How to CNC Machine a Large Laser Cutting Table
The process of designing, fabricating, and assembling a large laser cutting table using computer numerical control (CNC) machining is a complex yet rewarding endeavor that combines precision engineering, materials science, and advanced manufacturing techniques. A laser cutting table is a critical piece of equipment in industries such as manufacturing, aerospace, automotive, and fabrication, enabling the precise cutting of materials like metal, wood, acrylic, and composites. This article provides a comprehensive guide to CNC machining a large laser cutting table, covering design principles, material selection, machining processes, assembly, calibration, and maintenance. Written in an encyclopedic tone, this guide aims to serve as a definitive resource for engineers, hobbyists, and professionals seeking to undertake such a project.
Introduction to Laser Cutting Tables
A laser cutting table is a specialized platform designed to support workpieces during laser cutting operations. It typically consists of a robust frame, a cutting bed, and integrated systems for laser beam delivery, material handling, and exhaust management. Large laser cutting tables, often exceeding 2 meters by 1 meter in size, are used for industrial applications requiring high precision and the ability to process oversized materials. CNC machining is a preferred method for fabricating such tables due to its ability to achieve tight tolerances, complex geometries, and repeatability.
The construction of a large laser cutting table involves multiple disciplines, including mechanical design, structural analysis, and electrical engineering. CNC machining plays a central role in producing the table’s components, such as the frame, bed supports, and mounting brackets, with the precision required for laser cutting accuracy. This article explores the step-by-step process of CNC machining a large laser cutting table, addressing challenges, best practices, and technical considerations.
Design Principles for a Large Laser Cutting Table
Functional Requirements
The design of a large laser cutting table begins with defining its functional requirements. These include the table’s working area, load capacity, material compatibility, and integration with the laser cutting system. A typical large laser cutting table might have a working area of 2.5 meters by 1.5 meters, support loads up to 500 kilograms, and accommodate materials ranging from thin sheets to thick plates.
The table must ensure stability during high-speed laser cutting, minimize vibrations, and provide a flat, level surface for accurate beam focus. Additional considerations include exhaust systems for fume extraction, accessibility for maintenance, and compatibility with automation systems such as material loaders or robotic arms.
Structural Design
The structural design of the table focuses on rigidity, durability, and thermal stability. The frame is typically constructed from welded steel or aluminum sections, designed to withstand dynamic loads and thermal expansion caused by laser heat. Finite element analysis (FEA) is often employed to simulate stress distribution, deflection, and resonance frequencies, ensuring the frame can maintain precision under operational conditions.
The cutting bed, which supports the workpiece, is designed as a grid, honeycomb, or slatted structure to minimize contact with the laser beam and facilitate debris removal. The bed must be replaceable or repairable, as it is subject to wear from repeated laser exposure. Mounting points for the laser head, gantry, and motion systems are also critical, requiring precise alignment to ensure accurate beam delivery.
Motion System Integration
A large laser cutting table typically incorporates a gantry-based motion system to move the laser head across the workpiece. The gantry, supported by linear rails and driven by servo motors or stepper motors, must be machined to tight tolerances to ensure smooth, accurate motion. CNC machining is used to fabricate rail mounts, bearing blocks, and other motion components, ensuring compatibility with the table’s frame and bed.
Safety and Ergonomics
Safety features, such as interlocks, emergency stops, and shielding, are integral to the design. The table must comply with standards such as ISO 13849 (safety of machinery) and ANSI B11.21 (laser cutting machines). Ergonomic considerations include operator access to controls, visibility of the cutting area, and ease of material loading and unloading.
Material Selection for CNC Machining
Frame Materials
The frame of a large laser cutting table is typically made from steel or aluminum alloys due to their strength, machinability, and availability. Common choices include:
-
Mild Steel (A36): Offers high strength and affordability but is prone to corrosion unless coated. Suitable for welded frames.
-
Stainless Steel (304/316): Provides corrosion resistance and durability, ideal for environments with high humidity or chemical exposure.
-
Aluminum (6061-T6): Lightweight and corrosion-resistant, suitable for smaller or modular tables but less rigid than steel.
The choice of material depends on the table’s size, load requirements, and budget. Steel is preferred for large, heavy-duty tables, while aluminum is used for lighter, portable designs.
Cutting Bed Materials
The cutting bed is typically made from materials that resist laser damage and provide adequate support. Common options include:
-
Steel Slats: Durable and cost-effective, steel slats are replaceable and suitable for heavy materials. They require periodic maintenance to remove slag buildup.
-
Honeycomb Aluminum: Lightweight and precise, honeycomb beds are ideal for thin materials like acrylic or paper. They are more expensive and less durable than slats.
-
Ceramic Pins: Used in specialized applications, ceramic pins offer high heat resistance but are costly and fragile.
