A Comprehensive Guide on How to Set Up a Lathe Cutting Tool
Setting up a lathe cutting tool is a fundamental skill for any machinist, especially when dealing with Computer Numerical Control (CNC) turning machines. Proper tool setting is crucial for achieving precise and accurate machining results. In this comprehensive guide, we will delve into the intricate details of how to set up a lathe cutting tool for CNC turning. From the basics of lathe tool components to advanced techniques for optimizing cutting performance, this article aims to provide a comprehensive understanding of the process. By the end of this guide, you will have the knowledge and skills necessary to set up a lathe cutting tool with confidence and precision, ensuring optimal results in your CNC turning operations.
Understanding Lathe Cutting Tools
In the world of machining, lathe cutting tools are indispensable components for shaping and transforming raw materials into precision-engineered parts. Whether you are working with traditional manual lathes or advanced CNC turning machines, having a thorough understanding of lathe cutting tools is essential. In this section, we will delve deeper into the characteristics, functions, and types of lathe cutting tools.
Characteristics of Lathe Cutting Tools
Lathe cutting tools are designed to perform a variety of machining operations, such as turning, facing, grooving, threading, and more. These tools share several common characteristics:
- Hardness: Lathe cutting tools are typically made of high-speed steel (HSS), carbide, or other specialized tool materials. These materials are chosen for their hardness, allowing the tool to withstand the high temperatures and pressures generated during cutting.
- Cutting Edge: The cutting edge of a lathe tool is the portion that actually removes material from the workpiece. It's designed to be sharp and precise, and the geometry of the cutting edge can vary depending on the specific task the tool is intended for.
- Shank: The shank of the lathe tool is the part that is clamped into the tool holder. It provides stability and rigidity to the tool during the machining process. Shank designs can differ based on the type of tool and the manufacturer's specifications.
- Tool Holder: The tool holder is a crucial component, especially in CNC turning, as it securely holds the lathe tool in place. It must provide stability, precision, and ease of adjustment to ensure optimal tool performance.
- Geometry: The geometry of the cutting tool, including the rake angle, clearance angle, and chip breaker, plays a significant role in determining the tool's performance. Proper geometry is essential for achieving efficient material removal and chip evacuation.
- Coating: Many lathe cutting tools come with specialized coatings, such as TiN (Titanium Nitride) or TiAlN (Titanium Aluminum Nitride), to enhance tool life, reduce friction, and improve performance.
Functions of Lathe Cutting Tools
Lathe cutting tools perform several fundamental functions in the machining process:
- Material Removal: The primary function of lathe cutting tools is to remove material from a workpiece. This removal can occur through turning (rotating the workpiece while cutting), facing (creating a flat surface), or other operations.
- Dimensional Control: Cutting tools are responsible for ensuring that the dimensions of the machined part match the desired specifications. Precise control is essential for achieving accurate and consistent results.
- Surface Finish: The quality of the surface finish is determined by the cutting tool's sharpness, geometry, and the cutting parameters used. A well-maintained and properly set up cutting tool contributes to a smooth and fine surface finish.
- Chip Control: Effective chip control is essential for preventing chip buildup and maintaining a clean and safe working environment. The chip breaker on some tools helps facilitate chip removal.
- Efficiency: Lathe cutting tools are designed to make machining processes efficient and cost-effective. They help minimize material waste and optimize tool life, reducing production costs.
Types of Lathe Cutting Tools
Lathe cutting tools are available in a variety of types, each tailored to specific machining tasks. Here are some common types:
- Turning Tools: These tools are versatile and used for cylindrical turning operations. They can shape the external and internal surfaces of a workpiece.
- Boring Tools: Boring tools are employed to enlarge or finish existing holes. They are designed for precision and accuracy in hole machining.
- Parting Tools: Parting tools are used to separate a workpiece from a larger stock. They create defined parting lines with minimal waste.
- Threading Tools: Threading tools are used for cutting threads on a workpiece. They come in various shapes and sizes for different threading requirements.
- Grooving Tools: Grooving tools create grooves or recesses on a workpiece, typically for accommodating O-rings, retaining rings, or other features.
- Facing Tools: Facing tools are designed to create flat surfaces on the end of a workpiece. They are often used to achieve perpendicular surfaces or remove material from a workpiece end.
