Ergonomics Problems Related to CNC Machining Operations
CNC (Computer Numerical Control) machining is a manufacturing process that employs computer-controlled tools to create precise parts from various materials, such as metals, plastics, and composites. While CNC machining has revolutionized industrial production by enhancing efficiency and accuracy, it presents significant ergonomic challenges for operators. These challenges stem from the physical and cognitive demands of operating complex machinery, prolonged work periods, and repetitive tasks. Ergonomic issues in CNC machining can lead to musculoskeletal disorders (MSDs), cognitive fatigue, and reduced productivity, posing risks to worker health and safety. This article comprehensively explores the ergonomic problems associated with CNC machining operations, their causes, impacts, and potential mitigation strategies, supported by detailed comparative analyses.
Overview of CNC Machining Operations
CNC machining involves the use of computer-controlled machine tools, such as lathes, mills, routers, and grinders, to shape raw materials into finished components. Operators are responsible for programming, setting up, monitoring, and maintaining these machines. The process requires a combination of technical expertise, manual dexterity, and sustained attention, which can expose workers to ergonomic hazards. These hazards include repetitive motions, awkward postures, excessive force, prolonged standing, and exposure to vibration and noise, all of which contribute to physical and mental strain.
The ergonomic challenges in CNC machining are multifaceted, as they arise from the interaction between the operator, the machine, and the work environment. For instance, the design of CNC machine interfaces, such as control panels and displays, can influence posture and cognitive workload. Similarly, the physical layout of the workspace, including the height of work surfaces and the placement of tools, can affect operator comfort and efficiency. Addressing these challenges requires a systematic approach that integrates engineering controls, administrative measures, and worker training.
Historical Context of Ergonomics in Manufacturing
Ergonomics, the science of designing work environments to fit the capabilities and limitations of workers, has been a critical consideration in manufacturing since the Industrial Revolution. Early manufacturing processes relied heavily on manual labor, leading to widespread injuries and fatigue. The advent of mechanized production in the 19th century introduced new ergonomic challenges, such as repetitive strain injuries and exposure to hazardous machinery. The introduction of CNC machining in the mid-20th century marked a significant shift, as it reduced the need for manual intervention but introduced new risks related to human-machine interaction.
The study of ergonomics in CNC machining gained prominence in the late 20th century, as occupational health researchers began to document the prevalence of MSDs among machinists. Studies highlighted the role of prolonged static postures, repetitive movements, and poorly designed workstations in contributing to worker discomfort. Over time, regulatory bodies, such as the Occupational Safety and Health Administration (OSHA) in the United States and the European Agency for Safety and Health at Work (EU-OSHA), established guidelines to promote ergonomic practices in manufacturing. These guidelines emphasize the importance of workstation design, task rotation, and worker education in mitigating ergonomic risks.
Ergonomic Hazards in CNC Machining
Physical Ergonomic Hazards
Physical ergonomic hazards in CNC machining are primarily associated with the physical demands of operating and maintaining machinery. These hazards include repetitive motions, awkward postures, excessive force, prolonged standing, and exposure to vibration. Each of these factors can contribute to the development of MSDs, such as carpal tunnel syndrome, tendonitis, and lower back pain.
Repetitive Motions
CNC operators often perform repetitive tasks, such as loading and unloading workpieces, adjusting tools, and entering data into control panels. These repetitive motions, particularly those involving the hands, wrists, and arms, can strain muscles and tendons, leading to conditions like repetitive strain injury (RSI). For example, frequent use of a keyboard or mouse to program CNC machines can cause wrist discomfort, while repetitive gripping of tools can lead to hand fatigue.
Awkward Postures
Awkward postures, such as bending, reaching, or twisting, are common in CNC machining due to the design of machines and workstations. For instance, operators may need to lean forward to inspect workpieces or reach overhead to access controls, placing strain on the back, shoulders, and neck. Prolonged awkward postures can reduce blood flow to muscles, increasing the risk of fatigue and injury.
