How Are High Precision Parts Machined
2023-09-22
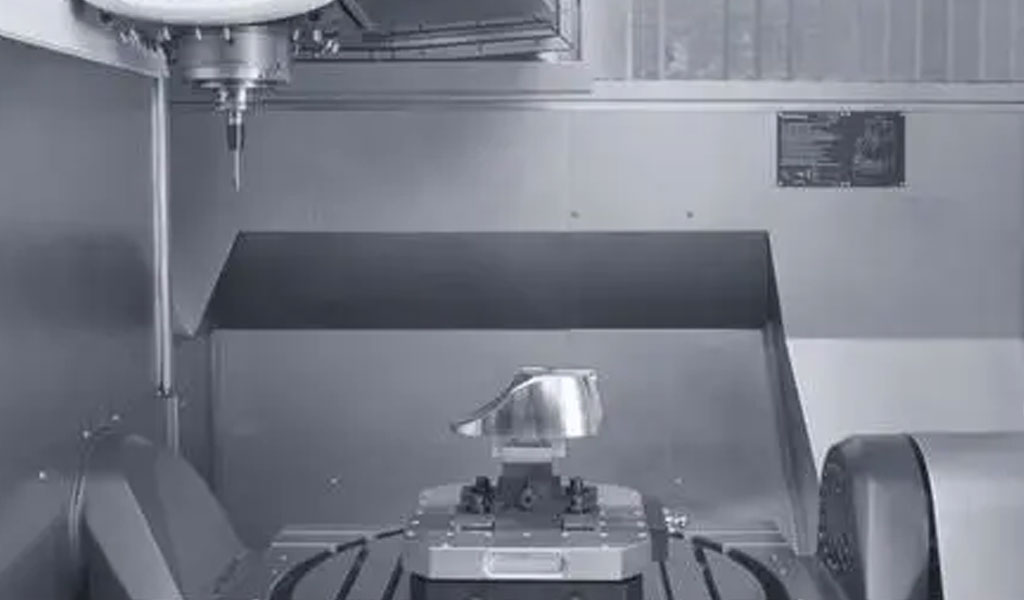
Understanding Precision Machining
Precision machining is a cornerstone of modern manufacturing, responsible for producing intricate and accurate components used in a wide range of industries. To grasp its significance fully, let's explore the core concepts of precision machining, its vital role in various sectors, and the historical journey that has led to its current state of excellence.A. What is Precision Machining?
Precision machining refers to a set of manufacturing processes that remove material from a workpiece with a high degree of accuracy and control, resulting in finely crafted components with tight tolerances. This process transforms raw materials, such as metals, plastics, or ceramics, into precise parts that meet exacting specifications. The key characteristics of precision machining include:- Accuracy: Precision machining ensures that the final product conforms precisely to the intended design, with minimal deviation.
- Tight Tolerances: It allows for the production of parts with extremely tight tolerances, meaning the finished components adhere closely to specified measurements.
- Superior Surface Finish: Precision machining provides exceptional surface finishes, often eliminating the need for additional finishing processes.
- Complex Geometries: It can create intricate shapes, contours, and features, making it indispensable in manufacturing components with complex designs.
- Repeatability: Precision machining processes are highly repeatable, ensuring consistent quality across multiple parts.
- Versatility: It can be applied to a wide range of materials, making it suitable for diverse industries.
B. Importance of Precision Machining
Precision machining holds immense significance in several critical industries, impacting various aspects of our daily lives. Here are some compelling reasons for its importance:- Aerospace Industry: In the aerospace sector, precision machining is indispensable for crafting components that withstand extreme conditions. Aircraft engines, landing gear, and structural elements rely on precision-machined parts for safety and performance.
- Medical Devices: Medical devices like surgical instruments, prosthetics, and implantable devices require precision machining for biocompatibility, accuracy, and patient safety.