Understanding the characteristics and functions of lathe cutting tools is essential for selecting the right tool for a specific machining task. The choice of cutting tool can significantly impact the quality and efficiency of the machining process, making it a critical decision in any lathe operation. Additionally, proper maintenance and tool setup are vital to ensure consistent and precise results, which will be discussed in further detail later in this guide.
Types of Lathe Cutting Tools
Lathe cutting tools come in various types, each specifically designed for a particular machining task. Understanding these different types of cutting tools and their applications is essential for selecting the right tool for a given job. Here are some common types of lathe cutting tools:
Turning Tools:
- Round-Nose Tool: Used for general-purpose turning operations. It features a rounded cutting edge and is suitable for both roughing and finishing cuts.
- Diamond Tool: Named for its diamond-shaped cutting edge, it is ideal for precise machining on various materials, including metals and plastics.
- Square-Nose Tool: Features a square cutting edge and is typically used for facing and shoulder turning operations.
Boring Tools:Internal Boring Bar: Used to enlarge and finish existing holes in a workpiece. It is designed for precision and can create accurate internal dimensions.
Parting Tools:Parting Blade: These tools are used to cut off a workpiece from a larger stock. They create a defined parting line with minimal waste.
Threading Tools:
- Thread Cutting Tool: Designed for creating external threads on a workpiece. They come in various shapes and sizes for different threading requirements.
- Thread Chasing Tool: Used for chasing or restoring existing threads. These tools are commonly used for thread repair.
Grooving Tools:Grooving Tool: These tools create grooves or recesses on a workpiece, often to accommodate O-rings, retaining rings, or other features.
Facing Tools:Facing Tool: Used to create flat surfaces on the end of a workpiece. It is often used to achieve perpendicular surfaces or remove material from a workpiece end.
Parting and Grooving Tools:Combination Tool: These versatile tools are designed for both parting and grooving operations, saving time and tool changes.
Threading and Grooving Tools:Combination Threading and Grooving Tool: Ideal for jobs that require both threading and grooving operations on the same workpiece.
Chamfering Tools:Chamfering Tool: Used to create chamfers or beveled edges on the workpiece. Chamfers are often applied to improve the appearance and ease of assembly of machined parts.
Knurling Tools:Knurling Tool: Knurling is a process of creating a textured pattern on a workpiece, typically for improved grip or aesthetics. Knurling tools come in various patterns and designs.
Forming Tools:Form Tool: These tools are custom-designed for specific part geometries, often used for producing complex and non-standard shapes.
Specialty Tools:Profile Tools: Used for creating complex profiles on a workpiece.
Facing and Turning Tools: These are designed for both facing and turning operations.
Cutoff Tools: Designed for cutting through the workpiece to create separate parts or remove excess material.
The selection of the right cutting tool depends on factors like the material being machined, the desired finish, the required dimensions, and the specific operation being performed. It's essential to choose the appropriate tool and to maintain it properly to ensure efficient and accurate machining. Proper tool selection, along with correct setup and adjustment, is crucial for achieving high-quality results in lathe operations.
Components of a Lathe Cutting Tool
A lathe cutting tool is a precision instrument designed for shaping, cutting, and removing material from a workpiece. To understand how it works and how to properly set it up, it's crucial to be familiar with its various components. Here are the key components of a lathe cutting tool:
- Tool Holder:The tool holder is the part that secures the cutting tool in place. It attaches to the lathe's tool post and provides the necessary rigidity and stability for machining operations. Tool holders come in various designs to accommodate different types of cutting tools.
- Shank:The shank is the part of the cutting tool that fits into the tool holder. It is typically cylindrical and is clamped securely within the holder. The shank's dimensions and shape may vary based on the tool type and design.
- Cutting Edge:The cutting edge is the sharp portion of the tool that contacts and removes material from the workpiece. The quality of the cutting edge and its geometry significantly affect the cutting performance and surface finish. It's essential to maintain the cutting edge's sharpness and precision.
- Insert:Many modern cutting tools use replaceable inserts, which are typically made of hard materials like carbide or ceramic. These inserts have the cutting geometry and are secured in a pocket on the cutting tool. They can be rotated or replaced when they become worn or damaged, prolonging the tool's life.
- Tool Nose:The tool nose is the very tip of the cutting tool where the cutting edge and insert (if used) come together. The tool nose must be accurately positioned and aligned for precise machining. Some lathe cutting tools have an adjustable tool nose radius for better control over tool performance.
- Tool Flank:The tool flank is the side surface of the cutting tool that is not part of the cutting edge. Proper clearance angles on the tool flank ensure chip evacuation and reduce friction between the tool and the workpiece.