Excessive Force
Tasks that require excessive force, such as tightening clamps, lifting heavy workpieces, or operating manual controls, can place significant stress on the musculoskeletal system. For example, lifting a metal blank weighing 20 kilograms or more without mechanical assistance can lead to back injuries. Similarly, applying force to turn stiff machine handles can strain the arms and shoulders.
Prolonged Standing
CNC operators often stand for extended periods while monitoring machines or performing setups. Prolonged standing on hard surfaces, such as concrete floors, can cause discomfort in the feet, legs, and lower back. This discomfort is exacerbated when operators lack access to anti-fatigue mats or opportunities to sit periodically.
Vibration Exposure
Exposure to vibration is another physical hazard in CNC machining, particularly when operating machines that generate high-frequency vibrations, such as grinders or milling machines. Hand-arm vibration syndrome (HAVS), characterized by numbness, tingling, and reduced dexterity, is a common condition among machinists exposed to prolonged vibration. Whole-body vibration, caused by standing on vibrating platforms, can also contribute to lower back pain.
Cognitive Ergonomic Hazards
In addition to physical hazards, CNC machining imposes significant cognitive demands on operators. These demands arise from the need to monitor complex processes, interpret data, and respond to machine alerts. Cognitive ergonomic hazards include mental fatigue, information overload, and decision-making stress.
Mental Fatigue
CNC operators must maintain high levels of attention over long shifts, often in noisy or distracting environments. Monitoring machine performance, checking tolerances, and troubleshooting errors require sustained concentration, which can lead to mental fatigue. Fatigued operators are more likely to make errors, such as incorrect programming inputs, which can result in costly defects or safety incidents.
Information Overload
Modern CNC machines are equipped with sophisticated interfaces that display a wealth of information, including tool paths, spindle speeds, and error codes. Operators must process this information quickly and accurately, which can lead to cognitive overload, particularly for inexperienced workers. Poorly designed interfaces, such as those with cluttered displays or non-intuitive controls, exacerbate this issue.
Decision-Making Stress
CNC operators often face time-sensitive decisions, such as whether to pause a machine to address an anomaly or adjust cutting parameters to optimize performance. These decisions can be stressful, especially when they involve balancing productivity with quality or safety. Chronic stress can impair cognitive function and contribute to burnout.
Environmental Ergonomic Hazards
The work environment in CNC machining facilities can also contribute to ergonomic problems. Environmental factors, such as noise, lighting, temperature, and air quality, can affect operator comfort and performance.
Noise
CNC machining operations generate significant noise from cutting tools, motors, and coolant systems. Prolonged exposure to noise levels above 85 decibels can cause hearing loss and increase stress levels. Noise also hinders communication, making it difficult for operators to collaborate or respond to verbal instructions.
Lighting
Inadequate or poorly positioned lighting can strain the eyes and contribute to fatigue. For example, insufficient lighting in the work area may make it difficult for operators to inspect workpieces or read displays, while glare from overhead lights can cause discomfort. Proper lighting is essential for maintaining visual acuity and reducing errors.
Temperature and Air Quality
CNC machining facilities are often subject to temperature fluctuations due to the heat generated by machines and seasonal changes. High temperatures can cause discomfort and dehydration, while cold environments can reduce dexterity. Poor air quality, caused by metal dust, coolant mist, or fumes, can irritate the respiratory system and exacerbate fatigue.
Health Impacts of Ergonomic Hazards
The ergonomic hazards associated with CNC machining can have significant health consequences for operators. These consequences include MSDs, neurological disorders, psychological stress, and reduced quality of life.
Musculoskeletal Disorders
MSDs are the most common health outcome of ergonomic hazards in CNC machining. These disorders affect the muscles, tendons, ligaments, nerves, and joints, leading to pain, stiffness, and reduced mobility. Common MSDs among CNC operators include:
-
Carpal Tunnel Syndrome: Caused by repetitive wrist movements and excessive force, leading to numbness, tingling, and weakness in the hands.
