How to Cut Aluminum Sheet Metal Fast | Best Tips & Tool to Cut Aluminum Sheet
2023-10-30
Cutting aluminum sheet metal efficiently and accurately is crucial for various DIY projects, home improvements, or professional applications. Aluminum sheet metal is a popular material due to its lightweight, corrosion-resistant properties, and versatility. However, it can be challenging to cut without the right tools and techniques. In this comprehensive guide, we will explore the best ways and tools to cut aluminum sheet metal quickly and effectively. By the end of this article, you'll be well-equipped to tackle your aluminum sheet metal cutting tasks with confidence.
What Is Aluminum Sheet Metal
Aluminum sheet metal is a widely used material known for its remarkable properties and diverse applications. It is a versatile alloy made from aluminum, a lightweight and corrosion-resistant metal, making it an excellent choice for a multitude of projects. From constructing aircraft components to crafting kitchen utensils and architectural designs, aluminum sheet metal finds its place in various industries and DIY endeavors.Importance of Accurate Aluminum Sheet Metal Cutting
The importance of precise aluminum sheet metal cutting cannot be overstated. Whether you are an experienced professional or a hobbyist, achieving accurate cuts is a fundamental requirement for any project involving aluminum sheet metal. The quality of the cuts directly impacts the final product's aesthetics, functionality, and structural integrity. Inaccurate cuts can lead to material wastage, delayed project timelines, and even compromise the safety of the end product. Therefore, understanding the best techniques and tools for cutting aluminum sheet metal is essential for ensuring the success of your endeavors. In this comprehensive guide, we will explore the various methods and tools available to cut aluminum sheet metal efficiently, allowing you to achieve precise results every time.Safety Precautions
When working with aluminum sheet metal, prioritizing safety is paramount to protect yourself and others in the vicinity. This section outlines essential safety precautions, including the use of Personal Protective Equipment (PPE) and creating a safe workspace setup.Personal Protective Equipment (PPE)
Personal Protective Equipment is your first line of defense against potential hazards when cutting aluminum sheet metal. Properly chosen PPE can help prevent injuries and ensure your well-being during the cutting process. Here's a breakdown of the necessary PPE:- Safety Glasses or Goggles: Protect your eyes from metal chips, debris, and abrasive particles generated during the cutting process. Ensure the eyewear you choose complies with safety standards.
- Hearing Protection: When using loud power tools, such as circular saws or grinders, wearing ear protection is crucial. Prolonged exposure to high noise levels can lead to hearing damage.
- Gloves: Wearing gloves is essential to shield your hands from sharp edges, abrasive surfaces, and hot metal. Opt for gloves designed for metalworking, offering both protection and dexterity.
- Long-Sleeved Clothing: To further protect your arms from cuts, burns, or other potential hazards, wear long-sleeved, durable clothing made from non-flammable materials.
- Dust Mask or Respirator: If your cutting process generates dust, fumes, or noxious gases, use a dust mask or respirator to protect your respiratory system. Choose the appropriate mask type based on the nature of the materials you are working with.
- Steel-Toed Boots: Sturdy, steel-toed boots provide protection for your feet against falling objects and potential hazards in your workspace.
Safe Workspace Setup
A well-organized and safe workspace is crucial for minimizing risks associated with cutting aluminum sheet metal. Follow these guidelines to ensure a safe environment:- Adequate Ventilation: Proper ventilation is crucial to disperse fumes and gases that may be produced during the cutting process. Install exhaust fans, open doors or windows, or use air filtration systems to maintain good air quality.
- Well-Lit Workspace: Ensure that your workspace is well-lit, with ample lighting directed at the cutting area. This enhances visibility, reducing the risk of accidents caused by poor lighting.
- Clean and Clutter-Free Area: A clean and organized workspace is less prone to accidents. Remove any obstacles, tools, or materials that are not in use. Keep your workspace clutter-free to prevent tripping hazards.
- Fire Extinguisher: Always have a fire extinguisher readily accessible in your workspace. In the event of an accidental fire, quick access to a fire extinguisher can make a significant difference in preventing a small incident from turning into a disaster.