Fasteners and Hardware
Fasteners, such as bolts, screws, and dowel pins, are typically made from stainless steel or high-strength steel to ensure reliability. Precision dowel pins are used for aligning components, while vibration-resistant fasteners, such as locknuts, prevent loosening during operation.
Comparison of Frame Materials
The following table compares common frame materials for CNC-machined laser cutting tables:
Material |
Strength (MPa) |
Density (g/cm³) |
Corrosion Resistance |
Cost ($/kg) |
Machinability |
Applications |
---|---|---|---|---|---|---|
Mild Steel (A36) |
400–550 |
7.85 |
Low |
0.5–1.0 |
High |
Heavy-duty frames, welded structures |
Stainless Steel (304) |
515–620 |
8.00 |
High |
2.5–4.0 |
Moderate |
Corrosive environments |
Aluminum (6061-T6) |
240–310 |
2.70 |
High |
2.0–3.5 |
High |
Lightweight, modular tables |
CNC Machining Processes
Overview of CNC Machining
CNC machining involves the use of computer-controlled tools to remove material from a workpiece, creating precise components. For a large laser cutting table, CNC machining processes include milling, turning, drilling, and tapping, performed on CNC mills, lathes, and machining centers. The process is guided by computer-aided design (CAD) models and computer-aided manufacturing (CAM) software, ensuring accuracy and repeatability.
CAD/CAM Workflow
The CNC machining process begins with creating a 3D CAD model of the table’s components using software such as SolidWorks, Fusion 360, or CATIA. The model includes detailed geometries, tolerances, and material specifications. The CAD model is then imported into CAM software, such as Mastercam or Siemens NX, to generate toolpaths, select cutting tools, and define machining parameters.
Machining the Frame
The frame components, such as beams, columns, and cross-members, are typically machined from steel or aluminum plates or extrusions. Key machining operations include:
-
Milling: Used to create flat surfaces, slots, and pockets for mounting hardware. For example, milling is used to machine the top surface of the frame to ensure flatness within 0.05 mm.
-
Drilling: Used to create holes for bolts, dowel pins, and alignment features. Precision drilling ensures accurate assembly.
-
Tapping: Used to create threaded holes for fasteners, ensuring secure connections.
For large components, a 3-axis or 5-axis CNC mill is used, depending on the complexity of the geometry. Fixturing is critical to prevent workpiece movement during machining, often requiring custom jigs or vacuum tables.
Machining the Cutting Bed
The cutting bed, whether slatted or honeycomb, requires precise machining to ensure uniformity and compatibility with the frame. For steel slats, CNC plasma cutting or waterjet cutting may be used to cut slat profiles, followed by milling to refine edges and create mounting features. For honeycomb beds, CNC milling is used to create the hexagonal grid, requiring high-precision tools to maintain cell consistency.
Tolerances and Surface Finish
Tolerances for a laser cutting table are typically in the range of ±0.01 mm to ±0.05 mm, depending on the component. For example, mounting surfaces for linear rails require tighter tolerances (±0.01 mm) to ensure smooth motion, while frame components may allow looser tolerances (±0.05 mm). Surface finish is also critical, with machined surfaces often requiring a smoothness of Ra 1.6 µm or better to minimize friction and wear.
Comparison of CNC Machining Processes
The following table compares CNC machining processes used for laser cutting table components:
Process |
Accuracy (mm) |
Materials |
Applications |
Tooling Cost |
Cycle Time |
---|---|---|---|---|---|
Milling |
±0.01–0.05 |
Steel, Aluminum, Composites |
Frame surfaces, slots, pockets |
Moderate |
Medium |
Drilling |
±0.02–0.05 |
Steel, Aluminum |
Bolt holes, alignment pins |
Low |
Low |
Tapping |
±0.05 |
Steel, Aluminum |
Threaded holes for fasteners |
Low |
Low |
Plasma Cutting |
±0.1–0.5 |
Steel |
Slat profiles, rough cuts |
Low |
High |
Waterjet Cutting |
±0.05–0.1 |
Steel, Aluminum, Ceramics |
Slats, honeycomb beds |
High |
Medium |
Assembly of the Laser Cutting Table
Frame Assembly
The assembly process begins with constructing the frame, typically using a combination of welding and bolting. Welded frames are assembled first, with CNC-machined components aligned using precision dowel pins and fixtures. Welds are inspected for integrity, and stress-relieving heat treatment may be applied to prevent distortion. Bolted frames, often used for modular designs, rely on CNC-machined holes and fasteners for alignment, allowing for easier disassembly and transport.
Installing the Cutting Bed
The cutting bed is installed after the frame is complete. For slatted beds, individual slats are inserted into CNC-machined slots or brackets, ensuring even spacing and levelness. For honeycomb beds, the grid is bolted or clamped to the frame, with shims used to achieve flatness. The bed is inspected using a laser level or coordinate measuring machine (CMM) to verify flatness within 0.1 mm across the working area.