-
Tendonitis: Inflammation of tendons due to repetitive motions or awkward postures, often affecting the elbows, shoulders, or wrists.
-
Lower Back Pain: Resulting from prolonged standing, awkward postures, or heavy lifting, leading to chronic discomfort and reduced mobility.
-
Neck and Shoulder Pain: Caused by forward head postures or overhead reaching, resulting in muscle strain and stiffness.
Neurological Disorders
Prolonged exposure to vibration can lead to neurological disorders, such as HAVS, which affects the nerves and blood vessels in the hands and arms. Symptoms include numbness, tingling, and loss of grip strength, which can impair an operator’s ability to perform fine motor tasks.
Psychological Stress
Cognitive ergonomic hazards, such as mental fatigue and decision-making stress, can contribute to psychological issues, including anxiety, depression, and burnout. Chronic stress can also impair cognitive function, leading to reduced concentration and increased error rates.
Reduced Quality of Life
The cumulative effects of ergonomic hazards can significantly reduce an operator’s quality of life. Chronic pain, fatigue, and psychological stress can limit an individual’s ability to engage in leisure activities, maintain social relationships, or perform daily tasks. In severe cases, ergonomic injuries may lead to long-term disability or job loss.
Comparative Analysis of Ergonomic Hazards
To illustrate the scope of ergonomic hazards in CNC machining, the following table compares the primary physical, cognitive, and environmental hazards, their causes, and their health impacts.
Hazard Type |
Specific Hazard |
Primary Causes |
Health Impacts |
---|---|---|---|
Physical |
Repetitive Motions |
Frequent loading/unloading, data entry, tool adjustments |
Carpal tunnel syndrome, tendonitis, repetitive strain injury |
Physical |
Awkward Postures |
Bending, reaching, twisting to access controls or workpieces |
Lower back pain, neck and shoulder pain, muscle strain |
Physical |
Excessive Force |
Heavy lifting, tightening clamps, operating stiff controls |
Back injuries, shoulder strain, muscle fatigue |
Physical |
Prolonged Standing |
Standing on hard surfaces for extended periods |
Foot and leg discomfort, lower back pain, fatigue |
Physical |
Vibration Exposure |
Operating high-frequency machines (e.g., grinders, mills) |
Hand-arm vibration syndrome, lower back pain, reduced dexterity |
Cognitive |
Mental Fatigue |
Sustained attention, monitoring complex processes |
Reduced concentration, increased error rates, burnout |
Cognitive |
Information Overload |
Processing data from complex interfaces, cluttered displays |
Cognitive overload, decision-making errors, stress |
Cognitive |
Decision-Making Stress |
Time-sensitive decisions, balancing productivity and safety |
Anxiety, burnout, impaired cognitive function |
Environmental |
Noise |
Cutting tools, motors, coolant systems |
Hearing loss, stress, communication difficulties |
Environmental |
Inadequate Lighting |
Poorly positioned or insufficient lighting |
Eye strain, fatigue, increased error rates |
Environmental |
Temperature/Air Quality |
Heat from machines, poor ventilation, metal dust, coolant mist |
Discomfort, dehydration, respiratory irritation, reduced dexterity |
This table highlights the diverse nature of ergonomic hazards in CNC machining and underscores the need for targeted interventions to address each hazard type.
Mitigation Strategies for Ergonomic Problems
Addressing ergonomic problems in CNC machining requires a multifaceted approach that integrates engineering controls, administrative measures, and worker education. The following sections outline key mitigation strategies, supported by examples and best practices.
Engineering Controls
Engineering controls involve modifying the physical work environment or equipment to reduce ergonomic hazards. These controls are often the most effective because they address the root causes of ergonomic issues.
Workstation Design
Optimizing workstation design is critical for reducing physical ergonomic hazards. Key considerations include:
-
Adjustable Work Surfaces: Workstations should allow operators to adjust the height of work surfaces to maintain neutral postures. For example, an adjustable workbench can accommodate operators of different heights, reducing the need for bending or reaching.
