How to Reduce Chatter in CNC Milling – Tips for Minimizing Machining Vibration
2023-10-30
CNC milling is a powerful and versatile machining process that allows for precise and complex part production. However, one common issue that machinists encounter during CNC milling is chatter. Chatter, in the context of machining, is the undesirable vibration or oscillation that occurs during cutting. It can lead to poor surface finishes, reduced tool life, and even damage to the machine. In this comprehensive guide, we will explore the causes of chatter in CNC milling and provide a wide range of tips and techniques to effectively reduce or eliminate it.
Understanding Chatter in CNC Milling
What is Chatter in CNC Milling?
Chatter, in the context of CNC milling, is a disruptive and detrimental phenomenon that occurs during the machining process. It manifests as unwanted vibration or oscillation in the machine tool, workpiece, or cutting tool. This phenomenon is often characterized by a distinct, unpleasant noise and can have serious implications for machining operations. To understand chatter more comprehensively, let's break down its key components and dynamics.Key Components of Chatter:
- Machine Tool: The CNC machine tool, including its structural components, spindle, and bearings, can be a source of chatter if they lack rigidity or are not properly maintained.
- Workpiece: The material being machined and its properties, such as hardness and fixturing, can influence chatter.
- Tooling: The choice of cutting tools, their geometry, condition, and material, can play a significant role in chatter occurrence.
- Cutting Parameters: The selection of cutting parameters, including feed rate, cutting speed, and depth of cut, can affect the stability of the machining process.
Dynamics of Chatter:
Chatter occurs when there is an imbalance between the forces acting on the cutting tool and the resistance offered by the workpiece material. This imbalance leads to vibration, which can result in a host of negative consequences, including:- Poor Surface Finish: Chatter-induced vibrations can leave behind irregular and rough surface finishes on the machined part, diminishing its quality and precision.
- Reduced Tool Life: The constant, rapid oscillations in the tool can lead to excessive tool wear and significantly shorten its lifespan.
- Machine Damage: Prolonged exposure to chatter can jeopardize the integrity of the CNC machine itself. Over time, the accumulated mechanical stress can lead to costly repairs and downtime.
- Productivity Loss: Chatter often necessitates the reduction of cutting speeds or feeds to mitigate the problem, which can result in longer machining times and reduced overall productivity.
Why Chatter Matters
Understanding why chatter matters is crucial for any CNC milling operation. While it might appear as an annoyance or inconvenience, its impact extends far beyond that. Here's why chatter is a matter of significant concern:- Quality of the Finished Part: Chatter can severely compromise the quality and precision of the machined part. If your goal is to produce high-precision components, chatter can be a major hindrance.
- Tool Life: Chatter-induced vibrations can lead to rapid tool wear and breakage. This means increased tool replacement costs and more frequent interruptions to the machining process.
- Machine Integrity: Prolonged exposure to chatter can cause damage to the CNC machine itself. This includes wear and tear on machine components, spindle damage, and other structural issues.
- Productivity: Chatter forces machinists to reduce cutting speeds and feeds to avoid further issues. This slower pace reduces overall productivity and can result in delays in completing machining tasks.
- Safety Concerns: Chatter can even pose safety risks in the workshop. The vibrations and instability it creates may lead to accidents, tool ejections, or workpiece damage.
What is Machining Vibration?
Machining vibration, often simply referred to as "vibration" in the context of machining processes, is an undesirable and oscillatory motion or oscillation that occurs during the cutting or machining of materials. This phenomenon manifests as rapid back-and-forth movements, typically in the form of vibrations, shaking, or oscillations, in the machine tool, workpiece, cutting tool, or a combination of these components. Machining vibration is a common issue in various machining processes, including turning, milling, drilling, and grinding. Key characteristics of machining vibration include:- Unwanted Motion: Vibration represents an undesired motion in the machining system. It can lead to instability, affecting the accuracy and quality of the machined parts.
- Repetitive Oscillation: Vibration typically occurs at a specific frequency or frequencies, leading to repetitive back-and-forth movements. These oscillations can be seen in the movement of the workpiece, cutting tool, or the entire machine.
- Noise: Vibration often produces a characteristic noise, which can be a result of components moving or vibrating against each other. This noise can serve as an audible indicator of vibration.