- Proper Electrical Setup: Ensure that your power tools are properly grounded and in good working condition. Avoid using extension cords that are frayed or damaged. Follow safety guidelines for using electrical equipment.
- Safe Storage of Materials: Store aluminum sheet metal and other materials in a secure and organized manner. Avoid stacking materials precariously, which could lead to accidents.
- Emergency Response Plan: Have a basic emergency response plan in place. Ensure that you and others in your workspace know what to do in case of accidents or injuries. This includes knowledge of the location of first aid kits and emergency contact numbers.
Essential Tools for Cutting Aluminum Sheet Metal
To cut aluminum sheet metal efficiently and accurately, you need the right tools. This section introduces the essential tools for cutting aluminum sheet metal and provides an overview of their capabilities.1. Snips and Shears
Description: Snips and shears are hand tools designed for cutting thin aluminum sheet metal. They come in various styles, including straight-cut, left-cut, and right-cut. These tools are ideal for cutting small pieces of aluminum sheet metal and making precise, intricate cuts. Pros:- Portable and easy to use.
- Suitable for small or detailed cuts.
- Affordable and widely available.
- Limited to thin aluminum sheets.
- May require more effort for thicker materials.
2. Jigsaw
Description: A jigsaw is a versatile power tool equipped with a thin, fine-toothed blade. It is used for cutting intricate shapes in aluminum sheet metal. Jigsaws are suitable for curved cuts and shapes. Pros:- Versatile for curved or irregular cuts.
- Relatively affordable.
- Provides clean cuts with the right blade.
- May not be as fast as other power tools.
- Not ideal for long, straight cuts.
3. Circular Saw
Description: Circular saws are powerful tools that can cut straight lines in aluminum sheet metal. They are commonly used for longer, straight cuts and are available with metal-cutting blades. Pros:- Suitable for long, straight cuts.
- Fast and efficient.
- Various metal-cutting blades available.
- Not ideal for curved or intricate cuts.
- Can produce a significant amount of sparks and heat.
4. Table Saw
Description: A table saw, equipped with a carbide-tipped blade suitable for metal, is excellent for making precise, straight cuts in larger aluminum sheets. This tool is typically used in professional settings. Pros:- Provides highly accurate, straight cuts.
- Suitable for large and thick aluminum sheets.
- Offers precise control and repeatability.
- Expensive and requires a dedicated workspace.
- Not ideal for curved or beveled cuts.
5. Bandsaw
Description: A bandsaw is a versatile tool for cutting various materials, including aluminum sheet metal. It is highly effective for cutting curves and shapes in both thin and thick sheets. Pros:- Suitable for straight, curved, and intricate cuts.
- Versatile and available in various sizes.
- Minimizes waste due to narrow blade width.
- Requires some skill to operate effectively.
- May not be as fast as some other tools.
6. Scroll Saw
Description: A scroll saw is similar to a jigsaw but is designed for more intricate, fine-detail work. It's suitable for cutting decorative or artistic shapes in aluminum sheet metal. Pros:- Ideal for intricate and artistic designs.
- Provides excellent control and precision.
- Minimal vibration for fine work.
- Limited to small or medium-sized projects.
- Slower than other power tools for straight cuts.
7. Router
Description: A router equipped with the appropriate metal-cutting bits can be used for trimming and shaping aluminum sheet metal. It's useful for finishing edges and adding decorative details. Pros:- Ideal for adding decorative edges and profiles.
- Versatile tool for various materials.
- Precise control for finishing work.
- Primarily used for trimming and finishing, not for primary cutting.
- Limited to edge work and detailing.
8. Plasma Cutter
Description: A plasma cutter is a high-powered tool that uses a high-velocity jet of ionized gas to cut through metal. It's excellent for cutting thick aluminum sheets quickly and cleanly. Pros:- Fast and efficient for thick materials.
- Minimal heat-affected zone, reducing warping.
- Suitable for industrial applications.