-
Ergonomic Control Panels: Control panels should be positioned at elbow height and angled to minimize neck strain. Touchscreens and large, clearly labeled buttons can reduce the need for excessive force or repetitive motions.
-
Tool Accessibility: Frequently used tools should be placed within easy reach to minimize awkward postures. Tool racks or magnetic strips can keep tools organized and accessible.
Machine Modifications
Modifying CNC machines can reduce physical and cognitive ergonomic hazards. Examples include:
-
Automated Loading/Unloading Systems: Automated systems can reduce the need for repetitive manual handling of workpieces, minimizing the risk of MSDs.
-
Vibration Dampening: Installing vibration-dampening mounts or using anti-vibration gloves can reduce exposure to hand-arm vibration.
-
Noise Reduction: Enclosing noisy components or using sound-absorbing materials can lower noise levels, improving communication and reducing stress.
Anti-Fatigue Mats
Providing anti-fatigue mats for operators who stand for long periods can reduce foot and leg discomfort. These mats should be made of durable, cushioned materials and cover the entire standing area.
Administrative Measures
Administrative measures involve changes to work practices or schedules to reduce ergonomic risks. These measures are often less costly than engineering controls but require ongoing management and worker compliance.
Task Rotation
Rotating operators between different tasks can reduce the risk of repetitive strain injuries and mental fatigue. For example, an operator might alternate between programming, machine setup, and quality inspection tasks throughout a shift.
Rest Breaks
Scheduling regular rest breaks allows operators to recover from physical and cognitive demands. Short breaks every 1–2 hours can reduce fatigue and improve concentration. Providing designated rest areas with comfortable seating can enhance the effectiveness of breaks.
Workload Management
Balancing workloads to avoid excessive demands can reduce decision-making stress and cognitive overload. For example, managers can prioritize tasks to prevent operators from being overwhelmed during peak production periods.
Worker Education and Training
Educating workers about ergonomic principles and safe work practices is essential for preventing injuries. Training programs should cover:
-
Proper Lifting Techniques: Operators should be trained to use mechanical aids or team lifting for heavy workpieces and to maintain neutral postures when lifting.
-
Ergonomic Awareness: Workers should learn to recognize early signs of MSDs, such as discomfort or numbness, and report them promptly.
-
Interface Navigation: Training on how to use CNC machine interfaces efficiently can reduce cognitive overload and improve productivity.
Personal Protective Equipment (PPE)
While PPE is typically a last resort in ergonomic interventions, it can be effective in certain situations. Examples include:
-
Anti-Vibration Gloves: These gloves can reduce the transmission of vibration to the hands, lowering the risk of HAVS.
-
Hearing Protection: Earplugs or earmuffs can protect operators from noise-induced hearing loss.
-
Supportive Footwear: Shoes with cushioned soles and arch support can reduce discomfort from prolonged standing.
Comparative Analysis of Mitigation Strategies
The following table compares the primary mitigation strategies for ergonomic hazards in CNC machining, including their advantages, limitations, and estimated costs.