- Tool Rake Face:The rake face is the surface of the cutting tool that faces the workpiece. The angle and condition of the rake face affect chip formation and the cutting process's efficiency. The rake angle is a critical aspect of the tool's geometry.
- Tool Relief Angle:The relief angle is the angle between the tool flank and the tool's axis. It ensures that the cutting edge doesn't rub against the workpiece, reducing friction and heat generation.
- Tool Clearance Angle:The clearance angle is the angle between the rake face and the workpiece surface. It allows chips to flow smoothly and prevents interference between the tool and the workpiece.
- Chip Breaker (if applicable):Some cutting tools, especially those used for roughing operations, feature a chip breaker, a groove or notch on the rake face. The chip breaker helps in controlling chip formation and improving chip evacuation.
Proper assembly, alignment, and maintenance of these components are essential for achieving precise and efficient machining. The choice of cutting tool and its setup must be tailored to the specific machining operation and material being worked on. Regular inspection and maintenance of the cutting tool components are also necessary to ensure consistent and high-quality results.
Choosing the Right Cutting Tool for the Job
Selecting the right cutting tool is a critical decision in any machining operation, as it greatly influences the quality, efficiency, and precision of the work. Several factors should be considered when choosing the appropriate cutting tool for a specific job. Here's a guide on how to choose the right cutting tool for your machining project:
1. Material of the Workpiece:
The material you are machining is one of the most critical factors in tool selection. Different materials have varying hardness, thermal conductivity, and abrasiveness. Consider the following:
- Hardness: Hard materials like hardened steel or ceramics require cutting tools with hard cutting edges, such as carbide inserts, to withstand the high cutting forces.
- Soft Materials: For softer materials like aluminum or plastics, high-speed steel (HSS) or other tool materials may be sufficient.
2. Machining Operation:
The specific operation you are performing, such as turning, milling, drilling, threading, or grooving, will dictate the type of cutting tool you need. Different tools are designed for various tasks, and choosing the right one ensures optimal performance.
3. Cutting Speed and Feed Rate:
Determine the required cutting speed and feed rate based on the material and the machining operation. Cutting tool manufacturers provide recommendations for these parameters based on the tool's design and the material being machined. Adhering to these recommendations is crucial for achieving the desired results.
4. Tool Geometry:
Consider the geometry of the cutting tool, including the rake angle, clearance angle, and tool nose radius. The tool geometry should match the material and the type of cut. For example, a positive rake angle is suitable for softer materials, while a negative rake angle is better for harder materials.
5. Workpiece Dimensions:
The size and dimensions of the workpiece also influence tool selection. Some cutting tools are better suited for roughing operations to remove bulk material quickly, while others are designed for finishing to achieve precise dimensions and surface finishes.
6. Surface Finish Requirements:
If you require a specific surface finish, select a cutting tool with the appropriate geometry and sharpness. Finishing tools are designed to provide a smoother surface finish, while roughing tools are more efficient for material removal.
7. Tool Material:
The choice of tool material is crucial. Carbide, high-speed steel (HSS), ceramic, and coated tools all have their advantages and limitations. Consider factors like tool life, wear resistance, and the cost of the tool material in your decision.
8. Coolant and Lubrication:
Consider whether the cutting operation requires coolant or lubrication. Some materials generate excessive heat during machining, and using the right coolant or lubricant can prolong tool life and improve cutting performance.
9. Tool Coatings:
Many modern cutting tools come with specialized coatings like TiN (Titanium Nitride) or TiAlN (Titanium Aluminum Nitride) to improve wear resistance and reduce friction. Choose a tool with an appropriate coating for your specific application.
10. Cost Considerations:
Balancing the cost of the cutting tool with its performance and longevity is crucial. While premium tools may offer longer tool life and better performance, it's essential to find a balance that aligns with your project's budget.
11. Tool Holder and Machine Compatibility:
Ensure that the chosen cutting tool is compatible with your lathe or machining center's tool holder system. The tool holder should provide stability and rigidity to the cutting tool during the machining process.
Ultimately, the right cutting tool for the job will depend on a combination of these factors. Always consult the tool manufacturer's recommendations and consider seeking advice from experienced machinists or tooling experts if you are unsure. Proper tool selection and setup are fundamental for achieving efficient and precise machining results.