- Reduced Surface Finish: Vibration can lead to uneven or irregular surface finishes on machined parts, affecting their quality and precision.
- Shortened Tool Life: The rapid and irregular movements associated with vibration can result in excessive wear and tool damage, leading to the need for frequent tool changes.
- Machine Wear and Damage: Prolonged exposure to vibration can accelerate wear and damage to machine components, including spindles, bearings, and structural elements.
- Inaccuracies and Dimensional Variations: Vibration can cause workpiece or tool deflection, resulting in inaccuracies and dimensional variations in the final product.
Causes of Chatter
Chatter in CNC milling is a complex phenomenon influenced by a combination of factors. Understanding these causes is fundamental to effectively addressing and mitigating chatter. These factors can be broadly categorized into four key areas:1. Machine Tool Factors
The characteristics and condition of the CNC machine itself are significant contributors to chatter. Several machine-related factors can influence chatter occurrence:a. Rigidity:
Rigidity refers to the machine's ability to resist deformation or flexing during the machining process. A more rigid machine is less prone to chatter. Machine components, such as the machine bed, columns, and spindle, should be designed and built with high rigidity in mind. The rigidity of the machine ensures stable cutting conditions, reducing the likelihood of chatter.b. Spindle Speed:
The spindle speed is a critical factor in controlling chatter. The spindle speed should be appropriately matched to the workpiece material and the cutting tool being used. Operating at the correct spindle speed helps prevent chatter by maintaining a stable and balanced cutting process.c. Dampening:
Some CNC machines come equipped with built-in damping systems designed to absorb vibrations during machining. These damping systems help reduce chatter, particularly during high-speed machining operations. Investing in a machine with advanced dampening features can be a practical solution to minimize chatter.d. Accuracy and Precision:
Machines with higher levels of precision and accuracy are less likely to experience chatter. The precision of the machine ensures that it maintains consistent cutting conditions, reducing the risk of vibrations and instability during machining.2. Workpiece Factors
The workpiece, including its material properties, size, and fixturing, can significantly affect chatter. Workpiece-related factors include:a. Material Properties:
The material properties of the workpiece material are crucial considerations. The hardness, density, and thermal conductivity of the material influence its ability to absorb and dissipate heat generated during machining. These properties can either promote stable cutting conditions or lead to chatter.b. Workpiece Fixturing:
Fixturing refers to how the workpiece is securely clamped or held in place during machining. Proper fixturing is essential to prevent chatter, as any movement or vibration in the workpiece can disrupt the cutting process. Securely clamping the workpiece ensures stability and reduces the risk of chatter.c. Overhang:
The overhang is the distance between the workpiece and the tool holder. Longer overhangs can amplify chatter due to increased tool deflection. Reducing the overhang or using shorter tools can help mitigate this effect.3. Tooling Factors
The choice of cutting tools, their condition, geometry, and material, can significantly impact chatter. Tooling-related factors to consider include:a. Tool Material:
Selecting the appropriate tool material based on the workpiece material is crucial. Different materials offer varying levels of wear resistance and heat resistance. The right tool material selection can reduce tool wear and the likelihood of chatter.b. Tool Geometry:
The tool geometry, including the number of flutes, rake angle, and helix angle, can influence cutting forces and, consequently, chatter. Tool geometries that provide better chip control and reduce cutting forces are preferable for chatter-prone materials.c. Tool Condition:
The condition of the cutting tools plays a significant role in chatter occurrence. Worn or damaged tools are more likely to cause chatter. Regular tool inspection and maintenance are essential to ensure that the tools are in optimal condition.4. Cutting Parameters
The selection of cutting parameters, such as feed rate, cutting speed, and depth of cut, directly affects the occurrence of chatter. Cutting parameter-related factors include:a. Feed Rate:
An inappropriate feed rate that is too high can lead to excessive cutting forces and, subsequently, chatter. Balancing the feed rate with other cutting parameters is essential to prevent chatter.b. Cutting Speed:
