What is an Engine Lathe & How Does It Work
2023-09-29
In the world of precision machining, the engine lathe stands as an enduring symbol of craftsmanship, versatility, and engineering excellence. It's a cornerstone tool in manufacturing and metalworking industries, renowned for its ability to turn raw materials into precise and intricate components. In this comprehensive guide, we will delve deep into the inner workings of an engine lathe, exploring its various parts, functions, and applications. By the time you finish reading, you'll have a thorough understanding of what an engine lathe is and how it plays a pivotal role in shaping the modern world.
The Early Origins of Lathes
The story of precision machining and the engine lathe begins with the humble origins of the lathe itself. In this section, we will embark on a journey through time, tracing the early origins of lathes and their evolution from basic hand-operated tools to the sophisticated precision machines we know today.- Primitive Beginnings:The history of lathes can be traced back to ancient civilizations, where primitive forms of these machines were used for shaping wood, stone, and other materials. Early lathes were often operated manually by craftsmen who rotated the workpiece against a cutting tool. These ancient lathes laid the foundation for the development of more advanced machining techniques.
- The Ancient Egyptians and Greeks:One of the earliest documented uses of a lathe-like device dates back to ancient Egypt, around 1300 BC. These lathes were primarily used for woodworking and pottery. Similarly, ancient Greek craftsmen employed lathes to create intricate designs on wood and metal.
- The Medieval European Lathe:During the Middle Ages in Europe, lathes continued to evolve. The Medieval European lathe, often referred to as the pole lathe or spring pole lathe, featured a foot-operated treadle and a spring mechanism, allowing for more efficient and precise turning of wooden objects. These lathes were crucial in crafting intricate woodwork, such as furniture and architectural elements.
- The Emergence of Metalworking Lathes:As metallurgy advanced, so did the need for lathes capable of machining metal. During the Renaissance, skilled metalworkers and inventors began designing lathes specifically for metalworking. These lathes incorporated innovations like lead screws and gear mechanisms to improve precision and control.
1.2 Evolution of Engine Lathes
The transition from manual craftsmanship to mechanized precision machining was marked by significant advancements in lathe technology. In this section, we will explore the evolution of engine lathes, the pinnacle of this machining evolution.- The Industrial Revolution and Early Engine Lathes:The Industrial Revolution of the 18th and 19th centuries brought about a dramatic shift in manufacturing. Innovations like the steam engine and mass production techniques created a demand for more efficient machining processes. This era saw the emergence of early engine lathes, powered by steam engines or waterwheels, which allowed for continuous and more precise machining.
- The Birth of the Modern Engine Lathe:The late 19th and early 20th centuries witnessed the refinement of engine lathes into the modern machines we recognize today. Key innovations during this period included the development of the quick-change gearbox, which allowed for rapid adjustments of cutting speeds and feeds, and the introduction of electric motors as power sources.
- World Wars and Advancements:Both World War I and World War II played significant roles in the advancement of engine lathe technology. The demands of wartime production required the development of more versatile and accurate lathes. These wartime innovations, such as the introduction of numerical control systems, set the stage for the computerized CNC (Computer Numerical Control) engine lathes of the future.
- CNC Revolution:The advent of computers in the mid-20th century ushered in a new era of precision machining. CNC engine lathes, controlled by computer programs, allowed for unparalleled accuracy and automation. This revolutionized industries ranging from aerospace to automotive and led to the production of complex components that were previously unattainable.
What is an Engine Lathe?
At its core, an engine lathe is a precision machining tool designed to turn and shape various materials into cylindrical or conical shapes with a high degree of accuracy and precision. Engine lathes are a fundamental part of the manufacturing and metalworking industries, serving as versatile workhorses for tasks ranging from simple turning to intricate threading and tapering operations. The name "engine lathe" reflects their historical use in manufacturing engine components. Engine lathes are characterized by their horizontal orientation, with the workpiece secured between two centers, allowing it to rotate while a cutting tool moves along its axis. This turning action is the primary function of an engine lathe, and it forms the basis for numerous machining operations.2.2 Types of Engine Lathes
Engine lathes come in various types, each tailored to specific machining tasks and workpiece sizes. Some common types include:- Bench Lathe: These compact lathes are small and portable, suitable for light-duty tasks and educational purposes.