- Expensive and may require specialized training.
- Not as precise as some other cutting methods.
9. Waterjet Cutter
Description: A waterjet cutter employs a high-pressure stream of water mixed with abrasive materials to cut through aluminum sheet metal. It's a precise and versatile cutting method, suitable for various thicknesses and intricate designs. Pros:- Precise and clean cuts with no heat-affected zone.
- Suitable for a wide range of materials and thicknesses.
- Minimal material waste.
- Expensive and typically used in industrial or professional settings.
- Requires specialized equipment and training.
Choosing the Right Tool
Selecting the appropriate tool for cutting aluminum sheet metal is a crucial decision that can significantly impact the efficiency and quality of your work. To make an informed choice, it's essential to consider various factors and understand the types of cuts you need to perform.Factors to Consider
- Material Thickness: The thickness of the aluminum sheet metal is a primary consideration when choosing a cutting tool. Thicker sheets may require more robust tools with higher cutting capacities, while thinner sheets can be cut with a wider range of options.
- Cut Type: The type of cut you need determines the tool you should use. Consider whether you require straight cuts, curved cuts, or intricate shapes. Some tools are better suited for specific cut types.
- Accuracy: Depending on the precision required for your project, you may need a tool that provides high accuracy. If your project demands precise measurements and cuts, a tool like a table saw or waterjet cutter may be more appropriate.
- Available Tools: Utilize the tools you have access to or can afford. Specialized equipment may be necessary for professionals but may not be cost-effective for occasional DIYers.
- Budget: Your budget may influence your tool choice. Some tools are more affordable and accessible, while others can be quite expensive. Balance the cost with your project requirements.
- Workspace and Safety: Ensure your workspace can accommodate the chosen tool safely. Some tools, such as plasma cutters or waterjet cutters, require specialized setups and safety measures.
- Project Complexity: The complexity of your project is another crucial factor. For straightforward, linear cuts in thinner sheets, simpler tools like snips, shears, or circular saws may suffice. However, intricate or artistic designs may necessitate more specialized tools like routers or scroll saws.
Types of Cuts
- Straight Cuts: When your project primarily requires straight cuts, tools like circular saws, table saws, and bandsaws excel. They are designed for precision and speed in cutting straight lines.
- Curved Cuts: For curved or rounded cuts, jigsaws, bandsaws, and scroll saws are the go-to options. These tools allow for greater maneuverability and control in achieving smooth curves.
- Intricate Cuts: When intricate designs or patterns are part of your project, scroll saws and routers are ideal. They provide the precision required to create detailed, artistic shapes.
- Thick Materials: When working with thicker aluminum sheet metal, plasma cutters and waterjet cutters are suitable. These tools can effortlessly handle the increased material thickness.
- Minimal Heat Impact: If you aim to minimize the heat-affected zone (HAZ) in your cuts, waterjet cutters and plasma cutters are excellent choices. They use alternative methods, such as high-pressure water or ionized gas, to avoid excessive heat generation.
- Speed and Efficiency: For projects where speed is crucial, circular saws and plasma cutters are fast and efficient. They can complete cuts swiftly, saving time.
- Low Waste: To minimize material waste, consider using tools like waterjet cutters, which produce minimal kerf (the width of the cut). This results in less material being lost during cutting.
- Detail Work: Detail-oriented projects benefit from the use of scroll saws or routers. These tools provide fine control and are capable of intricate detailing.
Preparation for Cutting Aluminum Sheet Metal
Before you begin cutting aluminum sheet metal, thorough preparation is essential to ensure accurate and efficient results. This section discusses the key steps involved in preparation, including measuring and marking, securing the material, and selecting the appropriate blade.Measuring and Marking
- Accurate Measurements: Start by measuring and marking the dimensions and shape of the cut you need. Use a steel rule or a measuring tape to ensure precise measurements. Double-check your measurements to avoid errors.
- Marking Tools: Use a scribe, a pencil, or a fine-tip marker to mark the lines on the aluminum sheet metal. Ensure that your marks are clear and visible. Consider using a square or a straightedge to create straight lines for your cuts.