Setting Up the Lathe Cutting Tool
Setting up a lathe cutting tool for CNC turning is a systematic process that involves several crucial steps. Each step is vital to ensure that the cutting tool is correctly positioned and aligned, ultimately leading to precise and efficient machining. Let's walk through the process step by step:
Step 1: Preparing the Lathe and Workpiece
Before you can set up the cutting tool, it's essential to prepare both the lathe and the workpiece:
- Secure the Workpiece: Make sure the workpiece is securely clamped in the lathe chuck or collet. Ensure that it rotates smoothly without any wobbling or vibration.
- Safety: Ensure all safety measures are in place, including the use of appropriate personal protective equipment (PPE) and the correct lathe settings.
Step 2: Selecting the Correct Tool Holder
The tool holder is a critical component in the setup process. Choose the appropriate tool holder based on factors like the type of cutting tool, the operation being performed, and the lathe's tool post system.
- Match the Tool Holder to the Cutting Tool: Ensure that the tool holder is compatible with the type and size of the cutting tool you intend to use.
- Tool Holder Rigidity: Choose a tool holder that provides stability and rigidity. This is especially important in high-precision applications.
Step 3: Mounting the Cutting Tool
Mounting the cutting tool involves securing it in the tool holder and ensuring it is firmly and correctly positioned:
- Secure the Cutting Tool: Insert the cutting tool into the tool holder and tighten any clamping mechanisms, such as set screws or collets. Ensure the tool is held securely.
- Orientation: Verify that the cutting tool is oriented correctly with respect to the workpiece. The tool should be positioned to engage the workpiece at the desired angle and depth.
Step 4: Adjusting Tool Height and Centerline Alignment
Correct tool height and centerline alignment are crucial for achieving precise machining dimensions:
- Tool Height Adjustment: Adjust the tool's height to align it with the lathe's spindle centerline. Use a tool height gauge or a test bar to set the tool at the correct height.
- Centerline Alignment: Ensure that the tool is aligned with the lathe's spindle centerline. Misalignment can result in off-center machining, affecting part accuracy.
Step 5: Setting Tool Nose Radius Compensation
For CNC turning, tool nose radius compensation accounts for the geometry of the cutting tool. This is particularly important when using insert tools:
- Determine the Tool Nose Radius: Measure or look up the exact nose radius of the cutting tool insert you are using.
- Input the Radius Value: In the CNC control software, input the measured tool nose radius value to ensure the machine compensates for the tool's geometry when machining.
Step 6: Setting Tool Offsets
Tool offsets account for variations in tool dimensions and workpiece geometry. They ensure that the tool's position is accurately adjusted for machining:
- Select the Correct Tool Offset: Determine the appropriate tool offset value based on the tool's geometry and the machining operation. This offset value compensates for any discrepancies.
- Enter Offset Values: Input the chosen offset values into the CNC control software. These values will instruct the machine on how to adjust the tool's position accurately.
Throughout the tool setup process, use precision measuring instruments like micrometers, height gauges, and dial indicators to verify and fine-tune tool alignment. Regularly inspect and maintain the cutting tool to ensure it remains sharp and in good condition, as a well-maintained tool contributes to consistent and accurate machining results.
Properly setting up the lathe cutting tool in these steps is crucial for achieving optimal results in CNC turning operations. Precision and attention to detail during tool setup are key factors in producing high-quality machined parts.
Optimizing Cutting Parameters for CNC Turning
Optimizing cutting parameters is essential for achieving efficient and high-quality CNC turning operations. The four key aspects to consider when optimizing cutting parameters are speeds and feeds, depth of cut, cutting fluids and lubricants, and tool life management.
1. Speeds and Feeds:
- a. Cutting Speed (Surface Speed):Cutting speed, often referred to as surface speed, is the speed at which the workpiece and cutting tool interact. It is measured in surface feet per minute (SFM) or meters per minute (m/min).To optimize cutting speed, consider the material being machined and the tool's material. High-speed steel (HSS) tools have lower recommended cutting speeds than carbide tools, for example.Consult tool manufacturer data or machining handbooks to determine recommended cutting speeds for specific materials and tooling.
- b. Feed Rate:Feed rate is the linear speed at which the cutting tool advances into the workpiece. It is measured in inches per revolution (IPR) or millimeters per revolution (mm/rev).To optimize feed rate, consider factors like material properties, tool geometry, and the desired surface finish. Higher feed rates are generally more productive but may require sturdier tooling.