The cutting speed must be selected correctly based on the material and tooling being used. An improper cutting speed, whether too high or too low, can result in chatter. The right cutting speed depends on factors such as material type, tool material, and tool geometry.c. Depth of Cut:
The depth of cut affects the chip load and the forces acting on the tool. A deep cut can overload the tool, leading to vibrations and chatter. Reducing the depth of cut can help prevent chatter, particularly when machining challenging materials. Understanding the interplay of these factors and their specific impact on chatter is crucial for developing effective strategies to minimize or eliminate this detrimental phenomenon during CNC milling. In the following sections, we will delve into various strategies and best practices for reducing chatter by addressing these root causes.Strategies for Reducing Chatter
Chatter in CNC milling can be a persistent challenge, but there are numerous effective strategies and techniques to minimize or eliminate it. These strategies encompass improvements in machine tools, proper workpiece preparation, tool selection and maintenance, optimization of cutting parameters, toolpath planning, damping techniques, and the use of monitoring and control systems. Let's explore each of these strategies in detail:1. Machine Tool Improvements
Improving the CNC machine itself is an effective way to reduce chatter. Here are some approaches to consider:a. Upgrading to a More Rigid Machine:
If your current machine lacks rigidity and stability, consider upgrading to a more robust one. A rigid machine minimizes deflection and can effectively dampen vibrations during the machining process, reducing the likelihood of chatter.b. Damping Systems:
Some machines come equipped with built-in damping systems designed to absorb vibrations. These systems are especially useful for reducing chatter during high-speed machining. Upgrading to a machine with advanced dampening features can significantly reduce chatter.c. Regular Machine Maintenance:
Frequent maintenance is crucial. Regularly inspect and adjust critical machine components to ensure that the machine functions optimally. This includes checking and tightening bolts, calibrating the spindle, and maintaining the machine's overall condition.2. Workpiece Preparation
Proper workpiece preparation is essential to prevent chatter. Consider the following steps:a. Secure Fixturing:
Ensure that the workpiece is securely clamped or fixtured to prevent any unintended movement or vibration. Proper fixturing is critical to maintaining stability during machining.b. Material Selection:
Choose the appropriate material for your workpiece based on the specific machining requirements. The material's properties, such as hardness and thermal conductivity, can impact chatter. Selecting the right material can promote stable cutting conditions.c. Minimize Overhang:
Long overhangs between the workpiece and the tool can amplify chatter due to increased tool deflection. Reducing the overhang or using shorter tools can help mitigate this effect.3. Tool Selection and Maintenance
The choice of cutting tools and their condition significantly impacts chatter. Tooling-related factors to consider include:a. Tool Material:
Select the optimal tool material based on the workpiece material. Different materials offer varying levels of wear resistance and heat resistance. The right tool material selection can reduce tool wear and the likelihood of chatter.b. Tool Geometry:
Consider the tool geometry, including the number of flutes, rake angle, and helix angle. Proper tool geometries that provide good chip control and reduce cutting forces are preferable for chatter-prone materials.c. Regular Tool Maintenance:
Ensure that cutting tools are in good condition by conducting regular inspections and maintenance. Worn or damaged tools are more likely to cause chatter. Proper tool maintenance includes sharpening, reconditioning, and tool changes as necessary.4. Optimal Cutting Parameters
Selecting the right cutting parameters is essential to prevent chatter. Cutting parameter-related factors include:a. Feed Rate:
Choose an appropriate feed rate that is balanced with other cutting parameters. An excessively high feed rate can lead to increased cutting forces and chatter. Adjust the feed rate to maintain stable machining.b. Cutting Speed:
The cutting speed must be selected correctly based on the material and tooling being used. An improper cutting speed can result in chatter. The right cutting speed depends on factors such as material type, tool material, and tool geometry.c. Depth of Cut:
The depth of cut affects chip load and tool forces. A deep cut can overload the tool, leading to vibrations and chatter. Reducing the depth of cut can help prevent chatter, especially when working with challenging materials.5. Toolpath Optimization