- Automotive Sector: Precision-machined parts are essential for the automotive industry to ensure the reliability and efficiency of vehicles. Components such as engine parts, transmission systems, and braking mechanisms rely on precise machining.
- Electronics and Semiconductors: Precision machining is pivotal in the production of microelectronic components and semiconductor devices, where minuscule tolerances are imperative for functionality.
- Energy Sector: The energy industry relies on precision machining for the production of critical parts used in power generation, including turbines, generators, and transmission components.
- Tool and Die Making: Precision machining is crucial in the manufacturing of tools and dies, which, in turn, are used to create countless other products.
- Consumer Electronics: The production of smartphones, laptops, and other consumer electronics benefits from precision machining to ensure sleek designs and optimal functionality.
- Research and Development: Researchers and scientists depend on precision-machined components for experiments, prototypes, and laboratory equipment.
C. Historical Perspective
The journey of precision machining traces back to ancient civilizations, where skilled artisans used rudimentary tools to shape materials. However, the precision achieved in those times was limited compared to contemporary standards.- Early Precision Machining: The industrial revolution of the 18th and 19th centuries marked a pivotal period in the development of precision machining. The invention of machine tools, such as lathes and milling machines, revolutionized manufacturing by enabling greater accuracy and consistency.
- World War II: Precision machining played a pivotal role in World War II, as it was essential for producing military equipment with the required precision and uniformity. This era witnessed advancements in machining techniques and the emergence of new materials.
- Post-War Advancements: The post-war period saw a surge in technological innovations, including the use of computer numerical control (CNC) machines. CNC machining allowed for automated and highly precise operations, ushering in a new era of manufacturing.
- The Digital Age: The integration of computers and software into machining processes has further elevated precision machining. Modern CNC machines can execute complex operations with unparalleled accuracy, making them indispensable in today's manufacturing landscape.
Materials and Their Significance
Materials are the foundation of precision machining, and the selection of the right material plays a pivotal role in the production of high precision parts. In this section, we will delve into the importance of selecting the appropriate materials, understand the significance of material properties, and explore the various factors that affect machinability.A. Selection of Materials
The choice of materials in precision machining is a critical decision that directly impacts the performance, durability, and functionality of the final product. Manufacturers must consider several factors when selecting materials:- Material Suitability: The material must be suitable for the intended application. Different industries and applications have varying requirements, such as temperature resistance, corrosion resistance, and electrical conductivity.
- Mechanical Properties: Mechanical properties like tensile strength, hardness, and ductility are crucial. For example, in aerospace, materials with high tensile strength are preferred for structural components.
- Thermal Properties: Some applications require materials with excellent thermal conductivity or resistance to high temperatures. This is especially important in industries like power generation and electronics.
- Corrosion Resistance: In environments where corrosion is a concern, materials with high resistance to corrosion, such as stainless steel or titanium, are preferred.
- Weight Considerations: Industries like automotive and aerospace often prioritize lightweight materials like aluminum or carbon fiber composites to reduce fuel consumption and enhance performance.
- Cost Constraints: Cost is a significant factor in material selection. High-performance materials can be expensive, so manufacturers must strike a balance between performance and cost-effectiveness.
- Regulatory Compliance: In industries like healthcare, materials must meet stringent regulatory standards for biocompatibility and safety.
- Availability: The availability of materials and their sources also affect selection. Some specialized alloys or composites may have limited availability.
B. Material Properties
Understanding the properties of materials is crucial for precision machining. Here are some key material properties and their significance:- Tensile Strength: Tensile strength measures a material's ability to withstand a pulling force without breaking. It is essential for structural components and parts subjected to mechanical stress.
- Hardness: Hardness indicates a material's resistance to deformation and wear. Hard materials are suitable for cutting tools, while softer materials may be preferred for certain applications, like seals.
- Ductility: Ductility refers to a material's ability to deform without breaking when subjected to tensile stress. Ductile materials are easier to shape but may not be suitable for applications requiring rigidity.
