throughput, but initial investment costs can be substantial.
Future Directions
The future of deep hole processing for aircraft wing surfaces lies in the integration of emerging technologies and sustainable practices. Key areas of focus include:
-
Additive Manufacturing Integration: Combining additive manufacturing with deep hole processing to create hybrid components with pre-formed holes, reducing machining time and material waste.
-
Artificial Intelligence and Machine Learning: Using AI to optimize cutting parameters and predict tool wear, improving efficiency and quality.
-
Next-Generation Materials: Developing processing techniques for advanced materials, such as ceramic matrix composites (CMCs) and graphene-reinforced polymers, which offer superior strength and weight properties.
-
Sustainability: Expanding the use of eco-friendly machining methods, such as cryogenic cooling, to reduce environmental impact.
Conclusion
Deep hole processing is a cornerstone of aircraft wing manufacturing, enabling the creation of precise, high-quality holes that ensure structural integrity and operational safety. The evolution of techniques such as helical milling, abrasive waterjet drilling, and deep hole boring has addressed the challenges posed by materials like aluminum, titanium, and CFRPs. Advances in automation, visual measurement, and tool materials have further enhanced the field, while sustainable practices are shaping its future. As aircraft designs continue to evolve, deep hole processing will remain a critical discipline, driven by the need for precision, efficiency, and environmental responsibility.
This article has provided a detailed examination of deep hole processing, supported by comparative tables and case studies. By understanding the principles, challenges, and innovations in this field, engineers and researchers can continue to push the boundaries of aerospace manufacturing, ensuring safer and more efficient aircraft wings.
Reprint Statement: If there are no special instructions, all articles on this site are original. Please indicate the source for reprinting:https://www.cncmachiningptj.com/,thanks!
3, 4 and 5-axis precision CNC machining services for aluminum machining, beryllium, carbon steel, magnesium, titanium machining, Inconel, platinum, superalloy, acetal, polycarbonate, fiberglass, graphite and wood. Capable of machining parts up to 98 in. turning dia. and +/-0.001 in. straightness tolerance. Processes include milling, turning, drilling, boring, threading, tapping, forming, knurling, counterboring, countersinking, reaming and laser cutting. Secondary services such as assembly, centerless grinding, heat treating, plating and welding. Prototype and low to high volume production offered with maximum 50,000 units. Suitable for fluid power, pneumatics, hydraulics and valve applications. Serves the aerospace, aircraft, military, medical and defense industries.PTJ will strategize with you to provide the most cost-effective services to help you reach your target,Welcome to Contact us ( sales@pintejin.com ) directly for your new project.
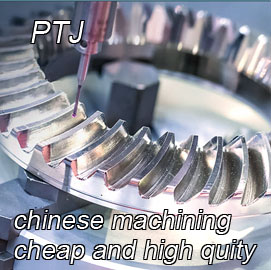
- 5 Axis Machining
- Cnc Milling
- Cnc Turning
- Machining Industries
- Machining Process
- Surface Treatment
- Metal Machining
- Plastic Machining
- Powder Metallurgy Mold
- Die Casting
- Parts Gallery
- Auto Metal Parts
- Machinery Parts
- LED Heatsink
- Building Parts
- Mobile Parts
- Medical Parts
- Electronic Parts
- Tailored Machining
- Bicycle Parts
- Aluminum Machining
- Titanium Machining
- Stainless Steel Machining
- Copper Machining
- Brass Machining
- Super Alloy Machining
- Peek Machining
- UHMW Machining
- Unilate Machining
- PA6 Machining
- PPS Machining
- Teflon Machining
- Inconel Machining
- Tool Steel Machining
- More Material