Strategy |
Hazard Addressed |
Advantages |
Limitations |
Estimated Cost |
---|---|---|---|---|
Adjustable Work Surfaces |
Awkward Postures, Prolonged Standing |
Accommodates diverse body sizes, reduces strain |
Requires initial investment, may need regular maintenance |
$500–$2,000 per workstation |
Automated Loading Systems |
Repetitive Motions, Excessive Force |
Reduces manual handling, increases efficiency |
High cost, requires space and technical expertise |
$10,000–$50,000 per system |
Vibration-Dampening Mounts |
Vibration Exposure |
Reduces vibration transmission, easy to install |
Limited effectiveness for high-frequency vibrations |
$100–$500 per machine |
Anti-Fatigue Mats |
Prolonged Standing |
Low cost, easy to implement, immediate comfort |
Requires regular replacement, may not address all standing-related issues |
$50–$200 per mat |
Task Rotation |
Repetitive Motions, Mental Fatigue |
No equipment cost, promotes skill development |
Requires scheduling coordination, may disrupt workflow |
Minimal (training costs) |
Rest Breaks |
Mental Fatigue, Physical Fatigue |
Low cost, improves concentration and morale |
May reduce productivity if not managed properly |
Minimal |
Ergonomic Training |
All Hazards |
Increases awareness, empowers workers to prevent injuries |
Requires ongoing reinforcement, effectiveness depends on worker compliance |
$1,000–$5,000 per program |
Anti-Vibration Gloves |
Vibration Exposure |
Affordable, portable, easy to use |
Limited protection for severe vibration, may reduce dexterity |
$20–$50 per pair |
Hearing Protection |
Noise |
Effective at preventing hearing loss, low cost |
May hinder communication, requires proper fit and maintenance |
$10–$30 per worker |
This table illustrates the trade-offs between different mitigation strategies, highlighting the need for a tailored approach based on specific workplace conditions and budget constraints.
Case Studies of Ergonomic Interventions
Case Study 1: Automotive Parts Manufacturer
An automotive parts manufacturer in the United States implemented a comprehensive ergonomic program to address MSDs among CNC operators. The program included adjustable workstations, automated loading systems, and task rotation. Over a two-year period, the company reported a 40% reduction in MSD-related workers’ compensation claims and a 15% increase in productivity. The initial investment of $150,000 for engineering controls was offset by savings in healthcare costs and improved efficiency.
Case Study 2: Aerospace Component Supplier
An aerospace component supplier in Germany introduced anti-fatigue mats and ergonomic training for its CNC machining workforce. The training focused on proper lifting techniques and early recognition of MSD symptoms. Within one year, the company observed a 25% decrease in reported back pain and a 10% reduction in absenteeism. The total cost of the intervention was approximately €10,000, making it a cost-effective solution.
Case Study 3: Small-Scale Machine Shop
A small-scale machine shop in Australia faced challenges with noise and vibration exposure. The shop installed vibration-dampening mounts and provided anti-vibration gloves to operators. Additionally, noise levels were reduced by enclosing high-decibel machines. These interventions led to a 30% reduction in complaints about hand numbness and improved worker satisfaction. The total cost was approximately AUD 5,000, demonstrating that small businesses can implement effective ergonomic solutions on a limited budget.
Regulatory and Industry Standards
Several regulatory bodies and industry organizations have established standards to promote ergonomic practices in CNC machining. These standards provide guidelines for workplace design, risk assessment, and worker protection.
Occupational Safety and Health Administration (OSHA)
OSHA’s General Industry Standards (29 CFR 1910) include provisions for ergonomic risk management, such as ensuring safe lifting practices and minimizing repetitive motion injuries. OSHA also provides voluntary guidelines for ergonomics in manufacturing, emphasizing the importance of workstation design and worker training.
European Agency for Safety and Health at Work (EU-OSHA)
EU-OSHA’s directives, such as the Manual Handling of Loads Directive (90/269/EEC), require employers to assess and mitigate ergonomic risks. The agency also promotes the use of participatory ergonomics, where workers are involved in identifying and addressing hazards.
International Organization for Standardization (ISO)
ISO standards, such as ISO 11228 (Ergonomics – Manual Handling), provide detailed recommendations for assessing ergonomic risks in manufacturing. These standards cover topics like lifting limits, repetitive task analysis, and workstation design.
Industry Best Practices
Industry organizations, such as the National Institute for Occupational Safety and Health (NIOSH) and the Manufacturing Skill Standards Council (MSSC), publish best practices for ergonomics in CNC machining. These practices include regular ergonomic assessments, cross-training to enable task rotation, and collaboration with equipment manufacturers to design ergonomic machines.