- Thermal Conductivity: Materials with high thermal conductivity efficiently dissipate heat. This property is vital in applications where temperature control is critical.
- Electrical Conductivity: Electrical conductivity is essential in electronics and electrical components, where materials must facilitate the flow of electricity.
- Magnetic Properties: Magnetic properties are significant in industries like electromagnetics and electronics, where materials may need to be ferromagnetic or non-magnetic.
- Chemical Resistance: Materials must resist chemical corrosion in environments where they are exposed to acids, bases, or other corrosive substances.
C. Machinability Factors
Machinability refers to the ease with which a material can be machined, cut, or shaped. It is influenced by various factors, including:- Material Hardness: Softer materials are generally easier to machine, while harder materials may require specialized tools and techniques.
- Chip Formation: The formation and evacuation of chips during machining affect the process's efficiency and surface finish.
- Tool Wear: Different materials can cause varying degrees of tool wear, impacting machining speed and cost.
- Coolant and Lubrication: Proper coolant and lubrication are essential to reduce friction, heat, and tool wear during machining.
- Cutting Speed: The speed at which the cutting tool moves through the material affects both productivity and the quality of the machined surface.
- Tool Material: The choice of cutting tool material, such as carbide or high-speed steel, depends on the material being machined.
- Cutting Parameters: Adjusting cutting parameters like feed rate and depth of cut can optimize the machining process for specific materials.
Machine Tools for Precision Machining
Machine tools are the heart of precision machining, enabling the transformation of raw materials into high precision parts. In this section, we will explore four key types of machine tools used in precision machining: CNC Machining Centers, Turning Machines, Grinding Machines, and EDM (Electrical Discharge Machining). Each of these machines plays a unique role in the production of precise components.A. CNC Machining Centers
CNC (Computer Numerical Control) machining centers are versatile and widely used in precision machining. They are automated systems that control the movement of cutting tools and workpieces with exceptional precision. Here's an overview of CNC machining centers and their significance:- Versatility: CNC machining centers can perform various machining operations, including milling, drilling, and tapping. This versatility allows for the production of complex parts with multiple features.
- High Precision: The computerized control of CNC machines ensures precise tool positioning and consistent results, making them ideal for parts with tight tolerances.
- Automation: CNC machining centers can operate continuously, with minimal human intervention. This automation increases efficiency and reduces the risk of errors.
- Complex Geometries: They excel in machining intricate shapes and contours, making them suitable for industries like aerospace, where complex components are common.
- Repeatable Results: CNC machines offer excellent repeatability, ensuring that each part produced matches the exact specifications of the design.
- Reduced Setup Times: CNC machining centers can be programmed to switch between different tasks quickly, minimizing setup times and increasing production efficiency.
B. Turning Machines
Turning machines are used to create cylindrical parts by rotating a workpiece while a cutting tool removes material from its outer surface. They are essential for producing shafts, pins, and other components with rotational symmetry. Key points about turning machines include:- Cylindrical Parts: Turning machines specialize in producing cylindrical or tubular components, including those with threads or intricate grooves.
- High Speeds: They operate at high speeds, making them suitable for parts that require a smooth and accurate finish.
- Single-Axis Operation: Most turning machines are single-axis, focusing on shaping the external surface of the workpiece.
- Efficient for Mass Production: Turning is highly efficient for mass-producing parts with minimal material waste.
- Lathe Machines: Manual and CNC-controlled lathe machines are commonly used turning machines, offering a range of capabilities.
C. Grinding Machines
Grinding machines are designed for precision surface finishing and shaping of hard or abrasive materials. They are crucial for achieving extremely tight tolerances and superior surface finishes. Here's why grinding machines are significant:- Micron-Level Precision: Grinding machines can achieve micron-level precision, making them essential for applications that demand the highest level of accuracy.
- Material Removal: They remove material by abrasion, allowing for the correction of surface imperfections and achieving exceptional smoothness.