Motion System Installation
The motion system, including linear rails, gantry, and drive motors, is installed next. CNC-machined mounting surfaces ensure accurate alignment of rails, which are secured using high-strength bolts. The gantry is assembled separately, with CNC-machined bearing blocks and motor mounts ensuring smooth operation. The laser head is mounted on the gantry, with alignment checked using dial indicators or laser trackers.
Electrical and Control Systems
The electrical system includes wiring for motors, sensors, and the laser power supply. CNC-machined brackets and conduits are used to route cables neatly, minimizing interference. The control system, typically a CNC controller or programmable logic controller (PLC), is integrated to manage motion, laser operation, and safety features. Software such as Mach3, GRBL, or proprietary systems is configured to interface with the table.
Exhaust and Safety Systems
An exhaust system, consisting of ducts and a high-capacity blower, is installed to remove fumes and debris. CNC-machined flanges and adapters ensure a secure connection between ducts and the table. Safety features, such as interlocks and shielding, are added to comply with regulations, with CNC-machined mounts ensuring precise placement.
Calibration and Testing
Geometric Calibration
After assembly, the table undergoes geometric calibration to ensure accuracy. This involves checking the flatness of the cutting bed, parallelism of the linear rails, and perpendicularity of the gantry. Tools such as laser interferometers, autocollimators, and CMMs are used to measure deviations, with adjustments made using shims or set screws.
Motion System Calibration
The motion system is calibrated to ensure smooth, accurate movement. This includes tuning servo motor gains, verifying encoder feedback, and testing backlash. A test cut, such as a simple square or circle, is performed to verify motion accuracy, with results measured using a micrometer or optical comparator.
Laser Alignment
The laser beam is aligned to ensure proper focus and perpendicularity to the cutting bed. A beam alignment tool or test cut is used to verify beam quality, with mirrors and lenses adjusted as needed. The focal length is set based on the material thickness, typically ranging from 50 mm to 150 mm for industrial lasers.
Performance Testing
The table undergoes performance testing to verify its capabilities. This includes cutting a range of materials (e.g., steel, aluminum, acrylic) at different speeds and power levels. Key metrics, such as cut quality, edge smoothness, and dimensional accuracy, are evaluated. The exhaust system is tested to ensure adequate fume removal, and safety features are verified under simulated fault conditions.
Maintenance and Upgrades
Routine Maintenance
Regular maintenance is essential to ensure the longevity and performance of a laser cutting table. This includes:
-
Cleaning: Removing debris from the cutting bed and exhaust ducts to prevent buildup.
-
Lubrication: Applying grease or oil to linear rails and bearings to reduce wear.
-
Inspection: Checking fasteners, welds, and alignments for signs of loosening or distortion.
-
Laser Maintenance: Cleaning optics and checking beam alignment to maintain cut quality.
A maintenance schedule, typically monthly or quarterly, is established based on usage intensity.
Upgrades and Modifications
Over time, the table may require upgrades to enhance performance or adapt to new requirements. Common upgrades include:
-
Automation: Adding material loaders, robotic arms, or conveyor systems to improve throughput.
-
Laser Power: Upgrading to a higher-power laser (e.g., from 1 kW to 4 kW) to cut thicker materials.
-
Control Systems: Upgrading to a more advanced CNC controller for improved precision or features.
-
Bed Design: Switching from slats to honeycomb or vice versa to suit different materials.
CNC machining is often used to fabricate new components or modify existing ones during upgrades, ensuring compatibility with the original design.
Comparison of Maintenance Tasks
The following table compares common maintenance tasks for laser cutting tables:
Task |
Frequency |
Tools Required |
Time (Hours) |
Impact on Performance |
Cost ($) |
---|---|---|---|---|---|
Cleaning Bed |
Weekly |
Brush, Vacuum |
0.5–1 |
High |
10–50 |
Lubricating Rails |
Monthly |
Grease Gun, Lubricant |
0.5–1 |
Moderate |
20–100 |
Inspecting Welds |
Quarterly |
Magnifier, Dye Penetrant |
1–2 |
High |
50–200 |
Aligning Laser |
Quarterly |
Beam Alignment Tool |
1–3 |
Critical |
100–500 |
Replacing Slats |
Annually |
Wrenches, Replacement Slats |
2–4 |
High |
200–1000 |
Challenges and Solutions
Thermal Distortion
Laser cutting generates significant heat, which can cause thermal distortion in the table’s frame or bed. To mitigate this, materials with low thermal expansion coefficients, such as stainless steel, are used. Additionally, cooling systems, such as water jackets or forced-air cooling, can be integrated into the design.