- c. Cutting Speed and Feed Rate Relationship:Balancing cutting speed and feed rate is crucial for efficient material removal. An increase in cutting speed typically allows for a higher feed rate, but the two must be adjusted together to prevent tool wear and overheating.
2. Depth of Cut:
- a. Depth of Cut (DOC):The depth of cut is the distance the cutting tool penetrates into the workpiece. It is essential to consider the material and tool's capabilities.Optimize the depth of cut based on the material's hardness and the tool's strength and rigidity. Shallow cuts might be necessary for harder materials, while deeper cuts can be achieved in softer materials.
- b. Axial and Radial Depth of Cut:In CNC turning, consider both axial (along the workpiece's length) and radial (across the workpiece's diameter) depth of cut. Optimal depths for each will vary based on the operation and material.
3. Cutting Fluids and Lubricants:
- a. Selecting the Right Cutting Fluid:Cutting fluids are essential for dissipating heat, reducing friction, and improving chip evacuation. Choose the appropriate cutting fluid based on the material and machining operation.Water-soluble coolant, mineral oil-based, or synthetic coolants may be preferred for different materials.
- b. Proper Application:Apply cutting fluids effectively to the cutting area to ensure adequate lubrication and cooling. This can be done through flood cooling, mist systems, or through-tool coolant delivery, depending on the machine's capabilities.
- c. Monitoring and Maintenance:Regularly monitor cutting fluid levels, condition, and contamination to ensure they remain effective. Maintain cutting fluid systems to prevent issues such as bacterial growth and degradation.
4. Tool Life Management:
- a. Tool Inspection and Maintenance:Implement a routine tool inspection and maintenance program to ensure tools are in good condition. Dull or damaged tools can result in poor machining quality and reduced tool life.
- b. Tool Replacement Schedule:Establish a tool replacement schedule based on factors like tool wear, machine uptime, and production requirements. This helps prevent unexpected tool failures and maintain consistent machining quality.
- c. Tool Life Optimization:Some tool materials and coatings offer longer tool life. Consider using high-performance tooling to optimize tool life and reduce production downtime.
- d. Tool Chip Control:Effective chip control, including the use of chip breakers and proper tool geometry, can extend tool life by reducing chip-induced wear.
Optimizing cutting parameters in CNC turning is a continuous process. Experimentation and fine-tuning may be required to find the best parameters for a specific application. Regularly monitor and adjust these parameters to ensure optimal machining performance, tool life, and part quality. Properly optimized cutting parameters not only improve machining efficiency but also reduce tool wear and, ultimately, production costs.
Troubleshooting Common Issues in Tool Setting
Troubleshooting common issues in tool setting is an essential skill for machinists and CNC operators. Understanding and addressing these issues can help maintain the precision and quality of machining operations. Here are some common tool setting problems and their solutions:
1. Tool Chatter:
Issue: Tool chatter occurs when the cutting tool vibrates during the machining process, leading to poor surface finish, tool wear, and potential damage to the workpiece.
Solution:
- Reduce Speed or Increase Feed: Adjust cutting parameters by either decreasing the cutting speed or increasing the feed rate. This change can dampen vibrations and reduce chatter.
- Check Tool Rigidity: Ensure that the tool holder and tool are correctly secured and that the tool is not extending too far from the holder.
- Check Workpiece Clamping: Make sure the workpiece is securely clamped to prevent any workpiece-related vibrations.
- Use Dampening Techniques: Some machines come with features for dampening vibrations. If available, consider using them.
- Choose a Stiffer Tool: A more rigid tool, such as one with fewer flutes, can help reduce chatter.
2. Poor Surface Finish:
Issue: A poor surface finish can result from issues with tool setup or cutting parameters, leading to rough or inconsistent surfaces on the workpiece.
Solution:
- Check Tool Geometry: Ensure that the cutting tool's geometry is appropriate for the operation. A sharp tool with the correct geometry is crucial for achieving a good surface finish.
- Optimize Cutting Parameters: Adjust cutting speed, feed rate, and depth of cut to find the best combination for the specific material and operation.
- Check for Tool Wear: Inspect the tool for signs of wear or damage, such as chipped edges. Replace or regrind the tool as needed.
- Use Appropriate Cutting Fluid: Proper lubrication and cooling can significantly affect the surface finish. Use the right cutting fluid for the material and operation.
- Minimize Vibration: Address vibration issues to avoid creating surface irregularities.
3. Dimensional Inaccuracies:
Issue: Parts may have incorrect dimensions due to misaligned tooling or tool wear.