Future Trends in Ergonomics for CNC Machining
Advancements in technology and research are shaping the future of ergonomics in CNC machining. Emerging trends include:
Automation and Robotics
The integration of automation and collaborative robots (cobots) is reducing the physical demands of CNC machining. Cobots can handle repetitive tasks, such as loading and unloading, allowing operators to focus on supervisory and cognitive tasks. This shift is expected to decrease the incidence of MSDs while improving productivity.
Wearable Technology
Wearable devices, such as exoskeletons and posture monitors, are being developed to support operators in CNC machining. Exoskeletons can reduce the strain of lifting heavy workpieces, while posture monitors provide real-time feedback to encourage neutral postures.
Human-Machine Interface (HMI) Design
Improvements in HMI design, such as touchscreens with intuitive layouts and voice-activated controls, are reducing cognitive ergonomic hazards. These advancements aim to minimize information overload and streamline operator interactions with CNC machines.
Data-Driven Ergonomics
The use of data analytics and wearable sensors is enabling employers to monitor ergonomic risks in real time. For example, sensors can track an operator’s posture, movement patterns, and fatigue levels, allowing managers to intervene before injuries occur.
Sustainable Ergonomics
Sustainability is becoming a key consideration in ergonomic design, with a focus on creating workstations and tools that are durable, energy-efficient, and adaptable to future needs. Sustainable ergonomics also emphasizes worker well-being as a core component of corporate social responsibility.
Conclusion
Ergonomic problems in CNC machining operations pose significant challenges to worker health, safety, and productivity. Physical hazards, such as repetitive motions and awkward postures, contribute to MSDs, while cognitive hazards, such as mental fatigue and information overload, impair performance and increase stress. Environmental factors, including noise and poor lighting, further exacerbate these issues. Mitigation strategies, including engineering controls, administrative measures, and worker education, are essential for addressing these hazards. Comparative analyses and case studies demonstrate the effectiveness of targeted interventions, while regulatory standards and emerging technologies offer promising solutions for the future. By prioritizing ergonomics, manufacturers can create safer, more efficient workplaces that enhance worker well-being and sustain long-term productivity.
Reprint Statement: If there are no special instructions, all articles on this site are original. Please indicate the source for reprinting:https://www.cncmachiningptj.com/,thanks!
3, 4 and 5-axis precision CNC machining services for aluminum machining, beryllium, carbon steel, magnesium, titanium machining, Inconel, platinum, superalloy, acetal, polycarbonate, fiberglass, graphite and wood. Capable of machining parts up to 98 in. turning dia. and +/-0.001 in. straightness tolerance. Processes include milling, turning, drilling, boring, threading, tapping, forming, knurling, counterboring, countersinking, reaming and laser cutting. Secondary services such as assembly, centerless grinding, heat treating, plating and welding. Prototype and low to high volume production offered with maximum 50,000 units. Suitable for fluid power, pneumatics, hydraulics and valve applications. Serves the aerospace, aircraft, military, medical and defense industries.PTJ will strategize with you to provide the most cost-effective services to help you reach your target,Welcome to Contact us ( sales@pintejin.com ) directly for your new project.
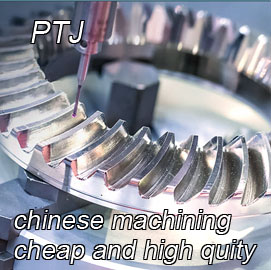
- 5 Axis Machining
- Cnc Milling
- Cnc Turning
- Machining Industries
- Machining Process
- Surface Treatment
- Metal Machining
- Plastic Machining
- Powder Metallurgy Mold
- Die Casting
- Parts Gallery
- Auto Metal Parts
- Machinery Parts
- LED Heatsink
- Building Parts
- Mobile Parts
- Medical Parts
- Electronic Parts
- Tailored Machining
- Bicycle Parts
- Aluminum Machining
- Titanium Machining
- Stainless Steel Machining
- Copper Machining
- Brass Machining
- Super Alloy Machining
- Peek Machining
- UHMW Machining
- Unilate Machining
- PA6 Machining
- PPS Machining
- Teflon Machining
- Inconel Machining
- Tool Steel Machining
- More Material