- Tool and Cutter Grinding: In addition to surface grinding, there are specialized grinding machines for sharpening cutting tools and producing precise profiles.
- Variety of Grinding Methods: Different types of grinding machines, including surface grinders, cylindrical grinders, and centerless grinders, cater to various machining needs.
- Hardened Materials: Grinding is particularly suitable for hardened materials like tool steel and ceramics, where traditional machining methods may be ineffective.
D. EDM (Electrical Discharge Machining)
EDM, or Electrical Discharge Machining, is a non-traditional machining process that uses electrical discharges to shape materials. It is ideal for creating intricate and delicate parts where traditional cutting tools may cause damage. Key aspects of EDM include:- No Physical Contact: EDM does not involve direct physical contact between the tool and workpiece, minimizing the risk of tool wear and damage to fragile materials.
- High Precision: It can achieve high precision and surface finish quality, even with exceptionally hard materials.
- Wire EDM and Sinker EDM: There are two primary types of EDM machines: wire cutting EDM, which uses a wire electrode, and sinker EDM, which uses a shaped electrode.
- Complex Shapes: EDM can produce complex shapes, such as dies and molds, with intricate details and fine features.
- Heat-Affected Zone: Since EDM does not generate heat at the workpiece, it is suitable for heat-sensitive materials like aerospace alloys.
- Slow Process: EDM is relatively slow compared to other machining methods, making it best suited for low-quantity, high-precision jobs.
Cutting Tools and Tooling
Cutting tools are at the forefront of precision machining, serving as the instruments that shape and transform raw materials into high precision parts. In this section, we will explore the various types of cutting tools, the importance of tool coatings, and the factors affecting tool life and wear.A. Types of Cutting Tools
Precision machining relies on a diverse range of cutting tools, each designed for specific tasks and materials. The choice of cutting tool greatly influences the efficiency and accuracy of the machining process. Here are some common types of cutting tools:- End Mills: End mills are versatile tools used for milling operations. They have multiple cutting edges and can remove material from the workpiece in various ways, including facing, contouring, and slotting.
- Drills: Drills are designed for creating holes in workpieces. They come in various forms, including twist drills, center drills, and indexable drills.
- Turning Inserts: These are used in turning machines to shape cylindrical parts. Turning inserts are available in a variety of shapes and materials to suit different applications.
- Milling Cutters: Milling cutters come in different shapes, such as face mills, ball mills, and slotting cutters, and are used in milling machines to create various features on the workpiece.
- Reamers: Reamers are used for finishing and sizing previously drilled holes to precise dimensions. They ensure smooth and accurate hole surfaces.
- Taps and Dies: These cutting tools are used for threading operations. Taps create internal threads, while dies create external threads.
- Grinding Wheels: Grinding wheels are abrasive tools used for precision surface grinding. They are available in various abrasive materials and grit sizes.
- Broaches: Broaches are specialized tools used for cutting internal and external shapes and profiles, such as keyways and splines.
- Counterbores and Countersinks: These tools are used to create recesses or chamfers around holes for fasteners.
- Boring Bars: Boring bars are used in boring operations to enlarge existing holes with precision.
B. Tool Coatings
Tool coatings are thin layers of material applied to cutting tools to enhance their performance and durability. These coatings offer several advantages:- Reduced Friction: Coatings like titanium nitride (TiN) and titanium carbonitride (TiCN) reduce friction between the tool and workpiece, leading to smoother cutting and longer tool life.
- Enhanced Hardness: Coatings increase the hardness of the tool's surface, making it more resistant to wear and extending tool life.
- Improved Heat Resistance: Coatings can withstand high temperatures generated during machining, reducing heat-related tool wear and increasing cutting speeds.
- Anti-Buildup Properties: Some coatings have anti-adhesion properties, preventing the buildup of material on the tool's cutting edges.