- Account for Kerf: Keep in mind the kerf, which is the width of the cut made by the tool you are using. Adjust your measurements to account for the kerf so that your final piece matches your intended dimensions.
- Layout Considerations: Consider the orientation and layout of your cuts. Avoid making cuts too close to the edge of the sheet, as this can weaken the structure. If you need multiple cuts or intricate designs, plan their sequence to avoid interference.
Securing the Material
- Workbench or Cutting Surface: Place the aluminum sheet metal on a stable and level workbench or cutting surface. Ensure that the work surface is clean, free of debris, and well-supported.
- Clamps: Use clamps to secure the aluminum sheet metal in place. Clamping the material prevents it from moving during cutting, ensuring straight and accurate cuts. Position the clamps outside the area you plan to cut to avoid interfering with the tool.
- Workpiece Support: For larger sheets, use support stands or sawhorses to elevate and support the material. This helps prevent the sheet from sagging or bending during cutting.
- Safety Considerations: Make sure the material is securely fastened, and there are no loose or dangling objects that could get caught in the tool during cutting. Safety first!
Blade Selection
- Consider Material Thickness: Choose a blade or cutting tool appropriate for the thickness of the aluminum sheet metal. For thin sheets, a fine-toothed blade is suitable, while thicker sheets may require a coarser, more robust blade. Ensure that the blade is designed for cutting metal.
- Tooth Count: Pay attention to the tooth count on the blade if you're using a saw. A higher tooth count provides a smoother cut for thinner materials, while a lower tooth count is better for thicker materials.
- Carbide-Tipped Blades: For power saws, consider using carbide-tipped blades. Carbide is a durable material that maintains sharpness for longer, providing cleaner and more efficient cuts.
- Cooling and Lubrication: If you're using a tool that generates heat, such as a saw or a router, consider using a cooling or lubrication system to reduce friction and prevent overheating. This is particularly important for thick aluminum sheets.
- Regular Blade Inspection: Periodically inspect the blade or cutting tool to ensure it is in good condition. Dull blades can result in uneven cuts and increased wear on the tool.
Methods for Cutting Aluminum Sheet Metal
There are various methods for cutting aluminum sheet metal, each suited to different types of cuts and thicknesses. In this section, we'll explore these methods and the tools commonly used for each.1. Cutting with Snips and Shears
Tools: Snips and shears Description: Snips and shears are hand tools designed for cutting thin aluminum sheet metal. They are ideal for making small, precise cuts and are particularly useful for curved or irregular shapes. Process:- Mark your cutting line on the aluminum sheet metal using a straightedge or template.
- Position the snips or shears along the marked line.
- Apply even pressure and make slow, controlled cuts following the marked line.
- Ensure that your hand follows the blades to prevent bending or distorting the metal.
- Suitable for thin aluminum sheets.
- Ideal for intricate or curved cuts.
- Portable and easy to use.
- May not be suitable for thick materials.
- Slower for long, straight cuts.
2. Cutting with a Jigsaw
Tool: Jigsaw Description: A jigsaw is a versatile power tool equipped with a fine-toothed blade, making it suitable for cutting intricate shapes and curves in aluminum sheet metal. Process:- Secure the aluminum sheet metal fabrication to prevent movement during cutting.
- Attach a metal-cutting blade to the jigsaw.
- Start the jigsaw and guide it along the marked cutting line, keeping the blade moving steadily to prevent overheating.
- Ideal for curved and irregular cuts.
- Offers good control and maneuverability.
- Versatile for various projects.
- May not be as fast as some power tools.
- Generates noise and vibrations.
3. Cutting with a Circular Saw
Tool: Circular saw Description: Circular saws are power tools with a circular blade, designed for straight-line cuts in a wide range of materials, including aluminum sheet metal. Process:- Secure the aluminum sheet metal, ensuring it doesn't move during cutting.
- Attach a metal-cutting blade with fine teeth to the circular saw.