- Gap Bed Lathe: Gap bed lathes feature a removable section of the bed, known as the gap, which allows the lathe to accommodate larger workpieces with a diameter exceeding the standard swing capacity.
- Turret Lathe: Turret lathes are automated lathes equipped with a turret toolholder, enabling rapid tool changes and the ability to perform multiple operations without manual intervention.
- Speed Lathe: Speed lathes are designed for high-speed operations, such as polishing, buffing, and light turning. They are commonly used in woodworking and metal polishing applications.
- Heavy-Duty Lathe: These robust lathes are designed for machining large and heavy workpieces, making them ideal for industrial applications, including shipbuilding and large-scale manufacturing.
2.3 Key Components of an Engine Lathe
Engine lathes consist of several essential components that work in harmony to facilitate precision machining. These components include:- Bed:The bed is the foundation of the engine lathe, providing stability and support for all other components. It is typically made of cast iron and features a precision-ground, flat, and hardened surface. The bed's design influences the lathe's size, weight capacity, and rigidity. Beds can vary in length to accommodate different workpiece sizes.
- Headstock:The headstock is located at the left end of the bed (when facing the lathe). It houses the main spindle, which holds the workpiece. The spindle is driven by a motor and can rotate at various speeds through a gearbox. The headstock also contains mechanisms for controlling the direction and speed of the spindle.
- Tailstock:Located at the right end of the bed, the tailstock provides support to the free end of the workpiece. It can be moved along the bed to accommodate different workpiece lengths. The tailstock often includes a quill that can be extended or retracted to apply pressure to the workpiece, allowing for drilling, reaming, and other operations.
- Carriage:The carriage is mounted on the bed and can move longitudinally along the bed's ways. It consists of several components, including the saddle, cross-slide, and compound rest. The carriage carries the cutting tool and is responsible for controlling the depth of cut and the feed rate during machining operations.
- Tool Post:The tool post is mounted on the carriage and holds the cutting tool securely. It allows for tool changes and adjustments, ensuring precise machining operations. There are various types of tool posts, including quick-change tool posts that expedite tool changes.
2.4 Size and Capacity
The size and capacity of an engine lathe are critical factors in determining its suitability for specific machining tasks. The primary parameters to consider are:- Swing: The swing is the maximum diameter of the workpiece that can be accommodated by the lathe. It is measured from the bed to the centerline of the spindle. The gap bed lathe's swing includes the gap, which allows for machining larger-diameter workpieces.
- Center Distance: Center distance refers to the maximum length between the centers of the headstock and tailstock. It determines the maximum workpiece length that can be turned on the lathe.
2.5 Precision and Tolerance
One of the key attributes of engine lathes is their ability to work with precision and tight tolerances. Precision in machining refers to the degree of accuracy and consistency with which a lathe can shape a workpiece. Tolerance, on the other hand, is the allowable variation from a specified dimension or specification. Achieving precision and tight tolerances on an engine lathe depends on several factors, including:- Machine Rigidity: The rigidity of the lathe's components, particularly the bed and tooling, is crucial for maintaining precision during machining.
- Tool Selection and Sharpness: The choice of cutting tools and their sharpness directly affects the quality of the machined surface and the ability to hold tight tolerances.
- Control of Cutting Parameters: Operators must carefully control cutting speed, feed rate, and depth of cut to achieve the desired precision.
- Measurement and Inspection: The use of precision measuring instruments, such as micrometers and dial indicators, is essential for verifying the dimensions of machined parts and ensuring they meet specified tolerances.