- Increased Lubricity: Coated tools have improved lubricity, reducing the need for excessive coolant and enhancing chip evacuation.
C. Tool Life and Wear
Understanding tool life and wear is crucial for optimizing machining processes and minimizing production costs. Tool life refers to the duration a cutting tool remains effective before it requires replacement or reconditioning. Several factors influence tool life and wear:- Cutting Speed: Higher cutting speeds can lead to increased tool wear due to higher temperatures generated during machining. Proper selection of cutting speeds is essential to balance tool life and productivity.
- Feed Rate: The rate at which the cutting tool advances into the workpiece affects tool wear. High feed rates may accelerate wear, while lower feed rates can extend tool life.
- Depth of Cut: The depth of cut influences the amount of material removed per pass. Deeper cuts can increase tool wear, so optimizing depth is critical.
- Material Hardness: Cutting hard materials can accelerate tool wear. Specialized tools and coatings are used for machining hard materials effectively.
- Coolant and Lubrication: Proper coolant and lubrication help dissipate heat and reduce friction, extending tool life.
- Tool Material: The material from which the cutting tool is made affects its wear resistance. Materials like carbide and ceramic offer excellent wear resistance.
- Tool Geometry: The geometry of the cutting tool, including rake angle, relief angle, and chipbreaker design, plays a significant role in wear patterns.
- Workpiece Material: The type of material being machined affects tool wear. Abrasive materials can lead to faster tool wear.
Precision Machining Processes
Precision machining processes are the methods by which raw materials are transformed into high precision parts with tight tolerances and exceptional surface finishes. In this section, we will explore five key precision machining processes: Turning, Milling, Drilling, Grinding, and Electrical Discharge Machining (EDM). Each of these processes serves a unique purpose and is employed based on the specific requirements of the workpiece.A. Turning
Turning is a machining process primarily used for shaping cylindrical parts. It involves rotating a workpiece while a single-point cutting tool removes material from the outer surface. Here are the key aspects of turning:- Cylindrical Parts: Turning is ideal for producing cylindrical components such as shafts, pins, and sleeves.
- Rotational Symmetry: It is well-suited for parts requiring rotational symmetry, as the workpiece rotates on a lathe while the cutting tool shapes it.
- Various Operations: Turning can perform various operations, including facing, turning (reducing the diameter), taper turning, and threading.
- Single-Point Cutting: A single cutting tool removes material in a continuous motion, resulting in efficient material removal.
- Lathe Machines: Both manual and CNC-controlled lathe machines are commonly used for turning operations.
B. Milling
Milling is a versatile precision machining process that employs multi-point cutting tools to remove material from a workpiece. It is well-suited for creating a wide range of shapes and features. Key aspects of milling include:- Versatility: Milling can produce flat surfaces, slots, pockets, and complex contours. It is used for both 2D and 3D machining.
- Multi-Point Cutting: Multiple cutting edges on the tool interact with the workpiece simultaneously, allowing for efficient material removal.
- Types of Milling: Milling can be performed using various types of cutters, including end mills, face mills, and ball mills.
- CNC Machining Centers: CNC-controlled milling machines offer precise control over tool movement and are widely used in modern machining.
- High Speeds: Milling can be performed at high speeds, enabling efficient production.
C. Drilling
Drilling is a precision machining process used to create holes in workpieces. It is a fundamental operation in various industries. Key aspects of drilling include:- Hole Creation: Drilling machines use specialized tools called drills to remove material and create holes of specific diameters.
- Types of Drills: Different types of drills are available, including twist drills, center drills, and indexable drills, each designed for specific applications.
- Accuracy: Precise positioning and alignment are essential in drilling to ensure holes are created with accuracy.
- Speed and Feed Rate: Drilling parameters like rotational speed and feed rate are critical for achieving desired hole dimensions.
- Coolant and Lubrication: Proper coolant and lubrication are used to dissipate heat and reduce friction during drilling.