- Start the saw and guide it along the marked cutting line. Keep the blade moving steadily to prevent overheating.
- Ideal for long, straight cuts.
- Fast and efficient.
- Suitable for thick aluminum sheets.
- Not suitable for curved or intricate cuts.
- Can generate sparks and heat.
4. Cutting with a Table Saw
Tool: Table saw Description: Table saws are stationary power tools with a flat, circular blade used for precision cutting. They are typically employed for straight-line cuts in larger aluminum sheets. Process:- Set up the aluminum sheet metal and ensure it's securely positioned.
- Equip the table saw with a carbide-tipped blade designed for metal.
- Turn on the table saw and guide the sheet metal along the blade for a precise cut.
- Provides highly accurate, straight cuts.
- Suitable for large and thick aluminum sheets.
- Offers excellent control and repeatability.
- Expensive and requires dedicated workspace.
- Not ideal for curved or beveled cuts.
5. Cutting with a Bandsaw
Tool: Bandsaw Description: Bandsaws are versatile power tools equipped with a continuous loop of teethed metal, allowing for straight and curved cuts. They are commonly used for cutting aluminum sheet metal due to their adaptability. Process:- Secure the aluminum sheet metal and ensure it's stable.
- Choose a metal-cutting blade with the right tooth count.
- Start the bandsaw and guide the sheet metal along the blade for the desired cut.
- Suitable for straight, curved, and intricate cuts.
- Versatile tool available in various sizes.
- Minimizes material waste due to the narrow blade width.
- Requires some skill to operate effectively.
- May not be as fast as some other power tools.
Tips for Clean and Accurate Cuts
To achieve clean and accurate cuts when working with aluminum sheet metal, it's crucial to follow best practices and consider various factors that affect the cutting process. Here are some tips to help you attain precise results:1. Blade Maintenance
- Keep Blades Sharp: Regularly inspect and maintain the cutting tool's blade. Dull blades can lead to uneven cuts and may cause the material to heat up excessively. Sharpen or replace blades as needed.
- Proper Blade Selection: Choose the right type of blade for your cutting tool and material. Make sure it's appropriate for cutting aluminum sheet metal. Carbide-tipped blades are durable and maintain sharpness longer.
- Lubrication and Cooling: Use cutting fluid, coolants, or lubricants when appropriate. These help reduce friction, heat, and wear on the blade. Lubricants can improve the quality of the cut and extend blade life.
2. Cutting Speed
- Consistent Feed Rate: Maintain a consistent and moderate feed rate when guiding the cutting tool through the material. Avoid pushing too fast, which can cause blade deflection, or too slowly, which can create excess heat.
- Match Tool to Material: Use a cutting tool and method that matches the material thickness. For thin sheets, use tools that can operate at higher speeds. For thick sheets, opt for tools capable of slower, more powerful cuts.
- Practice Control: Maintain steady control of the tool throughout the cut. Consistency in speed and direction helps achieve clean, even cuts. Avoid sudden changes or stops during cutting.
3. Cooling Methods
- Use Cooling Systems: For cutting methods that generate heat, such as saws and routers, employ cooling systems. These can include air jets, coolants, or a stream of water to keep the tool and material cool. Coolants also help extend the life of cutting tools.
- Monitor Heat-Affected Zone (HAZ): Be aware of the heat-affected zone during cutting. A smaller HAZ indicates less heat transfer into the material, which can help maintain material integrity and reduce warping.
- Minimize Friction: Reducing friction between the blade and the material can prevent heat buildup. Proper lubrication and cooling methods can effectively reduce friction and improve the quality of cuts.
Dealing with Common Challenges
Cutting aluminum sheet metal can present several common challenges, including material warping, burrs, and issues related to noise and vibration. In this section, we'll explore strategies for addressing these challenges.1. Preventing Warping
- a. Proper Tool Selection: Choose the right cutting method and tool for the thickness of the aluminum sheet metal. Tools that generate excessive heat, like plasma cutters or oxy-fuel torches, may cause warping in thin materials. Waterjet cutters and shears produce less heat and are less likely to cause warping.