- Machine Calibration: Periodic calibration and maintenance of the lathe are necessary to maintain its accuracy and precision over time.
The Basics of Turning
Turning is the fundamental machining process performed on an engine lathe. It involves the rotation of a workpiece while a cutting tool removes material from its surface. This process is used to create cylindrical or conical shapes, threads, and other intricate profiles. Here's an overview of the basic steps involved in turning:- Workpiece Preparation: Start by selecting the appropriate material and workpiece size. Ensure that the workpiece is securely mounted between the lathe's headstock and tailstock centers.
- Tool Selection: Choose the right cutting tool for the job. The tool's geometry, material, and edge geometry should match the material being machined and the desired shape.
- Setting Cutting Parameters: Adjust the lathe's settings, including cutting speed, feed rate, and depth of cut, to match the material and machining operation. These parameters affect the quality and efficiency of the machining process.
- Tool Engagement: Bring the cutting tool into contact with the rotating workpiece. The tool should be positioned at the desired starting point and orientation.
- Rotating the Workpiece: Activate the lathe's spindle, causing the workpiece to rotate. This rotation is essential for achieving even and symmetrical material removal.
- Cutting Action: As the workpiece rotates, the cutting tool engages with the material's surface. The tool's movement, controlled by the carriage and cross-slide, determines the shape and dimensions of the final part.
- Continuous Machining: Continue the cutting process, gradually advancing the tool along the workpiece's length. The carriage's longitudinal movement and cross-slide's lateral movement allow for the creation of complex profiles and features.
- Finishing Passes: For precision work, finish passes are often performed to achieve the desired surface finish and dimensions. These passes involve lighter cuts and finer tool adjustments.
- Coolant and Chip Management: Depending on the material being machined, a coolant or cutting fluid may be applied to reduce heat and improve tool life. Proper chip management is also crucial to prevent chip buildup and interference with the machining process.
3.2 Workholding Devices
Workholding devices are essential for securing the workpiece in place during turning operations. Engine lathes offer several options for workpiece clamping, including:- Chucks: Chucks are commonly used to hold cylindrical workpieces. They come in various types, such as three-jaw chucks and four-jaw chucks, and can be either self-centering or independent. Chucks provide a secure grip on the workpiece and are ideal for high-precision operations.
- Collets: Collets are precision workholding devices that grip the workpiece from the inside, ensuring concentricity. They are suitable for small-diameter workpieces and high-speed machining.
- Faceplates: Faceplates are used for irregularly shaped workpieces or those that cannot be clamped using chucks or collets. Workpieces are attached to the faceplate using bolts or clamps.
- Steady Rests and Follow Rests: These devices support long, slender workpieces during machining to prevent deflection or vibration. Steady rests are used for the outer diameter, while follow rests support the inner diameter.
3.3 Tooling and Cutting Tools
Tooling and cutting tools play a crucial role in the turning process. Key considerations include:- Tool Geometry: The choice of tool geometry, such as rake angle and clearance angle, affects cutting efficiency and surface finish. Different tool shapes are used for various machining tasks.
- Tool Material: Tool materials must be selected based on the workpiece material. Common tool materials include high-speed steel (HSS), carbide, and ceramics, each with its unique properties and applications.
- Tool Holders: Tool holders secure the cutting tool in the tool post and allow for precise adjustments of tool height and orientation.
- Coolant Delivery: Some machining operations require coolant or cutting fluid to lubricate the cutting tool and workpiece, reduce friction and heat, and improve chip evacuation.
3.4 Setting Up and Operating the Engine Lathe
Setting up and operating an engine lathe involves several essential steps:- Workpiece Mounting: Place the workpiece between the headstock and tailstock centers or secure it in the chosen workholding device.
- Tool Installation: Mount the cutting tool in the tool holder and ensure it is properly aligned and oriented for the intended machining operation.