D. Grinding
Grinding is a precision machining process that employs abrasive wheels to remove material and achieve extremely tight tolerances and surface finishes. Key aspects of grinding include:- Exceptional Precision: Grinding can achieve micron-level precision, making it ideal for applications requiring the highest accuracy.
- Surface Finish: It produces superior surface finishes, often eliminating the need for additional finishing processes.
- Materials: Grinding is suitable for hard and abrasive materials, including hardened steel, ceramics, and carbides.
- Variety of Grinding Methods: Different types of grinding machines, such as surface grinders, cylindrical grinders, and centerless grinders, cater to various machining needs.
- Coolant: Proper coolant is essential in grinding to prevent overheating and maintain wheel integrity.
E. Electrical Discharge Machining (EDM)
EDM, or Electrical Discharge Machining, is a non-traditional precision machining process that uses electrical discharges to remove material. It is particularly suited for machining complex and intricate shapes, as well as hard and heat-resistant materials. Key aspects of EDM include:- Non-Contact Machining: EDM does not involve direct contact between the tool and workpiece, reducing the risk of tool wear and damage.
- High Precision: EDM can achieve high precision, making it suitable for applications where tight tolerances are essential.
- Complex Shapes: It excels in machining complex shapes, dies, molds, and components with fine details.
- Wire EDM and Sinker EDM: There are two primary types of EDM machines: wire EDM, which uses a wire electrode, and sinker EDM, which uses a shaped electrode.
- Slow Process: EDM is relatively slow compared to other machining methods, making it best suited for low-quantity, high-precision jobs.
Tolerances and Quality Control
Precision machining demands meticulous attention to detail and a rigorous commitment to quality control to ensure that parts meet the specified standards. In this section, we will explore three critical aspects of quality control in precision machining: Geometric Dimensioning and Tolerancing (GD&T), Statistical Process Control (SPC), and Quality Assurance.A. Geometric Dimensioning and Tolerancing (GD&T)
Geometric Dimensioning and Tolerancing, often abbreviated as GD&T, is a system used to define and communicate the allowable variations in size, form, orientation, and location of features on a part. GD&T is vital in precision machining for the following reasons:- Precise Communication: GD&T provides a standardized language for engineers, designers, and machinists to communicate design intent and dimensional requirements accurately.
- Tolerance Clarification: It helps define the acceptable variation in critical dimensions, ensuring that all stakeholders understand the permissible deviations.
- Enhanced Quality: GD&T promotes improved quality by reducing ambiguity in design specifications, minimizing the risk of errors during machining.
- Cost Efficiency: Clear GD&T specifications can lead to reduced manufacturing costs, as parts are less likely to be scrapped or require rework due to misunderstanding or misinterpretation.
- Complex Geometry: It is particularly useful for parts with complex geometries, ensuring that all features are manufactured to the desired specifications.
B. Statistical Process Control (SPC)
Statistical Process Control (SPC) is a quality control methodology that uses statistical techniques to monitor and control the machining process. SPC is essential in precision machining for the following reasons:- Process Monitoring: SPC helps monitor machining processes in real-time, identifying variations or deviations from the desired parameters.
- Early Detection of Issues: By continuously monitoring the process, SPC allows for the early detection of issues that could lead to out-of-spec parts, reducing waste and rework.
- Data-Driven Decision-Making: SPC relies on data and statistical analysis to make informed decisions about process adjustments, ensuring that the machining process remains within acceptable limits.
- Improved Consistency: SPC promotes process consistency and reduces the likelihood of producing non-conforming parts.
- Reduced Scrap and Rework: By identifying and addressing process variations promptly, SPC minimizes the production of defective parts, reducing scrap and rework costs.
C. Quality Assurance in Precision Machining
Quality assurance in precision machining encompasses a comprehensive approach to ensuring that manufactured parts meet or exceed specified quality standards. It involves various elements, including:- Process Documentation: Detailed documentation of machining processes, including standard operating procedures (SOPs) and work instructions, ensures that each step is performed consistently.