Optimizing the toolpath can minimize chatter by avoiding sudden changes in cutting forces. Consider the following approaches:a. Trochoidal Milling:
Trochoidal milling is a technique that involves controlled, continuous toolpath patterns that can reduce chatter. It involves the tool following a circular or curved path rather than making straight cuts.b. Climb vs. Conventional Milling:
Choosing between climb milling (where the cutter rotates in the direction of feed) and conventional milling (where the cutter rotates against the direction of feed) can impact chatter. Climb milling often generates less chatter, as it reduces the impact of cutting forces.6. Damping Techniques
To address chatter during machining, various damping techniques can be employed:a. Tool Dampers:
Tool dampers are attachments that can be added to the toolholder to reduce vibrations and chatter. These dampers absorb vibrations and improve the stability of the machining process.b. Chatter-Resistant Toolholders:
Consider using toolholders that are specifically designed to reduce chatter. These toolholders incorporate advanced dampening technologies to enhance machining stability.c. Machining Chatter-Resistant Inserts:
Chatter-resistant inserts can be fitted to the cutting tool. These inserts are designed to dampen vibrations and enhance tool stability.7. Monitoring and Control Systems
To effectively manage chatter, consider the use of monitoring and control systems:a. Vibration Monitoring Systems:
Install vibration monitoring systems on the CNC machine to detect chatter in real-time. These systems can automatically adjust cutting parameters or toolpath to mitigate chatter when it occurs.b. Adaptive Control Systems:
Adaptive control systems use real-time data to adjust cutting parameters and toolpath dynamically to prevent chatter. These systems can be highly effective in chatter reduction.c. Cutting Force Measurement:
Measuring and monitoring cutting forces during machining can provide valuable data to help prevent chatter. By understanding the forces at play, adjustments can be made to minimize vibration. Implementing these strategies and techniques can significantly reduce or eliminate chatter in CNC milling, leading to improved part quality, longer tool life, machine reliability, and increased productivity. Additionally, these approaches can be adapted to suit the specific needs of your CNC machining operation, making chatter reduction a practical and achievable goal.In Conclusion
Chatter in CNC milling is a critical issue that can significantly impact the quality, efficiency, and cost-effectiveness of machining operations. Understanding the causes of chatter, including machine tool factors, workpiece-related issues, tooling factors, and cutting parameter considerations, is essential for addressing this challenge effectively. To reduce or eliminate chatter, machinists can implement a wide range of strategies and techniques:- Machine Tool Improvements: Upgrading to more rigid machines, utilizing damping systems, and ensuring regular maintenance can enhance machine stability and reduce chatter.
- Workpiece Preparation: Proper fixturing, material selection, and minimizing overhang contribute to workpiece stability and reduced chatter.
- Tool Selection and Maintenance: Choosing the right tool materials and geometries, as well as maintaining tools in good condition, can minimize chatter.
- Optimal Cutting Parameters: Adjusting feed rates, cutting speeds, and depth of cut to maintain balanced cutting forces is crucial in chatter reduction.
- Toolpath Optimization: Employing trochoidal milling and choosing the appropriate milling direction (climb or conventional) can help prevent chatter.
- Damping Techniques: Implementing tool dampers, chatter-resistant toolholders, and machining inserts designed to dampen vibrations can mitigate chatter.
- Monitoring and Control Systems: Using vibration monitoring systems, adaptive control systems, and cutting force measurement can detect and address chatter in real-time.
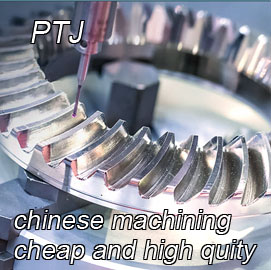
Our Services
- 5 Axis Machining
- Cnc Milling
- Cnc Turning
- Machining Industries
- Machining Process
- Surface Treatment
- Metal Machining
- Plastic Machining
- Powder Metallurgy Mold
- Die Casting
- Parts Gallery
Case Studies
- Auto Metal Parts
- Machinery Parts
- LED Heatsink
- Building Parts
- Mobile Parts
- Medical Parts
- Electronic Parts
- Tailored Machining
- Bicycle Parts
Material List
- Aluminum Machining
- Titanium Machining
- Stainless Steel Machining
- Copper Machining
- Brass Machining
- Super Alloy Machining
- Peek Machining
- UHMW Machining
- Unilate Machining
- PA6 Machining
- PPS Machining
- Teflon Machining
- Inconel Machining
- Tool Steel Machining
- More Material
Parts Gallery