Solution:
- Check Tool Setup: Verify that the tool is correctly set up with the right height and alignment with respect to the workpiece.
- Calibrate Machine: Ensure the CNC machine is properly calibrated and that it accurately interprets the tool offsets and tool data.
- Adjust Tool Offsets: Correct any errors in tool offsets by accurately measuring the tool and entering the proper offset values in the CNC control.
- Inspect Tool Wear: Regularly inspect the cutting tool for wear and replace or regrind it when necessary.
4. Chip Control Problems:
Issue: Improper chip control can lead to issues such as chip clogging, poor chip evacuation, and damage to the workpiece or tool.
Solution:
- Choose the Right Tool Geometry: Select a cutting tool with the appropriate chip breaker or geometry for the material and operation.
- Optimize Cutting Parameters: Adjust feed rates, cutting speeds, and depths of cut to optimize chip formation and evacuation.
- Use Adequate Lubrication: Proper use of cutting fluids can help lubricate and facilitate chip evacuation.
- Check Tool and Workpiece Alignment: Ensure that the tool is correctly aligned with the workpiece to prevent chip-related issues.
5. Tool Breakage:
Issue: Tool breakage can occur due to excessive force, incorrect tool setup, or material-related issues.
Solution:
- Optimize Cutting Parameters: Reduce cutting forces by adjusting parameters like feed rates, cutting speeds, and depths of cut.
- Check Tool Setup: Ensure that the tool is securely mounted in the tool holder and that it is correctly aligned.
- Use Proper Tool Material: Choose the right tool material for the specific material you are machining. For instance, carbide tools are better for hard materials.
- Inspect for Tool Wear: Regularly check the tool for signs of wear and replace it before it becomes excessively worn and prone to breaking.
Addressing these common tool setting issues requires a combination of proper training, regular maintenance, and a systematic approach to troubleshooting. The ability to diagnose and resolve tool-related problems is critical for achieving high-quality and efficient machining results.
In Conclusion
The process of setting up and optimizing lathe cutting tools for CNC turning is a crucial aspect of machining that significantly impacts the quality, efficiency, and precision of manufacturing processes. A deep understanding of the components and functions of cutting tools, as well as the factors involved in tool selection, is essential for machinists and CNC operators.
Properly setting up a cutting tool involves a systematic approach, from preparing the lathe and workpiece to selecting the correct tool holder, mounting the tool, adjusting the tool height and centerline alignment, and configuring tool nose radius compensation and tool offsets. Each step plays a pivotal role in achieving precise and efficient machining results.
Optimizing cutting parameters, including speeds and feeds, depth of cut, cutting fluids, and tool life management, is another critical aspect of CNC turning. By carefully selecting the right parameters, machinists can enhance productivity, maintain tool longevity, and improve surface finish quality.
Finally, being able to troubleshoot common tool setting issues, such as tool chatter, poor surface finish, dimensional inaccuracies, chip control problems, and tool breakage, is essential for maintaining consistent and high-quality machining results. Identifying these issues and implementing appropriate solutions ensures that the machining process remains smooth and efficient.
Overall, a comprehensive understanding of lathe cutting tools and their setup, combined with the ability to optimize cutting parameters and troubleshoot issues, empowers machinists to achieve the best results in CNC turning operations. Continuous learning, training, and experience are key in refining these skills and ensuring successful machining processes.
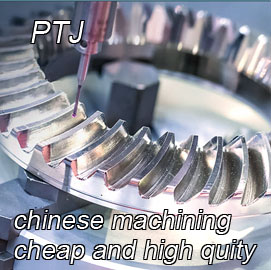
- 5 Axis Machining
- Cnc Milling
- Cnc Turning
- Machining Industries
- Machining Process
- Surface Treatment
- Metal Machining
- Plastic Machining
- Powder Metallurgy Mold
- Die Casting
- Parts Gallery
- Auto Metal Parts
- Machinery Parts
- LED Heatsink
- Building Parts
- Mobile Parts
- Medical Parts
- Electronic Parts
- Tailored Machining
- Bicycle Parts
- Aluminum Machining
- Titanium Machining
- Stainless Steel Machining
- Copper Machining
- Brass Machining
- Super Alloy Machining
- Peek Machining
- UHMW Machining
- Unilate Machining
- PA6 Machining
- PPS Machining
- Teflon Machining
- Inconel Machining
- Tool Steel Machining
- More Material