- Inspection and Measurement: Rigorous inspection and measurement using precision instruments and metrology techniques verify that parts conform to specified tolerances and quality standards.
- Calibration: Regular calibration of machining equipment and measuring instruments is essential to maintain accuracy and traceability.
- Material Verification: Verification of material properties, composition, and quality is critical to ensure that the material used meets design requirements.
- Employee Training: Training and skill development programs for machinists and quality control personnel ensure that they are proficient in their roles and responsibilities.
- Root Cause Analysis: When non-conforming parts are identified, root cause analysis is conducted to determine the source of the issue and implement corrective actions.
- Continuous Improvement: A culture of continuous improvement fosters innovation and drives ongoing enhancements in machining processes and quality control procedures.
- Customer Feedback: Gathering and analyzing customer feedback helps identify areas for improvement and aligns machining processes with customer expectations.
Conclusion
A. The Art and Science of Precision Machining
Precision machining stands at the intersection of art and science, where creativity, skill, and innovation converge to produce high precision parts that drive industries and shape the modern world. It is both an art form, requiring the craftsmanship and expertise of machinists who transform raw materials into works of engineering excellence, and a science that relies on cutting-edge technology, materials science, and advanced processes to achieve unparalleled precision. The journey of precision machining takes us through the understanding of materials and their properties, the mastery of cutting tools and machinery, and the meticulous control of processes and tolerances. It encompasses the language of geometric dimensioning and tolerancing, the vigilance of statistical process control, and the commitment to quality assurance. Precision machining plays a pivotal role in diverse industries, from aerospace and automotive to medical devices and electronics, shaping everything from aircraft engines to artificial joints and microchips. It enables the creation of components that operate with unmatched accuracy and reliability, often pushing the boundaries of what is possible.B. Final Thoughts
As we conclude this exploration of precision machining, it is clear that this field is not only about the creation of parts; it is about the creation of possibilities. The quest for precision drives innovation, pushing the boundaries of what can be achieved. Whether it's the delicate craftsmanship required to create a watch's intricate gears or the advanced technology needed to manufacture complex aerospace components, precision machining is at the heart of it all. The future of precision machining is filled with promise. Advances in materials science, automation, and digital technologies continue to reshape the landscape. Miniaturization, 3D printing, and sustainable manufacturing practices are becoming increasingly prominent, ushering in new horizons for the industry. In a world where precision matters more than ever, precision machining remains an indispensable pillar of modern engineering. It is a testament to human ingenuity and our unyielding pursuit of excellence in every facet of manufacturing. As the demand for higher precision and more intricate components grows, precision machining will continue to evolve, meeting the challenges of tomorrow with the same dedication and precision that have defined it for centuries.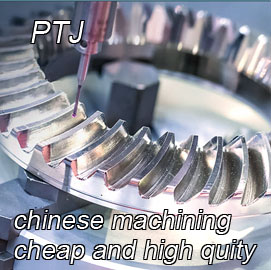
Our Services
- 5 Axis Machining
- Cnc Milling
- Cnc Turning
- Machining Industries
- Machining Process
- Surface Treatment
- Metal Machining
- Plastic Machining
- Powder Metallurgy Mold
- Die Casting
- Parts Gallery
Case Studies
- Auto Metal Parts
- Machinery Parts
- LED Heatsink
- Building Parts
- Mobile Parts
- Medical Parts
- Electronic Parts
- Tailored Machining
- Bicycle Parts
Material List
- Aluminum Machining
- Titanium Machining
- Stainless Steel Machining
- Copper Machining
- Brass Machining
- Super Alloy Machining
- Peek Machining
- UHMW Machining
- Unilate Machining
- PA6 Machining
- PPS Machining
- Teflon Machining
- Inconel Machining
- Tool Steel Machining
- More Material
Parts Gallery