Vibration Control
High-speed laser cutting can induce vibrations, affecting cut quality. Vibration-damping materials, such as rubber pads or viscoelastic coatings, are applied to the frame. CNC-machined mounts with tight tolerances also help minimize play in the motion system.
Material Handling
Large workpieces pose challenges for loading and unloading. Solutions include integrating roller tables, cranes, or automated material handlers. CNC-machined brackets ensure these systems align with the table’s frame.
Cost Management
The cost of CNC machining a large laser cutting table can be significant, driven by material prices, machining time, and labor. To manage costs, designers can optimize material usage through nesting software, select cost-effective materials like mild steel, and use modular designs to reduce machining complexity.
Case Studies
Industrial Laser Cutting Table
A manufacturer in the automotive industry required a 3-meter by 2-meter laser cutting table for processing steel panels. The frame was CNC-machined from A36 steel, with a slatted bed designed for heavy loads. The table incorporated a 4 kW fiber laser and a gantry system with linear motors, achieving a cutting accuracy of ±0.02 mm. The project, completed in six months, cost $150,000, including machining, assembly, and testing.
Modular Laser Cutting Table
A small fabrication shop needed a portable 2-meter by 1-meter laser cutting table for acrylic and wood. The frame was CNC-machined from 6061-T6 aluminum, with a honeycomb bed for lightweight materials. The table used a 1 kW CO2 laser and a stepper motor-driven gantry, with a total cost of $30,000. The modular design allowed for easy transport and upgrades.
Future Trends
Additive Manufacturing Integration
Additive manufacturing (3D printing) is increasingly used alongside CNC machining to create complex components, such as lightweight brackets or custom bed supports. Hybrid machines combining CNC milling and 3D printing are emerging, offering new possibilities for laser cutting table design.
Smart Manufacturing
The integration of sensors, IoT, and machine learning enables real-time monitoring and optimization of laser cutting tables. CNC-machined mounts for sensors ensure accurate data collection, supporting predictive maintenance and process control.
Sustainability
Sustainable manufacturing practices, such as using recycled materials or energy-efficient lasers, are gaining traction. CNC machining processes are being optimized to reduce waste, with techniques like near-net-shape machining minimizing material removal.
Conclusion
CNC machining a large laser cutting table is a multifaceted process requiring expertise in design, materials, machining, assembly, and testing. By leveraging precision CNC techniques, engineers can create robust, accurate, and reliable tables tailored to specific applications. This guide has outlined the key steps, challenges, and best practices, providing a comprehensive resource for those embarking on such a project. As technology advances, the integration of smart systems, additive manufacturing, and sustainable practices will further enhance the capabilities of laser cutting tables, solidifying their role in modern manufacturing.
Reprint Statement: If there are no special instructions, all articles on this site are original. Please indicate the source for reprinting:https://www.cncmachiningptj.com/,thanks!
3, 4 and 5-axis precision CNC machining services for aluminum machining, beryllium, carbon steel, magnesium, titanium machining, Inconel, platinum, superalloy, acetal, polycarbonate, fiberglass, graphite and wood. Capable of machining parts up to 98 in. turning dia. and +/-0.001 in. straightness tolerance. Processes include milling, turning, drilling, boring, threading, tapping, forming, knurling, counterboring, countersinking, reaming and laser cutting. Secondary services such as assembly, centerless grinding, heat treating, plating and welding. Prototype and low to high volume production offered with maximum 50,000 units. Suitable for fluid power, pneumatics, hydraulics and valve applications. Serves the aerospace, aircraft, military, medical and defense industries.PTJ will strategize with you to provide the most cost-effective services to help you reach your target,Welcome to Contact us ( sales@pintejin.com ) directly for your new project.
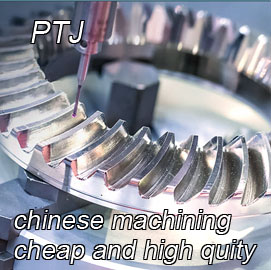
- 5 Axis Machining
- Cnc Milling
- Cnc Turning
- Machining Industries
- Machining Process
- Surface Treatment
- Metal Machining
- Plastic Machining
- Powder Metallurgy Mold
- Die Casting
- Parts Gallery
- Auto Metal Parts
- Machinery Parts
- LED Heatsink
- Building Parts
- Mobile Parts
- Medical Parts
- Electronic Parts
- Tailored Machining
- Bicycle Parts
- Aluminum Machining
- Titanium Machining
- Stainless Steel Machining
- Copper Machining
- Brass Machining
- Super Alloy Machining
- Peek Machining
- UHMW Machining
- Unilate Machining
- PA6 Machining
- PPS Machining
- Teflon Machining
- Inconel Machining
- Tool Steel Machining
- More Material