- Speed and Feed Adjustment: Set the appropriate cutting speed (rotation speed of the spindle) and feed rate (rate at which the tool advances along the workpiece) based on the material, tooling, and machining operation.
- Tool Positioning: Position the tool at the starting point, ensuring it is clear of the workpiece and other obstructions.
- Safety Precautions: Prioritize safety by wearing appropriate personal protective equipment (PPE), ensuring proper machine guarding, and following safety protocols.
- Machine Activation: Start the lathe's spindle and engage the tool with the workpiece, beginning the machining process.
- Monitoring and Adjustments: Continuously monitor the machining operation, making any necessary adjustments to cutting parameters, tool position, or coolant application to ensure a successful outcome.
3.5 Achieving Precision: Measuring and Adjusting
Achieving precision in turning operations requires meticulous measurement and adjustment processes:- Measurement Tools: Use precision measuring instruments, such as micrometers, dial indicators, and calipers, to measure workpiece dimensions and verify that they meet specified tolerances.
- In-Process Inspection: Perform in-process inspections at various stages of machining to identify and address any deviations from the desired dimensions or surface finish.
- Tool Wear and Replacement: Regularly inspect cutting tools for wear and damage, and replace them as needed to maintain consistent quality.
- Tool Offset and Compensation: Adjust tool offsets to compensate for wear and deviations, ensuring that the lathe consistently produces accurate parts.
- Surface Finish Evaluation: Assess the surface finish using roughness measurement tools to verify that it meets the required specifications.
- Documentation: Maintain accurate records of machining parameters, measurements, and adjustments for quality control and future reference.
Manufacturing Industries
Engine lathes are the workhorses of manufacturing industries, serving as the backbone for producing a wide range of components. They are indispensable in the creation of parts for machinery, vehicles, and consumer products. Some key applications in manufacturing include:- Automotive Industry: Engine lathes are used to manufacture various automotive components, including engine pistons, brake drums, and axles. Their precision and versatility play a crucial role in producing reliable and high-performance vehicles.
- Metalworking and Fabrication: Manufacturing plants rely on engine lathes to create precision metal parts such as shafts, gears, and threaded components. They are also essential for fabricating structural steel elements used in construction.
- Electronics Manufacturing: In the electronics industry, engine lathes are used for machining parts like connectors, switches, and custom housings for electronic devices. Their ability to work with various materials, including plastics and metals, makes them invaluable.
4.2 Repair and Maintenance
Engine lathes are equally important in the field of repair and maintenance, where they are used to restore and extend the lifespan of machinery and equipment. Applications in repair and maintenance include:- Machinery Repair: Engine lathes are employed to restore worn or damaged components of industrial machinery, ensuring optimal functionality and minimizing downtime.
- Automotive Repair: Repair shops use lathes to resurface brake drums, rotors, and engine components, ensuring safe and reliable vehicle performance.
- Ship Maintenance: In shipyards and naval facilities, engine lathes are used for the repair and maintenance of ship propulsion systems, including propellers and drive shafts.
4.3 Art and Craftsmanship
Engine lathes also find applications in artistic and craftsmanship endeavors, where they are utilized to create aesthetically pleasing and intricate designs. Examples include:- Woodturning: Woodworkers and artisans use engine lathes to craft decorative wood pieces, such as bowls, vases, and intricate wooden spindles for furniture.
- Metal Artistry: Artists working with metal use lathes to shape metal into sculptures, ornaments, and architectural elements, allowing for intricate and customized designs.
4.4 Space and Aerospace Industry
The space and aerospace industries demand components that meet rigorous standards of precision and reliability. Engine lathes play a critical role in producing parts for spacecraft, aircraft, and related equipment. Key applications include:- Aircraft Components: Engine lathes are used to manufacture critical aircraft components, including landing gear parts, engine components, and control system components.
- Spacecraft Components: In the space industry, engine lathes are employed to create components such as satellite housings, rocket nozzles, and fuel system parts.