- b. Cooling and Lubrication: Utilize cooling methods and lubrication, especially when using power tools. These help dissipate heat and reduce the likelihood of warping. Water-cooled saws or lubricants applied during cutting can be effective.
- c. Clamping and Fixturing: Secure the aluminum sheet metal properly to minimize vibration and movement during cutting. The use of clamps, fixtures, or jigs can help maintain the material's stability.
- d. Gradual Cuts: If you're making long cuts, consider making multiple passes with lighter pressure instead of a single deep cut. This approach reduces the heat generated and the potential for warping.
2. Minimizing Burrs
- a. Proper Blade Selection: Choose a blade or cutting tool with the appropriate tooth count and design for the type and thickness of the aluminum sheet metal. A blade with fewer, larger teeth can reduce the production of burrs.
- b. Backing Material: Place a backing material, such as plywood or a sacrificial piece of aluminum, beneath the material you're cutting. This supports the sheet metal and minimizes the risk of burrs on the underside.
- c. Cutting Speed: Maintain a consistent and moderate cutting speed. Avoid excessive feed rates or forcing the tool through the material, as this can lead to burrs and rough edges.
- d. Deburring Tools: Use deburring tools to remove any burrs that do form. These tools come in various shapes and sizes, including hand tools and power tools, and can be used to smooth and round sharp edges.
3. Reducing Noise and Vibration
- a. Ear Protection: To mitigate the impact of noise and vibration, always wear appropriate hearing protection, such as earplugs or earmuffs, when working with loud power tools or equipment.
- b. Tool Maintenance: Regularly inspect and maintain your cutting tools to ensure they are in good working condition. Dull blades can produce more noise and vibration, as they struggle to cut through the material efficiently.
- c. Vibration-Dampening Pads: Place vibration-dampening pads or mats under your tools or workbench to absorb and reduce vibrations. This helps to create a quieter and more comfortable workspace.
- d. Tool Isolation: Isolate power tools or equipment from their stands or work surfaces using rubber or anti-vibration mounts. This can reduce the transmission of vibrations to the surrounding area.
- e. Anti-Vibration Gloves: Wearing anti-vibration gloves can help reduce the impact of tool vibrations on your hands, reducing the risk of discomfort or injury.
Post-Cutting Steps
Once you've successfully cut your aluminum sheet metal, it's important to address post-cutting tasks to ensure the final product is safe, functional, and aesthetically pleasing. This section covers two key post-cutting steps: removing sharp edges and surface finishing.1. Removing Sharp Edges
After cutting aluminum sheet metal, sharp or rough edges are common and can pose safety hazards. Here are some methods for removing these sharp edges:- a. Deburring Tools: Use a deburring tool or file to remove burrs and sharp edges from the cut edges of the metal. A deburring tool is specifically designed for this purpose and can produce smooth, rounded edges.
- b. Sandpaper: Sand the cut edges with sandpaper to smooth them and remove any sharp burrs. Begin with a coarser grit and progressively move to finer grits for a polished finish.
- c. Edge Rounding: Consider using a router with a rounding-over bit to create rounded edges along the cut sections. This not only removes sharp edges but can also enhance the appearance of the aluminum.
- d. Chamfering: For a beveled edge, chamfer the cut edges with a chamfering tool or router. This can make the edges safer and more visually appealing.
- e. Safety Gloves: While performing these post-cutting tasks, wear safety gloves to protect your hands from sharp edges, metal splinters, and abrasive surfaces.
2. Surface Finishing
Depending on your project and aesthetic preferences, you may want to apply a surface finish to the aluminum sheet metal. Surface finishing not only improves the appearance but can also enhance corrosion resistance and durability. Here are some common surface finishing options:- a. Polishing: Polishing is used to achieve a shiny, reflective surface. Aluminum can be polished to a high sheen using polishing compounds and abrasive materials.
- b. Brushed Finish: A brushed finish gives the aluminum sheet a textured, linear pattern that adds a decorative touch. This is often done by using wire brushes or abrasive pads.