4.5 Medical and Dental Fields
In the medical and dental fields, precision and accuracy are paramount. Engine lathes contribute to the production of specialized components used in medical devices and dental equipment. Applications include:- Dental Prosthetics: Engine lathes are used to fabricate dental prosthetics, including crowns, bridges, and dentures, ensuring a precise fit and function.
- Medical Instruments: Precision instruments used in medical machining procedures, such as surgical tools, implant components, and diagnostic equipment, are often manufactured with the help of engine lathes.
- Orthopedic Devices: Engine lathes are utilized in crafting orthopedic implants like hip and knee prostheses, which must meet stringent tolerances and material requirements.
Routine Maintenance
Routine maintenance is essential for keeping an engine lathe in optimal working condition, preventing breakdowns, and ensuring safety. Here are the key aspects of routine maintenance: 6.1.1 Cleaning and Lubrication- Regularly clean the lathe, removing dust, chips, and debris from all components, including the bed, carriage, and tailstock.
- Lubricate all moving parts according to the manufacturer's recommendations. Use the appropriate lubricants and ensure they are applied at the specified intervals.
- Conduct visual inspections to identify signs of wear, damage, or misalignment. Pay attention to the condition of belts, gears, and bearings.
- Inspect electrical components, such as wiring and switches, for any signs of wear or damage.
- Periodically calibrate the lathe's measuring instruments, such as the tailstock quill, to ensure accuracy.
- Check and adjust the tool height and tool center height to maintain precision in machining.
- Inspect safety features, such as emergency stop buttons, guards, and interlocks, to ensure they are functioning correctly.
- Verify that warning labels and safety instructions are legible and in good condition.
6.2 Troubleshooting Common Issues
Despite regular maintenance, issues may arise during lathe operation. Being able to troubleshoot and address common problems is crucial for minimizing downtime. Here are some common lathe issues and troubleshooting tips:6.2.1 Excessive Vibration or Chatter
Potential Causes:- Loose workholding or tooling
- Unbalanced workpiece
- Worn or damaged tool
- Incorrect cutting parameters
- Check and secure workholding and tooling.
- Balance the workpiece if necessary.
- Inspect and replace worn or damaged tools.
- Adjust cutting parameters, such as speed and feed rate.
6.2.2 Poor Surface Finish
Potential Causes:- Dull or worn cutting tool
- Incorrect tool geometry
- Excessive tool wear
- Insufficient lubrication
- Sharpen or replace the cutting tool.
- Ensure the correct tool geometry for the material and operation.
- Monitor tool wear and replace as needed.
- Ensure proper lubrication of the workpiece and tool.
6.2.3 Inaccurate Dimensions
Potential Causes:- Tool height or tool center height misalignment
- Wear or damage to leadscrews or other components
- Incorrect tool offsets
- Inconsistent workpiece material
- Realign the tool height and tool center height.
- Inspect and replace any worn or damaged leadscrews or components.
- Check and adjust tool offsets as needed.
- Ensure consistent workpiece material quality.
6.2.4 Electrical Issues
Potential Causes:- Power supply problems
- Faulty wiring or connections
- Malfunctioning motor or control unit
- Check the power supply and circuit breakers.
- Inspect wiring and connections for loose or damaged components.
- Test and diagnose motor and control unit issues. Seek professional assistance if needed.
6.3 Extending the Lifespan
Extending the lifespan of an engine lathe involves proactive measures to maintain its structural integrity and functionality over the long term:- 6.3.1 Regular Inspections:Implement a regular inspection schedule to catch and address issues early, preventing them from becoming more significant problems.
- 6.3.2 Preventive Maintenance:Follow the manufacturer's recommended maintenance procedures and schedules. This includes routine oil changes, lubrication, and replacement of wear-prone components.
- 6.3.3 Operator Training:Ensure that operators are properly trained in the safe and correct use of the lathe. Operator errors can lead to unnecessary wear and damage.
- 6.3.4 Environment Control:Keep the lathe in a clean and controlled environment. Dust, humidity, and temperature fluctuations can impact the lathe's performance and longevity.
- 6.3.5 Replacement of Critical Components:Over time, critical components such as bearings, gears, and belts may wear out. Regularly assess these components and replace them when necessary to prevent catastrophic failure.
- 6.3.6 Documentation:Maintain thorough records of maintenance activities, repairs, and any issues encountered. This documentation aids in tracking the lathe's history and informs future maintenance decisions.
Conclusion: The Enduring Legacy of Engine Lathes
The engine lathe, with its rich history and multifaceted applications, stands as a testament to human ingenuity and innovation in precision machining. Its enduring legacy is rooted in its remarkable versatility, precision, and adaptability, making it an indispensable tool in a multitude of industries and applications. From its humble origins as a manually operated woodworking tool to the modern computer-controlled CNC engine lathes, this remarkable machine has evolved alongside the ever-changing needs of manufacturing, repair, artistry, and craftsmanship. It has played a pivotal role in shaping the world we live in today, contributing to advancements in transportation, technology, and healthcare, among others. In manufacturing industries, the engine lathe continues to be the cornerstone of production, enabling the creation of intricate and precise components that drive modern machinery and vehicles. It has been a catalyst for innovation, allowing for the development of high-performance automobiles, spacecraft, and medical devices. In the hands of skilled craftsmen and artisans, the engine lathe has transcended its industrial applications to become a tool of artistic expression. From finely turned wooden art pieces to intricate metal sculptures, it has empowered artists to bring their creative visions to life with precision and detail. The engine lathe's contributions to repair and maintenance are equally significant, ensuring the longevity and reliability of machinery and equipment across various sectors. Its role in revitalizing worn or damaged components has extended the lifespan of countless machines, minimizing downtime and reducing waste. In the aerospace and medical fields, where precision and reliability are non-negotiable, engine lathes continue to play an essential role in the creation of components that push the boundaries of what is possible. Whether it's manufacturing aerospace components or crafting dental prosthetics, these lathes are trusted for their ability to deliver uncompromising quality. The enduring legacy of engine lathes extends beyond their tangible contributions to industries; it encompasses a tradition of craftsmanship, skill, and innovation. As we look to the future, we can expect continued advancements in lathe technology, integration with digital systems, and a commitment to sustainability. In conclusion, the engine lathe is more than just a machine; it is a symbol of human achievement and progress in the world of precision machining. Its legacy is etched in the components of our daily lives and the marvels of modern engineering. As we celebrate the past, embrace the present, and look to the future, we recognize the enduring significance of the engine lathe in shaping the world as we know it.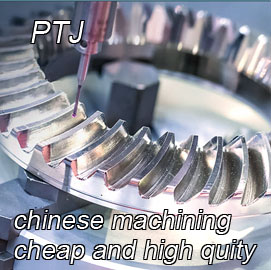
Our Services
- 5 Axis Machining
- Cnc Milling
- Cnc Turning
- Machining Industries
- Machining Process
- Surface Treatment
- Metal Machining
- Plastic Machining
- Powder Metallurgy Mold
- Die Casting
- Parts Gallery
Case Studies
- Auto Metal Parts
- Machinery Parts
- LED Heatsink
- Building Parts
- Mobile Parts
- Medical Parts
- Electronic Parts
- Tailored Machining
- Bicycle Parts
Material List
- Aluminum Machining
- Titanium Machining
- Stainless Steel Machining
- Copper Machining
- Brass Machining
- Super Alloy Machining
- Peek Machining
- UHMW Machining
- Unilate Machining
- PA6 Machining
- PPS Machining
- Teflon Machining
- Inconel Machining
- Tool Steel Machining
- More Material
Parts Gallery