- c. Anodizing: Anodizing is an electrochemical process that creates a durable and corrosion-resistant surface. It can be used to add color to the aluminum and is commonly applied to architectural or decorative aluminum components.
- d. Powder Coating: Powder coating involves applying a dry powder paint to the aluminum sheet, followed by baking it to create a durable and attractive finish. It comes in various colors and textures.
- e. Paint or Coating: Painting or applying a specialized coating can add color and protection to the aluminum. Ensure you select a paint or coating that is suitable for use on metal surfaces.
- f. Clear Coating: A clear coat can be applied to preserve the natural appearance of the aluminum while providing a protective layer against oxidation and corrosion.
- g. Sandblasting: Sandblasting is a process that uses abrasive materials to create a matte or textured surface. It can be used to remove imperfections or rust before applying a finish.
Conclusion
In this comprehensive guide, we've explored the world of cutting aluminum sheet metal, covering various aspects from the importance of accurate cuts to the tools and methods used, as well as safety precautions and post-cutting steps. Let's recap the key points discussed in this guide and provide some final words of encouragement and safety reminders.Summary of Key Points
- Aluminum sheet metal is a versatile material used in a wide range of applications due to its lightweight, corrosion-resistant properties.
- Accurate aluminum sheet metal cutting is crucial for the quality, safety, and success of your projects.
- Safety precautions, including Personal Protective Equipment (PPE) and a safe workspace setup, are vital for preventing accidents and ensuring your well-being.
- The choice of cutting tool should be based on factors like material thickness, the type of cuts required, and your budget.
- Proper preparation involves measuring and marking, securing the material, and selecting the right blade for the task.
- Achieving clean and accurate cuts depends on factors such as blade maintenance, cutting speed, and cooling methods.
- Common challenges like material warping, burrs, noise, and vibration can be addressed with appropriate techniques and safety measures.
- Post-cutting steps include removing sharp edges and applying surface finishes to enhance the appearance and functionality of the aluminum.
Encouragement and Safety Reminder
As you embark on your aluminum sheet metal cutting projects, remember that practice and experience are key to mastering the craft. Start with smaller, simpler projects to build your skills and confidence, and gradually work your way up to more complex endeavors. Never compromise on safety. Prioritize the use of Personal Protective Equipment (PPE), create a safe workspace, and follow safety guidelines for each cutting method. Your well-being is paramount, and adherence to safety practices ensures your projects are not only successful but also accident-free. Cutting aluminum sheet metal can be a highly rewarding and creative process. Whether you are a professional metalworker or a DIY enthusiast, precision and attention to detail will set your projects apart. With the knowledge and techniques shared in this guide, you are well-equipped to tackle a wide range of aluminum sheet metal cutting tasks. Remember to take your time, prioritize safety, and enjoy the journey of turning aluminum sheet metal into functional, beautiful creations. Good luck, and happy crafting!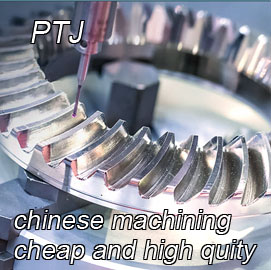
Our Services
- 5 Axis Machining
- Cnc Milling
- Cnc Turning
- Machining Industries
- Machining Process
- Surface Treatment
- Metal Machining
- Plastic Machining
- Powder Metallurgy Mold
- Die Casting
- Parts Gallery
Case Studies
- Auto Metal Parts
- Machinery Parts
- LED Heatsink
- Building Parts
- Mobile Parts
- Medical Parts
- Electronic Parts
- Tailored Machining
- Bicycle Parts
Material List
- Aluminum Machining
- Titanium Machining
- Stainless Steel Machining
- Copper Machining
- Brass Machining
- Super Alloy Machining
- Peek Machining
- UHMW Machining
- Unilate Machining
- PA6 Machining
- PPS Machining
- Teflon Machining
- Inconel Machining
- Tool Steel Machining
- More Material
Parts Gallery